Is it better to let concrete breathe or seal it off in a finished basement?

I’ve posted about my issue elsewhere in the Q&A, but in summary: 6 lbs/1000 sq.ft/24hr and up to 95%RH in a concrete basement floor, zone 5. Never any actual water, just high humidity. Cannot reliably do a floor coating like epoxy due to high levels of contaminants – risk of delamination.
I’ve read the articles, and I see conflicting information.
I’m going to finish my basement, using 2″ reclaimed XPS on the walls, 2×4 cavity w/ bat insulation, sill seal under the plate.
What is the best option for the floor? Our flooring choice seems to be LVT due to cost and waterproof properties (although I’ve seen articles saying don’t use it because it won’t let the floor breathe. I’m leaning away from tile due to the grout picking up efflorescence.
1) A dimpled membrane up to the finished wall and let the floor breathe to the edges (hitting the plate, drywall, insulation). Will this option mean my basement will have a musty smell?
2) Kovara MBX taped up to the finished wall (not beyond), which is supposed to provide a class 1 vapor barrier (if my terminology is correct), which will simply stop the vapor altogether, but provides little insulation. My assumption is this encapsulates the floor and the sill seal and foam will handle the edges of the room.
https://gcpat.com/en/solutions/products/kovara-moisture-barrier/kovara-mbx
3) Put down poly and 1/2″ of reclaimed XPS and 1 layer of OSB (trying to not have to redo furnace, stairs and walkout door, but if necessary can do 1″) – losing about 3″ of head space when complete; only have 8 foot walls, some beams will drop down to 6’6″. If this is the best option, does the poly go to and slightly up the concrete wall behind the foam?
The space is quite large, not all will be finished, but all will receive the flooring treatment due to the need to stop the humidity. 2700 Sq.Ft. total, about 1800 finished. That’s why I am concerned a little about the cost of any solution.
GBA Detail Library
A collection of one thousand construction details organized by climate and house part
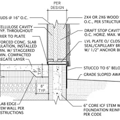
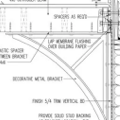
Replies
Concrete doesn't need to "breathe", it is perfectly happy sitting in water. The problem is mold. You want to avoid air getting to the wet surface.
I've done LVT on bare basement concrete floors with no barrier underneath, but these were dry with low moisture content. It works great and much more comfortable than tile.
If you have the time, one idea is put down a vapor barrier over an area (~100sqft) and cover it with LVT. You can use standard poly or the fancy one above, anything works as long as it is not compliant. Let it be for a while, a couple of months to a year, then lift up the LVT. If it looks good, then finish the entire basement the same way. Moisture under the vapor barrier is fine, you don't want to see moisture or mold under the LVT.
You can go with tile as well, if you roll the concrete with a standard shower waterproofing membrane, the efflorescence won't come through the grout.
You can also give the insulated sub floor manufacturers (Drycore or Barricade) a call and see what they say about compatibility with your concrete.
I wish I asked this question sooner - putting down 100sqft is a good idea.
I'll do more research on Drycore as well. I did initially look into that, but it has seams, so I backed away.
Thanks for your response.
Hi Scott
Curious what you finally did for your basement concrete. I am in a similar situations here with moist basement concrete floor and a low ceiling height. So my options are limited to low profile floor finish like Epoxy, polished concrete or LVT. Tiles or insulated subfloor are not preferred as it reduces ceiling height . How is your choose turning out ?
Thanks
Hey Charlie,
I ended up using a product called Eco Cork Foam (ECF) under Luxury vinyl plank flooring. I called and spoke with someone at ECF about their documentation which says it's not supposed to be used in these conditions, and she agreed with me that these conditions are exactly where it should be used. I never checked to see if they've updated the docs yet. She was a VP. I Zip taped the ECF to the edge of the sill plates to seal as much moisture from the drywall as possible. You cannot nail through the ECF.
https://www.homedepot.com/p/Eco-Cork-Foam-75-sq-ft-3-ft-x-25-ft-x-3-2-mm-Waterproof-Premium-Plus-10-in-1-Underlayment-for-Vinyl-Laminate-Engineered-Floors-220000503/204700858
The LVP is rated for 8 pounds/1000 sq/24 hours, so my floor was in spec regardless. I felt more comfortable using the underlayment though.
