Insulated garage: Insulate below slab?

Colder end of Zone 6A, Ottawa Ontario.
Attached garage/workshop, fully insulated/sealed.
I would like to heat the garage to keep it a few degrees above freezing, and temporarily heat the smaller workshop area to a comfortable temperature only when needed. The workshop area will only account for about 30% of the total garage space and will be separated by an insulated wall.
Since this is a new construction I am considering a hydronic heated slab, but I realize this would require insulating below the slab so the cost would not be insignificant.
Since the goal is to keep the garage at a low temperature, would a better approach be to NOT insulate below the slab and depend on ground heat for some of the heating? I believe annual ground temperatures are generally in the 40’s here, so with good perimeter insulation the slab could potentially stay above freezing on it’s own.
I’ve searched around a bit and opinions seem varied, with nothing really “concrete” (pardon the pun) and no real-world data to look at.
GBA Detail Library
A collection of one thousand construction details organized by climate and house part
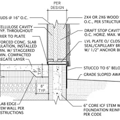
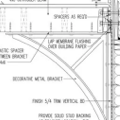
Replies
Lance,
At a minimum, you should install vertical insulation at your slab perimeter. The rigid foam should be 2 or 3 inches thick and at least 2 feet wide (with most of the insulation, obviously, below grade). The above-grade portion of the insulation needs to be protected with metal flashing, pressure-treated plywood, or stucco, and you'll also need horizontal Z-flashing between the top of the rigid foam insulation and the bottom course of siding.
I faced a similar decision when building my own garage in Vermont. The garage is unheated. I decided to install both vertical insulation at the slab perimeter and horizontal insulation directly under the slab, guessing that the advantages of the horizontal insulation outweigh the disadvantages.
The two-car garage attached to my superinsulated house is not itself superinsulated, nor is it heated in winter. The walls are just 2x6 studs, with well-installed FG batts. There is an R-30 loose cellulose layer in the attic space over it. There is a 2" XPS foam layer inside the short foundation walls, right down to the footings, protected by 1/2" Durock and capped by 2x6 to cover the top of the foundation and dadoed to capture the top of the Durock. There is no insulation under the slab. The back ten feet of the garage structure is an unheated workshop area, separated from where the cars park by a framed wall (2x4) and door.
Through nearly all of the winter, the temperature a few inches above the floor stays in the upper 30s (F). The coldest I have seen the garage temperature go, after a few days of nighttimes at or below zero, is 32-33. Any snow on or underneath the car melts off quickly inside the garage, making me wish I had installed a central drain and paid more attention to slope of the floor. I manage the meltwater issue by scooping up the melting snow shortly after it falls off the cars with a shovel. There is never any ice on the floor, even in the coldest outside weather I've seen here (Lakes Region NH, CZ6.
Lance,
Someone in your area may be selling reclaimed rigid foam. Reclaimed EPS or XPS is often a third the cost of new material.
One consideration is that even if the 40 F ground would normally help keep the garage warm, it's possible that some scenario in which the garage goes below freezing could lead to the ground under the slab freezing if it's not insulated, and perhaps frost heaving cracking the slab.
Another consideration is that in the summer, a slab connected to the cool ground can lead to higher humidity in the garage, accelerating rusting of tools and vehicles.
So I vote for insulation under the slab.
Thanks all for the replies!
Martin: I was planning to have vertical insulation on the inside of the garage foundation wall, going at least four feet below grade. Since I'm planning to insulate the rest of the house foundation above grade and a few feet below grade as well, it wouldn't be too hard to continue this around the garage portion of the foundation instead, as well as doing shallow vertical insulation to break the slab from the foundation. Do you have similar temperature information to what Dick is reporting?
Dick, thanks for the excellent report! It gets a little colder here than in NH, but with a little supplemental heat I think keeping the garage above freezing seems a reasonable goal. What type of garage doors are you using?
Steve, I've seen several people selling reclaimed board insulation and I'll definitely be looking for that when it comes time to insulate below my basement foundation (which likely will have hydronic heat) as well as for any below grade insulation I need on the foundation perimeter.
