Is rigid foam board over fiberglass batt insulation on a truss rim joist parallel to interior floor trusses ok?

My home in suburban Atlanta built in 2006 has a combination of 2 x 4 and TGI floor trusses built on a basement. On the rim joist parallel to the floor trusses it is framed with 2×4’s 16″ on center with a top and bottom 2×4 plate to equal the height of the floor trusses, 16 inches. The rim joist had poorly installed fiberglass batt insulation installed all the way around. I’d like to improve the insulation in these areas. My plan on the rim joist parallel to the floor trusses was to install unfaced fiberglass batt insulation the the cavities, then cover with 2″ of rigid foam board, seal with can spray foam . I will cover this with 1/2 drywall for a fire barrier. Is this installation ok, or should I forget the batt insulation and just cut blocks of foam and install in the cavities? The above grade basement walls have 2×6 framing, so I would be able to install sheetrock from the basement walls all the way to the first floor subfloor.
GBA Detail Library
A collection of one thousand construction details organized by climate and house part
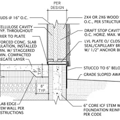
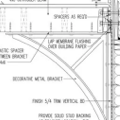
Replies
It's easier to make the rigid foam air tight when it's pressed up against the rim joist, and air-tightness is essential for avoiding wintertime air-transported moisture from ending up in the rim joist. With 2" of rigid foam against the rim joist you can put a substantial amount of fiber-R on the interior side of that without running into dew point issues at the foam/fiber boundary.
If that's too much cut'n'cobble, a flash inch of closed cell foam on the band joist and blown fiber in netting for a perfect fit would work. Even that would be overkill in your US zone 3 climate. Simply air-sealing the rim joist to the foundation sill and the foundation sill to the foundation would be sufficient, then blowing it full of fiber would be fine, as long as you install the interior-side gypsum and put a coat of latex primer on it. Closed cell foam and foam board is more vapor retardent than ideal, and would lower rather than increase the moisture resilience of the assembly in that climate. Like the foundation sill itself, you don't want cellulose to be indirect contact with the concrete- it needs a capillary break of some sort. A cut'n'cobble of 1" EPS (faced or unfaced) sealed in place with can-foam on any ledge of foundation would be fine. Having the cellulose in contact with the foundation sill, band joist, and trusses will LOWER the moisture content of the wood, since cellulose wicks and redstributes any moisture, without damage or loss of function (until it's fairly saturated.)
Brent,
I agree with Dana. If you install a combination of rigid foam and fluffy insulation, the rigid foam goes against the rim joist, and the fluffy insulation goes on the interior side of the rigid foam.
When you install the rigid foam insulation, it's essential to pay attention to airtightness. For more information, see Insulating Rim Joists.
But in Atlanta the wintertime interior moisture drives are miniscule, and the use of foam only hinders drying rates. As long as it's air-tight to the interior and there are capillary breaks between the fluff & concrete, fiber insulation makes it a more resilient structure in that climate. (Move 500 miles north and that's no longer true.)
In climate zone 3A (or 4A) the IRC doesn't even prescribe a minimum exterior-R for above grade walls for dew point control when using only latex paint as the interior side vapor retarder:
http://publicecodes.cyberregs.com/icod/irc/2012/icod_irc_2012_7_sec002_par025.htm
In a climate with winters that moderate, installing layers that are more vapor retardent (lower permeance) than latex paint doesn't help, only hurts the moisture resilience of the assembly, and increases the likelihood of mold issues during the humid summer months in air-conditioned homes. Air tightness is important here, but keep it relatively permeable to water vapor.