In-Line Booster for Heat Pump System

We’re installing an Arctic air-to-water heat pump connected to a hydronic radiant heat concrete pad.
The buffer tank for the heat pump system can also heat water for domestic use, but only to about 100-11o degrees. (Domestic water is heated as it flows through a copper coil inside the buffer tank.)
I’m considering a Rheem Booster in-line unit to bring the water temp from 100-110 up to 120-130. (The Rheem Booster is intended to be installed in line with traditional tank water heaters, to extend the hot water supply. When it’s in line with a water tank, it turns off the power to the electric water tank, and turns on the power to itself while it’s boosting–which doesn’t seem appropriate if used with the continuous warm water supply of our heat pump system.)
I’m wondering if anyone has the expertise to opine on whether this arrangement (Arctic Heat Pump>Warm water>Rheem Booster>domestic hot water) will work well. Thanks!
GBA Detail Library
A collection of one thousand construction details organized by climate and house part
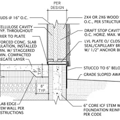
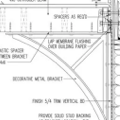
Replies
It would work. However, the Rheem Booster requires 30 amps! Can your electric panel fit that? An alternative would be a simple electric tank heater - it wouldn't need a high output since the ending temperature minus starting temperature is small.
I'm not sure I agree with your analysis here. Regardless of the low delta T, the tank will empty at the same rate and once it's empty you're going to be getting tepid water. The booster makes more sense to me. Presumably he's already accounted for the electrical draw.
It feels like overkill - save the amps for something more valuable than heating water. There's no reason for water heating to be just-in-time since it's so easy to store hot water. A cheap 50+ gallon tank could cut amps by 1/3 or more, give you a larger buffer and provide full hot water if the heat pump were to go down.
You may want to look at an AltSource with a preheat coil that feeds into a TurboMax for the final heat exchange. That would need a diverted between the buffer tank and DHW tank.
What I don't like about this is that the boost is going to run all the time. Let's say the Arctic provides 50 degrees of warming and the boost 15, that means that roughly a quarter of your water heating is resistance heat. It kind of defeats the purpose of using a heat pump.
How about just having a heat pump water heater inside the house? Much simpler, much cheaper. In the summer it's free cooling.
+1 on the HPWH. Tankless units are always maintaince, even with not so hard water, you end up having to descale at regular intervals. With a tank water heater, you install it and forget about it for the next 10 to 15 years.
If you haven't got the buffer tank with the indirect yet, I would skip it. If you look at the equipment cost complexity and maintaince down the road, for a very small efficiency gain the pre-heater from the air to water makes no sense. Get a stand alone heat pump water heater.
If you do already have the indirect, I would still get a HPWH as a booster. Not much extra cost and bit of free dehumidification in the summer time.
You want to run the booster at 140F especially if you are on well water. Use a thermostatic mixing valve to bring the temperature down to 120F for the house. If you use the pre-heater output as the cold feed for the mixing valve, running the tank hotter doesn't cost you much extra energy, keeps bacteria at bay and you effectively get more gallons of hot water out of the same tank.
Thanks so much to everyone who has contributed. It's going to take me a few days to digest and research these various ideas. When I can I'll send an update re how my search and decision process is going. Again thanks.
Some clarification: The hydronic heating system requires a buffer tank, or at least it's strongly recommended by Arctic Heat Pumps, as it provides a larger heat mass which saves on-off cycles, and provides a heat store. Also, the buffer tank CAN function as a standard water heater in case of very cold temps or heat pump failure. So we would have gotten the buffer tank regardless of the domestic hot water function.
The only addition required in order to get the 100 to 110 degree domestic warm water is the 160 foot copper coil placed in the buffer tank. The main water/antifreeze pool in the buffer tank comes from the heat pump then flows through the pex imbedded in the concrete slab. The domestic water enters the buffer tank through a separate port, flows through the 160 feet of copper coil, then exits warm (100-110 degrees) for domestic duty. So the domestic warm (100-110 degree) water is continuous, not limited by tank size.
What about in the summer? Do you have to have your heat pump on year-round?
