Insulating a 5/12 scissor truss system
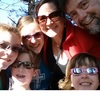
A builder is building the shell (dried in, with siding) and I’m increasing the insulation and air tightness.
The rear rooms in the house have vaulted ceilings, with a 5/12 roof and 2½/12 ceiling.
The builder doesn’t usually build with raised heel trusses and so the quoted price was high.
As a note, I can not fathom how to blow cellulose on the back side (away from the larger attic) of a scissor truss attic once the sheetrock is covering the ceiling. For this reason, I was going to sheath the vaulted ceiling with osb and create an air barrier before the sheetrock goes in. I will blow cellulose in phases as I sheath off the ceiling.
Anyhow, there is still going to be scant insulation for at least 2′ as the trusses get really shallow as they approach their bearing.
My idea is to install 3″ of polyiso to the ceiling, extending 36″ up the vaulted ceiling. Install 1/2″ battens over (under) the polyiso and screwed into the trusses. Fur the remaining ceiling down with 2x4s on edge (countersunk screws into trusses).
This set up still doesn’t give me R49 to the edge but it does give me R29 aged at the minimum instead of R14.
The great room wall is inset 24″ from the other wall. Both are shown together in the drawing.
Is this a reasonable, second-best solution to the cold edge problem?
[Chrome and Firefox keep crashing when I try to attach the picture. I’ll post it when I can.]
GBA Detail Library
A collection of one thousand construction details organized by climate and house part
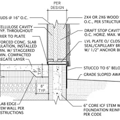
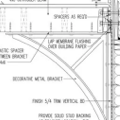
Replies
Mark,
If you chose the wrong trusses, and the trusses are already installed, that's a hard problem to remedy.
What is the available height for insulation and venting near the eaves (distance from the top plate of your exterior wall to the roof sheathing)?
Here's the drawing.
There is 4 3/4" at the inside plane of the wall to the underside of the vent baffle. 24" in from the wall (where the wall steps in), there is 9 3/4" below the baffle. I don't reach R49 until I'm in 4'9".
Adding the polyiso doesn't cure the whole problem of the cold edge but it goes a long ways.
In the drawing, the blue is the cellulose and the 3½" strapping is shown below the ceiling plane (but not labeled).
Now that I look at one more time, if I strap the ceiling (3½") and fill that with cellulose and skip the polyiso, I would be adding about R10 instead of an aged R16.
Is that ∆R6 worth the cost and trouble?
Mark, that doesn't look like a raised heel... is that what you were saying, that you didn't go with the raised heel?
Correct. No raised heel because the builder doesn't use them and was going to charge disproportionately for an 8" heel.
What is your climate zone? I think if you have the room you could scab down a bit more to make room for additional insulation and avoid condensation at the thinnest portion of your roof.
I'm in 4c. The plans examiner yesterday said, "Do the best you can," in reference to insulating the attic near the edge.
Whatever I do is already better than code. Two of the bigger builders in town who advertise how green they are don't use raised heels -- their attic insulation gets very shallow too.
Between builders not wanting to do incremental improvements, lumber yards not stocking good products (Zip sheathing) and code ignoring the obvious problem areas, there is much room for improvement BUT it's difficult even for those who want to improve.
Mark,
First of all, I'll remind GBA readers that it's important to think about insulation before a house is framed. For more on this topic, see Plan Ahead For Insulation.
The way I read the sketch, your trusses provide a gap of 4 3/4 inches at the interior side of the exterior wall. The height at the exterior side of the exterior wall is more relevant; that gap appears to be only about 3 inches. If you create a 1 1/2 inch deep ventilation channel using 1/4 inch luaun plywood, you'll take up 1 3/4 inch, so the space left for insulation is only about 1 1/4 inch.
At this point, it's going to cost you a lot of money to fix this error. I'm guessing that the cost to fix the error is going to be more than what it would have cost you to buy the right trusses in the first place.
