Exterior Insulation or Zip R Only

IDK what to do, colorado build at 10k’, cold dry breezy winters, zone 7, exterior insulation or zip R? I’m in the planning stages, sketches and notes, no architect yet. My build is remote, savy contractors will be tough to find. I know that I should be planning about 2″ or so of exterior insulation on my 2×6 wall system, but I’m afraid the few contractors I can find will not be familiar with a proper install and totally mess it up as well as overcharging me because the window, door and fiber concrete siding attachments are totally foreign to them on insulation. How crazy would I be to simply use zip R (2″ or so) and then siding? Our winters are very dry and site is on side of mountain and consistently breezy.
GBA Detail Library
A collection of one thousand construction details organized by climate and house part
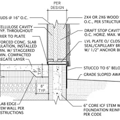
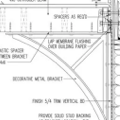
Replies
Zip R9 should work well provided you have a warm side vapor retarder. If you want to skip the vapor barrier, you need a bit more rigid insulation in your climate (R15):
https://www.buildingscience.com/documents/building-science-insights/bsi-100-hybrid-assemblies
2x6 with R9 rigid would get you around an R28 assembly. You can get pretty close to that with 2x8 24OC with HD batts.
That would be very close to standard assembly without having to deal with rigid foam or any window/siding details. If your siding can be hung 24OC you can even look at fiberboard sheathing which would get you pretty close to your original assembly R value.
If you do go with Zip R, make sure the installer takes care and does not overdrive the nails. Very easy to to do and it greatly reduces the strength of your walls.
With 2x8, you could get r30 Rockwool, minus thermal bridging. Add in a service cavity of 2x4 over Intello and add another r15 of Rockwool. Just seal the outside with Mento over plywood and seal/tape/caulk all the joints. 2x6 walls at r23 with r6 on the interior of Intello would be pretty good too with a service cavity.
Air tight, and vapor open on both sides.
Putting aside the question as to whether Zip R-9 is enough for your climate zone, once you get to 2" of Zip R, there's more to micromanage with your framers. You need a 3 1/2" nail for Zip R-9. Not sure what's common out there, but some framers' guns stop at 3 1/4".
I mention this because you're worried about quality contractors. (Believe me, I understand this concern.)
If it were my build and I wanted to avoid exterior insulation but needed a pretty high R value, I would probably lean towards a double stud wall (https://www.finehomebuilding.com/2012/05/17/double-stud-walls) with fluffy insulation of some sort.
Rckymtn,
I am at 8,000 ft and wind can be quite intense. Not many well protected locations at 10,000. Zip R needs to be done carefully per their specs to produce the racking resistance needed. The higher the R for zip the more careful you need to be. Despite the dry climate here, I agree with Akos that more on the outside would allow you to skip the interior vapor barrier. Being off grid will place a premium on your energy expenses. Even chopping wood will wear thin if you need to burn 4 cords to survive. Paul is right about quality workers. A double wall might be the safest course if you are remote.
We are in a very close situation. Colorado, 8300 ft, zone 7, dry and breezy/ windy near the base of mt Evans
We went with 2x6 stud wall with r19 fiberglass. Plywood sheathing with tyvek, windows set into this so it is easy for the framers as it is a standard install.
Then we put 3" rockwool on the outside for an additional r12 - total r31.
Siding is Boral truexterior over 3/4 ply sleepers as a rain screen.
carpenters wanted blocking for the furring so we used small blocks of rigid/. they did not trust attaching over the rockwol.
project is still in process with interior finishes, but so far seems to be working well in terms of performance.
The only hard part was getting the carpenters to understand the head flashing and building such a deep sill pan.
Thank you all for your posts, sorry for the delay. Although my county is technically zoned 6B, I believe I'm really zone 7 due to elevation. The ZipR9 has me on the fence, decoupling the sheathing from the framing gives me pause, as well as overdriven nails. Akos, your reference to a 2x8 24OC HD Batts and fiberboard has me intrigued.
What about the Bonfiglioli wall... furring the inside with 1.5" foam (ripping zipR) could I keep 2x6, go to 24OC and R-30HD Batts? it sounds like alot of bang for the buck? But is it safer from a moisture standpoint compared with zipR?