Charlie, good point on the humidity levels. I may install a minimal amount of PEX tubing in the slab even if I choose not to insulate; the cost would be minimal and would offer the option of heating it occasionally even if I didn't use that as a primary heat source. Because I will be going to great lengths to air seal my garage, I have considered using a cheap ERV to keep some ventilation in the garage area which should also keep humidity levels low. Even with a cool slab I think I'd be OK in the summer months.
Lance,
Q. "Do you have similar temperature information to what Dick is reporting?"
A. Here in Northeastern Vermont, we get stretches of weather with -20°F nights and daytime highs of 0°F. During the winter, snow and ice will linger inside the garage for days.
Martin, sounds similar to what we see sometimes in Ottawa. This year wasn't that cold, but we've had some pretty brutal cold snaps since I moved here in 2008.
Thanks for your input. With a well insulated and sealed envelope it would seem that not insulating the floor might be the way to go.
We are building in climate zone 5 - we are considering options for insulating the garage slab/floor. We continued the Zip R sheathing from the house on the garage. We are also insulating the ceiling as well. We are paying attention to air sealing details to keep the (attached) garage separated from the house by an air barrier...
In our current house, we heat the garage (around 50degF), I am hoping that we won't 'need' to heat this garage and that the insulation plus warm cars keeps the space warm. We will add heat in the future, if the garage isn't warm enough for us.
What is done at the side of the slab at the garage door? I can't imagine that the perimeter on that side can be thermally broken like the sides adjacent to the exterior walls of the garage can be broken.
XPS versus EPS type 9 under the slab?
Thanks in advance.
Mr. Afsari,
I see this thread is a bit old, but I now have three years experience with a zone 6a/b build that might be relevant to your question. My garage is attached to the house on one and a 1/4 of the sides of the total perimeter. I chose to insulate the exterior of the entire house/garage foundation with reclaimed XPS. (I get to feel green that way.) It was all 3", so R15 nominal maybe R12 functional. I also used it under all the slabs poured in the basement and garage to decouple from the ground. I also put in pex for possible heating. I did the work, so for a few hundred in tubing I covered my tail. I had extra foam panels so I insulated the wall between the main basement and the garage stem walls and the interior sides of the other garage stem walls. My thinking was to isolate the fill under the garage slab/foam and thus keep it at something like the roughly 50 degree neutral soil temp one would expect below 12' of depth. The fill inside the garage perimeter is native and lift packed pit run. (dirt and rocks)
The inside perimeter at slab/stone level was 1" xps board cut into 8" strips which included the door openings wall. I would have to go dig out the detail, but the 5" interior slab is actually in contact with the stem wall by a few inches of the walls total 8" pour width, the 1" foam between the interior slab and the exterior apron is set to have the garage doors kiss down onto it. The doors face south so even in the winter, the door side of the apron is probably not as cold as the parts out 12' . The garage doors are internally foamed polyurethane and seal quite well. The walls are a total of 4 1/2" of foam outside of the sheathing so roughly R16. The roof is 1 1/2 iso with 4" nailbase over that for about R22. The air sealing is quite tight even with three garage doors.
I am not using the pex. The garage will stay above 50 most of the time and if we drop into the single digits it will go down to 42 or so. The cars come and go just enough to keep things above melting points which sometime is quite messy. The snow and mud from the dirt roads here can be trying. The foam inserts at the door openings are surviving well beyond my expectations. I envisioned needing to devise some form of rubber insert to protect the foam, but time and my sloth have shown no need to do that yet. As long as I don't ding it with the snow shovel it seems to do fine. I should take some temperature readings and post those for your information. Maybe this weekend.
The fact that about 1/3 of the wall area in the garage is shared with the main house could be a major source of the warmth we are experiencing. The house walls are R19 batts in 2x6 with 2" iso sheets on the garage side with FireRock over that. I would guess a functional R28-30. I do think the fill under the slab is benefiting from all the insulation despite the 3" of foam separating contact. The foam only slows the rate of transfer, so without heat being added by the unused pex tubing, I suspect the neutral temperature of the slab and soil is buffering the dips in temperature.
