Humidity issues….suspecting brick foundation

I am more or less done with the energy aspects of a deep energy retrofit (DER) of my home (built in 1910) and now experiencing humidity issues. I am in NY in zone 5A. This is going to be a very long post as I am trying to get as many details as possible.
DER involved 6″ of exterior xps down to the base of the brick, basement is approximately 6.5′ deep. Perforated drain tube was installed and the foundation was backfilled with about 1′ of gravel, 2′ of sand’, then 1 foot of gravel- the foundation sits about 2-2.5 feet above grade. Above grade consisted of taped huber zip, 5.5″ poly issue first two layers taped, tyvek, then furring strips. Tyvek was installed because the polyiso was glass fiber reinforced paper faced, and it is there to protect the polyiso. Windows are serious fiberglass, mostly casement but single hung’s at porches, U= .22. They are outies, installed in 2×12 bucks.
It has a 12:12 roof and the attic was poorly converted into a living space with a dormer and the roof rafters went right to the top plate. I removed the dormer and restored it to a vented attic and raised the area above the top plate (changed the slope to 5:12 partially down the roof) to accomodate about 20″ of blown in cellulose. I installed tyvek on the floor as an air barrier, then spray foamed the knee wall bottom plates and the perimeter of the tyvek to ensure it is was fully tight. All tyvek seams and staples were taped. I then installed 20″ of blown in cellulose. The tyvek went in, then it was a few weeks before foaming, and then a few days after the cellulose was installed. As soon as the spray foam was complete, excessive condensation started appearing on the windows – they were dripping. Rough conditions were 60 F inside and 30-40 outdoor.
I was not too surprised about the dripping as there was no ventilation, at the time I would open the windows for a bit, this helped to an extent but it got cold and it was not a permanent solution. A few weeks later I installed a Venmar 1.5 EKO HRV with supplies to living spaces and exhausts in the kitchen and bathrooms. There are also two supplies and two exhausts in the basement I am struggling to get it balanced as one port will not provide an accurate reading- I am trying to resolve with Venmar. However I ran it at high speed and it resolved the condensation issue. This was mid December, and now that, barring this week, temperatures dropped, the condensation has started again. It’s not as bad as before but it is still an issue.
I borrowed a laboratory class hygrometer, and had RH levels of 70% in the basement with 55 degrees. In the living spaces the RH is about 60% with temp of 60 F. I Installed 10 mil plastic on the basement floor and brought it 1-2′ up the foundation wall, installed a furring strip and sealed the plastic against the brick with a polyurethane sealant. RH dropped a few percent (if it is not noise in the reading), in the basement and remained fairly consistent in the living spaces.
The basement foundation is about 1 foot wide and 6.5′ deep and made of brick. When we dug it out we found there was no footer and the bricks are sitting on the dirt so there is no capillary break. To make things more interesting all of the stud cavities were filled with nogging, a lower grade brick, which is resting on the foundation. It is ballooned frame so the nogging runs pretty much non stop from the foundation to the top plat. Some of it has been removed but most of it remains as it is desired to be the finished look. The nogging served as a fire break and a crude air barrier/draft stopper. Additionally the property has a well and the water table is approximately 15′ below the basement floor.
I am certain the high RH is the issue and I am unsure how to address this beyond a dehumidifier- assuming that would even work. Since there is foam on the outside of the foundation, I believe I cannot run plastic all the way up the interior wall as this would prevent drying. However, one could argue drying could occur through the nogging. I am concerned that with the HRV out of balance it may be increasing the moisture transfer between the brick and the ground, however I am hesitant to believe this is the dominating effect. Any thoughts?
GBA Detail Library
A collection of one thousand construction details organized by climate and house part
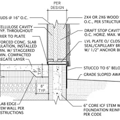
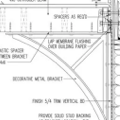
Replies
Upstate,
This is the type of moisture issue which is impossible to diagnose over the Internet, but your analysis and conclusion make sense to me.
It's possible to retrofit a capillary break (for example, stainless steel flashing) in an existing brick foundation. Here's how it's done: a section of brickwork, perhaps 12 inches wide, is dismantled and a length of flashing is inserted. Then the brickwork above the flashing is restored. Once that section is done, the next section is done in the same way. Working your way around the basement one section at a time, you can eventually install this type of capillary break all the way around.
It's not fast or cheap, but this approach may be necessary at your house.
A couple of interior basement photos could help. I'm assuming the balloon framing begins at the 2 - 2.5' above grade? Is there a bottom plate to work with?
Not being certain of the exact details, it sounds like Martin has your answer.
A slightly faster and possibly cheaper solution may be to cut a kerf in the brick with a demo saw and slide metal in....and/or inject some sort of product to make that well-needed capillary break. Your 10 mil plastic in the basement should reach that break.
Short of that, it sounds like you'll always have a constant battle between a house that is now sealed like a drum and a dedicated moisture source.
Enjoying the freakishly warm weather this week?
http://collectionsconversations.wordpress.com/2012/09/18/1416/
Brick and mortar wick moisture into old buildings
Why not insulate the basement ceiling joist bays and isolate the basement from the upstairs with an effectively applied vapor barrier on the basement ceiling. This will break the climate connection between the basement and the upstairs. You can run them at different, appropriate temperatures and humidity levels and "drive" them seasonally.
It might be easier and cheaper to insert a vapor break between the top of the brick foundation.
Your house was built at a time when the two spaces (upstairs and basement) were not conditioned. Basements were foundations not living spaces. You might consider using a separate HRV in the living space of the house and then dehumidify/ventilate the basement as a separate and independent space (it's an open system; whereas the upstairs is a closed system)
For climate quality and protection of the wood elements in the building, I would be more concerned with keeping the ground humidify out of the house than I would be in I incorporating the basement into the house.