How to insulate underside of roof deck in 1927 conditioned space

I have lived here for 18 months. First thing I did was re shingle to roof. Roofer is a pro and said decking was in great shape. Shingles are mid-dark gray in color. This is a 1.5 story home in central MN with the second story “finished” at some point with Homasote on the walls and ceilings. Homasote is a brand name associated with the product generically known as cellulose based fiber wall board, which is similar in composition to papier-mâché. It is in bad condition and needs to come down. There are two unfinished spaces behind knee walls that are accessible. There is a little bit of fiberglass batting under the roof deck but mostly newspaper from 1933.
The roof rafters in the exposed areas are 3.5 inches deep. There is no ridge vent. There is a single vent in both unfinished spaces. There are vent holes in the aluminum wrap on the soffit but I have no idea if they are actually functional. Contractor says that in a house this old they are typically blocked and useless. He thinks the best solution is to spray 3″ of closed cell foam on the complete underside of the roof deck making it a “hot roof”.
My original idea was to use 2″ rigid polyiso foam between rafters then another layer perpendicular to that taping all the seams. This seems a much more reasonable DIY project. Contractor says I would be asking for trouble. I can’t get anywhere near the code requirement on R value unless I reduce headroom in this finished space by 6-8″ with rigid foam “under” the rafters in addition to the spray foam. between rafters. Mostly I want to seal leaks and insulate better than the existing newspaper.
I am doing a lot of reading and my head is spinning. There are 4 windows, 1 heat vent and no cold air return. Co-worker is telling me I need to extend a cold air return up there from the basement ductwork. The house exterior is stucco.
Thanks for reading all this. I wanted to be as complete as possible. What would you do ?
GBA Detail Library
A collection of one thousand construction details organized by climate and house part
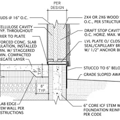
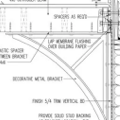
Replies
The contractor is right- cut'n' cobbled foam board between rafters have VERY high failure rates from tiny air leaks opening up, getting around the foam no matter how diligent you are. Installing 3" or more of an HFO-blown (not HFC blown) closed cell foam on the underside of the roof deck would get you to ~R20 in a much more robust, leak-free fashion. This part is not DIY, and it'll run something like $4.50 per square foot.
With the R20 of closed cell foam under the roof deck you can then add up to R15 of fiber tight to the foam and still have minimum dew point control at the foam/fiber boundary even in northern MN. In central MN on the zone 6/7 boundary it would have reasonable dew point margin.
That can be done with either 4" of cellulose, or cheap R19 fiberglass compressed to 4". One option would be 2x4s mounted perpendicular to the rafters blowing cellulose in netting. Another would be to make Bonfiglioni rafter edge strips with 2.5" or 3" polyiso foam and 1x furring through-screwed to the rafter edges with 4.5" cap screws to accomodate compressed batts. For an explanation of the edge strip approach see:
http://www.finehomebuilding.com/membership/pdf/9750/021250059.pdf
To to the higher air permenance of low density fiberglass, with the compressed batts you'll need to mount gypsum board to the furring.
A thermally broken R35 at center cavtity (in either approach) won't quite hit code performance on a U-factor basis, but it will be pretty close, and WAY better than just the 3" closed cell foam on it's own.
For tips on cutting foam board for the edge strip approach, see:
http://www.finehomebuilding.com/2009/01/29/theres-a-better-way-cutting-rigid-insulation
Thank you Dana for all the great info, advice, suggestions and general help! This is all really new to me and I want to do it right the first time. I spent this evening measuring and putting together a very rough estimate. It is turning out to be more expensive than I anticipated.
You mentioned this .."To to the higher air permanence of low density fiberglass, with the compressed batts you'll need to mount gypsum board to the furring." There seems to be a missing word at the beginning of the sentence. Perhaps..." to compensate for" the higher air permanence... I was considering shiplap boards. The real stuff. 3/4 pine with opposing rabbets on the edges to overlap each other. Would that do the trick instead of the gypsum board ?
My only hesitation about this approach is the encroachment on the headroom in the space. It's not great to begin with with the max being 80". This method would shrink that to about 76.5".
Mindy,
The shiplap will not serve as an air barrier. You might be able to install a vapor retarder and then the shiplap, but this approach is riskier. Dana will likely respond directly to your question and offer more information and advice.
Thanks Steve. I am still trying to wrap my head around this. I know I need to stop air flow. The "Hot Roof" sprayed closed cell foam is supposed to serve that purpose on the underside of the roof deck. My understanding is that I would not need further air or vapor barriers. Please correct me if I am wrong.
It would be an obvious benefit to get as much additional insulation up there as possible. I have discovered the method Dana described above is known as "Flash and Batt". I like it. I now understand the idea of the roof rafters being a thermal bridge. Any idea what the minimum thickness a foam furring strip needs to be to break that bridge ?
This may be totally unconventional but I am trying to get a balance of increasing R value and not losing a ton of headroom. If anybody has a suggestion on reducing the overall thickness of this assembly, I am all for it.
The closed cell foam stops air leaks. Alternating horizontal and vertical orientation of each layer would further slow down leaks of heated air out through the roof. I could do this not only to ceiling but also the walls that currently have no insulation. 1" rigid foam between rafter and furring strips would "Break the thermal bridge".... This is also very much within my skill set. I would only have to contract out the spray foam.
Am I crazy?
Thanks!