That would work and gets you a pretty decent R value assembly (~R27). The labor would be a fair bit more than 2x8, so it is probably only worth it if you can DIY the strips.
With either assembly 2x8 or 2x6+strips, your wall can only dry towards the outside, you should a rain screen under your siding to add a bit of extra drying capacity.
Unlike the wall above, a wall without sufficient exterior rigid insulation for condensation control relies on having a solid warm side air and vapor barrier to keep your sheathing dry. With a bit of attention to details this can work. If you don't want to have the amount of rigid this takes, a better assembly is to use permeable insulation on the outside (ie mineral wool, unfaced EPS or fiber faced polyiso).
Useful for building good walls, even when > 6":
See Table 2 A or B here.
If you want to mix techniques (lower perm interior plus some exterior insulation), then there is the 2021 code:
https://www.continuousinsulation.org/content/2021-ibc-and-irc-adopt-improved-vapor-retarder-requirements
I haven't seen a good analysis of Zip-R moisture performance that includes the joints. No doubt dry air helps.
Zone 7? Go exterior rockwool comfortboard 80.
Installation isn't complicated.
https://www.rockwool.com/siteassets/o2-rockwool/documentation/technical-guides/residential/comfortboard80-installationguide.pdf
OK, a little background. Its taken me many years to find and purchase the "perfect" land (attached). I am environmentally conscious, I did not want to by a piece of beautiful pristine Colorado land and destroy it by bulldozing it and building a house... After countless letters to property owners, I finally found an existing burnt down house on a parcel scorched by the spring fire in 2017. The spectacular view faces 10 degrees east of due south, looking over a large meadow and the expansive Spanish peaks. Had it not been for the fire, I would have likely never be able to afford such beautiful land. That said, I now have only a 100K to get the house to Lock-up, (dried in). I don't even know it that's possible, hence the investigation. The house is 1016 sf, passive solar (to the extent I can afford), the 100k will have to cover a shallow frost protected slab, the framing, the roofing system + roof, windows & doors + exterior siding... Just the necessities to get it dried in . Site prep (restoring the existing well, septic, grading and debris removal is covered elsewhere). This is the full extent my savings for this dream (cash) will allow. After the 100K, I will take the months (or years) necessary to finish the inside myself and cash flow it.
This is why my keen interest in keeping this simple for the contractor. I truly need the most cost effective, green, and simply way to get this to lock-up while attempting to not compromise insulation. I dreamed of a super tight house built to passive house standards, with the price of the land, reality will dictate something less.
Back to the wall system, ZipR9 vs Exterior Insulation. The bonfiglioli wall had me intrigued because its a detail I could do myself after lock-up and get right. The ZipR9 had me intrigued because on the surface it seems like an unsavvy contractor could properly estimate and execute.
Questions:
1) Do you think a 2x6 on 24" bonfiglioli wall would require engineered plans in Costilla County Co?
2) The "rainscreen" on a 2x8 or bonfiglioli 2x6, does this necessitate furring out before the fibercement siding? Or is this a product that is "stuck" or fastened to the exterior? (trying to understand the additional contractor work)
3) In the scenario of 2x6 Zip R-9, could I get away without the "rainscreen"?
My intent in all the questions is get this build to lock up in a economic fashion that minimizes contractor risk but can still provide a good degree of performance.
When tight on budget, stick to standard build and materials. Zip R is definitely not it.
Since you mentioned fire, the one thing I would spend extra cash on is getting the building more resilient on that front. For example, denseglass sheathing is not much more material cost but builder might charge extra if they haven't used it before. More important is roofing, big item that needs careful attention.
1) Only your local building department can answer that. Even if you do require bracing on both side, you can do it with a let in bracing on the inside of the 2x6 followed by the strips.
2) There is also crinkly house wrap, helps and not ideal, which would be the minimum I would include. There are a number of better rain screen products such as Slicker Classic that go over a standard house wrap. There are also some that are house wrap and rain screen in one (Driwall Rainscreen). Plywood strips or 1x4 strapping is usually the budget option but more labor. If you don't mind a bit of work on a ladder, strapping is pretty simple to install over house wrap before the siding goes on.
