Insulating Concrete Block Wall with Embedded Joists

I own a 2 story concrete block construction home build in the 1920’s timeframe. The floor joists are set in the concrete block. The interior walls are comprised of vertical firing nailed into inserts in the mortar joints and horizontal lath nailed to the firing strips and plaster. I have insulated the core of the block walls by injecting foam.
I am planning on removing the plaster and maybe the lath, framing 2×4 interior walls rewiring, insulating and finishing with drywall. I have done some studying on insulating basement walls including reading a couple of Martin Holladay’s articles in Fine Homebuilding. In my study, I understand the concern with condensation and moisture and I want to make sure I am planning and executing this job correctly.
I live in climate zone 5 (SW Michigan) which got me thinking my above grade walls will get much colder than basement walls possibly requiring a different design. Any guidance is very much appreciated.
GBA Detail Library
A collection of one thousand construction details organized by climate and house part
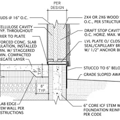
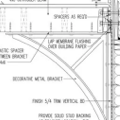
Replies
What is the finish on the exterior of the home? You may want to consider the effects of freezing on the block. If you insulate the inside, you will be preventing that energy that used to keep the block warm from leaving the house. If you're up for saving interior space too, I'd go the route of insulating the outside.
Kyle is probably right about insulating the exterior being better. I would not frame out a regular studwall on the interior, either, since it doesn't really gain you anything. I would try insulating the outside using rigid foam, at least 2" of polyiso. You could put your exterior cladding right over that, or add furring strips, depending on what you want to use.
On the interior, if you use 2x3s on the flat, you'll create vertical channels you can use for wiring in less than half the space of a full 2x4 studwall. You can use 4" square 1.5" deep boxes (which are standard), mounted through the back to the concrete with tapcons. You can use mud rings to mount devices in those boxes flush with your finished drywall. This is the standard way of wiring in commercial buildings, so any electrician will be familiar with the pieces needed to do it, and everything needed is readily available too.
Bill
AJL,
I would have to agree with both Kyle and Bill that exterior insulation is the way to go, if possible. If I ever get the chance to build a house, which I'd like to do, I would build a CMU house with exterior mineral wool insulation. To accomplish this I would use Z girts (or metal studs) to stand off the wall for the insulation and connect to those horizontal girders/beams (2x4s) with vertical metal siding over those. The girders/beams could also be installed vertically and the siding installed horizontally.
I've heard of condensation issues when insulating on the interior of CMU exterior walls. Perhaps some of the architects here can help with how to avoid that issue better than I. I would think a vapor barrier/retarder of some sort on the interior drywall surface and sealing all penetrations of the drywall would help mitigate that issue.
Best of luck.
Josh
Great advice all. Very much appreciated. Exterior insulation changes the game considerably (making transitions to windows, etc.). Back to the interior solution: The exterior of the block is painted. Which I trust is preventing water penetration. I completely understand the concern with water and the block freezing (which I think makes this a bit different than basement wall insulation). I also understand the concern loosing interior space, however I am tearing into the walls anyway and this prevents tearing up the inside and then still having to reside the exterior. What are the concerns with spraying closed cell on the interior and then either fiberglass bats or maybe better open cell foam in the interior 2x4 cavity. I get the inside surface of the spray foam could be a condensation surface at certain conditions, but the idea would be to control interior air via vapor barrier (maybe not ideal). Expense is the downside of the closed cell than open cell foam approach, but this would seem to be a pretty solid solution unless I'm missing something.
Appreciate everyone's help here!!
Rigid foam will likely be cheaper than spray foam, and it will give you a nice, flat surface too. I would not use batts here at all, I'd put all the R value in rigid foam against the block. Put some 2x3s on the flat against the rigid foam to allow for electrical, and to make drywalling easier. There is no need to frame out regular 2x4 studwalls here, they don't gain you anything over the simpler rigid foam + furring strip approach.
