Improvement on the Lstiburek Ideal Double Stud?

Hi all. Please see the attached PDF of a variation on Joe Lstiburek’s Ideal Double Stud Wall design (https://www.greenbuildingadvisor.com/articles/dept/building-science/lstiburek-s-ideal-double-stud-wall-design).
I am trying to go for something a bit quicker and less labour intensive to build, but that is still very vapour open to the exterior (and occasionally interior) to overcome the usual double stud wall shortcomings.
Please fire away with critiques. The main problems I see are:
– The thermal bridge around the entire perimeter at the floor system, from the multiple layers of sheathing running out to the exterior face
– How to blow in the dense-pack cellulose, as ideally one can net the interior face to visually inspect the quality and consistency of the blow-in as it is being installed, and also so that the building inspector can actually see it and inspect it.
Other than those two things, I am pretty confident that this would be a very cost-effective, and high performance wall without the cold/wet sheathing issue associated with typical double stud walls. Also much faster/easier to build from a labour standpoint that building both walls separate from one another.
Climate Zone 4 Marine, +/- 3500 HDD’s, in Canada (basically same as Seattle).
Thoughts?
GBA Detail Library
A collection of one thousand construction details organized by climate and house part
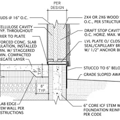
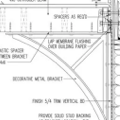
Replies
Burke,
My feedback:
1. I see no advantage to leaving the joints of the 1/2-inch plywood sheathing untaped. Airtightness is always good. Two air barriers do no harm.
2. It seems that you plan to install compacted gravel on the interior side of your foundation wall, and that this compacted gravel will be level with the bottom plate of your wall. This gravel will be damp, so your detail makes no sense to me. You want to keep that gravel well below your wood framing (to avoid any possibility of wood rot). Why is the slab elevated?
Thanks for the comments Martin.
I might consider taping the interior plywood seams, but it gets very hard to do once the walls are assembled and stood, because outside corners will have the sheathing interrupted by adjacent/connecting stucs, and they will be difficult to get at since they will be inside the double stud assembly, with only a 4" gap between the two walls to get at them. Since I really want to build the walls as a pair and stand them together, this makes air sealing that interior layer very challenging to do once all the exterior perimeter is standing. If one can't confidently air seal all of the connecting seams in that layer, there seems little point in connecting the seams in the field of the wall when it is laying on the ground without the outer wall framed on top it if yet. It might be worth trying to tape the first two walls at a corner, stand them and then see how hard it is to seal that corner to connect them. If it is in fact doable, then I agree, it would definitely be worth doing.
The slab is elevated so that there can be a full and continuous thermal layer connecting the walls and and the underslab insulation. The ¾" layer of plywood that runs from the top of the slab down the inside face of the foundation wall would be completely covered in a thick, durable layer of peel and stick, which would lap well down onto the concrete face. This protection, in conjunction with using a very free--draining crushed rock layer, and the fact that the top of the foundation wall and this rock layer would be 8" above exterior finished grade, makes me feel like there would be little to no moisture in the vicinity of the framing. Does that sound prudent, or does it still make you nervous? I have been wondering if there is anything in the code barring that practice, but since pressure treated wood foundations are allowed in the national Boulding code, I figured this is not nearly as bad as them!
My thoughts were the same as Martin's, plus one more suggestion. The additional suggestion is that fiberglass is a poor match for a service cavity, as fiberglass is notorious for being hard to install well around plumbing and electrical stuff. Mineral wool would work better. But it could also be cellulose again.
On Martin's point #1, the second air barrier, that plywood layer is a great opportunity for a robust air barrier, so I'd go ahead and take advantage of it.
On Martin's point #2, I think I understand what you were thinking--trying to make a floor/wall intersection with minimal thermal bridging. And trying to solve the damp gravel issue by running the peel and stick down into the gravel region. But in your design, that interior bottom plate will be cool, at ground temperature, all year. So sometimes it will be below dew point temperature and will accumulate moisture, and it will never dry. So even if that peel and stick layer is perfect, I'd expect that plate to rot.
Burke - I enjoy looking at your posts as i have been playing around with double wall plans for a future house, and like the air barrier in the middle. I'm in Zone 6 and am leaning towards a 2x6 exterior load-bearing wall, inside sheathed with plywood air barrier, outside sheathed with plywood, wood boards, gypsum sheathing, or fiberboard. This could be put up fairly quickly, and windows (and doors ?)installed, to get house weather tight fairly easily. Hanging 2'nd floor off this wall leaves a decent amount of insulation outside the rim. I'm planning to use mineral wool for increased drying potential. Once the inner air barrier is sealed, and house is weather tight, the second, 2X4 wall can be installed, with 2" space between.I know you'd like to have both walls up together, but the advantage of separate building is that any builder can do the first wall, one person can carefully detail the air barrier, and any builder can then build the 2'nd wall.The second wall lies on the slab and is not load bearing. The stem walls would be stepped to be only 6" at the top, supporting the 2x6 wall, and then 3" of foam ( or mineral wool board) at the slab edge, that ends up being co-planar with the inside of the double wall. The top of the foam exposed at the doors is a troublesome detail, and could be fixed with the doors hung in the middle of the wall with the sill over the foam, or doors hung as "innies" with an extended sill over the foam. I agree with Martin and Charlie that your slab detail is troublesome. Your plan would work with a wood floor system and crawlspace. I like the idea of 1 step up into the house, both practically and aesthetically. Your plan, would need at least 2 steps. Some day, I'll sketch this out and put it on the site - I'm not savvy enough with computers to do that now. Good luck to you. Keep sketching and thinking about these details.
