Insulating

Ok, didn’t plan to well & some instructions just ignored. Have had two contractors so building somewhat cobbled together. Need determine/clarify what to do in getting the place insulated. No dense pack providers & super expensive for loose blow. Everyone uses fiberglass around here.
Rural Mountains Upper East TN at KY/VA border climate zone 4a. Off-grid. Heat wood backup propane. No HVAC. Basic rectangle 28×52 over full walk out basement facing S/SE. 6:12 roof with 3:12 sloped inner ceiling/cathedral 2×4 ceiling trusses inside for 2/3 house. Rest flat ceiling with a small (short) room above for a range boiler to hydrosyphon from wood cook stove for hot water. No extra heel height. Roof is metal with UDL 30 underlayment over osb sheathing. Full ridge vent. Truss design allows relatively easy & plenty of room to access from stairwell & flat ceiling end.
I wanted to just use t&g for ceiling but reading says that is a no-no. Plan is to use soffit vents (accuvent adjusted to 19.2 oc or custom made-would permaR polystyrene stay together long term as a baffle material?). Blow all borate cellulose to aprox R38. No inspections except electrical if off-grid but trying to do by code if also good building practice. Absolutely don’t want rot!
Walls are 2×6 on 16oc. Plan to use Roxul R-23 batt. Siding will be rough cut dutch lap pine sealed all sides. Taped Tyvek, osb sheathing. Windows/doors all properly flashed. Osb vertical sheathing seams didn’t get sealed before tyvek.
Is there a way to not have to do two layers (dry+t&g) everywhere considering no HVAC? CertainTeed Membrain? I’ve had to re-do most things so far & another expense is tough to swallow especially given work won’t be done to level necessary to air seal so still need to deal with that after or do the drywall myself. Electrical was roughed to 1 layer so have to adjust or add rings to all (lighting is all surface mount).
Porches 32’ wide added on after the original roof. There is a gap between those two roof lines that is closed but not sealed on sides. layers are Metal roof/UDL30/sheathing, 2×6 rafters, space 0-2’, UDL30, sheathing, original trusses. What if anything should be done with this space? Leave as is no insulation or venting?
Will blow in cellulose stay put on 3:12? At wall side it would be filled to the baffles.
At the heel insulation space is limited at 3.5” at outside edge to 5.5 at inside edge. I’m thinking using roxul bat for that area before the blow. Or would something else be better to match my wall insulation value?
Is there a good low cost sealant to seal bays & plates. Seems something with good elasticity necessary. I like Big Stretch but for quantity needed that will get expensive real soon. Any experience with the Dupont Exterior with Kevlar (local supply has inexpensive & says 800% flex). Or is can window/door flexible enough? Even though about a 2 part pack to just go around air sealing but I’m not totally comfortable with foam in general..
As for my siding, thinking drain plane using folded 30# roofing felt strips stapled thru tyvek over studs which will also mark locations to fasten my siding. What would be minimum gap to wall to accomplish drain plane? Wood sealed all sides & smooth on back so no resistance to water flow there. I have left over UDL30 that could be cut into strips but was thinking the asphalt felt provide some fastner sealing that the UDL30 wouldn’t. Any thoughts?
Any diy creative ideas to accomplish a no rot/moisture problem given the place will not have HVAC! Good breeze for summer but protected winter storms & keep windows open and/or cracked most of the time. Thanks!
GBA Detail Library
A collection of one thousand construction details organized by climate and house part
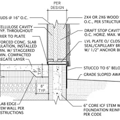
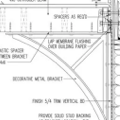
Replies
Glenn,
I think you need to slow down and take a breath. You should ask one question at a time; you are all over the place.
I'll tackle one of your questions: Neither loose-blown cellulose insulation nor mineral wool insulation is an air barrier. Both types of insulation are air-permeable, so you absolutely need an interior air barrier.
Taped drywall is certainly the best interior air barrier in terms of cost and durability. Tongue-and-groove boards leak air like a sieve; they are not an air barrier.
MemBrain is relatively thin and fragile. In theory, you could try to detail MemBrain as an interior air barrier, but I don't recommend that approach. It is too flexible and fragile. I advise you to use taped drywall as your interior air barrier.
As I'm sure you know, taped drywall is a perfectly acceptable finish material. You don't need to install boards over the drywall. But if you want to install tongue-and-groove boards on the interior side of your taped drywall, you can. The nails used to fasten the boards will not significantly affect the performance of the drywall as an air barrier.
-- Martin Holladay
Glenn,
Is your home dried-in at this point? Where are you in the construction process exactly?
If it's not already been insulated and drywalled, the untaped OSB sheathing can be caulked to the framing inside every stud bay with polyurethane caulk to air seal it. It will also take a bead of polyurethane caulk between any doubled up framing such has top plates, etc, and between the bottom plate & subfloor. That make it every bit as air tight as taped seams on the exterior as the primary air barrier. It goes surprisingly quickly with powered caulking guns and a case of caulk.