I don't know what level of ZipR you have chosen, so it maybe a good idea to batt the inside and sheetrock the entire garage. Get good garage doors, pay attention to the seals and mounting, and be sure to check the seals on fire rated doors between house and garage. Ours work quite well. If you opt for a people door to the yard from the garage, don't stinch there, get a good one that seals to keep the envelope tight as you can. Steady air leaks will chill any garage fast.
Old thread, but things to consider:
If somebody accidentally or deliberately leaves the garage door open for a while in this scenario five or ten or twenty years down the line, what happens?
Similarly: Is the garage door sealed well enough that if the heat were to go off for a few days, you could plausibly count on seasonal-average-soil-temperature heating? Garage doors are notoriously poorly sealed.
Lastly: Once you get to hot, humid temperatures, an uninsulated slab is going to cool air down to ground temperature, and leave the moisture behind. If you've sealed the garage up tight enough to function in winter - are you okay with high levels of condensation and high humidity in summer?
In summer, you could leave the windows and/or doors open enough of the time to warm the floors. Once you get past the initial condensation and the floors warm up, you should be able to maintain similar indoor/outdoor humidity levels. If your region is especially humid in summer, a dehumidifier will both warm and dry the air at a relatively low cost if the space is properly air sealed. This is also an easy thing to add down the road if needed. In CZ6, you probably only need it for a couple of months.
Burninate, Not sure what the point of asking about leaving a door open is. I can tell you for sure if someone leaves the door open during the winter here, it is going to freeze everything. I had the same principle demonstrated to me on a rental I took care of. The renters went off on a ski trip for a long weekend without remembering to close the door. Fortunately, no one robbed the place, but the water pipes in a shared wall were none to happy. Neither was I or the landlord.
Garage doors are indeed notoriously poor at sealing or insulating, but good ones do exist. I did point out the need for buying quality. I would point out that if the heat goes off for a few days then a cold garage might the least of your concerns. The rest of the house with all its pipes it the greater worry.
For my particular garage and climate humidity is not an issue. We are not quite desert level. In the midwest where I moved from the risk of dank garage smell is quite real if one seals it up thoroughly. Another risk is slippery floors if you put down the epoxy paint that has become popular. Bringing home a freshly washed car to a well sealed garage can create a slick film of condensate. I chose not to use epoxy to avoid that condition even with low humidity overall.
Sharing the details of my situation might not be repeatable everywhere, but the idea of GBA is to offer up discussions that at minimum give questioners aspects of building to consider. If they have an exact situation match then so much the better.
Roger,
Do you have to have a picture of the area where the garage door closes onto the foam?
I appreciate everyone’s input.
Thanks,
Alan
Alan,
Finally got time to sit and respond. I will be of course humiliating myself before all of GBA by revealing how slow I am to finish my projects. My wife is already overly familiar with the trait.
I took the temperature of the slab and the foundation perimeter both near the garage doors and back near the wall shared with the house. Right near the house, where the slab contacts the basement foundation I am holding about 54F on the slab and 58 on the wall. About six feet out from the house wall the slab reads 47F. Surprisingly, the fall off from there to the garage doors (about 18') was only 1-2 degrees according to the thermocouple sensor I use. The house foundation is not isolated from slab contact so I am definitely losing heat there. My bad.
The exterior temperature at the time was 30F, the air temp in the garage was 45F. The slab was mostly 47F and the apron 35F.
The slab is isolated from the garage apron at the door openings and the two sides of the garage not sharing contact with the house. The slab is pretty consistent as noted and running about 12 degrees warmer than the outside concrete apron. It can be a bit slippery to conclude how much the losses I am suffering from using only 1" blueboard to make the break. The doors all face south and the sun load here is quite high. I planned this to make use of the warmth to minimize the ice and snow build up on the apron. Works pretty well out to about 9'. After that it is a frozen hellscape.
I am likely seeing losses via the rebar and contact I make with the foundation at the openings. The cement contractor really recommended against trying to float the slab on the 3" reclaimed XPS as a completely unbound element. Probably a good call, as you can see the apron and slab are holding position quite well. The kiss mark of the door gasket can be seen in the sun fade and grime lines. Originally I had planned for the door gasket to kiss down on just the foam line, but best made plans of mice and men sometimes go awry. Please ignore the unfinished door trim on the sides.
