Insulating already framed basement walls

Hey all, Mike here. Portion of my basement was already finished when I moved in. I just recently refinished the remainder of the basement using XPS against the walls, w/ unfaced batts between the studs.
On the finished side. I opened up a piece of the wall and noticed that the previous owner simply painted the walls with Drylok, and placed faced batts between the studs. I’m aware that this can lead to mold issues. My question is this. Do I remove all of the trim, sheetrock, insulation etc.? This would be a major hassle. Or do I wait until a problem arises? Everything so far that I can see doesn’t seem to be a problem.
If your advice is to remove everything and redo, what is the best method of insulating between the framing and concrete? I can’t get XPS in there because of the framing. I don’t want to use spray insulation as it could get messy and I already have laminate floors down.
Advice and guidance would be greatly appreciated.
-Mike.
GBA Detail Library
A collection of one thousand construction details organized by climate and house part
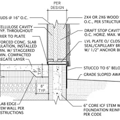
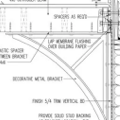
Replies
Mike,
This is a judgment call. If you are a perfectionist, and you can afford the work, rip everything out and do it right. If you're like most people, and you have a limited budget, leave well enough alone until there is evidence of a problem.
Run a dehumidifier in the basement. Keep the indoor humidity below 40%-50% or so depending on climate zone. With lower indoor humidity, you have less potential for condensation against the cool foundation walls. Make sure the dehumidifier drains automatically to a sump pit or condensate pump so you don't have to empty the bucket.
Martin,
I decided to cut 4' of the sheet rock and remove to see what was lurking behind. I did find one small area of mold, and some discolored (dark red) wet spots on some of the fiberglass insulation; which I'm guessing is indicative of condensation.
I was able to slide 1" XPS behind the studs and reinstall the unfaced without removing the studs. However, on one of my walls, the interior framed wall is 6" from the concrete foundation. Not really sure why, but what would you recommend here? I was thinking of gluing 2 2" XPS boards together and then using good stuff on the remaining 2" gap between the XPS and the 2x4.
Thoughts on this? I'd greatly appreciate your input.
>"I was thinking of gluing 2 2" XPS boards together and then using good stuff on the remaining 2" gap between the XPS and the 2x4.
Thoughts on this? I'd greatly appreciate your input."
Sure.
First, stop using XPS. It's the least-green insulation material in common use in North America due to it's HFC blowing agents, which are powerful greenhouse gases. As the HFCs slowly diffuse out over a few decades it's performance drops- it's warranteed to R4.5/inch (that 2" XPS is really R9, not R10, per the manufacturers' warranty) and even that is optimistic for performance 50 years from now.
Greener and higher performance would be polyisocyanurate.
Polyiso is blown with drastically lower impact pentane, and is slightly higher R/inch than XPS. Foil faced polyiso is dead-easy to airseal with foil tapes. The only caveat about using it in basements is to keep the cut edge off the slab, since it can slowly wick moisture from a damp slab and take forever to dry. Any amount of air gap is a sufficient capillary break, or you could install an inch of XPS from your left over scraps between the slab and polyiso. At 3" polyiso would be labeled R18-R19, but a foil facer facing an air gap gives it another R1 of performance. At R18 it's already above the IRC code minimum for any climate but if you want to install more, have at it.
As long as there is a firestop at the top of the cavity it's fine to leave a gap between the studwall and wall polyiso, leaving the stud bays empty.
There are several square miles of used roofing polyiso at materials reclaimation vendors at any moment in time, which would be a low cost, greener way to get there. Fiber face polyiso is denser and slightly lower R than the foil faced goods used for insulating sheathing. New it's labeled R5.5-R5.7 per inch, so even 3" would till be R17-ish, and beat code minimum anywhere in the US. Housewrap tapes work fine for air sealing most fiberglass or paper faced roofing polyiso.
If you're not sure if there's a foam reclaimer in your area, try running this search on your local craigslist- many advertise there:
https://cleveland.craigslist.org/search/sss?query=rigid+insulation
https://houston.craigslist.org/search/sss?query=rigid+insulation
https://seattle.craigslist.org/search/sss?query=rigid+insulation
https://atlanta.craigslist.org/search/sss?query=rigid+insulation