Insulation Dilemmas: Polyiso Derating and Cellulose Reuse
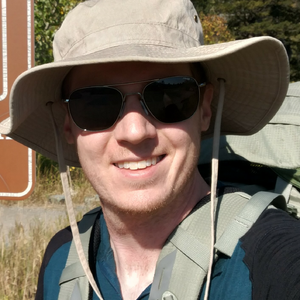
Zone 5, 2nd floor being significantly remodeled, re-roofing also needed. Running myself in circles looking at all the insulation options!
Rafters and joists are all 2×6, front of house is on a 33 degree slope (8:12), back is ~10 degree slope (2:12). This leaves some areas with only 6″ of insulation space. 6-8″ of blown in cellulose in attic space, ventilation provided thru vents at the gable ends (no soffit or ridge vents — and I don’t know how one would even do a ridge vent with a low-slope roof on one side). Also, no ventilation baffles in the areas that are only one rafter thickness between the sheathing and plaster — just filled up with cellulose.
(2nd floor section drawing attached) Original plan was to furr down the ceiling at the back edge and the front sloped ceiling section to provide enough space for R-30 insulation and ventilation baffles. But, R-30 in zone 5 isn’t even “code minimum” anymore, and why do all this work for only mediocre results?
Furring down the ceiling even further to provide more insulation depth starts really cutting down on usable space. I’m not a fan of ccSPF for many reasons, so that’s out. Second plan: Strip roof to sheathing and re-roof with new air barrier, 6″ of polyiso, second layer of sheathing, and ice&water shield. Provide additional 6-8″ of mineral wool batts or something between rafters. Derating the polyiso to R-5/in for cold weather performance and aging still gets this assembly close to R-50 (R-30 exterior, R-20 interior, meets the zone 5 requirement for ratios of interior/exterior insulation).
Second guessing the second plan: Upon additional research here and elsewhere, the R-5 polyiso derating may not be enough — I’ve seen as low as R-4 in cold temperatures, and one comment (that I can’t find again) suggested as low as R-2.8! That leaves me with roof insulation that performs worse and risks interior condensation more just when the weather gets coldest, not great. Foam is already somewhat regrettable from an environmental standpoint, but I can’t afford wood fiber and my structure can’t afford the weight of mineral wool.
So, what’s an “appropriate” derating for exterior polyiso in zone 5? Do I stick with the polyiso plan and just use 8″ instead of 6″? Or are there other options I’m missing? (Field fab a bunch of larsen trusses and dense-pack cellulose?)
Also, note the presence of 6-8″ of loose blown cellulose already present. A fair bit of the plaster is coming down for other work, and I know with the split exterior / interior insulation scheme, the interior fluffy insulation needs to be in contact with the roof sheathing — not sitting on ceiling. However, it seems a shame to dumpster a bunch of cellulose and then buy new batt insulation. Is it reasonable to slurp out the cellulose with an insulation vacuum, save it, and then later re-use it dense-packed behind Intello Plus or something?
Thanks!
GBA Detail Library
A collection of one thousand construction details organized by climate and house part
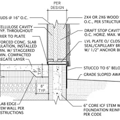
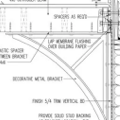
Replies
Before you contemplate putting 6-8" of exterior foam on a residential roof, I would make sure you have in mind the contractor who will be executing it and get comfortable with how much they will charge you to do it. It's incredibly uncommon and the only house I've ever seen foam on the roof of in NJ is my own (and that was just over an existing dormer where it was the only way to get any decent level of insulation). 6-8" of foam is A LOT and it will be a pain to install.
Point taken on complexity -- but the contractor who will be executing it is me and whatever
poor suckersgood friends I can rope into helping. That said I am a bit worried about the installation pain -- hitting rafters with screws thru 8" of foam doesn't sound easy, and seems to be glossed over in a lot of the project writeups I've seen on this kind of installation. Also, my initial cost estimated neglected the (actually pretty substantial) costs of all those extra-long fasteners.Thank you for the article, you really did a lot of work! Unfortunately, I still did not find a way to reduce and prevent the decrease in the characteristics of Polyiso. I've been thinking about how to start processing pulp for a long time and decided to create my own mechanism for this, how do you like it?
https://www.ramotion.com/
It's complicated. Joe Lstiburek has an article on the subject:
https://www.buildingscience.com/documents/information-sheets/info-502-temperature-dependent-r-value
That's one of the articles I've read -- and unfortunately it doesn't fully clarify the situation. For example, they test 2" of polyiso at various *mean* temperatures, with a fixed 50C temperature differential, and also at various *outdoor* temperatures with fixed indoor temperatures, but point out that the behavior of the insulation is nonlinear so it's hard to extrapolate results to other conditions.