Burke,
Unlike you I haven't pre-built double stud walls so bear with me...
Could you still make them sufficiently rigid to stand as one piece by temporarily tacking strips of plywood at both ends, tying either the studs or plates together? Once the walls are up, the subfloor and plywood ceiling would permanently hold everything in place.
Lowering the slab so the insulation was a couple of inches below the foundation top would seem to me to alleviate Martin's concerns. I'm not keen on the elevated slab for another reason: One of the main benefits of slab on grade is the possibility of step-less access, but this one ends up with a situation similar to using a framed floor.
As a general comment I wish more of the discussions placed as great an emphasis on build-ability as you do.
Thanks for the feedback guys. It's terrific to have an instant, experienced sounding board for feedback!
The more I consider air sealing that ½" plywood layer on the outside of the inner layer, the more problematic I realize it actually is. Firstly, there is absolutely no way to get to the corners, or joints in separate straight wall sections without leaving the outermost exterior gypsum layer of sheathing off. And if there is one thing that is slow and impractical, it is standing bare stud walls on a two storey house and then going around with ladders, planks, scaffolding, etc and sheathing all of those walls after the fact. I always shake my head when I see framers still doing that. It's like watching someone use a handsaw to rip a sheet of plywood when you know that the circular saw exists. So, having both stud walls sheathed so that they can be stood as a pair means that the ½" plywood layer is 100% unreachable for air sealing where they butt into one another. So, we are left with the outermost sheathing layer as the (single) air barrier. But considering that the cavity behind it will be insulated with dense-pack cellulose, the air-tightness does gain some backup support. I would love to seal that inner layer, but I have to be realistic about labour costs and practicality.
I appreciate the concern about the backfill being right at the level of the bottom plate that everyone is expressing. It was for me too when I first thought of it some time ago. The more I have considered it, the less concern I have, but perhaps dropping that backfill layer down a few inches would be prudent. It would also mean the finished floor height would get a littler closer to the exterior grade, meaning less elevation gain to have to deal with at doors. Definitely a fair point.
Charlie- Do you feel there is much of a difference hygrothermally between my detail at the interface of framing and foundation wall as opposed to the mud sill on a house with an unconditioned crawlspace and an insulated, air sealed floor system place on top of it? Those mud sills don't automatically rot out, and they are also completely cold and susceptible to moisture. When Ido see them rotted out on jobs, it is almost always because the the exterior grade has been piled up by the homeowner against the framing/cladding covering that rim board. That, or because there is no suitable moisture barrier between the concrete stem wall and the mud sill. I would absolutely peel-and-stick the top of the concrete wall, and I may even use a treated plywood plate and treated bottom plates of those walls just to be extra, extra cautious. Do you agree that that would remove any issues at that location, or am I understanding the conditions/moisture dynamics incorrectly?
As for the fibreglass batts, I agree that any batt is hard to fit around wiring and plumbing well! Something I like to do is have my electrician run all his wires at 4' above the top of the bottom plate. That way, the insulator's bottom batt will just butt up to the underside of the wire runs, and the top batt can just sit down on top of it. No splitting batts! It's a bit unconventional, but worth it if you actually want a good batt insulation job. Plumbing should of course be avoided if possible in exterior walls, so it poses less of a problem, as it is not nearly as plentiful an obstacle.
Kevin- I'm glad you're enjoying the double stud brainstorming! Your wall system also sounds like a good one, and quite build-able. The only tricky part will be connecting the plywood layer on the inside face of the main floor 2x6 wall to the plywood layer on the upstairs wall above the floor sheathing. You will have to seal that lower floor interior sheathing to your wall top plates, seal every single butt joint in all of your top plates all the way around the house, seal those top plates to your exterior sheathing layer, install your joists and subfloor, seal the exterior sheathing to the subfloor, seal every single seam in your subfloor back until you are inside the point where your upstairs interior sheathing will be, build and stand those upstairs walls, and then seal that interior sheathing to the subfloor. Not impossible by any means, but will take lots more attention to detail DURING framing. You will need to be there, baby-sitting the framers like a hawk, or interrupting them to do that work yourself. Other than that, it is a nice, practical system, and you can get dried in very fast. Zig-zagging your air barrier through floor systems (from interior to exterior and back), and accommodating upper floors that do not overlay the downstairs exterior walls can be a real headache and occasionally a head scratcher during framing. But, I just had to deal with A LOT of that on the house I am currently building for a client and we still achieved 0.19 ACH50 on our first blower door test. But you have got to be on the ball every step of the way. :)
Malcolm- I like your idea about eliminating the wall spreader plate sheathing layers to greatly reduce that floor level thermal bridge. It would be tricky to do and still be able to stand the walls and connect them. The window liners (½" plywood wrapping the insides of all rough openings) would help, as they do basically a similar thing, but it might take some creative thinking to get all the walls to stand without racking as they stood up. Good suggestion though, for sure.
