Mini-splits cause settling & cracking of drywall?

I am pretty committed to the idea of Mini Splits for various reasons I’ve read about on this site, but our contractor is putting up resistance, saying that we need to have heads in the bathrooms, otherwise temperature differentials will lead to settling and cracking of the drywall, which I have been completely unable to substantiate in online research. Is there any truth to this?
After a lot of combing through the various and highly-helpful articles on GBA; our design has evolved to a 2-story 25×45 box (2100 SF not counting unfinished basement) with R-30 walls (2″XPS + 2×6 walls with Icynene), and an R-40 roof (XPS-could go higher), with R15 on our unfinished basement walls. 17% Glazing/Wall ratio, 0.28 U-Factor windows, all large openings are shaded for summer shading, winter solar gain. These values exceed what I’ve been able to find on whatever Manual J sheets I have been able to find online (they only go up to R-25), but those give my home a heating load of around 36K BTU. The house spans in the 25′ direction, and the first floor is almost entirely open – 775SF of open, unwalled living/dining/kitchen space, open to another 100SF of office and corridor that is separated by walls, but no doors (42″x96″ openings to the rooms). Climate Zone 5 – in the Midwest.
In my mind, it works like this:
-All Bathrooms have electric radiant heat in the tile floors, are exhausted through an HRV, and provided with jumper ducts to adjacent bedrooms/corridors.
-The 875SF of open space on the first floor is heated by one 18K BTU MiniSplit Head, centrally located in the space. We will have a gas fireplace if it gets really cold.
-The second floor consists of 2 full baths, 2 bedrooms, and an open living space of around 400SF (that serves as a guest bedroom – there is a fair amount of north and east facing glazing in the space). Bedrooms get 6K BTU heads, open living space gets a 9K head.
I am thinking that what I have here is bordering on overkill as it is, but I’m an architect, not an HVAC contractor. Thoughts?
GBA Detail Library
A collection of one thousand construction details organized by climate and house part
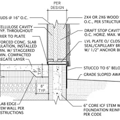
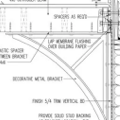
Replies
Joseph,
No, you don't need a minisplit head in your bathroom. What you need is a different HVAC contractor.
For heaven's sake, you even have electric resistance heat in your bathrooms already!
Drywall doesn't "settle." Drywall can crack, but only if your drywall contractor is incompetent or unaware of issues surrounding truss uplift. (There are easy ways to avoid truss uplift problems.)
You heating load estimate (36,000 Btu/h) sounds high to me, by the way.
That's what I thought. The contractor probably didn't realize that I was considering electric radiant, but is even that overkill? I thought it might be a nice luxury on those really cold days when jump ducts and air pulled through the HRV isn't enough, measured in the $100's of dollars and not the $1000's.
Thanks for confirming that I'm not crazy!
Joseph: For a comparison, In Maine, zone 6, we heat an area a bit bigger than your first floor space with a single Fujitsu 12RLS3 ductless minisplit. Our envelope is a little more robust than yours, with about U .12 windows and slightly higher insulation. The nominally smaller minisplits are a little more efficient, while their maximum heat output is almost the same. As far as i have been able to determine, the larger units have higher cooling outputs.
What stage of construction are you at now? Maximizing air tightness will yield significant benefit. Your 36K btu/hr heat load does seem high.
My wife is pleased we put heat in the bathroom floor.
Joseph,
Many people heat from a single source - be it a wood stove or ductless furnace. Many people also close off rooms during the winter. In my climate there is a risk of mold, but nowhere does the drywall crack.
We are still in pricing/design. I feel like our contractor is more experienced with typical forced-air systems, and would prefer that direction. We still have the opportunity to change our design to such an approach; however it is not without compromise. The open-concept first floor under a 24'-0" joist span makes finding large chases and duct runs perpendicular to the joists challenging. My sense is that for what we're doing, the cost for added bulkheads, lost floor space, and a possible need to raise the entire roof deck to keep our bulkheads higher than 7'-0" AFF on the second floor are going to offset any savings we would get with a forced air approach.
+1 on the notion that 36,000 BTU/hr is a very high Manual-J for 2100' of above grade house in zone 5A with that type of construction. That's 17 BTU/hr per square foot of conditioned space, a higher load ratio than my 1920s vintage sub-code 2400' house , not counting the 1500' of not directly conditioned insulated basement has at 0F outdoor temps, as measured by heating fuel use, not just a Manual-J. Most IRC 2012 code min houses under 12 BTU/ft^-hr, many under 10, and by it's description this house is better than code. Reality is probably less than 20,000 BTU/hr unless there are some serious design errors.