In one of the BSC tests, for example, with an outdoor temperature of 0F and indoor of 72F, apparent R-value ranges from 5-6 (on new, not aged & degraded samples). Presumably, the layers of insulation closest to the interior side are performing closer to their optimum ratings, while at some point that falls below R-5 such that the average works out to R-5. In Figure 1 of that article, at a 25F mean and 50F delta, R per inch ranges from 4 to 5.5. In the "exterior continuous insulation" case that I'm proposing (and that indeed seems like a common suggestion), *all* of the polyiso insulation will be colder than normal-indoor temperatures. If I have 50% of my R-value as exterior foam and 50% as interior fluffy, on a hypothetical 0F outdoor / 72F indoor day (same as the BSC "in service" test), the mean temperature of the polyiso would actually be 18F with a cold side at 0F and warm side at 36F -- which means that the entire thickness of the polyiso would already be experiencing some degree of derating, making it less than 50% of the R-value of the assembly, making it even colder & worse performing.
Worst-case (and to simplify the math), let's say there's a "cliff" in the thermal conductivity vs. temperature graph -- maybe polyiso is only good for R-3/in at temperatures below 30F. Performing testing with an indoor temperature of 70 and outdoor of 0, at equilibrium you end up with 40F of your temperature drop across the R-6 portion and 30F across the R-3 portion, but 60% of your insulation thickness is behaving as R-3 and your assembly R-value is R-4.2/in. If you then add some interior fluffy insulation that's not nonlinear -- say 6" at R-4/in interior and 6" polyiso exterior -- (here I did a bunch of math only to find that I inadvertently made it really easy on myself :P ) *all* the polyiso is below 30F and just behaving like R-3, so your polyiso is only good for R-3/in and your stack is only good for R-42 instead of your intended design of R-60 (with R-6/in polyiso) or R-54 (derating polyiso to the BSC recommended R-5/in)
Importantly, the above calculation is only an example and assumes a stepwise k vs. T relationship. In reality, I assume the drop in thermal performance is a nonlinear curve, and the above type of calculations become less algebra and more integrals. However, the point stands -- the only data I've found so far provide R-per-inch information at temperature spreads that do not reflect reality in an exterior-foam, interior-fluffy insulation scenario. Additionally, there are possible k vs. T curves that would be both entirely consistent with BSC's recommended derating to R-5/in in cold temperatures, but would provide significantly worse performance in real life when paired with another layer of insulation. The BSC article has a footnote which states that "Further BSC testing seeks to study this phenomenon further and establish a conductivity vs temperature curve for various polyisocyanurate insulation products.", but I haven't found that research yet.
So, I guess to summarize and clarify my question:
-Is there any more recent research on the k vs. T curve of polyiso and the implications that has on the use of exterior polyiso coupled with interior fluffy insulation?
-In my zone 5 climate, how do I effectively deal with these effects while avoiding more environmentally un-sound products, but without quadrupling the budget?
Thanks!
>"Upon additional research here and elsewhere, the R-5 polyiso derating may not be enough — I’ve seen as low as R-4 in cold temperatures, and one comment (that I can’t find again) suggested as low as R-2.8! That leaves me with roof insulation that performs worse and risks interior condensation more just when the weather gets coldest, not great. "
From a moisture accumulation point of view average wintertime performance is far more important to consider than the coldest-hours performance. Even latex paint on gypsum board is usually in the 3-5 perm range- you don't get "interior condensation" that keeps on building. When the sheathing reaches the dew point of the entrained air in any fiber insulation it takes on that moisture into the wood as adsorb (not condensation), which creates a vapor pressure across the paint layer, but the <5 perms is still a pretty good vapor retarder- it doesn't suck moisture out of the room very quickly. When the sheathing temp rises it re-releases the adsorbed moisture into the fiber insulation's entrained air, and at some humidity level the direction of the vapor pressure reverses, pushing some of that moisture back into the room.
To accumulate or remove significant moisture from the assembly takes weeks or even months, not hours or days. So it's the average temperature, not the peak that really matters.
>"Worst-case (and to simplify the math), let's say there's a "cliff" in the thermal conductivity vs. temperature graph -- maybe polyiso is only good for R-3/in at temperatures below 30F. "
Only wet roofing polyiso would perform that badly, just sayin'...
