LED strip lighting rough-in — what am I missing?
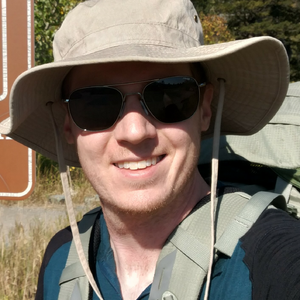
I’ve seen a number of articles promoting the use of adhesive LED strip for various purposes — indirect lighting behind moldings, task & accent lighting in cabinetry, etc. But, I’ve seen very little on the details of how to install it, especially in a neat and code-compliant fashion. So far, the products I’ve found seem to fall into two categories:
1) Very expensive, custom-ordered “architectural lighting” systems where one company supplies LED strip, aluminum extrusions to which it adheres, diffusers, cabling with specialty connectors, power supply, etc.
2) Assorted low-cost suppliers of varying levels of legitimacy, that sell one or more pieces of a system — perhaps they focus on LED strip only, or strip & white-labelled drivers, etc.
The part that I’m not seeing much detail on in all of #2 and some of #1 is rough-in. Let’s say for the sake of discussion that I want to install a couple channels of cove & accent lighting in a room, which is currently rough-framed. I have standard switch boxes with 120V supplied to them. Since the areas that will get the LED strips don’t have much space, I want to locate the drivers remotely — say, in a nearby closet. NEC has only a bit to say about “Class 2” installations, which I believe most LED strips would fall under (24V <100W — assuming a class 2 labelled driver is used) — mostly with regard to separation of the low-voltage and 120V wiring.
– The wiring between the drivers and the LED strips needs to be “class 2” — is there readily available and trustworthy cable suitable for concealed rough installation?
– How does one make a neat and code-compliant penetration through a finished surface? It seems super messy to just drill a hole through drywall and poke a wire out, but a standard junction box would be too big and seems overkill. Are there “micro” junction boxes for this kind of thing? Or some kind of bushing / cable gland that can get roughed-in and then drywalled around to provide a nice penetration point for the cable?
– Are there off-the-shelf cabinets of some sort that could be flush-mounted in a finished wall (or failing that, surface-mounted) that would be appropriate for containing several LED drivers, while providing the required separation between the 120V and low-voltage sides, and providing appropriate safety barriers for the 120V wiring? I don’t think the large “structured wiring” enclosures meet the requirements of 120V circuits, and regular metal junction boxes generally aren’t big enough for LED drivers.
I’ve seen plenty of photos of rooms with this kind of lighting — they look high-end and I can’t believe that they’re all just slapping stuff together haphazardly, so what am I missing? In the real world, how is this stuff done in a neat and code-compliant fashion?
GBA Detail Library
A collection of one thousand construction details organized by climate and house part
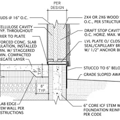
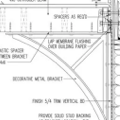
Replies
I would suggest just making sure that a 120V receptacle is close to the intended location and leave it at that, with the conditions I've set out below. I've used quite a bit of the IKEA Tradfri LED bits for several kitchens as their LED drivers integrate nicely with zigbee automation. The same rationale applies for HUE LED lighting which is expensive, but integrates quiet nicely with automation. For automation integration and reliability, the HUE LED system stands out. These systems all have a wall wart, or 120 Volt driver which would plug in to 120V. You want to make sure these items are easy to access. From the 120V driver component, everything is low voltage and can be hidden on cabinet tops etc. If you'd like to really nail this down, you can plan a hidden but accessible location for the 120V bits, and then run smurf tube to a low voltage box at the LED installation site.
Personally, I just make sure that the 120V receptacle is in an area that is both hidden from view, accessible and well vented. LED drivers will last a lot longer if they are kept cool. Make sure you have a good idea of the LED system you are using, and go over installation documents first. An example of this is the Tradfri undercounter LED components which can be chained together, but only to the capacity of the LED driver. A 30 watt driver will only be able to support five of their six watt LED light modules which can be chained together under the cabinet. In that case, you would need one 120V driver, and just one low voltage wire to the start of that chain. I point this out as the rough-in and installation may be easier than you think, depending on components that you use.