I used 2 inch reclaimed xps foam board behind the framed 2x4 walls and used sill seal foam under the pressure treated sill plates. Walls are insulated with R-15 rock wool as well. So somewhere around R-25 total.
I also installed a sump pump for extra insurance, and as expected there is no water anywhere near the floor. I believe it's several feet under, but only near the frost wall for the walkout. I think I will also install a passive radon system to start, just to see if anything changes, and perhaps go to a fan if needed. I already have the pipe that goes up to the attic, it's just not up through the roof yet. Could be overkill, but it's cheap enough.
Time will tell!!
Scott
Hi Scott, hope all is well. I have pretty much exact situation and plans when it comes to walls and floor, so I wanted to ask how is it holding up? What made you choose ECF vs Kovara? Were you able to eliminate the musty smell? Would you do anything different today? Much appreciated!
Hi Sebastian, the major factor was cost vs. performance. The Kovara was going to cost about $9-12k if I remember right, vs. about $1500. The floor already being in spec for the LVT anyway.
Knowing what I know now, I probably would not have done the sump pump, there just wasn't a need for it in my application. It's cheap insurance though if you think you might ever need it.
What I do suggest is to install a radon system. What I noticed in my house was the radon gas levels increased after finishing the space. The gas wasn't able to dissipate as easily as before due to the tight construction. Even without radon issues, the system creates a vacuum that will remove humidity and moisture (and smells) that can come through the concrete, and the systems aren't that expensive. I already had the pipe installed, just not completed in the attic and through the roof. You can just as easily do one that runs outside the house if you don't mind the aesthetics. In fact, you could try this first and let it run for a few months, see if conditions improve.
I'm happy to say, it's been complete for a year and no issues yet, plus my radon levels are basically as low as they can get. I am not running a dehumidifier anymore, and I have not had to heat or cool the space (although it's about 58 in the winter and 62 in the summer, some could argue that I could - it just doesn't seem that cold down there). Humidity remains consistent with the rest of the house (forced air system).
This all being said - I can't inspect the floor at this point, so I have to assume that all is well due to the lack of any symptoms!
I just read a comment by Martin Holladay on a GBA article
(at https://www.greenbuildingadvisor.com/article/smart-vapor-retarders-for-walls-and-roofs )
"From a moisture management perspective, it's hard to improve on a 2x6 wall with an adequate thickness of rigid foam on the exterior side of the wall sheathing.
Everything on the exterior side of the rigid foam dries to the exterior.
Everything on the interior side of the rigid foam dries to the interior.
The rigid foam prevents inward solar vapor drive during the summer.
The rigid foam keeps the wall sheathing warm enough during the winter to prevent condensation or moisture accumulation.
According to researchers who have monitored the moisture content of wall sheathing in a variety of wall types, this wall stays dryer than any other wall."
With a few minor variations, this is also what you want in your basement -- an impermeable barrier, and to the extent drying happens it's from the barrier outward in both directions.
Deleted
Hmm... won't let me reply to Sebastian's question directly, sorry if this is duplicated.
Hi Sebastian, the major factor was cost vs. performance. The Kovara was going to cost about $9-12k if I remember right, vs. about $1500. The floor already being in spec for the LVT anyway.
Knowing what I know now, I probably would not have done the sump pump, there just wasn't a need for it in my application. It's cheap insurance though if you think you might ever need it.
What I do suggest is to install a radon system. What I noticed in my house was the radon gas levels increased after finishing the space. The gas wasn't able to dissipate as easily as before due to the tight construction. Even without radon issues, the system creates a vacuum that will remove humidity and moisture (and smells) that can come through the concrete, and the systems aren't that expensive. I already had the pipe installed, just not completed in the attic and through the roof. You can just as easily do one that runs outside the house if you don't mind the aesthetics. In fact, you could try this first and let it run for a few months, see if conditions improve.
I'm happy to say, it's been complete for a year and no issues yet, plus my radon levels are basically as low as they can get. I am not running a dehumidifier anymore, and I have not had to heat or cool the space (although it's about 58 in the winter and 62 in the summer, some could argue that I could - it just doesn't seem that cold down there). Humidity remains consistent with the rest of the house (forced air system).
This all being said - I can't inspect the floor at this point, so I have to assume that all is well due to the lack of any symptoms!