Condensation on Tongue-and-Groove Ceiling

I’ve been searching the discussions on this great site, but haven’t yet found an answer to my specific challenge: Ending condensation dripping through my tongue and groove cathedral ceiling when replacing my very low volume roof on my log home. The existing ceiling/roof assembly is 2″ tongue and groove supported on exposed interior log purlins, with what the original drawings say is “black plastic moisture barrier” behind it, followed by 2″ wood firring strips with an unknown insulation in between, and then corrugated metal on top.
We live at 800ft outside of Portland, OR (climate zone 4C), and when the temp warms from below freezing outside our ceiling begins dripping from the lower 3rd of the roof slope. We’ve had multiple contractors out to bid a full tear-off down to the T&G, but everyone has a different idea of what to do after that. The two contractors we like best are both suggesting covering 100% of the exterior face of the T&G with ice and water shield, but then one is saying 2″ polyiso and the other 3″ fiberglass laminate to PVC (as is typical in metal outbuildings), with the PVC against the ice and water. Both intend to fasten 12″ 24ga steel standing seam roof panels directly on top of the insulation and screw through it to the T&G. So a very thin hot roof assembly.
Avoiding condensation dripping into our house is priority 1. I realize that this roofing approach will have a very low R value, which is a disappointment, but we don’t have the budget to build a larger roof plenum on top of our T&G to insulate to anywhere near new building codes. Our home is 100% electric and we intend to mount solar panels to the roof, so at least there’s that!
Assuming both approaches are sound (enough), which is better? The polyiso will maintain it’s thickness and R value, but leave slight air volumes under the metal roof panels that may become condensation sites, as well as the uncertainty of the foam’s performance over time and the potential for air gaps between foam panels. The fiberglass approach will have a minimal R value (R2? R4?) once it’s compressed by the roof panels, but would effectively conform 100% to the back side of each panel, reducing the air volume where moisture could live.
A possible third option could be 2″ polyiso with 2″ (or 1″?) laminated fiberglass, which might combine the best of both systems? But if my stack up is T&G, ice and water, polyiso, pvc-backed fiberglass (with the pvc in contact with the polyiso), and then metal roof panels, will I trap moisture between the ice and water and pvc, or will I have excluded airflow enough that it’s a non-issue?
Thanks in advance for any advice you could offer! Got to select my roofer and approach before 6 months of NW drizzle!
GBA Detail Library
A collection of one thousand construction details organized by climate and house part
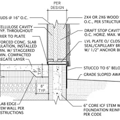
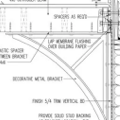
Replies
New developments! One of the roofers pulled up a section of the existing metal roof, and we found that on top of the tongue and groove there are 2x4 battens running horizontally, with 4x8 foil faced polyiso fully filling the gaps in between. The foam in the small section we pulled up looked okay. The roofer now wants to remove the existing metal, pave over the entire foam and batten assembly with ice and water shield, and lay down reflectix and then the new standing seam metal panels directly on top, fastened to the battens.
The issue I see is that the current roof assembly is T&G, then "black plastic moisture barrier" (haven't visually confirmed this, but it's in the drawings), then the foam/batten layer. If we go with his plan, the roof will be T&G / black plastic / polyiso / ice and water shield / reflectix / metal panels. Since the black plastic is clearly compromised, it seems like the moist air from inside the house is going to go up into the air spaces between the black plastic and the ice and water shield and get stuck there, no?
Seems like there's a risk of insulation/batten rot, as well as a chance that condensation will form on the sticky side of the ice and water shield where there are gaps between foam sheets or battens, if we take this approach, but I'm not sure.
It's a ton more work to pull everything off to the T&G, and there's the risk of breaking up the polyiso, which I'd like to re-use, but it seems like putting the ice and water shield directly onto the back of T&G would be the better build.
Thoughts? Could we get away with following the roofers suggestion to just hide everything with ice and water? Would certainly save a good chunk of time and money.
Hoping to hear from someone!
Anybody?
Quite a bit going on here, so a bit risky to comment with any confidence.
That said...
>"when the temp warms from below freezing outside our ceiling begins dripping from the lower 3rd of the roof slope."
This is confusing. Condensation is caused by vapor loosing energy to cool surfaces and thus condensing to a liquid state. Why do you think you are getting condensation when those surfaces warm up rather than cool down? Is your interior humidity increasing significantly during those warm ups? Is there any snow on the roof during these warm ups?
You mention not being able to use thicker insulation for monetary concerns, but now you're talking about the possibility of ripping apart multiple roof layers for some serious surgery. I would imagine the cost of labor involved in such an endeavor would dwarf the cost of extra thickness of insulation installed above.
I know nothing about the fiberglass/pvc product you are referring to, but it seems like what you need is adequate R value ABOVE your interior vapor barriers to prevent condensation. It sounds like foam (of adequate thickness) would be better in this regard.
Are you familiar with the ratio R values for roofs in your climate? You will want a certain percentage of R value above any vapor barrier.
https://www.greenbuildingadvisor.com/article/combining-exterior-rigid-foam-with-fluffy-insulation
Maine,
Q. "Why do you think you are getting condensation when those surfaces warm up rather than cool down?"
A. The phenomenon is common. The moisture (water vapor in escaping indoor air) accumulates as ice on cold surfaces in the roof assembly. Accumulation happens during cold weather. When the weather warms up, the ice melts and the ceiling drips.
Looking at this again, one thought is that maybe the outside air entering directly beneath the metal roof (is it open to allow air into there?) is condensing at night (night time cooling of roof). It looks like the roof is directly on top of the polyiso with no drainage plane? That would seem a problem. In any case, your new assembly should include a way to drain exterior water (that makes it past the metal or condenses beneath it) towards the eaves instead of slipping through cracks in foam board.
I have a similar dripping experience around skylights set above T&G, with 10" of foam panels above.
My assumption has always been that warm, moist air condenses under cold roof at night and freezes in place. When the morning sun hits the dark asphalt shingles, ice melts and dripping happens. Maybe it is 25F outside air temp, but 45F under roof shingles.
Having just reroofed, I have some other questions about my roof construction, which I will post separately. Obviously, I need better vapor barrier at least around the skylights and perhaps elsewhere ...