3) Rain screen helps with the durability of both wall assembly and siding. I would include it no matter the assembly. You don't need a big gap, even a 1/8" gap will make a big difference.
What would be pros and cons of using denseglass sheathing vs plywood? I've heard of gypsum sheathing but have never actually seen anyone use it.
I tried to check out Driwall Rainscreen but there are no specs about the WRB aspect on their website. They talk about rainscreen aspect only. Can't find permeability, wind resistance, etc.
> Driwall Rainscreen
Looks like it's a drainage mat that you put over a WRB - it replaces furring. But maybe there are other versions.
Densglass is commonly used for fire walls here, any exterior wall that needs a fire rating. Since it is structural sheathing, it works for bracing your walls similar to OSB/CDX.
It significantly more permeable (~20 perm) than plywood (10 perms) and OSB (2 perms) which adds a fair bit of drying capacity to your wall.
Install is the same as interior drywall but it can be nailed up which significantly speeds up install.
My only beef with it is that it is itchy (fiberglass facer after all) and heavy. Since it doesn't hold nails, all siding needs to go into the studs or you rain screen strapping.
Thanks. Where do you live? (My architect said he's only seen it here on a couple commercial projects.)
I'm in Toronto. In urban areas houses are much closer sometimes needing rated assemblies for exterior walls.
In places where land is measure in acres, I doubt anybody in residential would have heard of it.
Hi,
As mentioned above - a double stud wall is the simplest & a very conventional assembly. The width of the wall can be set to get a lots of insulation. It can be dried in then the inside wall installed later, as budget allows.
I'm in a similar climate and yes, builders are not used to non-standard walls. I am doing 2x6 with Rockwool, and 2" exterior Rockwool. The biggest concern I hear is about detailing windows in a thicker wall, so I introduced them to Thermal Buck.
I am debating a strapping rainscreen vs a drainable WRB housewrap because we have very little rain and my wall can dry to both sides.
I am for a double wall, this is quite an extreme climate so a minimum of R-40 is in order. (3) R-15 batts get you to R-45 in a 10 1/2" wall, can't go wrong. Plywood exterior sheathing, 6 mil poly or 8 mil Teno air barrier will perform nicely in this arid environment.
Look into T-studs. I just did a renovation on my home and used zip board. IMO I don’t think zip board is worth it. You have to seal every puncture and edges for it to work properly. I would think about using 1” foam sheets first and osb over it. You are still creating the thermal break without the price tag.
mal, I think you've actually got all three points backwards.
1. T-studs are a cost premium and this is a budget project. Also, I don't really see any advantage in using them in this application that would overcome their shortcomings. ...if you could even get them. I've still yet to see them in the field anywhere.
2. Zip is very much worth it if you need to get a good air seal. What punctures were you sealing? Nails? You don't need to. Just the panel seams and window openings which you'd have to flash anyway.
3. Tacking up foam sheets and then OSB and then housewrap is way more work for a far inferior end result compared to just using Zip-R. I don't even think you'd save any money doing it that way.
Ok. So t studs aren’t available where you’re at. Fair enough. But back to the zip. Yes all the nails need to be sealed. Why do you think they sell a caulking. Zip is nothing more than osb with a coating. I’ve seen it for myself. I used staples to attach mine. Every staple penetration is swollen because I didn’t seal it. Not sure how you figure that osb and ridgid foam would be inferior. In fact just the opposite. Putting the foam vertical then taping the joints and osb horizontal. There would be zero air penetration. Just because something is faster doesn’t make it better.
mal, Not to get into a pissing match here, but to explain my points a little better...
T-studs got a lot of attention from Instagram and social media influencers, but not actual builders. They're hard to find anywhere, cost premium, and have a lot of limitations especially when it comes to routing wires or pipes, or even doing simple things like cabinet blocking. And for what real benefit that can't be achieved otherwise?