You wrote, "Whatever I do is already better than code. Two of the bigger builders in town who advertise how green they are don't use raised heels -- their attic insulation gets very shallow too." Your logic is flawed. If the other buildings in your town use trusses like the ones in your sketch, they aren't complying with building codes. The local building inspector may be looking the other way, but the approach shown in your sketch doesn't provide enough room for minimum R-values to be achieved.
You are aiming for R-49 insulation. That requires 13 1/2 inches of cellulose, or about 7 1/2 inches of closed-cell spray polyurethane foam. Your trusses make it impossible to achieve this level of insulation above the top plate of your exterior walls (where you really want it). If you want to achieve R-49 elsewhere -- and I think you should aim to do that -- you'll have to lower your ceiling.
Mark,
One more point: You informed us that "a builder is building the shell," but you were a little vague about the current state of completion. If it's not too late -- if the roofing hasn't been installed yet -- another possible fix would be to install an adequately thick layer of rigid foam above the roof sheathing, as described in this article: How to Install Rigid Foam On Top of Roof Sheathing.
The costs of insulating at the roof deck compared to at the truss chords is (in most cases) a much bigger up-charge than the cost adder for energy heel trusses.
Even in earlier versions of the IRC, code-min for zone 4C was R38. Trusses that don't have at least a foot of space over the top plates of the exterior walls to accommodate vent-channel + insulation is nowhere NEAR "better than code" status in zone 4 for any home built this century.
@Dana
But Dana, don't you know that it's too difficult for builders to learn how to install raised-heel trusses !
I feel really bad for the OP as it seems that the local builders have him over a barrel.
Wait now. The builder probably knows quite well how to use raid-heel trusses and that's why their quote was higher. Standing trusses and sheathing the roof on a typical house usually takes a crew two days. Blocking and sheathing between the raised-heels can add another morning to full day depending on whether the blocks need to be engineered. So why should the quotes be the same?
If an owner chooses to include building features that enhance the energy performance of their house they need to pay for them. Just like upgrading their cabinetry of anything else.
What, rocket science wasn't until the NEXT semester? :-)
I realize these comments aren't very helpful for Mark's situation...
The cheapest code-compliant insulation job & the roof deck may get real push-back from the contractor, but it's worth running up the flag pole. If there is a local source for used/reclaimed rigid foam, 3" of rigid polyisocyanurate on top of the structural roof deck held down by a nailer deck for the underlayment & shingles through-screwed to the structural roof deck can be pretty cheap, followed by 6" of half pound open cell foam on the underside of the roof deck. The 3" polyiso runs about R17, the open cell foam R22-ish, and while that's still less than R49, with the amount of thermal break of exterior foam & encapsulated rafter elements on the trusses will come pretty close to a code-max U0.026.
In my area 3" reclaimed polyiso is $20/sheet (+/- $5) for nearly-perfect 4x8 sheets, or about 65 cents per square foot, and 6" of open cell foam runs $1.75 per square foot, then there's the cost adder of the nailer deck & screws and the additional labor, but with a reasonably trained crew it should come in at about $5-6 per square foot, well under the $8 per square foot cost of 7-8" of closed cell foam (R49) on the underside of the roof deck would be (and a heluva lot greener too!)
I come to GBA so that I can do better. You guys are a great help. Thank you.
If I can learn to clarify myself here, I should have no problem with the inspector.
1. We will break ground in about five weeks.
2. Assuming that the top chord bears on the exterior edge of the wall, 5/12 roof pitch, 1 1/4" for air vent and baffle, there is, or will be, 2 7/16" for insulation at the exterior side. The drawing is my estimate based on other scissor trusses I've seen.
3. I questioned the plans examiner on this point on Wednesday and he said, "Do the best you can." Minimum R values are not required/enforced at the edges.
4. Since code allows this diminished amount of insulation at the edges, whatever supplementary insulation I install, such as strapping the ceiling and filling with cellulose, I am doing better than code because code, as enforced, is poor.
