How to insulate rim joists & above grade basement walls in older home without using foam?

Hello,
I’d appreciate input on how best to insulate/air seal an older basement without using foam (rigid or spray). I’ve gotten input from a few several weatherization folks, but the information varies and seems pretty expensive. I’m looking for an affordable solution that will work. (Photos are attached).
My goal is to 1) air seal and insulate the rim joists, 2) air seal the above-grade brick. I will eventually insulate the brick when budget allows.
RIM JOISTS: One plan is to either caulk or use Eco-seal spray applied sealant to air seal the joist cavities, then insert mineral wool (Roxul). Does the mineral wool need to be covered? I talked to 475 and they suggested using Intello, but the material is expensive and the labor will probably be expensive, too.
ABOVE GRADE BRICK: The above grade brick is about 4 ft tall. The exterior has decorative rock applied on 3 sides of the house (see photo) and I want to keep that look so any air-sealing solution would have to be on the interior. The mortar joints have holes of varying sizes so I’d like to air seal to start with. I don’t think it’s a structural issue. Also, the brick looks like it’s been painted white, if that has any bearing.
One contractor suggested troweling on Quickrete Surface Bond (with fiberglass) and the Q rep agreed. However, a mason I spoke to said to avoid products like that with Portland cement and instead use lime (NHL) or clay based mortar. I’ve seen basements that have had some time of parging and it’s crumbing and flaking off. I want to avoid that.
Someone else used Tu-Tuf to line the joist bays and then follow down the basement wall. He placed Eco-cell (rigid cellulose) batts on top of that, securing them with an adhesive and some strapping. Not sure if this is a tried & tested approach, but would like to hear if anyone has experience with either of these methods.
Below grade foundation is large stone. There are no water issues in the basement, but it does have a musty smell so I run a dehumidifier. The house was built in 1908 and all the rim joists and framing are in great shape, no rot. I’d like to keep it that way. When I had a blower door test done, there were low numbers when the door to the basement was closed, but as soon as we opened it, the numbers almost doubled so I know air sealing is needed!
Thanks in advance for any insights or experience in doing this.
Theresa
GBA Detail Library
A collection of one thousand construction details organized by climate and house part
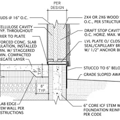
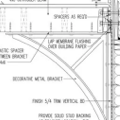
Replies
Theresa,
Trying to avoid the use of spray foam or rigid foam vastly complicates your task. I would strongly advise you to consider using some foam products.
If you want to use mineral wool, it has to be installed on the exterior of your foundation and the exterior of your rim joists, not the interior. If you install mineral wool on the interior, you will get condensation.
That means you will have to cover up your decorative rocks and brick.
If you insist on doing the air sealing work on the interior, you'll have to use rigid foam or spray foam.
Theresa,
You can airseal the wall, with a good parge coat. Lime based is great if you intend to insulate later with mineral wool. You can then use a fleece covered tape (like we carry at http://www.foursevenfive.com) to parge over (VANA, CONTEGA) to make the connections to the joist durably airtight. This will increase your blowerdoor number and airtightness of the entire building.
If you would like to insulate without foam in the basement, and the basement is dry, then indeed adding mineral wool and INTELLO is the way to go (see also: http://www.roxul.com/residential/how+to+install+roxul/basement). The big difference by using INTELLO compared to PE vapor barrier, it that the INTELLO smart vapor retarder will allow minor water infiltration in the insulation to dry inwards - this unlike foam board (en PE). those materials block this moisture in place and will not let it dry inwards. So a dry basement is a prerequisite, and INTELLO will let you insulate it without foam while adding a safety factor if small amounts of moisture do end up behind it.
There's no mention of the climate zone is here. Ideally there would be a capillary break and air barrier between any of the masonry and the fiber insulation (or other moisture-susceptible materials.) The appropriate ways of doing that can vary with climate. Can you share your location?
Take your mason's advice on the type of parge is needed based on the original mortar type. Since there are known gaps and you'll be covering it up, this is not something to just take a stab at. A good local mason has a much better handle on what's appropriate than the average renovation contractor.
Using cellulose anywhere below grade is risky, and using any fiber insulation in direct contact with the masonry (either above or below grade) is also risky, but it would be fine to use against the band joist, provided it has the appropriate interior side vapor retarders for the climate.
It appears to have vinyl siding on the exterior of the band joist, but what are the other layers (including any paints)?
I'll await climate zone information before commenting further.
Thank you, Floris. From what I had read, it seemed like Roxul and Intello would allow drying, if needed. I'd be interested in hearing what you think of this approach, Martin. Does having Intello on the interior change the rationale for only putting mineral wool on the exterior?
Theresa,
Floris works at 475 High-Performance Building Products, this country's most prominent distributor of Intello. So it stands to reason that Floris promotes Intello and feels that it is a great solution to many problems.
There is a judgment call here, and it has to do with your appetite for risk. If your basement is very dry, Floris's approach can work. That's why Floris warned you that "a dry basement is a prerequisite."