For cabinets that don't meet the ceiling, you can plan to have the 120V receptacle just above your uppers (and hide the drivers and wires on top of the cabinets), or have it exit at the back of a base cabinet (and mount drivers at the back or side of that cabinet) for easier access.
For theatre applications, you really need to have an idea of where acoustic wall treatments, acoustically transparent screening, speakers, false walls etc. will sit in order to plan the 120V receptacle for LED lighting appropriately.
I've used LED tape lights many times and I guess I've always gone with your #2 option, even on some fairly high-end projects. It mostly takes a lot of planning and patience. In both examples shown, I used aluminum extrusions and polycarbonate covers for LED strips recessed under the cabinet or floating shelf. The transformers are located nearby. All parts were sourced separately, via various online retailers.
There are *many* reputable sources for class 2 cabling. I typically buy through my commercial supplier (a wire and cable supply house), but there are online suppliers out there. What you need is a starting point for what wire you want.
A typical low voltage power cable would be 2 conductor, 18 gauge. You want bare copper (BC) conductors, preferably stranded in most cases. You need an outer jacket. You don't need plenum rating, but you need the commercial equivalent of the common CL2 rating used for residential, which means CM or CMR for commercial. You can use CMP (plenum) too, since it's a hierarchy -- CMR can be used in place of CM, CMP can be used in place of CMR. You can't go the "other direction" though. A suitable cable from West Penn Wire (a manufacturer commonly specified by architectural firms) would be their number 25224B. Note that Coleman Cable (now part of Southwire) is another possible brand. Many commercial wire and cable suppliers will cross that to a different manufacturer or a house brand. As long as it has the correct rating, you are good to go. I don't think the box stores carry this type of cable though, but you could usually use "thermostat wire" (which typically has a suitable rating) in a pinch, although I wouldn't recommend it -- it's solid wire, not stranded, and it usually has a brown jacket. The commercial standard jacket color for this cable is white.
The downside to buying this stuff commerically is that you usually have to buy standard lenght "put ups", which are typically 1,000 feet, but sometimes 500 feet. Some vendors will cut to order though.
Regarding concealing the hole, I like to take a piece of scrap trim/casing/molding/etc and mill a little slot in it with a router, then put that over the hole as a sort of combo wire guard and trim piece. Just try not to bend the wire tightly around a sharp edge (relieve the edge of the hole), since you don't want to damage the cable. You can use the little plastic cable clips that have a single nail in them to secure the wire under cabinets behind a lip -- you can leave the cable physically exposed like this with low voltage wiring, you just want to hide it from view.
Bill
Monoprice (https://www.monoprice.com) sells CL2 "speaker" wire in a variety of gauges and spool lengths. They also sell through Amazon, which makes shipping easy.
I ran this (16 AWG, stranded, CL2) below and above all my cabinets: https://www.monoprice.com/product?p_id=2823
The only thing I had inspectors check for class 2 lights is the transformer and wire. Outside of that you can do pretty much anything. If you want a better look than wire nuts for connections, you can get something like these:
https://www.diodeled.com/mini-terminal-junction-box.html
There are also nice Wago lever lock splice blocks that work, just make sure it is not a knockoff.
Stay away from magnetic drivers they have a large amount of 120hz strobe.
This cable is in stock at most home stores and is rated for in wall use.
https://www.homedepot.com/p/Southwire-500-ft-16-2-Grey-Stranded-CU-In-Wall-CMR-CL3R-Speaker-Wire-56911445/202316267
Code does not require boxes for class II wiring it is about how you want to do it.
