Improving Structural Integrity of Brick Garage

Hi all,
Folks were very helpful in my recent insulation thread here: https://www.greenbuildingadvisor.com/question/help-with-detached-garage-hip-roof-insulation
That thread may have some useful information that I’ll recap:
-1937 detached garage with brick walls (8″ thick) on concrete slab in historic neighborhood, zone 4 in Maryland.
-Slate hip roof, 7/12 pitch, with 2×6 rafter ties 48″ OC about 12 inches above the top plate. 1x hangers supporting the rafter ties.
-Rafters themselves are 2×6 24″ OC with the hip rafters being 2×8.
-Interior dimensions are 17.5 x 16.5 give or take a few inches.
The plan re: insulation was to add additional rafter ties to every rafter, so there will be a 2×6 24″ on center going both width wise and length wise. I will use 2×4 vertical hangers to support the ties. I’d then use 2″ rigid foam with R30 fiberglass batts on top.
Although I don’t think the dead load weight of the additional rafter ties, foam, and fiberglass will present a problem for the roof, I’d like to beef up the structure to the extent possible.
Quick aside, I do have some inquiries out to structural engineers to see if I can find someone for a quick consult, but if they are like other contractors I’ve been working with they are swamped and not especially interested in my small job. So I’d like to educate myself as best as I can acknowledging that you all are not here to see the roof.
So my question has a few dimensions.
First re: the placement of the rafter ties. I see that in many cases the rafter ties are placed directly on the top plate and nailed to the corresponding rafter and top plate. This shifts the vertical load (of the ties themselves, insulation, or whatever else) to the walls rather than the roof. Would it be advantageous to install the new rafter ties on top of the top plate rather than a foot up like the current ties? Once I installed the new ties 24″ OC, I would remove the old ties. The ties going in the other direction would sit perpendicular on top of the new ties and affix to the rafters. I would still use 2x4s as vertical hangers.
Although this would lower the ceiling so-to-speak, it might be more structurally sound. Are there other options to consider? Is there a way to leave the rafter ties a foot up but somehow transfer the load to the top plate? My searches have come up empty.
On other note, I measured the space from the front edge of the top plate to the rafter and there’s about 7.5″ meaning I *could* use 2x8s as rafter ties if there was an advantage. However, I don’t plan on creating a walkable space above, just enough to hold the insulation and rigid board (likely Thermax or similar exposed interior board).
Second, currently there are no collar ties. While I’m not sure they are needed, I do see one of the rafters is pulling away from the ridge beam. I figured adding 1x6s or maybe 2×4 or 2x6s in the top 1/3 to serve as collar ties could strengthen the structure without much downside.
Pictures forthcoming. Thank you for your time!
Matt
GBA Detail Library
A collection of one thousand construction details organized by climate and house part
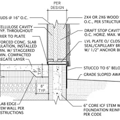
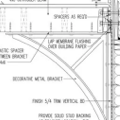
Replies
Looks like you have more of a ridge board (non-supported) than a ridge beam (load bearing with vertical supports) here. You have some vertical supports partway out , which help, but probably aren't really enough. Adding rafter ties to the the full-length rafters would probably help here, but you'll have to be careful how you do it since your structure appears to be nearly square. Normally rafter ties go across the narrow dimension of the structure so that you get more, shorter, ties.
I would be very careful with the brick. I have friends in Federal Hill, so lots of old brick. I've seen more than one shared wall come apart when one row house was doing renovations, which causes lots of excitement for the neighbor! Your structure is less of a risk since it's detached, but you'll still need to be sure you don't have any deterioration of the brick or mortar.
You'll really want to have an engineer or competant contractor check this in person. It's surprisingly difficult to work out structural issues from pictures since it's difficult to really see how it all goes together.
Bill
Hi Bill,
Yes, after I posted I double checked my language and I have a ridge board, not a beam (at least I believe).
There is some spalling of the brick in one corner, but it otherwise looks in decent shape to the untrained eye. One additional issue is that there's a big old cedar tree growing about a foot from another corner of the structure. We think we need to remove that otherwise the roots are going to mess up the foundation or the tree falls over (it is leaning), which would also destroy the garage more than likely.
A structural engineer in the area did reach out so I'll have to see what they say. Honestly, if there are issues, I'll probably just run 100a electrical to the garage, install a minisplit for occasional use, and buy myself some tools and cabinets and call it good.
I think your roof needs both sets of rafter ties. Typically a rafter tie can sit up a bit from the top plate, the only time this becomes an issue is if you have undersized rafters such as long span 2x4. This doesn't seem to be the case for you.
Since the structure has held up well as is, I would not worry too much about it. The insulation won't be adding all that much weight especially when you compare it to slate. I would add in the extra ties in between you need for the ceiling and call it a day.
An extra foot of ceiling height is always a good thing, I would keep it.
Matt,
What Akos said.
If any of the experts are still browsing, a structural engineer just quoted me a flat fee of $1200 to assess the space. I was hoping for more like $7-800 but it is what it is.