I don't love the step up to the main floor either, but was thinking I would have non-attached, ground-level decks just outside the floor, so could easily make them close to flush with the interior finished floor, moving the steps far away from the entrance (or even use a gentle ramp) which would soften the approach, and could even be done very attractively by incorporating interesting landscaping/planter/deck features into the design.
I really appreciate the feedback, all. We don't always have the luxury of clients with no budgetary constraints, so it is imperative that we figure out highly effective wall systems that are super-insulated, but also quick to build. Faster to construct and with fewer fussy details means less labour expense and more certain performance, and that means they will fall within the price range of more people and the skills of more builders. And that will go a long way towards helping people get on board with highly efficient homebuilding.
Does anybody have any genius ideas about my second original concern about how to leave the cellulose cavity visible for inspection during and after blow-in? I have had panelized walls come from pre-fab places filled with dense-pack cellulose and they had Agepan fibreboard on the exterior and ⅝" OSB on the interior. They drilled holes on the OSB layer (then air sealed after) and did not use any netting. Is it purely experience of the installer to ensure you don't get any voids doing this, or does anyone have any tips to guarantee success when visible inspections aren't possible? Trained hamsters to go in the walls and inspect? Remote wi-fi video cameras on tiny robots that I can drop in a hole and drive around?
Those are indeed sarcastic, if you couldn't tell. ;)
By the way, sorry for the novel I just wrote.
Q. Do you feel there is much of a difference hygrothermally between my detail at the interface of framing and foundation wall as opposed to the mud sill on a house with an unconditioned crawlspace and an insulated, air sealed floor system place on top of it?
A. Yes. The difference is that top of the foundation in an unconditioned crawl can get warm in the summer whereas your gravel stays cold in the summer.
Hmm. Very good point, thanks Charlie. Can you offer a detail, or an alteration that is reasonably simple and yet offers similar thermal performance? I know the typical Passive detail involves placing the load bearing wall on top of foam, but I'd rather avoid that given my seismic situation.
Burke - I'm not trying to convince you to use my ideas, but your reasons against it are due to my incomplete explanations and lack of diagrams.So I've enclosed a diagram. My build will have virtually no attention to air sealing during framing, other than unusual framing. On the inside of the outside 2x6 load bearing wall, 1/2 " by12" plywood strips would be installed prior to the hung floor joist system.These would be taped to the rest of the air barrier after the structure was weather tight. That stud wall will be 9' tall, to accommodate the joist system. I plan to build a cape, but have drawn the detail attached as a 2 story, since that's your plan. It may not fit your needs or wants. The advantage is quick close in ( good for cold climates). I plan to use mineral fiber batts, for their breathability, but the inner 5.5" could be dense pack cellulose. Please let me know your thoughts. Thanks
Kevin- your diagram explains a lot. I hadn't realized that you were thinking of essentially hanging your floor system off a ledger that will be bolted to your structural wall studs. That air sealing makes much more sense. I think you've got a nice wall system there. While much of what Dana has said about vapour barriers being able to be at the cold 1/3 of the wall surely makes building science sense, to me that is the only concern with this assembly- I would rather increase my margin of safety by having that ½" ply VR layer a bit closer to the warm side. Other than that, I think you have a very nice, very buildable/practical super insulated wall there! Having your outermost sheathing be fibreboard or gypsum would probably be smartest, just so your drying potential to the exterior is as high as possible. Nice work!
Thanks,Burke. By using Roxul in the outermost layer, the percentage of insulation outside of the air control layer can be significantly less, as the Roxul is extremely vapor permeable. Those rules of thumb assume foam or other impermeable outside layers of insulation, so all the drying must be to the interior only. Since my desire is to get the house enclosed ASAP, I'm willing to stretch those rules, but I'm really hardly stretching them at all. This assembly is certainly MUCH more resilient than a simple double stud wall, and those appear to do well if built properly and use plywood ( not OSB) and a rain screen.John Straube ( BSD-163 : Controlling Cold Weather Condensation Using Insulation) writes " If the selected sheathing layers ( including structural sheathing, water control, and insulation) are somewhat vapor permeable…less R-value can be used and diffusion condensation will still be controlled ( because much of the vapor that diffuses or leaks with air into the stud bay will pass harmlessly through to the outside by diffusion)." I figure my wall as drawn has about 45% of the R-value outside the air control layer.
Kevin,
Thanks for posting that. It's an interesting section that solves a lot of problems. The one thing I'm not sure about is whether using just the ledger to tie the hinge point in the outer-wall is enough (I'm assuming the subfloor ends at the inner plywood wall sheathing). Our code wants load-bearing wall studs to be continuous. I bet you could get an engineer to approve it and specify an attachment for the ledger supporting the floor, but Burke might find it harder here due to the high seismic design requirements.
Malcolm- I spoke with an engineer about doing just that kind of load bearing wall detail a few of years ago, where the hinge point of the walls was just above the floor system, and there was a ledger on the lower wall. He said that he wasn't that concerned about it. Although, I think that was before all the new seismic code changes came into play, so it could be viewed differently now.
