Interior rigid foam over concrete slab

Looking to remodel my 1980’s slab-on-grade home located in southern Maine. The plan calls for removing the carpets and replacing with hardwood or engineered flooring. Where this will involve placing over concrete, I had planned to put a class I vapor barrier (15-mil poly) over the floor, then two layers of plywood for the new flooring substrate. I’m wondering if I could use 1 or 1.5-inch foil faced EPS foam instead of the poly, followed by the plywood. Do you think this assembly would provide the same moisture protection for new wood flooring? Does the foam offer any energy benefits, insulating the presumably cold underlying concrete? Is the EPS the correct choice… or do I need to use a different product?
Any info is much appreciated. Thanks!
GBA Detail Library
A collection of one thousand construction details organized by climate and house part
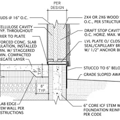
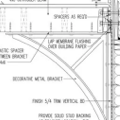
Replies
An inch of EPS is sufficient to keep the bottom of the subfoor in you stackup above the average summertime outdoor dew point in southern ME, limiting the mold potential. An inch of EPS on it's own is not sufficient protection against ground moisture unless there is already sub-slab vapor barrier, but with a foil facer it's enough.
Tape the seams with foil tape to avoid moisture-striping. Overlap the edges of the subfoor layer with those of the foam by a foot or more- if the edges of the subfloor & foam are aligned there is some potential for compression of the foam in high traffic areas.
There is an energy benefit, and it's financially rational on a lifecycle basis for more than an inch, but it's really mostly about resilience and avoiding the musty-basement smell.
Todd,
Dana gave you good advice. To sum up:
1. If you choose rigid foam without a foil facing, include a layer of polyethylene between the concrete and the rigid foam.
2. Consider installing rigid foam that is thicker than 1 inch.
Going thicker than an inch as a retrofit often requires re-building the stairs to meet code for rise-height. Sometimes that's true even at 1".
But if there's sufficient headroom, as much as 2.5" of EPS can still be financially rational on a full lifecyle basis (lifecycle of the house, not necessarily your occupancy.)
Going thicker than 3/8" requires re-building the stairs. That's the allowable amount of riser deviation from tread to tread. People always miss this when changing floors.
One solution can be to build a landing, if there's space. The step up to the landing can be different than the riser heights going up from the landing. The right landing can also be a nice aesthetic improvement to the stairs, if done right.