Insulation Over Furring Strips in Basement

I’m thinking of insulating a basement wall with 2-1/2″ polyiso continuous. This would be covered in drywall. I know that a common way of doing this is to put the insulation against the wall, then hold it with 1x furring strips, then attach the drywall to the furring. But I want to do it differently. I want to attach the furring to the wall, then tack the foam to the furring and use long drywall screws to attach the drywall to the furring through the foam.
I want to do it this way for a few reasons. First, I think it’s easier. If I attach the furring directly to the wall I can use short fasteners, which are inexpensive and available in a lot of different styles. If I go through the foam I have to use 4″ or longer fasteners, which are expensive and have limited choices. Long drywall screws are easy to find and cost pennies. If I’m attaching the furring directly to the wall I can see what I’m drilling into and avoid mortar joints; if I go through the foam I’m drilling blind. With the furring strips against the wall I can run electrical against the wall and out of harm’s way rather than directly under the drywall. I can also follow the more usual construction sequence of framing/electrical/insulation/drywall rather than having the electrician come back after the insulation guy is done.
Any reason not to do this?
GBA Detail Library
A collection of one thousand construction details organized by climate and house part
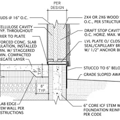
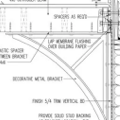
Replies
DC,
I can't see why it wouldn't work. Presumably you would need thicker furring. Maybe insulate between the strips too, or would that defeat the easier electrical install?
>Presumably you would need thicker furring.
Drywall screws only need to penetrate 3/4" so 1x furring is fine. However, the thickness of my assembly is 3/4"+2-1/2"+1/2"=3-3/4". Since the furring has masonry behind it the screws can't penetrate any deeper, so I'd have to use 3-3/4" screws. Which aren't a standard size. But 4" are. So I might use either a 5/4 furring strip or 1/4" plywood shims so I can use 4" screws. This has the benefit of making the assembly 3-1/2" to the drywall, so I can put a treated 2x4 at the bottom without having to rip it.
>Maybe insulate between the strips too, or would that defeat the easier electrical install?
I wonder if that would make it easier to air seal the assembly (and reduce the damage from air leaks). With two layers I could tape both layers. With the furring shimmed I could put 1" between the furring. I might then be able to get away with 1-1/2" continuous over top. Then I can use 3" drywall screws, even better.
There's not going to be a whole lot of wiring so I think I could just cut channels in the 1" insulation where needed. With the furring shimmed I could run the wire between the furring and the wall. It would need protection plates so I don't put a drywall screw through the wire.
Deleted
Searching the archives I finally found someone asking about a similar construction. But now I can't find it. The objection posed was that the gap between the foam and the wall would be cool in summer, at ground temperature, and if air got in there water vapor would condense. There would be no way for the water to dry either to the inside through the foam or to the outside through the wall. The water would be trapped, and the furring would rot away.
I need to ponder this.
That seems like a valid concern. The question is not about whether air might get in there - of course it will. Even if the cavity is air sealed top and bottom, it won't be airtight. And that cavity has very good vapor barriers on both sides. Worse, it probably gets a low amount of moisture vapor flow through the masonry. We can safely assume that the cavity will be at 100% RH permanently, though whether or not it has actual condensation could be debated. That will depend on lots of outside factors. I would certainly allow for a drainage pathway just in case. Regardless, whatever material is used for furring must be moisture-proof. Treated lumber would probably be OK, with stainless fasteners. There are SS alternatives to Tapcons, at close to $.50 each. Steel studs generally don't have enough galvanization on them to last more than a few years in that environment. Pultruded fiberglass channels would be great if you can find them at a decent price. These are also termite proof, which is a good side benefit in termite country. Once installed, you won't be able to inspect the cavity for termites.
I’m going to suggest an unusual alternative: use pvc trim board for the furring. This material won’t rot, and doesn’t require the use of stainless steel screws, either. It’s not that expensive in 1x2 sizes.