Malcolm - I suspect you're right. For my place,a cape, the plan was to extend the second floor plywood subfloor out over the top plate. I tried to modify it for Burke's 2 story plan. Maybe joist hangers would satisfy? Or the same plan could be applied to the 2 story, with the top plate ending at the height of the floor joists and the plywood subfloor running out over the plate. You'd have to caulk the wall to floor plywood layers as you framed it to keep continuity of the air barrier. Thanks for your comments.
Kevin,
I'm trying to thing through what the advantages or disadvantages of that section are versus making the inner wall load-bearing with the plywood on its outer face? It would mean re-thinking the foundation wall to provide bearing.
Malcolm - The advantage for me is to get the shell up and weather tight ASAP, and then insulate, air seal, and build the inner wall in a dry place. The inner wall does help support the second floor, but is not needed for that support. Maine can have a long winter, and long stretches of inclement weather.It can also have long stretches of nice weather. Getting the house dry quickly gives the builder more options.If you can figure out how to easily seal the plywood on the outer face of the inner wall, go for it. This plan is more expensive as there are 2 layers of sheathing, but one could argue against the outer sheathing., and just have a rain screen. This plan would be for myself, and I like the idea of a wall that's strong and solid. Thanks for your thoughts, you always have practical, sound advice, that I appreciate, delivered in a tone that is not "better than". Hey - give me more thoughts on the structural integrity and seismic resistance. Would extending the subfloor out over the plate suffice for your codes? Sorry to all for interjecting on this thread. If it continues, I'll start a new one.
Kevin,
Our code has two paths to seismic compliance:
There is a prescriptive one, where you have to provide continuous clad shear walls, from foundation to roof, which are either 25% or 40% of each wall depending on where you live.
The other is to get an engineer involved.
So that second path is where Burke and I end up speculating as to what they would accept based on conversations we've had with them. - and your guess is probably as good as ours! We buzz around variations on double walls like bees on flowers, looking for some advantage in resilience or build-ability. The complication seismic brings to us here in the PNW is in limiting our choices for the placement and materials used as sheathing.
Temperamentally what I like about the double walls we are discussing are the way they bury the air and vapour control layers, provide a service cavity and allow for the exterior to be detailed in a way that is familiar to the inspectors and trades here. Not having built one, what I can't quantify is how much more the second layer of sheathing involves - and maybe this is a very design specify thing. Slapping another layer of plywood on a trussed-roof bungalow is a lot easier than on a multi-storey house with gables.
Why I prefaced my last remarks with "temperamentally" is, in the current circumstances of working where I do, building a double wall may be hard to justify from a building science perspective. The energy used to heat the moderately well-sealed, rain-screened houses I built here is very small, and is dwarfed by both the plug loads, occupant behaviour and transportation costs of their rural residents. Of course over time that may change.
Forgive me for writing a novel. I'm enjoying this interesting dialogue.
Malcolm (and Burke) - I can't see going through the trouble of a double wall when the climate doesn't justify it, though I get it that you like the challenge of the details. There are easier ways to get to, say, R-30. Another challenge is that I'm trying to minimize or eliminate foam. Yes, used foam is an enviable choice, but foam as a building product is really not sustainable. Everything has a lifetime, and what do you do with the foam at the end of its life? I guess they are coming out with ways to grind up and re-use EPS. Burke - I was re-looking at your drawing, and your question about the 1.75" "thermal break" around the building. If your building had a 200' perimeter, it works out to be about 30 square feet of, let's say, R- 15. ( Assumes 12" at R-1.25 per inch.) To put it in perspective, that's 2 average windows in size, at significantly less cost and significantly better R-value - not too shabby, if that's the "weak link" of your system. If I have the time, I'll repost a modified drawing on a new thread for more comments from the readers. Thanks for your input.
Kevin- thanks for putting the floor system thermal bridge in perspective! I hadn't really thought about it like that. I am somewhat fearful to admit on GBA that I have taken the Passive House Training through CanPHI, given that the non-contextual universality of the standard has certainly received some flak on the site. However they have a logic that I have to respect (we all live on the same planet and should be held to the same energy consumption standards regardless of location). This is not the thread for that, but suffice it to say, I obviously suffered from the PHI thermal bridging paranoia as a result, and didn't question that that 1-¾" thermal bridge really amounted to. So thanks for putting it in perspective!
I totally understand Kevin's reasons for designing the wall he did, and think it is actually quite a good, practical one for the goals he is trying to achieve.
I am attaching here a revised PDF of my original double stud wall, and have made the changes to the original apparent in red type. Would like to know what people think. The main reason for moving the interior, load-bearing wall's sheathing to the innermost face is twofold:
-It permits one to leave off the structural sheathing so that the wall can be netted and dense-packed normally, allowing inspection of the dense-pack thoroughness, and
- it makes air-sealing that ½" ply layer (as a secondary A.B.) possible (it simply is impossible to do if one wants to
The wall looks much more "typical", but I think it becomes far more realistic to build, and because the exterior air barrier is the main one, if you don't manage to get every single interior penetration sealed perfectly, then it's not a huge deal. In Edmonton, our main air barrier was the 6-mil poly VB on the innermost surface of a double stud wall, and we routinely were able to achieve <0.4 ACH50 blower door tests using nothing but poly, acoustic sealant and tuck tape. So, I don't feel that a service cavity is actually all that necessary, and ESPECIALLY not so when your exterior sheathing layer is your real air barrier.
