Insulating and Air Sealing a Shed-Style Workshop

Hey guys. Climate Zone 4, central KY. I plan to build a 10×12 “shed” to do climate controlled hand tool woodworking in. It will be drywalled, have electric, etc, so I want to make sure I air seal and insulate it appropriately. Not subject to permit or inspection but I still want to do it right. It’s pretty small, so I don’t think I need to go super high R-value or anything. My main concern is the details and making sure I don’t get in a situation where I am having condensation inside the floor, walls, or roof assembly.
The shed will be built on concrete piers, with pressure treated 2×12’s for the floor joists. Here’s my plan. If someone can alert me to any blunders, that would be helpful.
Floor
2×12 joists, pressure treated blocking and 3/4″pressure treated plywood to fit the joist cavities, thus making 6-1/4″ joist bays instead of 2×12. Spray foam from the inside along the edges of each joist bay to air seal then completely fill each bay with R-19 fiberglass insulation. Subfloor over this.
Use caulk to air seal stud walls to sub floor.
Walls
Use 2×4 stud walls and R13 fiberglass insulation in the bays. R5 foam board on the exterior taped to air seal the assembly. Additional foam board cut to fit in between rafter tails on shed roof, with spray foam filling the gaps and airsealing wall assembly to roof assembly. The rafter tails will have an eave built around them that is essentially just empty air.
Roof
Unvented shed roof (no peak, just a single slope). R30 fiberglass in the 2×10 cavities that completely fills the bays, with the exception of space made for electrical boxes for lights. R20 foam board sandwich on the roof taped to air seal the roof assembly.
Does anyone see blunders here, or have suggestions for how to accomplish similar results more cost effectively? Due to the type of foundation I have chosen, and the weight of the floor assembly, it won’t be very feasible to insulate the floor with rigid foam from underneath, though that would be my preference.
GBA Detail Library
A collection of one thousand construction details organized by climate and house part
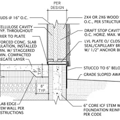
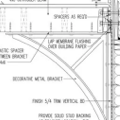
Replies
For such a small building, I’m assuming your concrete piers will only be around the perimeter? If that’s the case, then you should be able to use rigid foam on the bottom of the joists, just cut it to fit around the piers, maybe with some extra treated blocking on top of the pier to give you some space for the rigid foam. I’d fill the joist cavities with blown cellulose if you put taped rigid foam underneath, and I’d use a bead of polyurethane sealant around the perimeter to seal the rigid foam to the underside of the rim joist edges.
I don’t see anything wrong with your wall assembly, that part seems pretty standard.
You could make that a vented roof, just use soffit vents “sideways” under the upper peak, assuming you have a lean-to style of roof like I’m thinking you do. You don’t have to use a ridge vent, all you need is “intake vents low and exhaust vents high”. If you’re able to vent the roof that way, then all your ceiling details become less critical and you could use blown cellulose again. If you don’t want to use blown cellulose year (shake and rake would be another option, BTW), then I’d probably just use unfaced batts.
Bill
I think the floor will be <1’ off the ground and too heavy to flip over. That’s why I was thinking I couldn’t do rigid foam on the underside. I agree that would be better, but will I have a moisture problem with my initial plan?
Cutting plywood to fit between floor joist bays will be a pain and very difficult to airseal well. Better to run the sheets continuous on the bottom of joists and seal with sheathing tape. For that you will want at least 18" clear from grade for access. Loose fill cellulose would be cheaper and more resistant to convective heat loss in the floor.
For 10x12 floor, you won't need 2x12 joists, there is not much benefit to over-sizing them. Depending on which direction your joists run and where the posts/beams are, 2x6 is plenty.
Even with 2x12 and plywood sheathing, you can easily build a floor that big upside down and flip it over. I would do as Bill recommended with the foam under the floor joists covered by plywood and fill the joist bays with cellulose. Make sure to protect the edge of the foam either with 2x lumber cut to size or by dropping the wall sheathing all the way down.
You could build the floor on elevated supports (rigid supports properly braced) to give you room to work underneath. Once you’re done, lower the floor assembly with jacks into its final brackets on the piers. You need to do this correctly to be safe, but it’s not terribly difficult if you only need an extra foot or two of access.
Bill
When it comes to air sealing, always test (vs assume).
WRT cost effectiveness, do consider the amount of time that the space is heated/cooled.
Any other thoughts on if my original plan will cause moisture problems? I ha e some leftover 16” pieces of rigid foam and it will be a lot easier than insulating the joists. So far no k e has said my original plan won’t work, only that to insulate underneath would be better. I just want to make sure I’m not going to be inviting mold and rot doing it this way even if it’s not quite as energy efficient.
Thanks in advance!
Conceptually, your assemblies work. If you're concerned about moisture management, focus on controlling bulk water from top to bottom. Then, to a lesser degree, air leakage, vapor control and thermal control. No blunders in your approach, but the devil is in the details. Include a rainscreen. Flash the window and door properly. etc. etc.