Keeping a crawlspace vented–insulation options?

I live in a 100 year old barn that was converted to a single family in 1971. It has a field stone foundation and a vented crawl space. Beneath the floor and betweent the floor joists is 30 year old fiberglass insulation.
I want to improve the insulation and eliminate any air flow between the crawl space and living space.
I’ve read every thing I can find about crawl space design and the merits of enclosing the crawl space and including it as part of the conditioned space. However, i’m wondering if that applies in my case considering there are no mechanicals in the crawl space and there will not be in the future. Can I just better insulate the underside of the floor and keep the crawl space vented?
I thought I could put 6 or 12 mil vapor barrier under the joists, and that would support insulation between the joist. Or better, fasten rigid foam board under the joist and use that to hold additoinal insulation. All joints with either method will be taped and spray foamed for air sealing.
Any major flaws in this thinking? Thanks in advance for any help.
GBA Detail Library
A collection of one thousand construction details organized by climate and house part
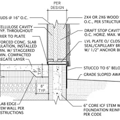
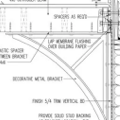
Replies
Steven,
In a house like yours, you can leave the crawl space vented if you want.
If the old fiberglass batts are deteriorated, I would throw them out. Once the joist bays are empty, you could insulate between the joists with spray polyurethane foam.
If the fiberglass batts are in good shape, you can leave them in place. I would insulate under the joists with at least 2 inches of rigid polyisocyanurate foam with taped seams. This work will be difficult to do well if you have round log joists; however. If you have sawn joists, it should go fairly smoothly. Use caulk or canned foam as necessary to assure an airtight installation.
By the way, what's your climate? How do you keep your plumbing pipes from freezing?
Thanks for you reply Martin. I forgot to mention I am in zone 5A ( massachusetts).
I will be disposing of the old fiberglass batts because they are in poor shape and have been home to many critters over the years. The real challenge is going to be access...the crawl space is very shallow in some spots and I will need to do some excavation just to get enough space to get on my back and get under there. I looked into spray foam, but it's expensive, and I'd still need to do some digging for the installers to get under there.
Glad to hear keeping the vents open is an option in this case.
Edited to add that the joists are sawn, not log.
You have a vented crawl space in Massachusetts and your plumbing pipes don't freeze? What do you use -- electric heat tape?
The crawl space has vents, but not all of the crawl space is vented. This is because the original joists of the barn actually sit on the soil, while a newer set of joists was built on top of those. So effectively, not all of the crawl space has exposure to exterior air, but it is not insulated well either.
The water main is below the frost line is about to about 12 feet into the house. The verticle part of the water main that enters the house is wrapped in a lot of insulation. No heat tape. So far, so good, but I suppose the next day or two will be the test because we're having the coldest weather we've had here in years.
Steven,
Since you're going to remove the fiberglass "nest", you might consider replacing it with borate-treated recycled blue jean batts (if the joist spacing is regular). It's a lot harder to cut than fiberglass, but won't be attractive to insects of rodents.
And you would need to apply 2" foil-faced polyiso board, as Martin suggests, under the joists and tape the joints with foil tape. This will not only eliminate the thermal bridging through the joists but also radiantly decouple the floor from the cold ground.
Thanks for your input Robert. Fortunately, I found a local supplier of the recycled denim insulation and have a few 100 square feet sitting in my house now. I'll need to get more. But unfortunately, I'm finding that nothing is regular in this house! So a lot of cutting will be involved.
For the rigid board, I'm assuming a product like Dow's Tuff R?
New questions as my project moves along...
As far as I understand, code calls for vapor barrier on warm side, so in my case that would mean vapor barrier under subfloor above insulation that is between the joists. I'm thinking of the setup as a horizontal wall assembly.
--My plan was to use rigid foil-faced foam under joists to address thermal bridging. If I add additional insulation between the joists and add vapor barrier on top of that, am I creating a bad situation (no way for moisture to escape through foam or through subfloor)?
--Batts would be difficult to place between the joist because they would have to be cut in half the long way. So I think loose fill insulation may be the easiest thing to do. If it settles and I have an airspace under the subfloor, is that a problem? I'd rather not dense pack because that would be harder for me to do myself.
Thanks.
Steve
Steve,
Q. "The code calls for vapor barrier on warm side."
A. No, building codes call for vapor retarders, not vapor barriers, on the warm-in-winter side of some walls and ceilings, in some climates.
Q. "In my case that would mean vapor barrier under subfloor above insulation that is between the joists."
A. No it wouldn't, because as far as I know there is no code requirement for vapor retarders in floors. In any case, plywood and OSB both qualify as a vapor retarder.
Q. "My plan was to use rigid foil-faced foam under joists to address thermal bridging."
A. That will work.
Q. "If I add additional insulation between the joists and add vapor barrier on top of that, am I creating a bad situation?"
A. Adding additional insulation between the joists is fine, but forget adding an additional vapor barrier on top of the insulation between your joists.
Q. "I think loose fill insulation may be the easiest thing to do. If it settles and I have an airspace under the subfloor,is that a problem? I'd rather not dense pack because that would be harder for me to do myself."
A. I suggest you install unfaced fiberglass batts or Roxul mineral wool batts. Install oversized batts so they stay in contact with the subfloor.