I've used plenty of Zip myself. A few homes built with it including my own. We're in a seismic zone so have very specific nailing schedules and can't use staples. That said, the nails are self sealing and a few words to the framing crew at the start will keep you from having too many overdriven nails. Even when a nail is overdriven on standard zip it's not an air sealing problem, but a shear strength problem. Also, the edges of the panels are taped so that covers those leaving only field nails exposed. Not a problem and not a need for caulk.
As far as using separate layers of foam, OSB, and WRB, the reason I believe that approach is inferior is that you are doing triple labor by separating your layers and you don't have a bonded panel but three loose layers. You have to connect those layers leaving the opportunity for increased air leakage, but more realistically increased opportunity for error or omission. Labor isn't free even if you're doing it yourself...opportunity costs.
I will admit that I lack firsthand experience using Zip-R, again seismic concerns keep a lot of us here from trying it just yet. I know there are challenges and also tricks to making it work, but it's a proven product in less seismically active regions.
If I was the OP here, would I choose Zip-R? Eh, maybe but probably not. Zip? Yes. In a high wind area I'd want a good air seal.
I'm also in climate zone 7, northern Minnesota. I'm a fan of standard Zip nailed directly to the framing. This becomes the main air control along with the WRB. I would then add 4 inches of Rockwool's Comfort Board 80 which would get your exterior insulation to R-16 for a 2x6 wall. If you are able to get to a minimum of R-15, you can eliminate the interior vapor control product. The good smart vapor control products on the market are expensive, part of the savings from eliminating them will help offset the cost of the exterior insulation. Still will need a class III vapor control on the interior, some low perm paints over drywall will qualify. Rockwool has building scientists on staff that can help you with moisture modeling for your climate if you are concerned about moisture on the inside of the sheeting. Because the Zip is the WRB and rockwool doesn't care if its wet or dry, there would be no need for another water management product outside the ComfortBoard as long as you can address the window and door openings. I've used ThermalBuck in the past for windows, had good luck with their product. I like using 1x for a vented rain screen and also for siding attachment. A second, less costly option would be to build 2 x 4, which would require less exterior insulation, code specifies R-10, drawback is your total R-value for the entire wall assembly would be less. R-21-R25 depending on the cavity insulation used. Your correct with the difficulties in finding a builder who has installed thicker exterior insulations. It's not difficult, but the details need to be well thought out and their are a few tricks.
Note that Comfort Board 80 is far more expensive than unfaced EPS.
Rockwool Comfortboard 80 doesn't care if it's wet or dry, but does it care about wind?
Ok, drinking from a firehose here... (and I thought trying to figure out my roofing system was going to be most challenging...)
1) Double Stud: How could it be possible the extra cost and expense of building a double stud wall and the added complications of dense packing it could be more cost effective than a single layer fo zipR with a warm side VB? Or is the recommendation merely based on the possible issues the ZipR has with possible moisture in my zone?
2) The T studs are sweet, but I cant see that as economical compared to doing a double stud, and I cant see double stud economical compared to ZipR.
3) Since no one seems to screaming the praises of ZipR for a econ build in my zone, I'm considering 2x6 w/ standard zip for tightness, 3-4" of comfortboard 80, 1x strapping with thermalbuck, then my fiber cement. I really like these products, but price has me shaking my head...
PS: More background: I have lived in a 9" D log cabin off grid for 16 years at 10,020 ft less than a mile from this new property. This requires burning no less than 9-12 cords of aspen and fir every winter. Its a heaping wheelbarrow every day. I used to think that because I was "off-grid" I had less impact. As time progressed my winter carbon footprint began to eat at me.. Now, I just want to help, not detract from the environment.
Back to walls... the point is, I know this area well, in winters we kept two water kettles on the woodburner to get the humidity up to a more comfortable level. My dry cracked hands painfully split deep into my finger tips and knuckles every winter. My wife would say my snoreing was 2x louder in winter. The snow is never in flakes... its a fine dust that comes down by the feet, like glitter... I never covered the firewood, in winter you just brush the snow off and clap it together, there is no moisture in it, no problems with creosote, everything is so dry... it lights instantly and burns hot. I can't imagine that moisture is going to be an issue... Up at the new site, wind will be the issue, wind chill will be the new issue, the lack of trees and protection will be an issue. But wet walls will not... And hopefully, attempting to keep the cabin warm will not.