That’s commonly referred to as a reverse indirect tank - a good choice for this setup. Another option would be an external plate heat exchanger fed by the buffer tank, but that would require a circulator. You'll have a good bit of capacity thanks to the buffer tank, but the hot water will not be limitless.
If it is DIY than by all means put in the coil although at current prices a pex loop is probably a much cheaper option. If you need to buy an indirect instead of a simple tank for the buffer than it is not worth it.
If you are looking to do cooling as well with the setup, you'll now need two buffer tanks which complicates plumbing. At that point the domestic pre-heat is definitely not worth it.
A radiant heat concrete pad by itself is a pretty large thermal buffer. You might not need much more than a small resistance tank with the elements removed or a large volume hydraulic separator. I would talk to the manufacturer about what they recommend.
@DC: in the summer the heat pump reverses to cool the concrete pad. If neither heating nor cooling is needed, then the heat pump can function primarily as an indirect water heater via the buffer tank. THanks.
@paul: Are you saying the hot water won't be limitless because the cold water going through the copper coil will cool the hot water in the surrounding buffer tank? I'm under the impression that the heat pump can keep the buffer tank contents hot while the domestic water continuously flows through the copper coil. ??? Not sure though. Thanks for the comment/.
@AKOS: It's not DIY. Arctic Heat Pumps has an option to place a copper coil in their buffer tank (which is an ALTSOURCE). ALso, I'm thinking copper will more efficiently allow heat transfer (compared to PEX) from the hot buffer tank solution to the cold domestic water in the coil. ???
This system will indeed have a separate tank for cooling. And the pump can alternate between warming the buffer tank for domestic hot water and cooling the solution in the cool buffer tank and the radiant heat lines in the concrete pad. Thanks for your comment.
So in the cooling season 100% of your domestic hot water is coming from the booster? That's when a heat pump water heater would work best.
At the price point of the an extra Altsource with coil, you will have negative ROI on your DHW pre heat, the cost of equipment will never pay in energy savings before you need to replace it.
You don't need anything fancy for buffer tanks. Get a side ported resistnace tank, remove the elements. Most will have 1"npt ports for the elements or can be converted to NPT with an adapter plate. These can be used for temperature probe or plumbing. The combination of elements/DHW ports /drain for connecting it up.
For efficiency you want the coldest temp water to be fed to your heat pump, so a T on the heat pump return is the best spot for connecting the floor return.
You want the bufffer tank plumbed up like this (minus the DHW indirect):
https://uh8ex3jph2xqg0pb4bs7if12-wpengine.netdna-ssl.com/wp-content/uploads/2015/12/new-buffer-layout1-768x595.jpg
@DC: During the cooling season (summer) the domestic water will be heated to 100-110 degrees by the heat pump, which alternates between heating the water/antifreeze solution for the AltSource copper-coil containing buffer tank, and cooling the water/antifreeze solution for the cooling buffer tank (not AltSource) and floor pex/concrete pad. The booster is only needed to bring the domestic water temp from 100-110 to 120-130. (And if in the summer we're fine with 100-110, we may turn off the booster, or turn down the min temp setting on the booster, and just go with what the heat pump gives us.
If you get a heat pump water heater as your booster, just use that in the summer and don't bother with a separate cooling buffer tank. Bypass the DHW coil that runs through the buffer tank for summer mode. The heat pump water heater won't be quite as efficient as the Arctic system but you'll get free cooling from it, and you'll avoid the need to cycle the Arctic between models, saving wear and tear and energy.
I was going to post exactly the same. No need for a separate buffer. Use the preheat in the winter, get free cooling in the summer.
I'm not even sure how the efficiency of the HPWH compares to the Arctic. In the summer I think you're miles ahead with the HPWH. In the winter, I'm not sure you're saving anything by preheating the hot water rather than just having the HPWH pull that much more heat from ambient. The heat is all coming from the same place.
"Are you saying the hot water won't be limitless because the cold water going through the copper coil will cool the hot water in the surrounding buffer tank? I'm under the impression that the heat pump can keep the buffer tank contents hot while the domestic water continuously flows through the copper coil. ??? Not sure though. Thanks for the comment/."