Polyurethane caulk is not exactly "low cost", but it does retain flexibility & grip over time, and it isn't as messy to deal with as "never dry" goops like acoustic sealants (which has been the traditional gold standard, despised by drywallers and insulation contractors alike.)
That does NOT mean you can then ignore air-sealing the interior sheathing, since wintertime air leakage from the interior can leave copious quantities of moisture in the OSB.
Make sure to air seal electrical boxes & electrical/plumbing penetrations in all framing. (Much of that can be done with PU caulk too.)
Buy a batt knife, and take your time sculpting-in every batt, splitting rather than stuffing around wiring & plumbing, and around electrical boxes, etc, taking care to tuck in every edge & corner to ensure full contact with the OSB at the framing, then tugging it gently back to where the interior side of the batt is just proud of the framing for a compression fit when the drywall goes up.
Wow, thank you both for such quick responses.
Sorry Martin if you think I'm all over the place. The questions are all related as need to determine/confirm how to proceed. The place is dried in. No insulation or drywall yet, thus the questions. You have confirmed what have been reading but was hoping there was another alternative even though sure there wasn't. This was to be rustic farm cabin & I do not like drywall. I'm trying to confirm my path forward so don't have to re-do anything else. Have full length decks that builder refused to flash (deck is bolted to house) & ignored my request to let me install the deck boards so having to deal with that before can even put siding on. Deck boards all perpendicular to house & screws were embedded deep. Lots of time & $ just trying fix things before can move forward. Since I have to switch back & forth between projects due to weather or helper availability I need materials on hand. Answers to all are important. It is a long way to town so can't just run out for an extra bit of this or that (which more often than not is only available 1.5 hrs away &/or has to be special ordered) & try to consolidate getting materials in as few trips as possible.
Dana, I'll continue with plans to seal everything which was my goal just trying determine best product to use. Thanks for narrowing focus on that. I wasn't too thrilled about the acoustical sealant option. .
What if anything should be done with the dead space between the two roofs. The porch roofs tie in aprox 1/2 way up to the ridge.. If something needs to be done, now is the time to be doing it. before siding & interior ceiling in place. Will be happy if it can just be ignored as not looking for more things to do.
You both have helped a lot! This site is a valuable resource & I've spent many days perusing the knowledge it contains. But nothing like direct answers for a specific situation.
Glenn,
Q. "Porches (32’ wide) added on after the original roof. There is a gap between those two roof lines that is closed but not sealed on sides. ... What if anything should be done with the dead space between the two roofs? The porch roofs tie in approximately 1/2 way up to the ridge."
A. Your question is unclear. Is the gap between the porch rafters and some (unnamed) component of the building? Or is the gap between the porch roof sheathing and the sheathing on the main roof? Or is the gap between the porch roofing and the roofing on the main roof?
Unless you describe the gap -- telling us the materials on each side of the gap -- we can't help you.
-- Martin Holladay
Sorry if description gap not clear. It is the space between the two roofs which extends half way up to ridgeline.
The outside edge at house wall plane has been closed in with sheeting & blocking which leaves a triangle of air space between the two roofs. Layers from top to bottom are porch roof = metal roof/UDL30 underlayment/sheathing/rafters then closed in gap/air space gap then old roof = UDL30 underlayment/sheathing/roof truss then my insulation at the heel.
I'm thinking not an issue as the insulation envelope will be below & space fluctuate with outside air temps. However, any chance condensation? Any moisture that might develop inside that space would run down the UDL30 water & air barrier & hit the sheathing at the wall plane.
Glenn,
You wrote, "It is the space between the two roofs which extends half way up to ridgeline."
This is still unclear. You need to use words like rafter, sheathing, roofing, or flashing -- or else we will never know what you are talking about. Maybe the sketch below will help you.
-- Martin Holladay
.
I am really interested in this issue. I have a "dead space" located where one roofline met an older roofline creating a triangular space with zero insulation and zero ventilation. The rest of the home is sprayed with closed-cell. This "dead space" was created by part of a new roof that was added for an addition which included an enclosed porch. I am in the middle of rebuilding and finishing the porch space to full living space and opened this "dead space" up when removing some older sheathing. Any advice would be helpful. Happy to provide more pictures as well.
For clarification, there is spray foam on the underside of the old roof as shown in this photo (old roof shingles visible). My question would be whether I should be concerned about this space if I were to add a wall covering this up. From the point of view of my photo, I would be located in the old porch, which is to be converted to conditioned living space, also spray foamed ceiling and walls. I plan to spray this cavity completely since it is currently open and visible, but I am aware of two other places similar to this one on my home, but neither abut an outer wall, just the non-sprayed underside of the roof.