Insulating an old house with lath and plaster walls from the outside

I recently uncovered some original T&G siding on the front porch of our mid-1800s Greek revival farmhouse in upstate NY, climate zone 5 I believe. Not long after, I discovered that there was no insulation in these two walls. Being that the old boards were covered in deteriorating lead paint, I decided to just pull them off to insulate from the outside and then reside. This is the only part of the house that had this type of siding. The rest of the house, I believe, has horizontal board sheathing, old clapboards, cedar shingles, 1″ foil faced polyiso (un-taped seams), and finally vinyl siding. Also, the two walls that were stripped have different stud depths; one at about 3-1/2″-4″, the other a bit over 6″. The interior wall covering in this erea is lath and plaster.
We would like to reside the whole house eventually and want to keep things consistent as far as the insulation goes. In some rooms we’d like to keep the old lath and plaster walls. Other rooms will need to be drywalled. I was planning to use either mineral wool batts or cellulose for the cavity insulation, followed by plywood sheathing, an appropriate WRB, exterior rigid insulation, a rainscreen gap and then siding. I’d like to use mineral wool for the exterior insulation as well and avoid foams as much as possible. As for the siding, we’re leaning towards cedar shingles for the majority and T&G boards for the front porch area again. To attach the new porch roof, I’d like to go with Maine deck brackets to allow for uninterrupted exterior insulation.
What I’m afraid of, thanks to various websites and articles online, are the horror stories of moisture problems after insulating old houses like these. I realize that it’s imperative to have an air tight assembly, and thought it would be beneficial if the wall could dry to both the interior and exterior.
Unfortunately there is vermiculite in the “attic” of this story-and-a-half house, which I have yet to send out for testing to see if it is Zonoite brand, so there isn’t much I can do to improve the roof insulation at this time. I know the attic space is poorly insulated and the estimates we’ve gotten for abatement are incredibly expensive. However, any suggestions as to the wall stackup for this type of home would be appreciated.
GBA Detail Library
A collection of one thousand construction details organized by climate and house part
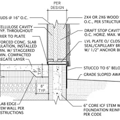
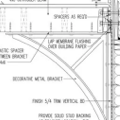
Replies
I have a similar project on my own house, except I have all drywall. I should think air sealing the plaster walls you have will follow the same general guidelines as for drywall, but will be a little more labor intensive since you won’t have nice smooth surfaces to work with due to the lath.
My plan is to replace the R11 fiberglass in my walls with R15 mineral wool, mostly for the sound deadening properties but also because I’ve found mouse damage to some of my old fiberglass insulation. I’m planning on plywood sheathing, 3” of rigid foam in two layers, WRB, rain screen gap, then fiber cement siding. The wall will dry to the interior and won’t use a vapor barrier on the interior.
Be careful of old utilities, especially knob and tube wiring, that may be in those old walls.
Bill
The most critical thing to get right here are the window & door flashing details. Bulk water incursions getting soaked into the insulation is the biggest cause of moisture disasters in these antiques.
In zone 5 as long as the new siding is back ventilated (building in a rainscreen gap, or vinyl siding) the sheathing will stay dry, unless a low-vapor permeance layer (such as foil faced foam) is inserted between the sheathing and siding. If that low-perm layer has enough R-value to keep the average wintertime temperature at the sheathing above 38F or it'll still stay dry. For a 3.5" deep stud bay in zone 5 the exterior foam needs to be R5 or higher- an inch of foil faced polyiso is enough. For a full 6" deep stud bay it would need to be at least R8.2, say, 1.5" of polyiso or 2" of EPS.
Odd stud spacing & depths are often not suitable for insulating with batts. The insulation has to fit pretty snugly on all 6 sizes of the cavity to be effective. Blown cellulose is pretty cheap & effective, and protective of the structural wood by sharing & redistributing the moisture burden. Just be sure to not soak it with improperly lapped window flashing- it can take up a LOT of water before you notice a leak.
But if using rigid rock wool on the exterior the vapor permeance is high enough that it's R-value doesn't really matter- the sheathing can still dry.
Air sealing OSB or plywood sheathing is pretty straightforward, and #15 felt is just fine as a WRB, antique plank, not so much. Use a broadsheet vapor permeable WRB, detailed as an air barrier over any plank sheathing.
Thanks for the quick responses guys. I really appreciate it. I am thinking that blowing in cellulose is my best option at this point. The stud spacing and the odd nailers for the lath attachment are not conducive for batting. I figure I'll attach the new 1/2" plywood, drill 1" holes for the blower nozzle and fill each space.
Would I be better off ordering some insulweb netting and try getting a denser fill in the wall before sheathing?
From the inside out:
plaster and lath, cellulose cavity insulation, 1/2" plywood sheathing with taped seams, WRB (tyvek, #15 felt, or other), 1-1/2" to 2" of mineral wool board insulation, rainscreen gap, wood siding. Am I missing anything?
Thanks again!
It's pretty easy to drill 2.5" holes in OSB/CDX sheathing with a hole saw for dense packing the cavities (recommended), which is quicker and less trouble than blowing in mesh. Save the hole saw plugs for an easy air-tight patch/repair using polyurethane caulk & housewrap tape after the insulation is installed. In your climate/location 3.2lbs per cubic foot is the minimum, 3.5 lbs density is the target.
Be sure to assess the condition of the lath nails before dense packing. If they're too far gone it may not be advisable to dense pack. If marginal but still hanging in there, a hefty person holding a sheet of 3/4" plywood against the plaster during installing can keep it from cracking or blowing out.
More questions come to mind. Dana, can you clarify your comment on the 3.2 lb. minimum in my area? If I don't get it that dense, will I have problems resulting from it? I have an older blower machine that is probably comparable in power to what the home centers loan out.
Also, can anyone give suggestions on how best to air seal the sheathing, particularly around the perimeter, to old hand hewn timbers? Are there gaskets I could use or spray foam adhesives that would be appropriate? Any specific articles I should search for on this topic?
When you’re drilling those holes, get a hole saw with a quick release. I use a set from Bosch. It’s sooo much easier to just pop out the holesaw from the arbor, then stab the center bit through the oversized hole in the back of the holesaw to pop the wood piece out. Lots easier this way than stuffing a screwdriver in the side of a welded holesaw if you have a lot of holes to do, and the plugs tend to come out with less damage.
For airsealing those rough timbers, you might try Dow’s great stuff drywall gasket. It’s a foam urethane gasket in a spray can. It’s normally for sealing drywall to studs, but I think it might do a good job in your application too. I saw this stuff at a builders show but haven’t tried it myself yet.
Bill
Jodi,
No one has mentioned a couple of issues that are potentially worrisome:
1. If you are removing old siding that contains lead paint, be very cautious. You need to understand lead safe practices. For more information, see "Managing Lead Paint Hazards."
2. Experts advise that all vermiculite insulation should be assumed to contain asbestos. Testing is not recommended. For more information, see "Fixing Attics With Vermiculite Insulation."