Bill
I should mention, the block is a "raised" face (decorative) block and there are nice cast concrete lentil and headers above windows. I actually tore down a garage to salvage the same style block when I put on an addition to add bathrooms. The addition is 2x6 construction and I cut the block in half lengthwise to set on a brick ledge to match the existing. So I have some interest in maintaining the current exterior if there is a workable solution!
Insulating masonry from the interior is always problematic. You can read more about it here:
https://www.buildingscience.com/documents/digests/bsd-114-interior-insulation-retrofits-of-load-bearing-masonry-walls-in-cold-climates
Your safest option is a thin layer of closed cell spray foam (~2") plus batts.
Great article. Appreciated!
Maybe I'm going overboard, but I would love to evaluate a couple of concepts via hygrothermal analysis. Can you connect me with any consultants that could run a couple scenarios?
It seems there are really four options:
1) Closed cell spray foam is your recommendation as well as the consensus. The key is getting to a thickness that controls the dew point in my region. I am still researching that. Although I have gone over every square inch of the exterior repairing cracks and it is now coated in a quality masonry paint, my concern is outside wetting and then freezing. The spray foam has very low water vapor permeability (more or less a plastic sheet), so there will be essentially no drying to the inside. I just don't know how big of a concern this is. In my mind, rigid board installed on the interior masonry is the same solution with the same concern as the extruded board basically the same vapor perm.
2) The article mentions cases where an air gap is maintained between the masonry and insulation. There are two methods that could be applied (this one and (3) below). In this method the goal is low vapor perm from interior to the air space and masonry. I could space rigid insulation off the masonry using the existing firing adhered to the block wall (which is in surprisingly good shape) and go from there. Rigid extruded polystyrene is less than 1 perm for 2" of thickness (if my data is correct). The goal would be to keep interior moisture out of the air space. If the block is wet, would it dry to the inside (basically the air gap). This seems to require air flow in the gap to reduce the humidity. The article did talk about forced low humidity airflow. This isn't in the scope, so maybe this concept falls apart. I could at least drill holes between floors periodically to enable some chimney effect in this air space.
(3) What about spacing the insulation from the masonry, controlling vapor from the living space and allowing permeability to the inside living space via one way membrane? I could retain the firing and lath to space the insulation from the wall and use insulation with higher permeability (open cell, even cellulose of fiberglass). I would think the lath is close enough together to keep insulation out of the air space. I would then use a one way membrane (MemBrain) allowing one way diffusion to the drywall and interior. The MemBrain would prevent (slow) interior moisture in the winter from migrating into the wall but allow moisture from the masonry to diffuse through the insulation, membrane and drywall into the home.
(4) Of course the last option is to control moisture and not worry about insulation. I have injected the cores of the block with foam. Not sure what that is getting me, but not a lot. But if the freeze and thaw is a concern, it might be better to not install any interior insulation.
I can certainly follow-up with sketches if this is unclear.
I would love to evaluate these options via hygrothermal analysis and pick the best one for zone 5. Maybe these are pretty straight forward options and the answer is clear to someone skilled in the art like yourself. Maybe similar enough analyses have been run that I could learn from.
Any help is appreciated!
Closed cell SPF is about 2perm/inch. If your block wall is insulated, you are part of the way there for dew point control. What is left over, say 1" to 2" of SPF will still be above 1 perm, so you can get drying to the interior.
I have run into issues with rigid over masonry. Seemed to work for a while but some exterior water issues followed by solar drive that pushed water between the block and the foam. This turned into a moldy mess. Maybe it would have survived if the foam was permeably but still a risky assembly.
The reason that spray foam works is that it is fully adhered so there is no air at all, even if there is high humidity, mold won't be able to grow.
The only way I could see an air gap working is if it is vented outside, similar to a masonry veneer wall. In your case, this would defeat the insulation in the block wall, so not the best option.
AKOS,
I can't tell you how much I appreciate your expert advice. Many thanks!
Allow me to close one point. This is an above grade exterior in zone 5 (not a basement). In addition to mold, freeze / thaw damage is a concern.