Mineral wool insulation does nothing to block the migration of moisture toward the cold foundation, so interior mineral wool raises the risk of condensation compared to spray foam or rigid foam. Intello reduces the risk, but it's hard to install Intello in a manner that prevents mixing of the air that resides between the fibers of the mineral wool and the basement air. Changes in temperature are enough to set up a pumping action that encourages air exchange between the air between the insulation fibers and the basement air.
I stand by my advice, because my approach is less risky than Floris's.
We could comment more with climate information...just a zip code would let us figure it out.
I think Intello is great stuff and used a bunch of it in my project. However, I think that it is much more effective in an above grade wall than below grade. In an above-grade wall, the drying to the interior happens when the wall is warm, and the Intello helps make that work. But much of a below grade wall stays relatively cool even in the summer, especially if it's well insulated. So you don't get the same driving force for drying, and it can be hard to get the Intello into the humidity range where it opens up to help facilitate the drying.
Another option is Foamglas, which is just what it sounds like, an insulation foam made with glass instead of plastic. It's completely waterproof, airtight, and won't support mold growth, so it's at least as good as foam for solving below-grade problems, and it's non-combustible, so you shouldn't need an combustion barrier. The downsides are that it's expensive and that it's new and few people have experience with it. I'm not sure I've heard of it being used for interior below-grade insulation, so you might need to work out some of the installation details.
There are many good reasons to avoid using foam, including avoiding toxic fire retardant chemicals, avoiding emitting high-global-warming potential gasses and avoiding supporting the petrochemical industry. If there are some of these that are higher priorities for you than others, we can help find foam types that avoid some of them. For example, EPS and polyiso don't have the blowing agent issues that XPS and closed cell spray foam do.
Hello Martin,
I was aware that Floris works for 475. It's helpful to hear the other view and your rationale was helpful. Still, hard to believe, there still aren't good, affordable non-foam options for old basements that usually have some dampness.
As Charlie mentions, there are many good reasons to avoid foam. It sounds like there isn't a viable way to do that right now so I'll have to consider the alternatives.
Thank you all for your input.
What's do-able or not is somewhat climate dependent, and we're still in the dark on that.
Hi Dana,
I thought I had given location, but guess I didn't. I'm in southern VT, zip is 05101.
None of this work is below grade. I'm not going to tackle that at this point. And I'm only insulating the rim joists right now. (And would like to air seal the above grade brick.)
One of the energy contractors said they've used EcoSeal spray sealant in the rim joists prior to insulating with Roxul. I know Martin had mentioned the risk of condensation when using Roxul, but I'm wondering if the EcoSeal would mitigate that. The cost is about 50% more than the rigid foam solution, something to consider with my budget.
Thanks!
The US zone 6A climate makes it tougher to do without foam, and may take some monitoring of how it's doing the first few winters.
EcoSeal is good for sealing up the cracks, but doesn't provide a vapor retarder toward the interior, so if you let the foundation sill& band joist run cold they'll load up moisture over the winter unless there is an interior side vapor retarder. It's has no moisture mitigation value.
There is some benefit from painting the interior side exposed wood with "vapor barrier latex", which will limit the rate of moisture adsorption from the entrained air in the Roxul. Before you paint it, buy a $35 2-pin wood moisture meter from the local box store, and make sure the moisture content is under 20% (under 15% would be even better.) Go ahead and insulate with Roxul, but sometime around half-past March pull the insulation and test a few spots, particulary on the north side, that gets no sun-warming, or sections where the wintertime snowpack was in contact with the foundation within 15" of the sill (which may be everywhere some years.)
If the moisture content is north of 30% at half-past April when it's warm enough for mold to start growing in spring it's a problem, but I'd expect that with VB latex on the interior side the moisture content of the foundation sill and band joist the moisture content will be a function of the outdoor RH and the moisture content of the foundation. Fortunately field-stone foundations don't wick as much moisture as poured concrete, so it's probably going to be OK. If the moisture content of the band joist & sill is under 20% by mid- April on all sides of the house the risk of problems are very low. With a leaky interior side air barrier you may get frost formation in the rock wool, but you'd be able to assess how well it's doing during the early-spring inspections. There are many existence proofs of band joists insulated with crummy R19 batts with and without facers that do not end up with mold/moisture problems, despite the risk. With a VB primer paint you'd be able to see the beginnings of mold growth long before there was a real problem.
The heat loss out of the above-grade foundation is going to be substantially higher than the heat loss through the band joist. A non-structural studwall with an exterior side air barrier that isn't susceptible to moisture (like housewrap or fiberboard) insulated with rock wool batts, and an interior smart vapor retarder would still work. If it leaks much air there may be condensation events or even frost formation on the interior side of the foundation or the air-barrier, but it does no damage.
Maybe Florin can get ahold of some Multipor boards. They're basically AAC boards; insulating and non-petrochemical, and used a lot in Europe. They don't seem to have made the journey over to the USA for some reason. If not these, then foamglas could work too. You'd just cover them with a parge coat or skim coat of plaster once they're up.
I suppose you could stack up a non-structural AAC block wall there too, but I'd think that would take pretty hefty budget compared to rock wool and smart vapor retarders.