I also added some thermal protection on the inside of the foundation wall and made the materials adjacent to the foundation wall top pressure treated. Do you all think this alleviates the shared concern about those materials being highly susceptible to moisture damage over time?
I would love to hear your thoughts, and I think keeping going with all the different double-stud iterations we're discussing on this single thread makes sense, as it will be pertinent to the interests of anyone intrigued by the title.
Burke,
My concern with moving the plywood to the inside would be that you don't end up with a continuous layer of sheathing, which is acting both as your shear resistance and required interior vapour barrier.
Thanks for the thoughts, Malcolm. I would have to ask an engineer if it is critical that the structural sheathing needs to be continuous across the split between the two walls. That is an important concern that I would have to verify.
The vapour barrier, which is the plywood, would only be interrupted by the layer of subfloor running between the lower and upper walls. Because the vapour barrier does not need to be sealed, as it is not acting as my air barrier as well, I don't think this would be a problem.
Burke,
I was thinking more of the interruptions for interior partition walls.
For bracing: Piecing in what could be a lot of short sections of plywood as discontinuous shear walls probably means a stud at each side off each wall, instead of the usual backing.
The vapour barrier: When we use poly, we maintain continuity by placing strips behind the intersection of interior walls. I don't know what you would do if the vb is plywood.
You could make the sheathing continuous by installing the interior partitions afterwards, but that would make the electrical and media wiring a nightmare.
Burke - Yes it would be easier to build, but I'm not sure that the plywood inner layer is doing much more than carefully applied and caulked drywall would do. Every electrical box is still cutting into your inner layer. Any changes made to the wiring in the next 50 years will disrupt that layer. What is the advantage over any double wall? The inner wall air barrier is what makes that wall "robust". With your new wall, you still have condensation potential - more than on your last wall. If you are going to keep that slab over the framing, what about dropping it down 6"? Someone recommended that before, and I don't see the downside to that. I don't think you need the plywood running down the inside of the foundation wall; it seems like the foam will do the job. Sorry, but for all the potential problems with your old wall, I think it will hold up better over time - for reasons of increased condensation potential.
Hmm. Those are excellent points you guys make. Especially Malcolm's issue with interrupting the sheathing for partition walls. That would certainly jeopardize the integrity of the lateral bracing. Because the first floor walls will be about 11' tall, there will be a 3'-ish strip of sheathing in middle of the walls. I could install this as soon as the exterior walls are stood, and that is where all my wiring could run from the partition walls into the exterior walls. Likewise, the second floor wall sheathing would extend over the truss heels, and so that wall sheathing span about 9' 4" or so, meaning I could install a 16" strip of sheathing in the middle of those walls after they were stood, and where the wiring could penetrate to the exterior. I'm really glad you raised this, but that doesn't seem like a terrible work-around to remedy, as I would have been installing those strips of sheathing in the middle of the walls regardless. running the sheathing behind the floor joist hangers, however, does pose more of a challenge that I can't see how to easily resolve . . .
Kevin- I'm not certain I agree that having an interior air barrier makes a wall more robust over an exterior air barrier. The consensus seems to be that if one is using dense-pack cellulose as the cavity insulation, then it is irrelevant where the air barrier is, because there won't be any convective looping carrying moisture into the wall. So, I would still utilize the exterior Denseglass sheathing as my main air barrier. My understanding is that the risk of condensation has mainly to do with air movement through the wall, and with the exterior sheathing layer's vapour permeance to transmit any moisture to the exterior as easily as possible. That is why using plywood or OSB sheathing on the exterior of a double stud is such a no-no: because it severely inhibits outward drying potential.
The main issues with having the plywood on the outside of that interior wall is that it makes it impossible to air seal that layer if the walls are built together, and it is also impossible to install dense-pack cellulose and visually confirm that the installation is not leaving voids AND to have it viewable for inspection by the building official. I care less about that layer being an effective air barrier, but I don't see how to possibly install the cellulose.
I do quite like Kevin's wall system, but I don't feel convinced that having one's vapour barrier that far towards the exterior is ideal. It may be acceptable, which I would love to see hygrothermal studies for our climate confirming, but closer to the interior is better, is it not? The Passive House wall often used is the 2x8 with fibreboard exterior sheathing and plywood AB/VB interior sheathing, and then the 2x4 service wall inside of that. Problem is, I am trying to avoid the labour of framing and standing two separate sets of exterior walls, as well as allowing a visually open installation of the cellulose.
Back to the drawing board?
Kevin- dropping the slab down 6" means that there is much less insulation separating my slab from the top of my foundation wall, meaning my heat loss across that diagonal around the entire perimeter goes way up.
Burke,
I agree. Breaking up the cavity only makes sense if you are using batts. In one sense a house built with sheathing on the exterior of the interior wall has more in common with exterior foam or mineral wool than a "true" double wall.