It will depend. You'll be heating the house and heating the water at the same time, so if house BTUs + DHW BTUs > Heat Pump output, the temperature in the tank will start falling. The Rheem Boost will have to compensate and you could easily exceed its capacity as well. The common situation would be a day when you're using say 75% of the heat pump's capacity for central heating and then you have a large hot water draw (bathtub, laundry, or a few showers for example). In that situation, maybe the heat pump has only 10,000 btus to contribute to DHW. It'll be much easier to have a 40-80 gal tank of 120+ degree water. I'd treat the pre-heat as a bonus and run the buffer tank at the lowest temperature required for the floors, which will maximize the central heating efficiency. If that's only 80-90 degrees, that's still significant savings. Basically the booster is limited in capacity, inefficient, and has a large power draw so unless you need to save space, there's not really any use case for it vs. a tank.
I'm going to go off on a bit of a diversion based on Akos' post #14. The image he links to shows the buffer tank in parallel with the heat distribution, which is configuration I haven't seen before. I've been thinking a lot about buffer configuration recently. In April I installed a Chiltrix air-to-water heat pump in my own home. Chiltrix recommends a buffer tank, and they recommend what I'll call a cross-connection -- the buffer tank has four ports, and the heat pump supply and return, and the heat distribution supply and return all mix in the tank. I've been doing models of cross connection vs. a serial hookup, where the water goes through the heat distribution and then into the buffer tank and back to the heat pump.
Attached to this message is a chart showing the modeled tank temperature over the course of an hour, for the cross-connected buffer tank and the following assumptions:
* Heating load is 6,000 BTU/Hour
* Heat pump produces 24,000 BTU/hr at 5 GPM. It cycles on when the incoming water drops to 110F and cycles off when it exceeds 120F
* The heat distribution can produce 12,000 BTU/hr, and is cycling on and off every three minutes.
If you look at the graph, you see that the heat pump cycles on for six minutes, then off for 16 minutes. There's a stairstep pattern as the heat distribution cycles on and off. This is the behavior you want basically.
OK, next graph is for the series-plumbed buffer tank. Same assumptions, but the output of the heat pump goes directly into the heat distribution. The blue line represents the tank temperature, and the red line represents the temperature going into the radiators/AHU/radiant loops. The blue line is actually exactly the same as the cross-coupled tank graph above, it has the same cycle time and the heat pump temperature is the same. However, when the heat pump is running the water going into the distribution is quite a bit hotter -- the red line rises above the blue line. When the heat pump isn't running, we're running on tank heat and the red line and the blue line are the same.
The question is whether this behavior is more desirable than the cross-coupled buffer. For heating, I'm not sure, there are actually advantages in a more stable temperature. For cooling, in my climate this absolutely is beneficial, because the colder the water the more dehumidification you get, and if you're paying to chill that water you want the full benefit.
OK, now the parallel buffer tank. For this one I had to add an additional assumption, which is how the flow is split between the buffer and the heating system. The assumption I made is that the heating system is on a zone valve. When the heating is off, the zone valve closes and 100% of the flow goes through the buffer tank. When the heating is on, 1/3 of the flow goes into the buffer tank and 2/3 goes into the heating.
Again, red is the water temperature entering the heating and blue is the tank temperature. The heat pump goes through the same 6 minutes on/22 minutes off cycle as the other two configurations, and the same temperature range. But look at the shape of the red line. As in the serial configuration, when the heat pump is running you get the hot water direct from the heat pump. But when the heat pump isn't running you get a mixture of tank water and return water from the radiators, which is colder than the tank water, so your input is colder than the tank water.
I would argue that this configuration has not benefits over either the cross-coupled or serial configurations.
Really interesting discussion! It's hard to know what criterion to consider in deciding which is best, but after thinking about it, I think what you really want it to minimize the return temperature to the heat pump, as that will drive the highest COP. From your plots, I think the cross connection is likely the best for that. But do you have a way to add that temperature to the plots?
DC,
That is good stuff, glad to see some analysis put into this. For increased accuracy, I would do a model with a buffer tank with stratification. In larger tank, the water out will be pretty close to what was supplied from the heat pump for a fair bit of time.
Might be also worth while to include return water temps in the model as well.
Thanks Akos.