Most IECC climate zone 5 locations have an hourly binned average outdoor temp in the mid-20sF even in January yielding much higher mean temps through foam layer than 30F even during the coldest 5 weeks of winter, higher still over the coldest 12 weeks. Eyeball the average January outdoor temp in say Chicago:
https://weatherspark.com/m/14091/1/Average-Weather-in-January-in-Chicago-Illinois-United-States#Sections-Temperature
Looks to me like about 27-28F for the January average, 32-34F for the 12 week average.
Dana, Thanks for explaining the moisture physics -- that alleviates some of my concerns.
I'm near Cleveland, and the weather averages look very similar to Chicago, so you're right that the average winter temperatures are going to be more like mid-20s to low-30s. But, when we get a week of polar vortex induced 5F I don't want all my insulation to stop working ;)
It sounds like you're not super concerned about the low-temperature performance loss of polyiso, given the average conditions in my climate -- Do you think it's fair to assign it R-5 per inch in my design, as BSC suggests, or derate further to R-4.5 or R-4 or something?
EDIT: Actually, I just came across this old comment of yours https://www.greenbuildingadvisor.com/article/in-cold-climates-r-5-foam-beats-r-6#comment-23504 which suggests that polyiso falls as low as R-2 at low temperatures. The images in the gallery for that article also suggest that polyiso performance starts to degrade significantly below 60F, is worse than any other type of insulation tested below 40F, and is quickly approaching the category of "comparable with wood" rather than "comparable with insulation" at 0F! Admittedly, 0F is rare in zone 5, but 40F certainly isn't, and in the outer foam / inner fluffy scenario, the polyiso might be entirely below 40F continuously for a majority of winter. Granted -- the data in that article are only reported for one unspecified sample of polyiso, and as Bill mentions below that might make things look worse than they are, and manufacturers might have improved their product since 2013 -- but it all gives me pause as to how good of a choice polyiso is in this area. Thoughts?
>"I'm near Cleveland, and the weather averages look very similar to Chicago, so you're right that the average winter temperatures are going to be more like mid-20s to low-30s. But, when we get a week of polar vortex induced 5F I don't want all my insulation to stop working ;)"
It's never going to "stop working", and it's doubtful that any polyiso is going to hit R2/inch at a mean temp of +10F (or whatever it would in your stackup when it's averaging -10F outside). Even the world's crummiest 2lb density roofing polyiso won't go that low unless it has taken on some moisture from a roof leak.
The cheap polyiso DOW is using as the straw-man comparison in this bit of Thermax marketing is only labeled ~R5.2/inch a the FTC mandated test temp of 75F mean temp through the foam:
https://i.imgur.com/a3SvC7H.png
Note that even THAT crummy product levels out above R4/inch at a mean temp of 0F through the foam. DOW Thermax (a ~1lb density foil faced sheathing type) polyiso hits about R7/inch at that temp. The different manufacturers keep tweaking their proprietary blowing agent mixes & processes to improve on this problem, but DOW seems to be claiming to have beaten it completely.
Not that it matters, but Cleveland's winter temperature averages are a degree or three warmer than Chicago's:
https://weatherspark.com/m/18154/1/Average-Weather-in-January-in-Cleveland-Ohio-United-States#Sections-Temperature
>"Do you think it's fair to assign it R-5 per inch in my design, as BSC suggests, or derate further to R-4.5 or R-4 or something?"
It depends on the purpose of derating. From a moisture/dew point control point of view derating 2lb roofing polyiso to R5/inch is about right. That would also be about right from a seasonal average energy use point of view.
From a peak heating load maybe R4/inch is closer, but that hardly matters since it's a reasonably high-R assembly. The difference between R5/inch vs even R2.5/inch for the foam layer is probably going to be comparable to or less than the error on air infiltration estimates. The difference in heat loss between a tiny number and merely half of a tiny number just isn't very big relative to other heat losses in the house.
In NE OH there are several foam reclaimers selling used roofing polyiso & roofing EPS (usually Type-VIII, which is 1.25 lbs per cubic foot nominal density) for cheap. Many of them advertise here at least once per month when sales are slow:
https://cleveland.craigslist.org/search/sss?query=rigid+insulation&purveyor-input=all
Ohio Insulation King in Akron is one of the bigger regional players, and if you have a truck it may be worth the drive, but the shipping wouldn't be very far. Both Repurposed Materials Inc and Nationwide Foam/Insulation Depot are nation wide, but depending on how far it is from your job site to their nearest facility the shipping rates can add up. There are other vendors of used foam in your area- keep looking.
