Mold?

Hello,
This is my first post. I (perhaps unwisely) decided to do my own finishing on my house. The house was 2×6 framed, housewrapped, sided (in vinyl) before this past winter winter. I’m in central Wisconsin. I had the furnace (direct vent) installed and began heating the house since the winter started. I started doing the insulation about the same time along with other finish work. I have a simple 2 level rectangular home including poured cement basement foundation. I don’t have drywall on the walls yet. And I don’t have plastic (vapor) barrier on the inside of the 2×6 walls. I had the upstairs ceiling drywall put on before winter set in and got R60 blown-in cellulose. I started heating about that time. I’m only heating the main level and basement to about 57F. The upper level also has a furnace but it isn’t running. It’s probably about the same temperature upstairs due to air movement from below.
Apparently I thought it was ok to put the “lid” on the house and insulate with some heat going in the house before getting plastic on the 2×6 studs.
I recently pulled back the main level insulation just to check behind and noticed that the main level north facing exterior walls seemed a little damp but appear fine otherwise. The main level, east, west, south exterior walls seemed dry enough. I hadn’t really checked the upper level walls, expecting to see basically the same thing. But when I mentioned to my framer/contractor the main level dampness he mentioned it might be good to pull back the insulation and let the walls dry and then put the insulation back up and then the plastic vapor barrier. I had only seen the main level dampness at that point and mentioned it to him in passing. So I hadn’t pulled the upstairs insulation back until today. So today on the north facing walls I noticed what is in the attached pics. What is this? Is this mold? And what are my next steps here? I sent the picture to the framer/contractor today as well and he said to pull the insulation and let it dry. Is that all or do I have a major mold problem that a mold pro needs to deal with?
I’m beside myself here. Have I made a massive mistake not getting the plastic up sooner? Or do I just proceed by letting it dry and putting the insulation back up? Or do I need to get new insulation? I’m tempted to just spray foam now instead of putting that insulation back…. Not sure really what to do. Or maybe I’m worried about something that will go away like the framer/contractor mentions when it dries out.
I can provide any other info I may have missed and I really appreciate the wisdom of this board. Sorry it’s so long! 🙂
Jeff
GBA Detail Library
A collection of one thousand construction details organized by climate and house part
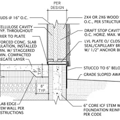
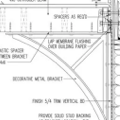
Replies
Looks like mold, especially the block spots.
What did you use for insulation? Fiberglass batts? If you used facer fiberglass batts, the paper facer is a vapor retarder. Putting up poly may not be a good idea though. I’m also a little surprised you have enough moisture in the air to have any real problems since I assume you’re not running a humidifier if you’re not even done with construction yet.
Bill
The moisture from your foundation is quite significant for a time and the surface of the OSB is cold (a condensing surface). The OSB is organic enough to support the growth of some mold the way it looks. A bit of 1/2 bleach and water on those mold spots will take care of it in my opinion.
I have worked with Mac Pierce here in MN on several mold cases and as a foremost expert he says we somewhat overblow mold. We should be aware of it, remediate it and our building assemblies should be mold free if done properly. Dry ice is used sometimes as a removal mechanism in kind of a sandblast procedure when water would create a mess. Bleach and water is a killer of mold, have good ventilation and gloves when using ( guaranteed runny nose). Mold out side of the living space separated by a barrier is generally not a health hazard but should be considered.
Yours is very minor mold from the photos and you have attached, you have been given an opportunity to think about your final exterior wall detail. I use and have used warm side polyethylene sheathing in a cold climate and I believe in it. If your code calls for it and you have a fear of near zero perm go with one of the variable perm barriers available to us today. Most all wall systems will handle a slight bit of moisture migration from warm to cold as there is some dissipation through the sheathing and top plates.
Most all new housing in the last many years here in MN has been poly, fiberglass batts, OSB and housewrap. Not the optimum wall for a number of reasons but wholesale mold has not been observed. Most builders do quite a good job of a continuous warm side air barrier however.
>”OSB is organic enough”
I have to comment on this. This statement is meaningless. “Organic” in the chemical world means “carbon-based”, period. Wood is organic, regardless of how it’s been processed. Gasoline and plastics are also comprised of organic molecules (carbon chains). Inorganic things would include steel and glass. Plastics are organic materials.
Some have noticed that the more processed the wood product, the more mold seems to like to grow on it. That would mean OSB is most likely to grow mold, then plywood, and regular milled framing lumber last. In my own experience, I don’t think mold particularly cares what kind of wood it grows on, but plywood and OSB tend to be used as exterior sheathing materials so they’re colder, thus more likely to have condensation form on them, which gives the mold the moisture it needs to grow (the wood is the food).
Bill
Luedtke do that?
