Insulated rim joists with concrete patio close to height of sill plate

Hello, Being a DIYer who noticed several articles about the benefits of sealing rim joists with foam board, I decided to do the same in my house with 2” XPS and great stuff around the cracks. I live in Idaho zone 5a, the house was built in 2006, and additionally has a 1/2” layer of exterior (EPS or XPS) under the siding. There are overhangs with gutters all around the house. The foundation is 6-8″ off the grade in most spots. My main concern is that I have a large concrete patio in my backyard that spans the entire back foundation wall of my house, and is quite high up to the foundation, with a 1.5” gap from patio to siding, and therefore maybe a 2-4” gap between the patio and the sill plate. Do you think this set up will be a severe issue in terms of bulk water entry and drying potential? If so, is there anything I can do to prevent water from getting to the wood behind the siding, like metal flashing? Or should I simply remove the foam board, as there were no problems before I installed the foam?
GBA Detail Library
A collection of one thousand construction details organized by climate and house part
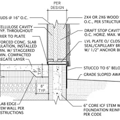
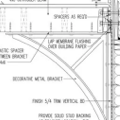
Replies
1/2" EPS will allow for quite a lot of drying potential for the wood. You shouldn't have a moisture issue with the rim joist.
Bulk water could possible be a problem. Your concrete slab should be pitched away from the house so that water runs AWAY from the house, and doesn't pool up near the foundation. If the slab is not pitched properly, you can use concrete resurfacing compounds to build up the slab near the house so that you have a surface that will cause water to run away from your foundation.
I suppose you could use some flashing to keep water coming down the siding from getting into the gap between the slab and rim joist, but that still depends on the slab being pitched away from the house for proper drainage.
Bill
Hi Bill,
Thanks for your response. The concrete slab is graded, allowing water to run away from the house and onto the grass. But I still worry about that little of a gap being between the patio and the sill when the the wood can't "breathe" on the other side, even though the sheathing is covered by a housewrap. Am I overthinking this too much? Curious if anyone else has any suggestions. I'd really like to play this as safe as possible.
Andy,
To pick up on what Bill said: Building codes mandate the distance from ground to the top of the foundation (typically 6" to 8"), but not the distance between finished surfaces like slabs for a couple of reasons. First because they assume they are designed to stop bulk water from pooling next to the foundation, and also to provide a gap between plantings and the bottom of the siding, so they don't grow up into the wall.
As Martin frequently points out, the distance necessary to protect the bottom of walls from splash-back is a lot higher that 8". So if your slab is sloped the right way, you don't have planting that can infiltrate the wall, and you have good overhangs to deal with splash-back, the 2" gap shouldn't be any more of a problem than the 8" you have elsewhere.
Will the interior foam decrease drying to the inside enough to make the rim-joist vulnerable to rot? I think it's more probable that keeping interior air and moisture from getting to the rim-joist will more than offset any drying to the interior that occurs now.
What if the foam on the exterior were 1/2'' XPS insulation, do you think that would be an acceptable set up?
!/2" XPS is about 2 perms. Your interior foam will be about 0.5 perms, so the drying should exceed the wetting by a sufficient amount to be safe.
Thanks!
Another question and thank you for your help so far... My crawlspace walls are insulated with r10-r15 fiberglass blankets that hang from/are stapled to the sill plate. I've read that's not best practice but seems to be common in unvented crawls here, likely due to how dry our summers are here. As long as the walls stay dry this set up shouldn't be problematic in terms of condensation and mold I assume? There is a vapor barrier on the ground that's sealed a few inches up the walls as part of our radon system. I assume that would help prevent the batts from getting soggy at the bottom.
Andy,
The most common method of insulating crawlspace walls here are fibreglass batts that come wrapped in plastic, which is an advantage as far as maintaining the insulating value of the batts, and keeping them dry.
As long as you aren't seeing mold on the foundation walls, or moisture in the fiberglass, the only disadvantage of hanging batts is they don't provide much insulation without being encapsulated on all sides. The preferred insulation is rigid foam, which sometimes needs to be covered for code reasons to do with it being imflammable.
Malcolm,
The requirement of a 15 min thermal barrier is exactly why i'd rather stick with the fiberglass blankets. Whereas I can simply place mineral wool behind my insulated rims as a thermal barrier, I can't with the walls unless I use a thermal-rated foam, which would be very costly. While my batts aren't encapsulated on all sides, as far as I can tell they stay dry and there isn't any mold on the walls so it is most convenient for me to leave them. Thanks for your help!
Deleted
Update... after getting a good look under my siding it would appear that the foam board sheathing is faced, likely with polypropylene. That would make the sheathing vapor impermeable correct?