Join a continuously insulated wall with a regularly insulated wall? (Dew point effects?)

I’m in the Seattle, WA area and currently underway on an addition to our 1910 home. We’re not allowed by code to add exterior (“continuous”) insulation to much of the existing house due to setback requirements and the house already encroaching on them, but I’d really like to add continuous insulation (CI) via mineral wool to the addition we’re building. I’m concerned, though, that joining a CI wall with a non-CI wall (via both inside and outside corners at different parts of the house) — or connecting insulated sheathing to uninsulated sheathing— will create a temperature gradient at the joint that results in some on the insulated sheathing being effectively below the minimum R-value required to avoid dew point effects on insulated sheathing.
Has anyone seen a resource that examines this or had experience with doing something like this? I don’t imagine I’ll have another chance to add exterior insulation to my walls for a few decades, but I’d hate to rot my wall corners for the sake of a little extra R!
GBA Detail Library
A collection of one thousand construction details organized by climate and house part
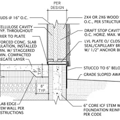
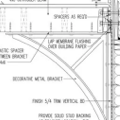
Replies
You only have to worry about cold sheathing if you have a "wrong-side" vapor barrier -- a vapor barrier on the cold side of an assembly. Most commonly this is seen in unvented roofs. If the assembly can dry to the cold side it doesn't matter if the insulation is fully continuous.
Tangentially, here in DC the setback is measured from the sheathing, exterior insulation and siding is allowed to encroach.
DC_Contrarian,
Ah, that makes sense. The current plan is an assembly that, from outside to inside, is: cement fiberboard -> air gap via 3/4” battens -> 1-2” mineral wool -> Tyvek -> sheathing (regular ol’ plywood or OSB) -> framing. Non CI walls will be the same minus battens/air gap and mineral wool. I think this places my vapor barrier on the “wrong side” (cold side”) of the sheathing, is that right? But I think Tyvek is also supposed to allow drying as opposed to poly— does that change the equation at all?
We’ll also definitely be using latex paint on interior walls, so that may retard some drying in the inward direction, too. But I’ll plan to use unfaced batts inside the walls to mitigate that some (or does that not really matter here?).
DC’s code is smart. Unfortunately, I checked with the city and insulation is not allowed to encroach — I was hoping we might have a similar provision. Instead, it seems we measure setback encroachment from the “outside of the exterior wall”. There are a number of backward things in our code that prevent old existing structures from fully realizing energy efficiency gains.
Thanks!
Hi finePNW-
I'll provide my $.02, but disclaimer: I'm not a pro. Much of what I have learned has come from the experts at this site.
I'm building an addition on an older (1908) Maine house, Zone 6A. In essence, I'm tackling the same thing that you are considering - an addition with external CI with a rain screen joined to older non- CI walls. It definitely added considerable complexity to the process. Of course, my rookie-ness has been a factor as well ;-). If I had it to do over again, I would probably keep it simple and more closely mirror the existing structure wall detail, within reason.
As for the old-to-new wall connections; in hindsight I believe I would have been better off to air seal the joints with a piece of membrane- to be subsequently tied-in at the interior and exterior. The goal being to prevent air from the very airy old walls from entering the new wall assemblies. However, my situation was a little different in that I used foil-faced polyiso on the exterior, so inward drying is the only option.
Also - If you haven't yet done so you'll want to look up the ratio requirements for inside/outside insulation for your area.
Best of luck with your project.
Thanks @steve41. Very interesting.how would you have tied in that air barrier?
My climate (Zone 4 coastal) is fortunately relatively mild, and so CI needs are only about 30 % of total — about R 3.5 max for 2x6 walls with fiberglass in the bays.
I’m currently thinking about the rain screen portion of things… do I use tyvek under the mineral wool CI and something else under the non-CI aside from Tyvek? I guess if I’m not using battens over the non-CI bits, it should be fine?
And what about gable ends of my vented uninsulated attic (insulation is just in the attic floor) where I don’t really get any benefit from CI. Does CI over knee walls / gable ends cause any issues with weird temperature/dew point effects? Does leaving gable ends non-CI but the remaining wall below them CI make things weird? I’m thinking I just use extra thick wood fitting against the Tyvek in the gables and keep the whole wall the same thickness… but is different Tyvek needed then? Rain screen Tyvek? Oiy.
I did reach out to Rockwool to see if they have any Details or guidance. Fingers crossed, because I have to get this all into the City’s planning dept soon or risk further delays! (We’ve already poured most of the foundation and will start framing soon) Fun.
@steve41, I’m also trying to figure out my top edge detail. I saw a post of yours on your *bottom* edge detail and wonder if you might be willing to share what your top edge finally looked like?
FinePNW-
**"how would you have tied in that air barrier?" In my case I would have taped the sandwiched piece of membrane to the interior air barrier for continuity and done something similar on the outside...perhaps tape it to the sheathing (sheathing is my air barrier). In effect, this would isolate each wall assembly at the new/old joint. (I would also caulk the new/old joint with something like Contega HF). Again with the disclaimer - I'm not a pro ;)
As for the other tyvek / gable wall CI questions- hopefully some of the experts will chime in. I feel reasonably dangerous with my grasp of my own build, but it would be a stretch for me to offer you feedback....just too many different products.
Thanks @steve41, totally get it re: "danger" :). Thanks! And your description of tying it in makes sense, thanks for sharing. I'll start a new question specifically about the architectural detail questions.
@DC_Contrarian, I'm still a bit confused by "a vapor barrier on the cold side of an assembly". In my case, the coldest side of the assembly is outside of the CI, but the vapor barrier will be between CI and sheating, which makes it on the cold side of the sheathing and certainly not the warm side of the assembly. Just to be clear, you mean the cold side of the CI in the assembly, yeah? My case would not qualify as "wrong sided"? Screenshot of my current draft attached (full disclaimer to anyone looking at this in the future that I have not yet run it by my architect, contractor, or engineer and I am absolutely no pro at this so don't follow my draft).
Thanks!