Is 3 inches of sub slab EPS enough in Climate Zone 7?

We are remodeling a 40 x 30ft house with extensive cat damage and urine odor. House is located in Vilas County, northern Wisconsin, in climate zone 7. Although I think IECC 2021 may have shifted it into zone 6?
40 x 30ft basement is a walkout with one 40 ft above grade wall facing due west. The other 3 walls are at least 5 ft below grade. No washed stone, plastic, or insulation under, around, or outside the old slab or basement. However, soil drainage is good. No radon system and radon runs 4-7. House was built in 1971. 48 inches of exterior horizontal XPS was added under ground next to house on walkout side years ago when grading around house was fixed to shed water away from the foundation.
We cut up part of the old basement slab to replace non functional plumbing, filled the rest of the plumbing trench with washed stone and added radon piping in case it is needed.
We are getting ready to put in the sub slab foam which will be sandwiched between the old slab and new slab. After much discussion, there will be NO radiant heating in the slab.
I was originally going to put 3 inches of GPS (R15) under the slab and along the slab edge. A 2 inch layer covered by a 1 inch layer with taped seams. I could only find 13 PSI GPS and it is much more expensive than I expected. I read many things online suggesting it was cheaper than XPS.
I decided to just use 3 inches of GPS on the slab edge (and possibly 2 inches on the wall – I have a different post about that) and use EPS sub slab. Unfortunately I can’t use 4 inches of EPS due to some height constraints I did not plan for even though the house was lifted to give a little extra height to add the new basement slab.
Will 3 inches of EPS foam (R13) be enough to prevent condensation and cold spot issues in the new slab on the walk out side of the basement? I was trying to get to the R15 recommended for slab on grade for climate zone 7 due to the walkout. My feeling is that 3 inches of EPS is decent considering my constraints but I would prefer getting that confirmation from others who have some experience.
15 mil vapor barrier will be placed over foam. Seams and plumbing will be taped. I am hoping I won’t need to use the radon piping we put in but if we do, the sealing attempts should help depressurization the slab if we need to hook up a fan.
Thanks for any input.
GBA Detail Library
A collection of one thousand construction details organized by climate and house part
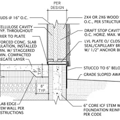
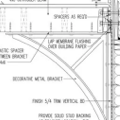
Replies
All of Wisconsin is now in CZ5A or 6A (https://codes.iccsafe.org/content/IRC2021P1/chapter-11-re-energy-efficiency#IRC2021P1_Pt04_Ch11_SecN1101) Vilas county is 6A.
There are no code requirements for sub-slab insulation under unheated slabs but practically speaking in cold climates it's a good idea, especially with walkout basements. The IRC does call for R-10 either 4' down, 4' horizontally or a mix; your 3" EPS will be about R-12 so it should meet code. Doubling the R-value cuts heat flow in half, so the difference between R-12 and R-20 means you'll lose a little less than twice the heat that you would otherwise. But heat loss under a slab is not huge due to the relatively small change in temperature. Your main heat loss will be at the exterior wall so if you can beef up the insulation and thermal breaks there it will have an effect. But R-12 under the slab is not bad at all. In fact the Pretty Good House recommendations for cold climate sub-slab insulation, borrowed from Dr. Joe Lstiburek's recommendations, are at least R-10, so you are in good shape.
Michael,
Thanks to Bill, I am now considering foam board on the cement block basement walls above the slab instead of spray foam due to timing issues where the block might be too cold to spray foam this fall. It is also greener.
I was originally going to bring the slab edge foam up above the new slab at least 12 inches. That way, if I did decide to use foam board instead of spray foam, I could use one 8ft foam board on top of that to reach the top of the block or bottom of the joists on top of the sill plate. I should have 106 inches from the top of the horizontal sub slab foam to the bottom of the floor joists. I have not seen much guidance on foam board sealing and good detailing at the top of the wall.
Would it be better or worse, long term, to just use 8 ft sheets from the sub slab foam until they ended approximately 10 inches from the top of the wall? I am using more than one layer on the slab edge to get a higher R value and this would only apply to the thickest sheet up against the wall. I would keep the other layers shorter but still above the slab. That way I can overlap the seams.
Is this a bad idea if there is a problem later because the slab edge foam might get damaged if the wall foam ever needs to be removed? Should I be trimming all the slab edge foam to slab height and then placing the wall foam on top?
Thanks,
Jay
Michael,
Thanks for the zone clarification and your input regarding the amount of EPS. I will start referencing zone 6A when I look things up now.
I feel better knowing that, yes, it could be a little bit better with another inch of EPS, but 3 inches is pretty good, especially compared to the zero inches it is replacing.
I will have R15 GPS on the slab edge. Not much better, but a little. And I posted a different question about my basement wall insulation.
We also plan to put in a patio slab (someday) outside the walkout basement and will put another layer of foam (EPS this time) under the patio slab. I forgot to mention that the footing on the walkout wall (from 1971) is not a frost depth footing so it is only down about 12 inches. That is why we added the horizontal XPS (2 inches thick) previously to try to keep frost away. Luckily the soil is well drained and also drops sharply to a lake in front of the house.
Jay