The downside is it’s not super stiff and might not be suitable if you want to hang stuff off of it. If you just want the strips as spacers you’ll be fine, if you want them to be supporting other materials you probably don’t want to try this idea. My thinking is if you’re going all the way into the concrete wall with your fasteners anyway PVC might be a good material here, but if you want to hang the wall off of the furring to avoid using long masonry screws then PVC isn’t a good choice.
Bill
Interesting idea, Bill. I was thinking maybe pressure treated but PVC is actually impervious. Agree that stainless fasteners aren't necessary or wanted.
I'm thinking 1x3 so the drywall guy has a fighting chance of hitting it through a few inches of foam.
My thought where I have to hang heavy things is to use 1/2" plywood instead of drywall, and attach it to the furring with deck screws instead of drywall screws. If I have something really heavy I'd run it all the way to the floor, rest it on the floor and screw it to the 2x4 I have running along the bottom. So the furring strips aren't holding any weight, just keeping everything against the wall. Depending on how we do trim I may run a strip of plywood along the bottom to give something for the baseboard to attach to.
> I'm thinking 1x3 so the drywall guy has a fighting chance of hitting it through a few inches of foam.
Subcontractors in very specific fields get very good (and fast) at doing the common thing they're asked to do. Once you ask them to do something outside normal operating parameters, they either get expensive or bad.
Maybe I'm a bit more cynical than you, or maybe it's harder to find good labor in NJ, but I would never try to get a typical drywall contractor to do what you're describing.
I have installed drywall over foam in a basement using tapcons through the drywall and foam directly to the concrete block. I kept the quantity of screws to a minimum, as the wall was rock solid with full insulation behind it. I have done the same with osb, however osb may not provide a code-legal thermal barrier.
I have to put 32 screws in each piece of drywall. That's a lot of tapcons.
I didn't put near that many.
This will be inspected. Drywall is part of the fireblocking of basement walls. DC is fanatical about fire code, there's a lot of old housing stock that is firetraps so they want everything new to be strictly to code.
That seems strange to me. A place not far from a friend of mine in federal hill had an existing brick wall collapse while doing some major renovation work. I can’t remember if it was a 2 or 3 story wall. Apparently things got interesting and litigious since it was a shared wall with an adjoining property. I’m surprised it wasn’t more thoroughly checked.
My personal recommendation would be to inspect ALL masonry structure out there when doing ANY project that makes such an inspection feasible. It’s not worth risking a collapse or problems down the road. I love the old structures, but they bring potential risks that need to be considered when doing any work.
I haven’t been out there in several years and miss it, especially all the crab stuff :-) I hope restaurants out there are doing ok with all the pandemic issues. Maybe it’s time for me to put in an order with G and M. Hmmm...
Bill
If it's existing it's grandfathered. New construction pretty much needs an structural engineer. This project will use part of the existing foundation and part new. I found it ironic that the new part required soils tests and an engineer to design the footings, the existing part the engineer basically said, if it's standing it's good.
So now I'm thinking (over-thinking?) that drywall sits best when it rests directly on the thing it's screwed to. So that would mean furring on top of foam.
I would see if you can reduce the insulation a bit. In zone 4, you don't need all that much R value in a basement unless code calls for it.
If you can go down to 2" rigid, with 1x4 strapping, you can nail up the whole thing with 4" nylon hammer set anchors. No need for reverse strapping and issues with gaps, the 4" anchors are $0.30 each, not a huge budget item.
I haven't personally confirmed it but I was told the city now wants R-15 continuous in basements. DC wants to be a leader in energy efficiency.
IMO, foil faced polyiso + against wall furring creates a sizable and very high humidity gap and this increases mold smell risk. Even with no gap it's questionable.
https://www.buildingscience.com/documents/insights/bsi082-walking-the-plank
Reaffirmed in 2015 (long after "The perm rating doesn’t matter"):
https://www.buildingscience.com/documents/information-sheets/crawlspace-insulation
My immediate reaction was that sandwiching wood, and even electrical connects, between poly-iso and a concrete foundation wall is a recipe for material degradation. Perhaps this stems from my living in Maine with wet basements, but I can't imagine doing that, even on new construction with exterior waterproofing materials (just a risk thing).