For the serial and cross buffers the return water temp is the tank temp, the heat pump pulls directly from the tank.
Attached is a chart for the parallel tank that includes a gray line that shows return water temp. The return water temp is only lower than the tank temp when the heat pump isn't running! When the heat pump is running the return water temp is equal to or higher than the tank temperature. The reason for that is that in my model, when the heat pump is running and the heaters are running the water coming out of the heaters is hotter than the water in the tank and that gets mixed together to create the input to the heat pump. When the heaters aren't running the input to the heat pump is the tank.
I don't know how to model a stratified buffer tank. With the cross-coupled tank there is mixing and there shouldn't be stratification. I would think stratification would benefit the serial tank the most, but that's just a guess. If you're using the tank for both heating and cooling, unless you reverse the direction of flow from season to season stratification is going to work against you part of the year.
My model uses a flow rate of 5 gpm and a 17 gallon buffer tank, so the tank does a complete change about every three and a half minutes. So I'm not sure how much stratification is going to happen. That's the tank size that Chiltrix recommends. Their heat pump has a variable speed pump so I picked 5 gpm as a middle of the road number.
Either a modcon or a modulating unit, any type of mixing of return and supply means a bit of a hit in efficiency.
My thinking about these, design for the system to work with no buffer. The buffer if needed in the end should only get "overflow" not the main flow. This is why I like the setup in the link.
Not the easiest to set up in a spreadsheet, maybe a simple way to model a stratified tank is to model it as two separate volumes where the sum of the two is always the overall capacity of the buffer. This way the temperature of the two volumes can be independent.
This is great discussion as I will eventually have to convert two gas fueled radiant houses to air to water heat pump.
Akos,
" I will eventually have to convert two gas fueled radiant houses to air to water heat pump."
Your place?
[Replying to Akos' post #26 as we've hit maximum nesting depth]
For a heat pump, the primary concern is preventing short cycling. You want to have enough water in the system so that when the heat pump turns on it runs for a good long time, and then stays off for a good long time. This is particularly important in mild weather when the system is running at partial capacity, that's why I modeled a heat load of 25% of heat pump capacity.
Deleted
BTW here's my Arctic Heat Pump plumbing diagram:
I still say you're better off doing a HPWH instead of the on-demand. If you only do the pre-heat during heating season you can get rid of the 3-way valves and the cold buffer tank, you use the same buffer tank for heating and cooling. You can either put manual bypass valves on the preheat coil, or if you want to be fancy you can use the electric 3-way valves there.
I would skip the glycol injector. I know why they like them, when you commission a new system it takes a few days to get all the air bubbles out, the installer just wants to set it up and go. But once the system is set you shouldn't be adding fluid. If it needs fluid it means there's a leak, and you want to know about it so you can fix it. With the automatic injector a leak could go undetected for a long time.
Otherwise the diagram looks good.
@DC: Thanks very much. Very useful comments. I'll consider doing this.
Here is clearly the reason why air to water will always be a niche. Looking at that diagram there is about $25k in equipment and that is only to start. Still has to be all plumbed, wired and configured.
I really whish this wasn't the case, hydronics is so much more fun.
It's not just that it's more fun. If you need to get a certain amount of heating and cooling into a space, which would you rather run: an air duct, a copper pipe filled with refrigerant, or a PEX pipe filled with water? The PEX is just so much more practical. If what you want to do is deliver a small amount of heating and cooling to a lot of rooms hydronic is clearly technologically superior.
I think prices will come down with higher volumes. Think of how cheap something like a washing machine hookup box is, because every house needs one. The hydronic components aren't fundamentally more complicated, they're just niche items.
With high efficiency low load construction you need fresh air supply so you are already running a duct. A bedroom would need a 3" duct for fresh air, if I want to use the duct as dual duty for conditioning, that bumps up to about 5". Not really a lot of extra cost, complexity or labour.
PEX is easier to run but if you need to cool with pex you need to insulate and insulate very well otherwise you can have sweating and a lot of water damage form condensation. Takes a lot of time for the extra attention to detail to get this right.
There is simply no way to justify anything hydronic and that is coming from a guy that loves it. Cost and complexity is simply not worth it and at the end of day I don't think it is any more efficient than an ASHP.