Hi Mindy,
Even if the closed cell foam is providing a perfect vapor retarder, your local inspector will likely want to see an ignition barrier. That is just my suspicion. Perhaps one of the pros will chime in.
Mindy,
I will remind GBA readers in a situation similar to yours that the best approach is always to install a continuous layer of rigid foam above the roof sheathing. Unfortunately, you installed new roofing before considering this approach. In your case, it's now too late for that option.
In general, an interior air barrier is a good idea if you plan to install any fluffy insulation (fiberglass batts, mineral wool, or cellulose) as part of your insulated roof assembly. Taped drywall is an effective air barrier, while 3/4-inch pine boards are not.
Thanks Steve and Martin,
Perhaps the jpeg I attached isn't actually visible ? What I am proposing is having the contractor spray 3" closed cell directly to roof deck and then I install an assembly of 2x2 furring strips attached horizontally to the rafter with a 1" foam spacer. Between the furring strips is 2.5" ISO foam boards. On top of all that with seams running vertically is 1" ISO foam boards. Next, is .5 drywall hung horizontally.
My understanding is that the drywall would be both thermal and ignition barrier. No fluffy stuff in this plan however I am not totally ruling that out. I could run compressed fiberglass instead of the 2.5" rigid foam. Save a bit of money but also loose a couple R Value units.
Martin, you are right about putting foam on the roof deck along with the new shingles etc..... At that time, insulation in the roof was no where near my train of thought. The shingles were falling off before my eyes and at the time the most important task was to get it watertight again so the interior damage could be repaired. This was a foreclosure that had been sitting empty for about a year before I bought it.
Thanks!
Mindy,
I suggest reviewing post #1. Dana really knows this subject, and he has suggested a couple of cost-effective (and safe) options for your climate.
It is my understanding (and I am just a homeowner like you) that the cut and cobble method is risker because, over time, the framing is likely to move and the foam may shrink. All this movement can create gaps around the edge of the foam.
Of course, it is your house. Don't do anything that will keep you up at night.
Sorry for the typos etc (I'm doing this all one-eyed with out-of prescription glasses this week due to recent eye sugery- not a big deal, but I'm not my best editor for the time being.) That should have read:
"Due to the higher air permanence of low density fiberglass, with the compressed batts you'll need to mount gypsum board to the furring."
Ship-lap planking is not a sufficient air barrier for low density fiberglass. A sheet of variable-permeance Intello Plus under the shiplap detailed as an air barrier would be fine, or a layer of gypsum board (painted with any standard latex primer)
Installing 2.5" of rigid foam board between the furring + spacer foam blocks severely impedes the drying toward the interior, and buys very little in terms of whole-assembly performance, despite the higher center-cavity R. Installing high R/inch foam where it is thermally bridged by R1/inch wood is never a winning strategy. Using thinner 1x furring and thicker foam spacer blocks with only fiber insulation under the closed cell foam is cheaper, more moisture-safe and comparable thermal performance.
Dana...I hope the eye surgery is successful and you heal quickly!
Thanks for chiming in. I will take your advice and go back to the original assembly you proposed. On the R-19 fiberglass that is compressed, do you reccomend faced or unfaced?
The drywall is the part I am least looking forward to. I have a goofy staircase and there is no way I am getting a 4x8 sheet around the corner and up the steps. Windows are not big enough upstairs. I'm not even entirely sure I can get a 2x8 sheet up the steps. You mentioned using Intello Plus "on top of" the fiberglass. If I did that I wouldn't need the drywall at all ?
Thank you !
The compressed R19s can be either unfaced or kraft faced, but not foil faced.
Intello Plus is a fairly rugged flexible membrane with variable permeance that won't create a moisture trap (the way heavy polyethylene can.) It can be detailed as an air barrier that has "reasonable" ruggedness in areas that aren't going to be used for storage or living space, with limited risk of accidental damage. It's not nearly as robust as drywall or OSB, but it's not as susceptible to incidental tears & punctures as 2-mil nylon (MemBrain) or 4 & 6 mil polyethylene.
Cool ! I appreciate all the help. I am trying to get the plan fully baked before I start the demo and reach a point of no return. The reality is that I may need to do this in stages. I love the fact that the Intello is fairly tough. This will be finished space but it is not actively used. Chances of damage before I get a final wall covering on will be very minimal.
One last detail question if you don't mind. In your first response to me you state "One option would be 2x4s mounted perpendicular to the rafters blowing cellulose in netting. Another would be to make Bonfiglioni rafter edge strips with 2.5" or 3" polyiso foam and 1x furring through-screwed to the rafter edges with 4.5" cap screws to accomodate compressed batts. For an explanation of the edge strip approach see:
http://www.finehomebuilding.com/membership/pdf/9750/021250059.pdf"
I understand the idea behind this but am a bit concerned about the structural integrity of using a 3" thick x 1.5" wide strip of foam behind the wood furring that will ultimately be used to secure my final wall covering. I am mostly concerned about the sloped and flat portions of the ceiling. As I think this through I believe this really comes down to the type and length of screw used to secure 1x wood to 3" foam to the rafter. You mention a 4.5" cap screw. Might you have a specific example ? Would this work? https://www.homedepot.com/p/GRK-Fasteners-5-16-in-x-5-1-8-in-Rugged-Structural-Screw-40-Piece-per-Pack-112231/203533480?MERCH=REC-_-PIPHorizontal1_rr-_-202268258-_-203533480-_-N