The garage insulation levels are modest compared to the house,R-19 walls, R-20 roof. I only wanted to moderate the temperatures inside. Summer build up from the sun on the doors, which are nominally R11, gets the heat up to mid 80s. Still as I have noted in early comments it rarely goes below 40 and mostly hovers around 50. Hope the pics posted help you in figuring out your garage design.
Alan,
Small addendum. The foam has been exposed as you see it for three years now, with the car going over it unprotected. I had intended to trim the foam and pour in some of the crack sealant sold for patio cracks or the better quality concrete sealer in caulking tubes. As noted, I don't get my projects done.
Also, the seeming inconsistency of R value for the walls of the garage is due to remembering I have 4.5" total foam on those walls thanks to the fake stucco base foam. Thanks to all the foam being outside of the sheathing I think it is safe to guess that the functional whole wall value is close to R-19 including air film effects.
reviving an old thread. I have a few questions, about to pour a garage slab in zone 5a
1. Can I use "normal" EPS for under slab? Other areas I put 2 layers of 2" EPS under the 4" concrete slab. But the garage slab is obviously holding up the weight of cars, so I wonder if the compressive strength of normal EPS (very compressible!) is ok.
2. How much insulation should I install under the slab
3. Do I still need a vapor barrier? Would taping the foam sheets or staggering the foam sheet layers act as the vapor barrier?
blamus20,
The foam typically seen at my big box store is not dense enough to use to my mind. It sounds like you have already done a house slab, so what follows may not reflect your experience.
I did not use EPS for fear of low durability during construction. I personally would use XPS which is tougher even at a 15 psi rating. There are lower GWP extruded foams available in some markets though they remain a bit hard to source and can be spendy. In Colorado the Corning low GWP XPS is very close to the same price as the traditional Foamular. Lead times are long though. When I built in 2015 there were ample supplies of reclaimed foam, so I ended up with 3" sheets of 25 psi XPS taken off a commercial roof.
It proved to be very durable, surviving much stomping about setting radiant loops and mesh. If you can find reclaimed XPS or the new low GWP I would recommend it. High psi EPS does exist, but I have not found it readily and it costs more.
There is disagreement about the water absorption behavior of EPS vs XPS which really should be mostly moot if the foam is properly set on a drainage layer of washed rock that keeps the foam above any bulk water. I think you will still want to put plastic film on top of the foam to ensure a better barrier to moisture. In the case of EPS, a film barrier will keep water from migrating out of the concrete and keep the curing rate as intended. Taped sheets in two XPS layers should work as well, but I prefer to use the plastic film and just enough tape to keep the foam sheets from skidding around. My back and wallet approve of this method. HD has a nice filament re-inforced plastic sheet that is quite reasonably priced.
Regarding cars and loads - Many cars approach 4,500 lbs empty, so each tire print is roughly 1125 lbs. The car's psi presented is higher though since contact area per tire is well under a square foot. Some EPS stock is 10 psi (or less) or 1440 lbs per sq ft. although with a theoretical compression limit of 10% or >3/8". The slab alters the way the weight acts.
A concrete slab redistributes a cars weight over more than the "footprint" of the four tires, so on balance the load seen by the foam can work with 10 psi foam. 15 psi foam is better simply by being more durable during construction activity. I had 25 psi foam so I did not worry about the compression factor or durability. If you are parking a F250 diesel dually inside you might want to go with a 5" pour and rebar along with a synthetic fiber to minimize crack potential. Hopefully, better informed concrete opinions will be offered. Don't forget crack relief cuts.
As to insulation thickness, R15 is code here in CZ6 for interior slabs with no garage slab rating. I went with R15 under a 5" slab since I have R20 walls and R24 roof. My shared wall with the house is R34. It can get to 35 on really bad nights, but mostly it never goes below 45. Your mileage may vary.
If the slab you are getting ready to pour will be up against the house slab I would put in a foam separator at the house edge so you don't pull heat from the house slab.