You need to dry it now.
I build in central WI, your dew point profile without the poly is going to condense on the inner surface of sheathing like crazy based on outdoor temps and construction humidity and you firing heat. There is so much moisture in a fall winter build you should be dehumidifying constantly and if you don't, and/ or you don't have the poly up you’re experiencing the consequences.
Bill is flat wrong, it’s not the sheathings fault, it is your indoor conditions, and paper faced batts in our climate is not an effective vapor retarder, lets be honest about that. We are on the edge of poly being a friend or foe in central WI, generally as you should be finding out it is our friend. There is a lot at play, but there is nothing wrong now or ever with your wall assembly when things are in sequence.
Dry it out and sterilize.
Im speaking not from building and walking away but ripping mistakes apart and seeing results of actions.
>”Bill is flat wrong, it’s not the sheathings fault, it is your indoor conditions, and paper faced batts in our climate is not an effective vapor retarder, lets be honest about that.”
I didn’t blame the sheathing, and I agree it would be the indoor conditions at fault. I’m just surprised there was enough of an issue for mold to grow so quickly.
The paper facing IS a vapor retarder in all climate zones, but how effective it will be here may vary. That was mostly just a question about how the wall was put together. Obviously whatever is in that wall is allowing the conditions within the assembly to allow mold to grow.
You can (and probably should) mist that mold with a bleach or peroxide solution to kill it. If you leave it as is you’ll likely get more.
Bill
Hello and first of all, thank you so much for your reply! Ive read on this forum in the past and really appreciate all the great information.
Unfortunately, I’m the one to blame for this. I had thought I’d be much, much further along by now. I did not anticipate things going as slow as they did on my end. And I had been keeping an eye on the OSB, except upstairs :-(. I just didn’t anticipate such issues. The cold weather building process urgency really escaped me. So no, it’s all self inflicted ;-)
I will read the article Martin linked. I must have missed that in reading quite a while back. But to your points.
Do you recommend the steps in this order:
1.Pull and throw away insulation
2.rent a dehumidifier. I see sunbelt has one that’s around 385cfm for $1k for a month
3. Clean/sterilize mold
4. Insulate
5. Poly
6. Drywall
Or should I perhaps (and maybe this sounds completely wrong) skip the dehumidifier phase and proceed from 1-6 (skipping 2) as quick as possible.... this time with others doing the work so it gets done fast. I know there’ll be plenty of moisture again during mudding.
If you recommend dehumidifying, how long before re-insulating and what kind/size? We are 32x50. Basement, first and second floor.
Again, thank you so much for the wisdom.
Best,
Jeff
Jeff,
I wrote an article addressing this topic. Here's the link: "Condensation on Wall Sheathing During Construction."
Thank you, Martin! I read your article and really appreciate you sending that link. With the help of that and other comments on this board I feel like I have a path forward which is exactly why I posted here.
I know your article mentioned 6 cases. And although I would consider it a badge of honor to be inducted by you as a 7th, I will refrain from advocating for that. ;-).
Joking aside, I hope this thread and others like it continues to be a service to others. I really appreciate the help!
All the best,
Jeff
I’d switch steps 1 and 2. Get the humidity down first; then proceed with the next steps. You don’t want to seal in the mold without a cleaning step, that’s asking for trouble down the road. It’s also recommended to encapsulate moldy surfaces after cleaning when possible. There are anti-mold primers you can use for that here. A quick application here would probably be a good idea for some belt and suspenders protection.
I would try to get the steps done quickly once you get started. Construction does always tend to be behind schedule, that’s just life, but for anything where weathering is a concern, plan for more time than you expect it to take. I’ll mention that I have some walls in similar state to yours right now (open inside, just mineral batts installed), but it’s a Reno project and I’ve been intentionally keeping the humidity low until I’m done. I also have 1/2” polyiso on the exterior and no wood sheathing directly under the mineral wool, so I haven’t had any mold issues.
BTW, good to see a post from you Martin. Long time no see :-)
Bill
Thank you so much, dehumidifying it is. Do you think a standard 40-50 pint home dehumidifier starting in the basement could do the job? Or am I going to need the bigger $$$ >1k units for this? Perhaps something I should rent? I’m sure a costlier/bigger unit would work faster. Just trying to gauge a balance between what’s “nice to have” vs “will do the job”. And maybe the smaller unit just can’t keep up. I don’t know. There is no moisture on the windows at this point. Thanks, again, for the helpful feedback!
You’ll probably need the bigger unit. You could try taking some measurements first to be sure. If you already own the smaller unit hook it up and see what happens. If you don’t see humidity levels drop after a day or two of running, then you know you need the bigger unit.
Bill
If you monitor inside and outdoor dew points, you can often use ventilation for dehumidification this time of the year.