I'm tempted to have the analysis done as if it turns out I can strengthen the structure to a fair degree then it might open up other insulation options. My current plan with the 2" Thermax is quite expensive--I'm seeing $110+ a sheet for 2 inch Thermax. I'm estimating over $3000 for the Thermax, batts, furring, tape, spray foam, screws, and odds and ends.
If anyone has thoughts on whether it's a worthwhile expense, let me know (with the usual caveats that you aren't on site to evaluate, etc.)
I am a licensed engineer and I don't do much for less than $1k so I would say the price is reasonable. One time I had a home buyer with a house in my town than needed a second opinion on some foundation cracks, just a verbal opinion with no written report. That was about $300 IIRC.
Add in any travel, analysis, written report, etc. and you get to $1k very quickly.
You are at the point where you need to ask yourself if your vision is worth the cost. You can look at ROI if this is purely an investment to you. If the comfort is an issue, maybe ROI isn't the sole deciding factor, but I'm sure there are other things you could spend the money on that you may want to prioritize.
Depending on what your goals are with the space it may be time to take Walter's advice and go for a low-tech solution until some other reason presents itself to reconstruct the garage.
Hi Huey,
I just had this exact conversation with my fiance today--if my vision was worth it. My current vision is pushing $20k now with me doing most of the labor (I charge $0/hr). I've always dreamed of having a hobby/shop space and when me and my partner moved in together me having this space was part of the deal. However, as I look at our 1937 home there are quite a number of improvements we could make for $20k that would offer great ROI whereas my garage project would likely result in little to no ROI. I'm not doing this for financial ROI but I don't want to be stupid either:)
So I'm at the step back and look at this differently point of my planning. I have some questions around Walter's idea but I'm trying to figure out a "perfectly good enough" solution to insulating, etc. that allows me time and money to actually enjoy my hobbies.
Why the 2" Thermax? You can save a fair bit by going thinner.
Skipping the thermax and going with 3/4" polyiso with taped seams covered by either drywall/OSB/CDX/T&G is probably cheaper but a bit more labor.
Weight mostly. The foil or white faced Thermax (or similar product from RMAX or JM) can be left exposed to the interior. Two inches to make it stiffer if was putting batts on top of it. If I use drywall then I would use a normal foil faced polyiso at probably 1" as my favor barrier and for CI to reduce thermal bridging.
The fact is I have to get the price down. $1700 for 15 sheets of 2" Thermax for an occasional use space isn't a wise investment.
From a dollars and cents point of view the smart move is to pack the voids with fiberglass and cover it with drywall that will give you R13 at very low cost.
If you pay the engineering plus framing and insulation you will have spent 5 thousand before you can blink getting to R38. The number of hours you would need to heat the space to recover your 5k seems likely to exceed the number of hours you are likely to use the space.
In fact consider skipping the insulation and install a wood stove and burn your scraps at zero fuel cost making more than enough heat.
Walta
Hi Walta,
Thank you for your suggestion. This is the novice in me, but the whole reason I was looking to avoid drywall is the weight and I only have collar ties 48" OC. So if I'm understanding the only way to put up ceiling drywall is to add the additional rafter ties.
If you mean filling the rafter bays with fiberglass leaving 1.5 inches for ventilation and then putting the drywall against the rafters--I wouldn't need to add structural timber but again, can the rafters support drywall weight?
Thanks for your help.
The way I see it the weight of the drywall is small compared with the weight of the slate the roof is supporting and knowing this roof has supported large snow load in the past make me think it will hold a little extra. If you happen to get 20 inches of snow rake the roof to control the load.
I would not leave a gap for ventilation fill the void cover with visqueen and attach drywall to the rafters leaving the beams exposed. The way I see it moisture should not be a big problem as I doubt you are likely to heat the space 24-7 and I am assuming you are smart enough not to use an unvented fuel burning heater.
Walta
The only issue is that even if the weight of the drywall is small relative to the weight of the slate, what if the carrying capacity of the existing framing is arleady nearly entirely "used up" by the weight of the slate? That's when you have a problem -- the proverbial straw that broke the camel's back...
You can save some weight here by using plywood instead of drywall, which is commonly done in workshops and sheds. The usual way to do this is to use 3/8" or 1/2" plywood, then paint it with a heavy white primer. If you don't want to paint it, OSB is also an option. Plywood weighs less than drywall in the thinner sizes, so it saves you some weight, but I do think it's wise to check out the structure before adding a lot of new dead load.
Bill
Residential structures generally have a big safety factor, the limiting factor almost always is deflection.
If the structure is not showing any of the typical trouble signs like bowed walls, sagging roof rafters, bent door header, I would not worry about drywall weight.
Slate is around 10 lb/sqft, snow load is probably 30 to 50 lb/sqft. Lightweight drywall is around 1lb/sqft, compared the rest, I would call that noise for most structures.
I tend to agree. Using plywood would also help to tie the structure together though. While I know some areas allow drywall to provide some shear strength in walls, I’ve never trusted it in any structural application.
Snow load is probably pretty minimal in the OPs climate zone too.
Bill