Burke - As I understand it, the issue, or potential issue, with conventional double wall is the condensation potential on the cold sheathing. Lstiburek's ideal double wall addresses this by placing the air barrier inside the wall, where it is warmer and less prone to condensation. Moisture will still travel from warm to cold through the wall system by diffusion, unless there is a very impermeable vapor barrier like polyethylene. Moisture will still travel through the plywood "vapor barrier", as it is still relatively permeable ( it's considered semi-permeable, having a perm rating of 1 when dry, but up to 20 if wet ). Cellulose has the nice property of being able to hold and then release moisture, but studies show that the exterior sheathing gets pretty wet by Feb.,then dries out by May. See Martin's blog, "Monitoring Moisture Levels in Double Stud Walls", 11/1/2013 in GBA. Your 2'nd wall will probably work fine, and will definitely be easier to blow cellulose into, but the tradeoff is it is not as robust from a moisture point of view. Malcolm is right in that my wall is more like a foam( or mineral wool board) sheathed wall, just using a stud wall in place of foam. I'm ( so far) settling on this because I like mineral wool, and the batts are so much less expensive than the boards. Hang in there. Whatever you decide to build will be great - you've put a lot of good thought into it.
Kevin- I agree with everything you are saying, with the exception that the amount of vapour moving through 2 coats of latex paint on the drywall and then through the ½" plywood on my second (or first) assembly is extremely small compared to what would be transmitted through air leakage (which is usually referenced as being 100 times the amount moved through a hole of a the same size under the same conditions by vapour transmission alone). By having an extremely simple and effective exterior air barrier at the outermost sheathing plane (the exterior water resistant gypsum layer) preventing the transmission or large amounts of moisture into the wall through air leakage, there should be little concern about the amount of vapour transmission through the materials themselves. And any vapour that does get through, the wall is increasingly vapour open as one moves outwards toward the exterior (cellulose= 35 perms/inch, ½" CGC Securock= 28 perms, Tyvek= 58 perms), so it will dry extremely easily to the exterior with no moisture buildup.
Your wall detail is much easier to build than mine, for which you get bonus points! But I am still mildly unsettled by the fact that you will have vapour from your interior moving through your wall to the exterior, and at the mid-point it will hit a vapour retarder. It may not necessarily condense, as that ½" plywood shouldn't ever be below the dew point, but it is definitely a bottleneck. So now you have high humidity levels stuck in the middle of your assembly until they reach such an elevated point that your sheathing is so moist that it now becomes more vapour permeable (activating the "smart" capability of ½" plywood), and allows that moisture to move outwards again. If you have fibreboard of a gypsum product on the outermost surface, you should be fine. If you have another layer of OSB or plywood on the outermost sheathing plane, then you've got all that stored up vapour migrating onto a cold condensing surface and you've gained nothing for your efforts.
To me, having your vapour retarder much closer to the interior (as the Lstiburek wall does) and a increasingly vapour open assembly outboard of it makes the most sense for a high risk climate like the coastal one that Malcolm and I live in. Unfortunately, Joe's wall is extremely costly to build from a labour perspective, and therefore not much better than an interesting intellectual exercise in good moisture dynamics. If someone can show me the light on how to sequence this quickly and easily, I will sing their praises!
I totally get the notion that protecting that vapour retarder layer on my wall is an ideal concept, but moisture issues from vapour transmission are pretty low down the totem pole of concerns. Firstly the problem is always bulk water management from the exterior (which I know how to handle through meticulous cladding/flashing detailing and ventilated rain screen cavities), second is moisture loading into walls from air leakage (which I am confident is easily addressed but the exterior gypsum air barrier), and lastly is simple vapour transmission from interior humid air. A few small holes in that ½" plywood layer from imperfectly sealed electrical boxes is nothing to lose sleep over if the first two concerns are addressed. If someone cuts a hold in that wall in the future to install a new electrical box, we will get a bit more vapour transmission, but I don't think it would seriously jeopardize the durability of the wall. The small amount of moisture that does get in will quickly and easily migrate outward through the vapour open materials.
But the problem still remains: how can one build something that follows the outward drying ease of the Lstiburek Ideal Double Stud wall but in a more realistic labour/cost friendly fashion? I will continue to give it thought and will post new drawings when they arise. Please share any thoughts you guys have too!
(This comment also posted on the "How to Attach a Thick Layer of Exterior Insulation" article: https://www.greenbuildingadvisor.com/blogs/dept/qa-spotlight/how-attach-thick-layer-exterior-insulation#comment-form)
I have done some cost comparisons on my future house plans to determine which wall system would be more cost effective for me: a super insulated wall using the exterior Roxul or a double stud wall system with dense-pack cellulose. The short story is that the exterior Roxul is, in my estimation, more expensive in both materials and labour.
For my plans with approximately 2970 square feet of exterior surface area (I did not subtract window and door areas in either estimate, for simplicity's sake), here is the breakdown:
Assume a cost baseline assembly of a standard 2x6 wood framed with exterior sheathing which is the main air barrier, no insulation and treated plywood rain screen strips (which are code mandatory in our jurisdiction).
