Modified Flash and Batt in Dallas, TX (zone 3)

I’m considering what I would call a “modified” flash and batt using 1″ or 1.5″ of polyiso cut to fit between the studs on my house rather than spray foam, and then sealing the edges of the polyiso with canned spray foam. On top of that I would then add the unfaced fiberglass batts. The sheetrock is already down due to other renovation work taking place, and I’d like to cut down on the electric bill, particularly in the summer. everything I’ve read an research on DIY sprayfoam makes it sound pretty aweful to deal with, plus it’s about $1/ board ft (if their projections are accurate) vs ~ $.50 board ft for polyiso.
Anyone see any problems with this beyond it being a lot of work? (moisture is obviously the main worry)
Thanks for your comments and assistance.
GBA Detail Library
A collection of one thousand construction details organized by climate and house part
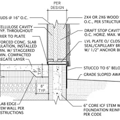
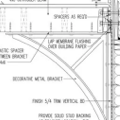
Replies
In some ways, using board is better than spray because the resulting surface will be nice and flat. You will also get a consistent thickness.
I'm in a heating climate and not much familiar with the specific issues in hot/humid areas, but it might be that you want 2" of foam, or more. You do not want the exterior surface of the foam getting to dewpoint temperature (when the a/c is on) and becoming a condensing surface for exterior moisture when it's hot/humid out. Someone who is familiar with your climate and insulation strategies should comment on that.
What is the wall thickness? What is the sheathing, weather-resistive barrier, siding, etc?
Thanks David,
Here's my entire plan/ set up:
The house was built in 1961 and is a typical Brick home with a brick veneer and sheathing that states "water repellent gypsum with sheathing complying with ASTM specification C 79- 50" inside of that I have 2x4 walls with about 1.5" of rockwool batt.
I'm planning to do what I mention above and either add it all in the 3.5" provided by the 2x4 space, OR more likely, I will add a wall of 2x3s (2.5" deep) on the inside of the existing wall and space it 1/2" from the exisitng 2x4 wall to create a thermal break. That 1/2" gap might be filled with a thin stip of 1/2" polyiso, but I may ditch that idea. That would create a total wall thickness of 6.5"
Brick veneer, eh? Hopefully this will elicit some further, knowledgeable commentary. It may be that up to now, your building has depended on drying to the interior, i.e. the brick takes on a certain amount of water during the year, and some of that escapes into the house as vapor. If you put a low-perm insulation like foam into the wall you will inhibit that vapor movement. I believe there is a Building Science Corporation paper on insulating brick buildings, and regardless there is plenty of reading out there... maybe even something already here at GBA.