How many fasteners are needed to attach the furring to the concrete? If the answer is too many, how about standing up a 2x3 or 2x4 wall with plates, interior to the foam, and forget about the masonry fasteners altogether—if avoiding long masonry fasteners is a primary goal. Glue the foam to wall beforehand.
No fasteners would remove the ?? risk of fasteners eventually rusting and the drywall falling down.
OP here. After reading the input I'm now thinking of abandoning the idea of furring to the inside. Instead, I'm thinking of 1.5" of foil-faced polyiso continuous against the wall, attached by furring strips ripped 1" thick from a 2x4, with 14.5" strips of 1" polyiso between the furring strips. At the bottom there would be a pressure-treated 2x3 (or more likely a 2.5" strip ripped off of a 2x6). At the top there would be a top plate that is sized to sit flush against the sill on one side and the drywall on the other, to provide fire-blocking. The inner layer of polyiso would be horizontal with the seams taped, the outer layer would be vertical and taped to the furring. Between the concrete wall and the polyiso I would put waterproof sheeting.
The furring would be attached to the plates at the bottom and top, and then 3-3/4" tapcons on 24" centers. An 8" furring strip would have three tapcons, which I think I can manage, they're $24 for 100 on Amazon.
I'd have to carve space for electrical but that's just going to be wall outlets every 6'.
Thanks everyone for their input.
1" strips ripped from a 2x4 will probably split when fastening them. I'd use strips ripped from 3/4" plywood instead which will hold up much better while you're installing them.
I would bevel cut the lower edge of the polyiso where it sits against the 2x3 sill plate, or gap it a little. This will help limit the changes of water wicking into the polyiso if you ever have any moisture down there. Just a little extra insurance, basically.
It shouldn't be too bad cutting out spots for electrical work. I would decide if you want to feed from the ceiling or horizontally along the wall, then I'd install EMT conduit between 4" square boxes. If you use 1.5" polyiso, then standard 1.5" boxes will fit flush. If you need to adjust the depth any, just use mud rings on the boxes. The conduit will make wiring easier, especially if you ever need to make any changes, and you can encapsulate the conduit in canned foam in the slots in the polyiso if you want to maintain your air seal.
Bill
Thanks Bill. I was thinking for electrical I would try to run the wire so the outlets are all at the end of a run so just a single cable going into the box, coming down from the ceiling. I'd use shallow new work boxes, 8 cubic inches and 1-1/4" thick, with a side bracket attached to the furring strip. These would go in after the first foam layer and furring strips are up, but before the second foam layer. The second foam layer would be notched on the back for the wire and cut for the box.
How does that sound?
Probably doable. I'd try to use 4" square boxes and mud rings if at all possible, they make the electrical work a lot easier and the mud rings come in many depth options so it's easy to get the devices up to the correct level in the finished wall.
No problems running the wire in the foam, but I'm a HUGE HUGE proponent of using conduit in places like this where the wire will be buried in the wall. Conduit also eliminates the code issue with keeping the wire deep enough in the wall to avoid the possibility of nail/screw hits. You could either run conduit from each wall box up to a ceiling junction box (note that code requires these junction boxes to be ACCESSIBLE though, so either concealed above a drop ceiling you can open, or mounted with a blank cover on the ceiling so that you can get into them after finishing the room), or you could run the conduit horizontally to pick up all the wall boxes and only go up to the ceiling in one place for a supply wire.
Lots of options, so which way you go is really dependent on the layout of your specific site. I'd strongly consider the conduit option though. Foam walls aren't fishable like hollow walls are, so you can't ever add another wire without cutting into the wall. With conduit, you have more options, and more protection. Imagine someone hanging a picture one day with a nail and going through the foam right into your wiring. Mr Murphy is probably hiding out in your house somewhere right now giggling about that possibility ;-)
Bill