Encapsulating a Crawlspace

Thanks to GBA, I have made numerous upgrades to my 1952 ranch home. This includes applying a bitumous paint on the exterior of my crawlspace, then applying Rockwool Comfortboard80, and adding a foundation drain before back filling. Inside the crawlspace, I added poly sheeting on the dirt/rock floor and all the way up the sides of the concrete block, taping the joints and the termination points, adding insulation in the sill joists, insulating all water pipes, and running a SantaFe dehumidifier 24/7. Recently, I added some Rockwool Safe ‘N Sound to the floor joists to add a bit of warmth and lots of sound dampening to the rooms above.
Now that it has been several (5 +/-) years since that work was completed, I am starting to work on the basement. The home is shaped like a capital “T” (basically), with the crawlspace in the “vertical” portion of the T, and the basement in the “horizonal” portion. There is a half wall that allows access from the basement into the crawlspace.
I would like to:
1. Add Rockwool Comfortboard80 to the crawlspace floor to add a bit of warmth. These boards will be placed without fasteners, as I plan to leave this “room” isolated from the rest of the basement. Must I then remove the insulation in the floor joists above?
2. Build an insulated wall with an access door in the opening above the half wall.
3. Add a vent, attached to a pipe that runs to the dehumidifier, to this new half wall in order to continue dehumidification in the basement (SantaFe has instructions on how to do this).
Does this sound like a reasonable plan? I plan to insulate the basement and turn it into a teen hangout/gym/future Mom cave (;)) according to the advice I have already received here, but I think that making these two spaces separate may help with climate control and healthy air management. Will that be the case?
GBA Detail Library
A collection of one thousand construction details organized by climate and house part
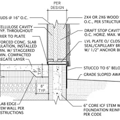
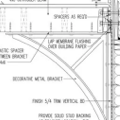
Replies
Moisture migrates into your basement through the concrete walls and floors. Even if the outside of the wall is coated, chances are you didn’t coat the bottom of the footing & that moisture migrates up & into the basement. Your assembly needs to include a heavy, tight, unbroken moisture barrier on the interior. Chances are, once that’s done, you’ll need the dehumidifier much less if at all.
"Inside the crawlspace, I added poly sheeting on the dirt/rock floor and all the way up the sides of the concrete block, taping the joints and the termination points, adding insulation in the sill joists, insulating all water pipes..." Isn't this a "heavy, tight, unbroken moisture barrier on the interior"? It is probable that I don't need the dehumidifier most of the year, but it is a (pricey) security blanket.
When I see people using words like isolate and encapsulate it seems to me, they are setting themselves up for failure.
The way I see it the space can be vented safely or conditioned safely. When people try to be somewhere in between it becomes a game of Russian roulette with mold and rot.
Only once people can bring themselves to call it a conditioned crawlspace will be willing to commit to putting ductwork/equipment to keep the space at more or less the same temp and humidity as the rest of their conditioned spaces.
I see insulating the dehumidifiers waterline plan as an admitting that you want to play roulette.
I see insulating the joist plan as an admitting that you want to play roulette.
I think you need to move all the insulation to the exterior walls and heat and cool the space.
Walta
"I see insulating the dehumidifiers waterline plan as an admitting that you want to play roulette." I'm not sure what the "dehumidifiers waterline plan" is; could you clarify?
"I see insulating the joist plan as an admitting that you want to play roulette." Is this referring to the floor joists? Why would this be a problem?
"I think you need to move all the insulation to the exterior walls and heat and cool the space." The insulation is on the exterior of the exterior walls; do you mean to add insulation to the interior of the exterior walls, as well? One of the reasons I wanted to separate these two "rooms" is that the basement, uninsulated, is much cooler than the crawlspace area.
My home is heated and cooled by ductless minisplits, so there is no HVAC unit to which I could add a vent. Should I add a two floor vents that will allow the conditioned air to circulate to both the basement and crawlspace (one floor vent from the main living space to the crawlspace, one floor vent from the main living space to the basement)? And another vent in the half-wall adjoining the basement to allow the conditioned air to circulate from crawlspace to basement?
Exterior foundation insulation, if foam, is subject to critter infestation. It can (theoretically) be stopped by a good layer of stucco. Problem is that critters can and do dig below the stucco level. I used that method years ago, but stopped when I had a few calls about critter infestation into the house, and the solution was to call Pest Control regularly. I decided against using a method that required poison around the house. Isolating the slab does not involve mold as there are no materials there except soil, gravel, concrete and water, and none of them will support mold. We've built many homes this way with -0- issues, but we do end up with dry, comfortable basements. I don't disagree that you need to be careful insulating basements, or that mold can be a problem if you are not careful. We understand the problems and do nothing that will come back and bite us.
We do not insulate the joists; we fully insulate the basement with methods that also keeps out much of the moisture.
"Exterior foundation insulation, if foam, is subject to critter infestation." Rockwool Comfortboard80 is a rigid board made solely of mineral wool.
"We do not insulate the joists; we fully insulate the basement with methods that also keeps out much of the moisture." Assuming you mean floor joists? Can you expound upon how you insulate basements? Is there anything you do to help eliminate sound traveling up through the floor joists into the living space?