Here, then, are the MATERIAL ONLY cost premiums (in CDN$, at contractor prices, not including taxes) to upgrade to either:
- a 2x6 wall @ 24" o/c with 6" of exterior Roxul Comfortboard IS (three layers @ 2") and 1x3 rain screen, OR
- a 12" wide double-stud 2x4 wall @ 16" o/c with exterior gypsum drywall and a layer of ½" ply on the interior for the load bearing wall. (See attached PDF for a section of the double stud wall, since it is a more complicated assembly to describe).
EXTERIOR ROXUL WALL COST PREMIUMS:
Cedar 1x3 rainscreen @ 24" o/c: $487
8" long GRK fasteners through rainscreen @ 19.25" o/c vertically: $1685
Roxu/Rainscreen/Cladding attachment engineering costs (required by Roxul for >4" insulation): +/- $750
Roxul Comfortboard IS (three layers of 2"): $18192
Cost of extended through wall flashings (6" deeper than normal): +/- $500
Fibreglass batts for the 2x6 stud cavities, with a 6 mil poly vapour barrier, including installation: +/- $3680
TOTAL= $25294
DOUBLE-STUD WALL COST PREMIUMS:
Extra framing: $1046
½" Denseglass exterior gypsum: $2379
12" Dense-pack cellulose (including installation): $13663
Interior secondary air barrier air sealing with 3M All Weather Flashing Tape: $278
Inner Wall "temporary" bracing during rough-in phase: +/- $250
TOTAL: $17616
MATERIAL ONLY COST DIFFERENCE: Double stud wall is over $7600 less expensive.
That's not as large of a material cost difference as I had expected, but it is still worth considering. (It would pay for the purchase and installation of a high quality HRV system!) However, when I started considering the labour costs between the two systems, the exterior Roxul system really started to look onerous. To frame the double stud wall I am proposing would realistically add about 4 days max. to the wall framing of the house. That's pretty much the extent of the extra labour required for the double stud wall. Alternatively, the exterior Roxul attachment in 3 layers would take far longer, once one factors in the additional work surrounding how the Roxul terminates around window/door openings, how one installs 3 layers of Comfortboard concurrently without having them fall off, as well as having to drive 1150 (on my project) 8" long screws one at a time through the rain screen (and then checking it all to make sure it is flat/co-planer) instead of just nailing it to the framing with an air nailer, as well as a bit more time bending and dealing with the much longer through wall flashings (which would all be 6" deeper than those on the double-stud wall), and how those flashings interrupt your installation of the Roxul as you move above openings. As a ballpark, I would guess that labour for the exterior Roxul would add at least 12 days of extra labour at best. So, that's 4 days of labour for two guys vs. 12 days extra labour for 2 guys.
Combined with the material cost differences, for my scenario I figure the double-stud wall all-told will probably be around $13000 less expensive AND a good week or more faster to build in terms of timelines.
I understand that every project is different. Different climates demand different assemblies, and different material availability and trade expertise are all important considerations. But for me it was a valuable exercise to price things out and consider labour times to determine which wall system seems to make more sense from a purely financial perspective. While a fantastic wall system in terms of hygrothermal performance and durability, the exterior Roxul SUPER-INSULATED wall system is definitely an expensive one.
BURKE - Thanks for your post and efforts. Your new modified wall looks very good and quite resilient. I'm assuming you want to use a rain screen? It's not listed in your material comparison as it is in your exterior Roxul wall, but I think it would be good insurance towards drying potential. I am still concerned about your slab detail. Martin's recent blog about the diminished returns of extra insulation on the overall energy consumption picture makes me think that what you're saving in energy at the slab edge with your current system is not justified by the potential trouble of the bottom of your wall having zero potential to dry to the inside. There are plenty of double walls built with other slab to wall details that may not be quite as energy efficient as yours but would be safer in terms of their drying potential. One easy one would be to use deep ICF's as the foundation wall. I'd like to see that slab even with the top of your foundation. One step up from outside. No wet wall worries. Just my thoughts.
Kevin- This will definitely have a ventilated rain screen, you're right. I am considering changing the slab edge detail. You're probably right about it being potentially more trouble than it is worth. It also complicates construction, as tilting the walls up onto the foundation would be a real challenge if the slab is one foot above the top of the wall. Lots of potential for things to go wrong when standing walls. I will consider some lesser slab edge thermal breaks that permit better drying and easier construction. Thanks for your continued persuasion about the moisture concerns there!
BURKE - You may have already seen this, but the current issue of Fine Homebuilding ( July 2016, #260) has a double wall house as one of the articles. It has the flooring system inside the wall, as you have planned. Your details appear to be an improvement ( he uses Zip sheathing on the outside), but he has a foundation/slab detail that you may find interesting. He uses high compression foam over the top of the foundation wall and under the slab. The slab takes the weight of the house, but it is over the foundation, and still has 4" of foam on the slab edge, with 2x12 plates mostly on the slab, but cantilevered over the edge foam.
Kevin- thanks for the tip! I have had that issue sitting beside my computer, unread, as I laboured over this slab edge detail for a few days now! I just took a look and will give it some thought. The anchoring of our walls down in our high seismic region may make this tricky, but it definitely warrants consideration. Thanks for keeping my troubles in your thoughts, ha, ha!
The wall needs to be vapor open to both the inside and the outside of your air / moisture barrier. Both sides need to be able to dry.. adding a second moisture barrier really does sound like a prescription for mold and rot
I am late to this discussion but am hoping earlier participants can re-engage!