5. What passes for "green" in the industry - I quote a local builder's website, "Green Components, The Authority In Green Building" - is lacking also. That builder's top chord bears on the exterior side too and they will have 2 7/16" of insulation at the exterior side and will pass inspection.
6. This problem area of mine is 34' in length along part of the back wall. The front of the house has a covered front porch and the attic depth at the front wall is over 2'. The interior rooms abut the garage for ~34' on the front and the attic depth at the interior/garage wall junction is several feet. The sides of the house are, or I should say, will be, the gable ends and will accommodate the necessary insulation. To raise the heel on the back 34' requires raising the heels for the entire house and the cost becomes disproportionate to the benefit.
7. Strapping the ceiling in this one room (great room) might be a PITR but the cost is in the few hundreds of dollars plus my time, not several thousand plus educating the framing crew. The incremental increase in R value at the edge is large and I can do all this after the shell is complete.
8. Is this a reasonable solution to the poorly insulated edge problem?
@Malcom
Apologies. I didn't want to imply that the cost should be the same because of course it shouldn't be the same, but you might agree that when a builder doesn't want to do something they discourage it by quoting an exorbitantly high price. Blame it on my inner curmudgeon. :)
Mark,
It sounds like you have come up with a solution that satisfies you. If so, proceed.
I wouldn't be happy with your solution, but I'm different from most builders. I'm a stickler for insulation details. (I also live in a colder climate than you do, and I care more about ice dams than you.)
The Achilles heel of your solution is the fact that there is so little insulation above the top plates of the exterior wall. Dana Dorsett's solution (with rigid foam above the roof sheathing, and open-cell spray foam under the roof sheathing) is more satisfying from a performance perspective.
Here's the BIS approximation of the heat loss through the ceiling (22°F design temp, 2265 ft² total, 34'x3' area of shallow attic insulation, not using differential calculus to get the exact loss over those 102 ft²):
The 102 ft² is 4.5% of the total area and represents 14.2% of the heat loss through the ceiling. If I only look at the great room (not shown), the 102 ft² is 11% of the area and 31% of the heat loss.
To look at it another way, the 102 ft² lowers the entire ceiling average from R49 to R44. Looking at just the great room, it lowers the great room ceiling average from R49 to R38. It's not as extreme as Allison Bailes attic stair example (http://www.energyvanguard.com/blog/34932/Attic-Stairs-A-Mind-Blowing-Hole-in-Your-Building-Envelope), but it's heading in that direction.
Mark,
You make an important point about the use of the word "green" in the construction industry. "Green" has no legal definition, so any builder -- including a builder who skimps on insulation thickness -- can use the word "green" without fear of being hauled into court.
That said, even a cursory look into the issue on the web shows many web sites that emphasize the importance of including the full thickness of insulation over the top plates of the walls, as the images below demonstrate.
.
Martin, I hear you.
Lowering the ceiling plane (and installing a fireblock at the new ceiling/wall joint) strongly resembles the raising of the top plate like you show. The fireblock starts looking like the original top plate and the wall cavity between the new fireblock and top plate becomes part of the depth for the attic insulation. For that little cavity, I could cut and cobble it with polyiso and quickly have my full insulation.
Call it a tray ceiling and it becomes a feature.
John
No need to apologize. You would be right about builders charging too much for things outside their comfort zone more often than you would be wrong.
It's really hard to get a grip on the effect of energy improvements on construction costs. So much comes from the advocates of various approaches that you can't trust a lot of the numbers.
I'd be inclined to think about Jon R's suggestion of adding trays or bulkheads at the perimeter. They often add rather than detract from the architecture.
Jon, Yup. Properly air sealed, of course. The master and another bedroom have flat ceilings and a shallow attic over two walls in each bedroom. Those will both get the trays - insulated where needed - and will look sharp.