"I see insulating the dehumidifiers waterline plan as an admitting that you want to play roulette." I'm not sure what the "dehumidifiers waterline plan" is; could you clarify?
Since a conditioned crawlspace will be more or less at a normal room temperature there is no practical reason to insulate the lines. One could assume you are spending money insulating the lines because you expect they might freeze if you did not insulate them.
"I see insulating the joist plan as an admitting that you want to play roulette." Is this referring to the floor joists? Why would this be a problem?
Yes, the floor because if you want to avoid mold and rot you need the crawlspace to be more or less the same temp and humidity as the rest of the conditioned space. You put insulation where you expect to see a temperature differential from one side of the insulation. If you insulate the floor one would assume it is because you expect the crawlspace to be cooler than the rest of the house.
You need to condition the air in the crawlspace the way I see it your dehumidifier is a heater that happens to collect liquid moisture for easy disposal. It seem a dehumidifier will keep the crawlspace warm and dry in the warmer months you will need something for the colder months.
Walta
#1. Your instinct to consider removing the mineral wool from the floor joists over the crawl space seems to be consistent with having one thermal boundary. Moving the thermal boundary to the vapor retarder may, on the surface, may seem consistent with recommendations we've seen elsewhere in GBA and building science induced discourse. Bob's and Walta's posts both reflect moisture concerns, but I think they are "different" moistures.
Ground source moisture is being stopped at the poly water vapor "barrier" on the crawlspace floor. Air source moisture needs to be controlled with a vapor retarder on the warm side or you need sufficient insulation on the cold (out) side of the potential condensing surface. Today the polyethylene is a cool surface because you have reduced the flow of heat from the room above with the RW Safe'nSound. With little or no moisture control in the floor system, your indoor air moisture will diffuse to the cooler drier space and condense on the cool poly. The same holds true for your basement even though it may get more heat. Your solution to date is the use of dehumidifier(s) which lowers the air moisture content (absolute humidity), and adds heat thus raising the air temperature (and lowering the relative humidity.)
As we (you Jennifer, and me Eddy) proceed with our DERs we must either:
> keep the insulation outside of the potential condensing surface, OR
> restrict air moisture movement to the condensing surface.
As I see it, you have Two choices:
A. Rigid foam over the poly & remove SafeN Sound from the joists.
> To achieve ~R10 (2021 Code for slabs at 4-ft. below grade), you can keep it simple and use 1 or two layers of EPS or XPS foam that add up to R-10.
> Because you need keep the air temperature up, you need to remove most of the mineral wool from the joists. If you relocate it to the ground over the foam, you can interpret the Code guidance for a hybrid wall assembly with R5ci (presumably foam) and an R13 stud wall (presumably batt insulation). If you go much more than 3-in. of relocated Safe& Sound, I think you need to calculate the estimated foam surface temperature and avoid a mold conducive condition.
B) Foam - free
> Remove the polyethylene
> Place insulation on ground
> Cover the insulation with the polyethylene and seal
I don't think there is any need to use rigid MW insulation.
Simply relocating the joist SafenSound to the ground under the polyethylene should function splendidly.
That is so simple there must be something wrong with this approach.
Perhaps routine maintenance access is the problem.
In both cases, you should not need the dehumidifiers.
In both cases you should revisit the adequacy of the exterior insulation. Code calls for R15 ci. You can add either rigid mineral wool behind the poly, or foam over the poly. Rigid MW over the poly entails holes in the poly and risk of inadequate condensation avoidance.
#2. Insulating the half wall - Forget it. Instead, promote air circulation. If you need a wall, keep it simple - 1 layer of gypsum wall board.
#3. Dehumidifier:
A. You won't need dehumidification in the crawl space if you have adequately insulated to the exterior of the vapor barrier and allow for air circulation.
B. If you build the wall, add a small ventilator fan and an inlet or return register depending on whether you blow the air into or pull it out of the crawl space.
C. If you have an ERV , add a withdrawal in the crawl space.
Additional thoughts:
Basement - Seal the block or concrete,
For the wall, minimum R5 foam first then you can do a batt insulated stud wall (a great place to relocate the Safe'n'Sound to) . Or go all foam with 4-in. Type 1 EPS (my choice), or 3-in. Type 9 EPS or 3-in XPS..
For the floor, I see no practical alternative to foam. I'm using 2-in. Type 9 (2 lb/cu.ft.) EPS foam for R 8.6. and 7/8-in. OSB and 7/16" cork plank flooring for R 1.3. Although that adds up to 9.9, I take comfort in EPS' (and XPS') characteristic improvement in R value as temperature goes down. I am using reclaimed Type 7 XPS under non-bearing walls.
On the walls I am using 2-layers of Type 1 EPS for an R of 15.4.
Of course, the devil is in the details.
For ground moisture ingress - Concrete floor - I applied a concrete penetrating sealer marketed for Radon.
Mold eradication - Sodium carbonate, Sodium bicarbonate and Trisodium phosphate... do not use bleach or vinegar. Second hand lessons learned from Sandy and others.
Insect control - Borax and Boric acid in case you use foam outside, also works to protect wood.
Eddy
Thank you, Eddy!