A well sealed building with people in it can have high humidity issues in the wintertime, with only two people this might be less of a problem. If your building is tight, doesn't matter how dry the outdoor air is as it won't get into the house, thus it won't help with keeping your walls moisture free.
The benefit of double stud is that it is simple to build and easy to explain to your contractor. Dense packing is generally only worth it if it is low cost in your area. The double stud walls I built were insulated with batts.
Zip R is simple if your framer is familiar with it and can take a bit of care with the install. This is rarely the case ie:
https://www.greenbuildingadvisor.com/question/badly-overdriven-nails-on-zip-should-i-wrap-house
If you can find somebody that has built with it before, it is a great way to build an energy efficient building. Material cost is more but saves a fair bit of labor.
Rigid mineral wool is definitely not a cheap assembly either. Never mind the material is spendy, it is still somewhat squishy. This means you need to tweak every screw in your strapping to level the wall otherwise the siding will be wavy. Great if you can DIY, but you are paying for install, you'll have a hack of an expensive wall. This stuff is intended for commercial buildings where it goes between metal Z grits not holding siding through strapping.
My budget decent R wall is 2x4, taped CDX, 2" rigid roofing polyiso , WRB, strapping. This is exactly the same thickness as a 2x6 wall so you can use standard doors and windows. About the only special detail is the small buck you need around your windows and doors. I find it simple to build but your local builder might think otherwise.
Akos, imagine my pensive nod... I see the value here... Yes, a good budget build that excludes the premium names yet balances function, execution, and material cost. Im getting my head around exterior insulation.
Wouldn't you be concerned about condensation with the non-permeable polyiso?
I read this...needless to say I'm sufficiently terrified this will be my framing crew... I will not question why zipR is not easy or cheap anymore...
https://www.greenbuildingadvisor.com/question/badly-overdriven-nails-on-zip-should-i-wrap-house
When the budget is that tight I say cut the number of square feet to almost tiny house size with a drawn plan for the next 3 or 4 expansions to get to your full dream size home.
Note in most locations you would not be permitted to live in an unfinished building. Make sure the county will allow that before proceeding with that plan.
The way I see it the big downside with Zip+R is the way it weaken the building structurally.
The reason your current home is so dry is because so much “warm moist” air is leaking out and being replaced by colder and drier air. Hopefully your new home will be much less leaky. It is very likely that the first winter you could have excess humidity from the new building materials.
If you will heat the new house with wood be sure that you make provisions to supply the stove with the outside air it will need this is no small feat in a high performance building. It would be best to find a stove that has its own supply connection.
Walta
Thanks Walter, I'm beginning to understand this moisture issue. New build will be grid tied mini spit, 1000sf, and perhaps I don't need such a tight and insulated house that I can't even reliably light a small efficient, externally vented, wood stove. Great advise in this thread, I'm rethinking everything...
ComfortBoard is relatively expensive and hard to source in parts of Colorado, but is of course also very good for fire resistance. It can also be hard to find (economical) dense-pack insulators. You can get used iso for exterior insulation in Denver from https://www.repurposedmaterialsinc.com/polyiso-insulation/ Their stock comes and goes, and it you're in N Costilla Co it might be worth the drive. The used iso may be fiber-faced, which I think can't (??) be taped, and is vapor-open.
Here's another reason for a good think :). I'm doing a zone 6 build in N.H. and have settled on a super insulated slab, double stud, zip exterior with all roof overhangs added After air sealing.
With the zip as the air control layer like this....you would be amazed at how tight the house will be.Depending on your skill level, you can have the contractors build the exterior shell and bearing walls, then you can build the double wall and partition walls.
In your zone, in a tight house, the addition of a Masonry Heater will reduce your Btu load to about a wheelbarrow a week. Russian stove, Swedish stove, Finnish stove. Check out rocket stoves also. Many different names and designs are available. I would definitely add exterior air to any fireplace or stove. You don't want to be sucking air through your doors and windows to feed the heater.
An Erv or Hrv might be needed later down the road for interior moisture control, just put a plan in place to add easily after the walls are sheetrocked. Good luck.