The ways that a 36K load calculation COULD be that high is if it has an excessive amount of window area, or if it was using a high and unrealistic number for air leakage. Glazing ratios typical of new homes run about 15% window to FLOOR ratio, (not window/wall area.)
If your design loads for those bedrooms aren't at least 4000 BTU/hr it's likely that the half-ton heads would be cycling more of the time rather than modulating, which has a toll on both comfort and efficiency. If the design load for the whole house is under 20,000 BTU/hr (and I think it is), you might even be cycling the compressor whenever it's above freezing, which will take a toll on efficiency too. It's important to drill down on the heat load numbers and get to know what the loads really are. Sometimes it's possible to split the output of a mini-duct head between 2-4 adjacent rooms to keep it modulating, but there are trade-offs. No matter what their HSPF bench tests say, a mini-duct cassette that's modulating all the time will be more efficient than a ductless wall coil that's cycling on/off most of the time.
Your walls are not R30, but rather R20 cavity + R10 continuous. With most siding types that would have a whole-wall R of about R25, or a U-factor of about U0.040. A code min wall under IRC 2012 is specified at U0.057 (maximum)., so your wall losses are about 30% less than a code-min house, which is quite a chunk off the heat load.
A continuous R40 foam roof + roof deck + ceiling gypsum + composite shingle layup would have a U-factor of about U0.023. Code-max is U0.026, so you are 10-12% better than code there too.
If you can swap the XPS specified in the walls and roof for polyisocyanurate inch-for-inch you'd be doing the climate a favor. XPS is blown with HFC134a (automotive AC refrigeratant), which has a high global warming potential (~1400x C02). Polyiso is blown with pentane (7x CO2), and while it's mid-winter performance won't hit it's labeled performance, it'll still be comparable inch-for-inch with XPS in your stackups. As XPS loses it's blowing agent it's performance drops about 15% over several decades, and will eventually underperform polyiso even at the mid-winter averages.
If your heat loads are as low as I think they are it's probably a 2 separate mini-split solution: A properly sized wall coil for the open space first floor (probably a 1 ton or 1.25 tonner) and a dedicated mini-duct cassette mini-split (not a multi-split) mounted in a ceiling service chase to handle the doored-off bedrooms upstairs, provided you can find competent mini-duct designers/installers. If need be, Fujitsu has some 7K mini-duct cassettes that could be used to cover a pair of rooms at a time, with a mult-split approach to the second floor, but a 6K head per room for a design heat load that's probably on the order 2000 BTU/hr or less is just silly (yet all too common.)
Thanks for the detailed response, Dana. The online Manual J calculator I used did not allow me to go above R19+6 for walls or above R-38 for the roof. In terms of window to floor ratio, we are probably closer to 25%, which will probably drop down to 23% when all is said and done; but we love our daylight, and most of the windows are operable for cross-ventilation. First floor is 10'-0" ceilings,second floor is 8'-0".
I am still leaning towards two wall-mounted cassettes on the second floor, one serving the 330 SF of the master suite (bed, bath, closet, exterior walls on 3 sides of the suite) and another serving the other 550 (bed,bath,open living space). I prefer this largely for ceiling height, as there is no attic, and the roof joists are set at 8'-0".
I suppose that if our little one's bedroom is cold or hot, we could add a baseboard heater or a ceiling fan after the fact, which would probably only be necessary in extreme weather.
With a 23% glazing/floor ratio you'll need window performance higher than U0.28 to keep the heat loads bounded. A single square foot of U0.28 window is as much heat loss as nearly six square feet of U0.040wall. So if 17% of the gross wall area is window literally half the heat loss of the gross wall area is through the windows.
U-0.20 triple panes would be a real comfort factor on the colder days- large windows with higher U-factors will have cascades of cold air falling creating a draft, and the radiant loss out the window is something you can feel from five feet away.
With the stated limitations the online Manual-J you used is next to useless. Run an I=B=R spreadsheet model using the above mentioned U-factors for wall & roof instead.
In a well insulated house like you plan, it isn't really necessary to supply heat to every room. But it's sometimes hard to convince people of that truth. Ducted minisplits are a better solution than putting oversized minisplits in each room. Another solution is an air-to-water heat pump, such as the Chiltrix, which can then be combined with small fan-coil units that are like minisplit heads. Martin had a good blog post about them recently. One nice thing about them is that if you need a very small amount of heat in a room, you can provide it with a small panel radiator, or tubing in the floor. So if you, or your code official, or your HVAC contractor, decides you need heat in a small space, you can do it with minimal added cost per added heat emitter.
It's not necessarily an ideal solution because you need an HVAC contractor who is willing to learn to install a new type of system--someone with commercial experience would be more likely to have worked with something similar.