Dana, thanks for the thorough replies! Don't want to beat a dead horse, but I'd like to try to summarize your position:
> Yes, (some) polyiso exhibits substantial performance loss at low temperatures. But, in a zone 5 climate, it just doesn't matter much, especially when averaged over a year. You could use a product like Thermax to avoid some cold temperature derating, but it might be more cost effective to just use a couple more inches of cheap, random manufacturer, used insulation and call it a day.
Does that sound fair?
If you look into the polyiso derating data, you'll find that they often test material from different manufacturers, all of which performs differently. Dana had once pointed out to me here, and I think he's right, that some of the data applies to what he called "world's worst polyiso". It is possible to cherry pick data to make polyiso look bad by choosing to test a sample that is already known to perform worse than others. Not all polyiso is created equal it appears...
Dow Thermax, BTW, specifically address this and claims their R value actually increases in colder temperatures. I suspect they're using a different blowing agent, since condensing blowing agent gasses is what is thought to cause the "reduced R value in cold temperatures" issue with polyiso.
All this discussion is making me think I should build my test rig for this. I did the design work, just have to assemble it and write a bunch of firmware. Then I can test however I want, and however others might ask for, and post data more relevant to the questions asked here in the Q+A forums. Now I just need some time... :-)
Bill
Yeah, I noticed the spread in R-value between manufacturers in those graphs was sometimes greater than the change in R-value for each manufacturer alone -- pretty crazy when they all claim the same performance. Unfortunately, as the researchers (understandably) want to remain impartial and need funding from the manufacturers, they're not willing to "name names", so I can't just go buy "the good stuff" and have to assume that whatever I can buy will be "average" at best. On that note, thanks for naming Thermax, I'll look into that as an option.
Time, of course, is the scarcest resource! Maybe I'll stick thermocouples between every layer of insulation I install, and a heat flux sensor if I'm feeling spendy, and report back in a couple years as to how it performs in practice.
Dow has a small article/brochure about using their Thermax product for large, refrigerated warehouses. That's the document that talks about it's cold weather performance.
Regarding testing, you really need a controlled system to get good measurements. You could monitor it in actual use, but you'd need to watch it over a very long time and normalize all your measurements. This is a lot of work. My test setup design holds the cold side at a constant, programmable temperature, and holds the hot side at another constant, programmable temperature. Since the two "sides" can be independently set in regards to temperature, it's possible to maintain any chosen temperature differential within the limits of the heating and cooling devices. By monitoring the amount of energy going into the heaters on the "hot" side, it's possible to accurately measure the rate of heat flow from the hot side to the cold side through the insulation. Everything else can be calculated from that. I did the design work, and have the parts, but I have to assemble the system (which means some machining), and write some microcontroller firmware to control things (which takes time). I hope to have the time sometime later this year.
Bill
This rabbit hole goes deep! Found the article that I think you're referring to, which looks promising (with the "it's marketing material from the manufacturer" grain of salt...) : https://www.csiresources.org/HigherLogic/System/DownloadDocumentFile.ashx?DocumentFileKey=39ccb701-38b7-d04b-7de6-c50317e463e6 -- though the graph they provide is again based on mean temperature. There's also this article https://www.dupont.com/content/dam/dupont/amer/us/en/performance-building-solutions/public/documents/en/tech-solutions-1270-understanding-cold-storage-roof-insulation-43-d100712enna.pdf which mentions in passing that thermax performs better than other manufacturers, but then goes on to compare other manufacturers to dupont XPS foam and suggest XPS for cold applications.
Interested to see your results whenever you have enough of that elusive "spare time"; hopefully I'll have made a decision and have a roof on my house by then though :D
I'm pretty sure those are the two articles I was referring to. Note that they mention "Roofing ISO", which is lower density than the usual foil-faced polyiso usually discussed on GBA. Note also that some of those graphs are maintaining a -20F indoor temperature, which is pretty cold. You could extrapolate out the same results if you "flip" the graph though, with -20F on the exterior instead, but I think the interior temperature would then be 80F.
They may have also cherry picked crummy performing polyiso to push their Styrofoam product. That's really what I want to investigate with my own test rig. I am interested in the cold weather performance of polyiso for living spaces, houses and the like. DuPont's graphs are for a different application. The BSC graphs are under different conditions, and they don't want to talk about which types of polyiso were better. My interest is to setup normal "house-like" temperatures, so maybe 70F warm side and 0F cold side, to simulate a 70F house with 0F outdoor temperatures.
I will post results when I get around to building the setup, but it's months away so it's going to be a while. I have some other stuff ahead of it, including some commerical product development work.
Bill