I am building a 4-story passive house apartment building in Minneapolis (6A). We are doing a double stud assembly with cellulose because we also have embodied carbon reduction targets.
We have settled on a load bearing exterior wall to simplify the thermal layer details at the foot/stem-wall transition. The load bearing wall is 2x6 for structural reasons.
Like everyone here...we are weighing material cost, buildability, and durability/failure risk.
Kevin Zorski's wall was our initial preferred approach. To address Burke's concerns about inspecting cellulose install, it would simply be installed with netting and inspected prior to plywood going on. That said, this approach presents a few costly drawbacks in our application over the baseline presented by Ben Bogie in his FHB article:
1) ($ + Material) Hangers for our 18" trusses are quite expensive
2) ($ + Material) Using hangers will require an 18" wide double layer plywood ribbon around the entire building perimeter at each floor to serve as a nailer for the truss hangers
3) ($ + labor) An extra mobilization of our HVAC subcontractor to install and air seal ductwork through the exterior stud wall before the interior stud wall goes up.
4) ($ + material/labor) - having both exterior sheathing (DensGlass) and interior sheathing (plywood) of exterior stud wall
We are waiting to hear back on hygrothermal modeling of this assembly to determine whether locating the air/vapor barrier 5 1/2" into the 15" wall assembly is enough in our climate zone to meet PHIUS+ requirements. I will post those results.
The cost and buildability drawbacks above keep bringing me back to trying to make Ben Bogie's assembly work for a multifamily building built to last 100+ years.
The assembly below is a tweak on his, with the addition of a smart vapor retarder.
Exterior to interior: (15" total depth)
- Cladding
- 1x4 rainscreen
- 1/2" plywood taped at seems with Siga Wigluv (air barrier #1)
- 2x6 load bearing exterior stud wall
- 2x4 interior stud wall
- netting between two stud walls and on interior face of interior stud wall to sub-divide
- dense packed cellulose
- Certainteed MemBrain (Air & Vapor Barrier #2)
- USG EcoSmart GWB
It is clearly better to put the MemBrain at the exterior of the interior stud wall to 1) ensure continuity at install (i.e. no tricky outlet boxes, drywallers being carless with sawzalls, etc) and 2) protect it from future maintenance work / tenant wall hanging nails.
That said, the sequencing is much simpler and more cost effective putting the MemBrain on the interior of the interior stud wall.
In weighing the risk/costs of this path, I'd like people's thoughts on some scenarios
Scenario-1: The vapor barrier is compromised with nails from hanging pictures.
Question-1: How much risk (moisture) does a nail sized hole allowing humid air / vapor intrusion during cold months into a wall with 15" of cellulose really pose given the hygric properties of cellulose? Does your answer change over 100 years?
Scenario-2: At install, the detail around an electrical box is poorly executed. As gypcrete is being poured, vents are accidentally left off and humidity in the building gets astronomically high (winter months).
Question-2: Can the assembly recover from this one-off super moisture accumulation event followed by years of seasonal moisture similar to Scenario-1?
I would love a range of expert answers on questions 1 & 2 above!!
Assuming you answer: (1) It is risky, especially over 100 years and (2) would likely result in mold. That leads us to putting the vapor retarder on the exterior of the interior stud wall.
I prefer to use MemBrain instead of plywood to reduce material cost and embodied carbon.
Installation Hypothesis: Prior to stud wall being tipped up, insulation subcontractor would...
- staple cellulose netting / fabric
- apply acoustical caulk to bottom of bottom plate & top of top plate
- MemBrain cut with 8" excess on top and bottom of wall and on wall ends
- MemBrain stapled to wall through acoustical caulk
- Wall is tipped up by framer
- At the corners, fold the two pieces of MemBrain from adjoining walls together and stapled them inside a stud, then tape the joint.
- Cut hole through MemBrain/netting and blow in dense packed cellulose
- Patch all holes
This seems incredibly complicated, slow ($$) and requires both the framer and insulator to be working on the wall at the same time and coordinating the prep and tip up of each section of wall.
With the MemBrain installed and the exterior plywood sheathing taped, I also don't know where the air goes during dense packing. Waiting to tape the exterior sheathing seems insufficient. Question-3: Is this a problem?
This approach also has no way to sub-divide the wall to allow for quality dense pack installation. With the MemBrain on at tip up, its not possible to install netting at intervals between the two stud walls. Question-4: Do we need netting to break up a 11.25" deep wall of cellulose?
If we just used plywood instead of MemBrain...
Question-5: Is it sufficient to tape vertical seams, tape top/bottom plate seams before tip up, apply a bead of acoustical caulk to bottom of bottom plate before tip up? I'm then at a loss on what we do to keep the vapor barrier continuous at the top plate.
The threads linked below are ones related to this thread...linking to consolidate here for this conversation:
https://www.greenbuildingadvisor.com/question/double-stud-wall-midwall-air-barrier
https://www.greenbuildingadvisor.com/question/can-someone-explain-the-science-behind-a-mid-wall-vapor-barrier-on-a-double-stud-wall
https://www.greenbuildingadvisor.com/article/lstibureks-ideal-double-stud-wall-design