https://www.digikey.com/en/products/detail/hammond-manufacturing/1551BGY/7644387?utm_adgroup=Boxes&utm_source=google&utm_medium=cpc&utm_campaign=Shopping_Product_Boxes%2C%20Enclosures%2C%20Racks&utm_term=&utm_content=Boxes&gclid=CjwKCAiAleOeBhBdEiwAfgmXfx8BIvsXNpKQ5useY9eFV3yJpPxd_CET1t5KQ2oLxLzLHus-NKZxGhoCLT0QAvD_BwE
Walta
I'm in the middle of converting my workshop to an office and movie theater and am installing all 24v lights. I have one 600W 24v AC-DC converter in a central location that will power everything. My setup might be a bit unique but I'm hoping actual execution isn't too challenging: From the DC converter I'll be powering a DMX wall plate switch and a DMX decoder that is inside a structured wiring cabinet, all 24V power runs are ran with 12-2 romex, DMX data is ran with in wall rated cat6 ethernet, depending on light and distance light runs are a combination of 14-2 romex, 14-3 romex, and 16 gauge in wall rated speaker wire. Since the cove lighting is two ~20' runs I'm running 14 gauge 3 conductor to both ends of each run to ensure I don't run into voltage drop issues, 3 conductor is because the LEDs are tunable white. My plan for terminating the run/connecting the strip is to have a horizontal single gang box with a blank plate that has a hole drilled in the middle so I can run the lead from the LED strip into the box and make the connection in there. I also am planning on doing LED lighting for my built in bookshelf by the desk, and unfortunately will probably just go the hole in the wall/side of bookshelf for each shelf that has lighting but will at least be able to do a decent job of hiding it with trim on the sides and shelves, again since there will be quite a bit of strip length wise between all the shelving I'm going with 14-2 on each end of the strip on every shelf to ensure uniform brightness. Lastly I have just 3 24V downlights that will be connected with the speaker wire, this solution works great with the remotely located driver because the light ends up needing only like 1/2" of height above the drywall so no worries about it fitting with the cavity I made using 2x4 on the flat.
A big bonus in my mind by using romex that can run on 120V 15A is if something happens with the DMX setup (unlikely since DMX is a widely known and adopted standard) that causes it not to be reliable for home lighting I should be able to somewhat easily change the lighting out to a more standard system that runs on 120v. The downlights could be controlled by a much more simpler constant voltage driver so I didn't feel it was necessary to run romex to those.
One question I haven't answered for myself is if I want to build some type valence for the ceiling wash lighting or go with one of those aluminum channels I've seen that can be embedded in the drywall and direct the light up. I'm leaning towards the valence type install since I'm worried being able to directly see the light source might cause unwanted glare.
Interested to hear other things people have tried out, especially as I am just now starting the wiring phase of my project!
You are right to be worried about a direct LED strip. To get even light out of an extrusion you generally need high-ish density tape, a deep extrusion and a quality diffuser. For an indirect install this matter much less but you have to be careful with your drywall finish as side lights will show even the smallest imperfection. Some LED tapes will have a yellow tinge on the light at the very edge, this can be quite visible depending on the angle it is installed.
There is no such thing as 600W 24v class 2 power supply. There are some specially one that have individual breakers to generate class 2 outputs from a big supply but these are expensive. Generally, best to stick with individual standard 96W class 2 supplies.
Akos, thanks for the feedback. I realize the power supply is not a class 2 supply but I had trouble coming up with any other practical solution to get more than 200 watts to my DMX decoder (which does limit to 96W per output channel). With LED strips that are 4+ watts/foot it seems pretty easy to run into the 100W limit pretty quickly, what are the options in that case?
Don't buy LEDs from online marketplaces, the W/foot on most is wishful thinking. Even if they do hit the power level, they do so by overdriving the LEDs which causes them to fail quickly. Very few strips can reliably use 4W/foot as at that point you need cooling.
I think the options is to use smaller DMX decoders which can be fed from a class 2 supply or get ones that have class 2 outputs. Even if each of the outputs is limited to 96W, unless it is labeled as class 2, you can't use class 2 wiring.
On visibility of the tape, yes…you really need to model the room, typical eye height in the room and then adjust accordingly so that people are not blinded by your cool light effects :-)
Also, as Akos has pointed out, light down wash and imperfections don’t go well together.