Insulation for condensation control in unconditioned space

I want to run this past the brain trust.
I’m working on a house in Rhode Island, CZ4. It’s right next to the ocean so it’s very humid, in the summer we often get fog and sometimes it’s thick enough to set off smoke detectors.
The house has a garage that is in the basement. The garage is not conditioned, above it is a bedroom and there is a wall between the garage and the rest of the basement that is 2×6 with R21 rock wool insulation. In the summer the exterior walls of the garage are in contact with the ground and stay cool, so condensation often forms on them. The exterior walls are concrete block. I’m trying to decide if there is a way to insulate them to keep the condensation from forming.
I’m thinking 1″ or 1-1/2″ of polyiso might be the way to go. The owners want to put up plywood or something similar so they can hang things on the wall. So I’m thinking treated 2×4 or 2×3 uprights laid on the flat side against the wall, polyiso between them and then plywood fastened to the uprights.
Here’s the twist: when the house was built, c. 1976, the well-digger mis-understood the plan and connected the well to the garage rather than the conditioned basement. The water line comes in about 18″ off the floor and runs along the wall to the conditioned part of the basement. Since the garage is unheated it has been known to freeze. I believe that insulating the garage will make it colder in the winter. Frost depth here is 40″, which equates to about R-13, so I feel there should be at least R-13 between the pipe and the interior of the garage, with the wall side of the pipe uninsulated. So I need to figure out how to do a bump-out for the pipe of about 6″.
Thoughts?
Thanks.
DC
GBA Detail Library
A collection of one thousand construction details organized by climate and house part
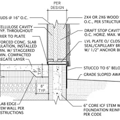
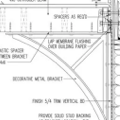
Replies
DC,
No amount of insulate will help with the condensation in that climate. A garage space like that will tend to stay pretty close but lag daily mean temperature so you'll always see condensation in the mornings. About the only way is to heat or dehumidify the garage space. I would leave gaps bellow and above the plywood to allow for some drying capacity.
Your best bet for the water line is thick pipe insulation and rope heat. I've used the thick fiberglass insulation sleeves with the white shell you see in commercial building for this. The proper solution is bring it in bellow frost death but that ship has sailed.
The soil temperature is in the low 50's year-round. Dewpoint probably peaks in the mid-60's. The wall that is attached to the house doesn't have a condensation problem, the basement on the other side is typically around 70F in the summer. The garage door faces due south and has windows so there is solar gain. I'm pretty sure if there is some sort of protection from direct contact with the soil the space will stay above the dewpoint in the summer. Although there's no way to guarantee it, and I can't think of any way to engineer it.
" I can't think of any way to engineer it."
Is it the water pipe that is giving pause? I'm not sure I understand what the specific challenge is with regards to the foam installed on the block wall?
I would be tempted to do continuous and taped foam with the flat framing placed in front like strapping (but connected top and bottom reducing the need for lots of concrete fastening). It seems cobbling the iso between the framing would leave more pathways for air contacting the block and subsequently the condensation.
+1 on the dehumidifier as the best option in this tricky scenario.
I'm in a similar climate and have grappled with the same issues. Yesterday, for example, was sunny and a high of about 78 degrees. Dewpoint was around 66 degrees all day. By 9pm, temp dropped below 66 degrees and all the exterior side of all our windows instantly were soaking wet. Saw it happen in real time while cleaning up the kitchen. Challenging moisture conditions for June, July and August here! But pretty great swimming to be had.
If you get a dehumidifier with decent humidistat controls, you could set it pretty high (maybe even 70%) to use less energy. That would be ok if you don't have much stuff in the garage susceptible to rot.
Ordinarily I would agree with you, but this is uninsulated, unsealed, unconditioned space. There is a 14-foot wide door that is often open. Running a dehumidifier would be like trying to dehumidify the outdoors.
I probably should have posited that I would be satisfied to keep the walls at ambient temperature.
I've been thinking about how to model that. The standard way to think of it is that the interior side of a wall is at ambient, but clearly that's not happening. I think there is so little insulation value that the air film on the wall becomes significant and I'm getting a temperature gradient across it. An interior wall air film has an R-value of 0.68, a CMU is 1.1. If the soil is at 50F and the air is at 75F that would put the surface of the block at 65F.
With R6 of insulation (ie one inch of polyiso) and 3/4" plywood (R0.9) you get 8.68 total R value. That puts the surface at 73F. With R9 of insulation it's 11.68 total and the surface is at 73.5F.
The other way to look at it is that in order for condensation to happen heat has to be dissipated. With the bare block wall the heat flow through the wall is 14.9 Btu/sf/hr. It takes about 1000 BTU to vaporize a pint of water, so a 100 square foot section of wall has the heat flow to condense about 1.5 pints per hour.
With R6 of insulation the flow is 2.9 BTU/sf/hr, the same 100 square feet can condense 0.3 pints per hour. With R9 the flow is 2.1 BTU/sf/hr or 0.2 pints per hour.
It doesn't seem like there's a big difference between 1" and 1.5".