Am I correct that your opinion is:
(1) the masonry wetting from the exterior will be both controlled enough via a well maintained, painted exterior (2) The vapor retarder under the drywall (I intend to use Membrain) and the spray foam itself will minimize or eliminate interior moisture from coming in contact with the block and (3) Any moisture coming in from the exterior [item (1)] above will dry through the face of the block as well as through the spray foam to the interior in a reasonable time frame.
Please correct me if I am wrong.
I am attaching a sketch of the proposed installation. My preference is concept 01 because I just don't believe the second spray is worth the $.
If you have time to give it a look I would appreciate it!!
Lastly, I'm sure it would have come up by now, but I am assuming there isn't a "tar" or adhesive of some sort that you "paint" or spray on 4 x 8 extruded polystyrene sheet to bond the sheet and act like spray foam.
The only thing that suck more than paying for SPF is ripping out a fully finished wall, paying for the SPF and rebuilding it. This was not a basement but above grade walls. I would be hesitant to go with any above grade masonry assembly with interior rigid. The above grade masonry gets much colder in the winter time than a foundation wall and much more risk of condensation. Once the weather warms and the sun hits the wall all that moisture can be pushed into the gap between the rigid and the wall creating a mess.
If you are not going with the SPF route, assuming the existing insulated block wall is decent R value, I think the of interior fluid applied WRB and batts shown in Figure 11 in the link is the better option.
That type of assembly (minus the interior WRB) is pretty common here in commercial construction (zone 5) and it seems to mostly hold up well. Once you add in some exterior insulation by insulating the cavity of the blocks, you should have a reasonably safe assembly.
I like that Bill. Any thoughts on attaching the rigid foam to the block? Any concern with the small air gap between the rigid foam and interior surface of the concrete block? I think I need to make a sketch or two and make sure I understand your design. I will works something up later today and attach for alignment.
If we neglect the cost and internal space loss momentarily, is there a concern with the closed cell spay then open cell foam fill method.
Thank you.
If you can't get the rigid foam to sit flat against the block, which depends on how much of a decorative face the block has, then spray foam might be better since it can form a fully adhered insulating layer. You do NOT want a gap. With spray foam, I would frame out a wall an inch or so away from the block, then spray foam so that that "inch or so" gap gets filled too.
I don't see a problem with closed cell for a few inches and then open cell for the rest. You will need all of your electrical installed before insulating with that option though, to avoid having to cut all the electrical into the foam. The important part with that mix is to have enough closed cell spray foam for dew point control, which can be determined from the usual R value tables. More closed cell as a percentage of the total is safer.
Bill
Many thanks Bill. Your input is Appreciated!
I'm not sure if you can see my reply (#12) to Akos Toth's advice from 12/8 (#7).
I would love your thoughts.
Also, I have done some looking for R tables. Any help to make sure I am finding the right information for zone 5 is appreciated.
I got to ask to my ear this well-meaning project makes no economic sense.
Both the interior and exterior options are so difficult and costly the economic say pay the bigger heating bill until you sell it is soon is likely to be the low cost option.
If the place has some sentimental value this work seems likely to destroy much of that.
What do we think the current walls R value is today? Foam filled block maybe R10 if by some miracle there are no voids.
Walta
There appears to be products that will finish smooth and be applied directly to foam insulation. No need to frame out. Use wiring techniques employed for SIP buildings.
Be sure to also read Martin’s article on insulating concrete walls with embedded floor joists, which as you know, poses the threat of thermal bridging and condensation. In the article, Martin notes: “Building scientists have therefore concluded that when it comes to embedded joists, monitoring field conditions results in more useful information than hygrothermal modeling.” He also makes clear that interior insulation makes the situation worse. Read to see his explanation of why it’s always safer to insulate this type of wall on the exterior rather than the interior. (Exterior foundation insulation keeps the foundation walls warmer and dryer than interior insulation, and that’s good for embedded joists.)
Thank you Kiley. I will take a read. I came across an article that recommended "thermally conductive metal "inserts" (assuming aluminum) wedged into the gap between wood and masonry extending into the warmer interior to transfer heat. doesn't sound too challenging if there is room.