Need advice on proper vapor barrier and capillary break placement

One of the requirements for certification under the NAHB Green Standard is to install a vapor barrier (in direct contact with the slab) and capillary break (min 4″ thick 1/2″ aggregate) somewhere beneath it. I don’t know about the rest of the country, but in my market (Oklahoma City) I would guess that 80%-90% of the slabs here do not have a vapor barrier and I’m not aware of any that have an aggregate capillary break so I don’t have a good local knowledge base of how to accomplish this.
In my research there seem to be many different schools of thought on how to layer everything and there seem to be good arguments for all theories. I would like to know from people with extensive practical experience rather than theories as to what works best. There have been scientific studies showing that concrete with higher water to concrete ratios (typical of the building industry) placed over sand is 30% stronger than concrete placed over plastic because the sand will effectively lower the water to concrete (w/c) ratio. Another study in the same article suggests that the sand decreases the strength of the concrete because it leeches water away necessary for proper curing of the slab so it should be poured directly on the vapor barrier. Here’s the link to that article by the way:
I realize proper finishing techniques and proper water to cement ratios are important, but difficult to make happen all the time. I’m looking for ideas for best practices to mitigate problems like cracking, curling, strength, etc.
My conclusion so far is to place 4″ of clean 1/2″ aggregate on the grade and then top it with 8″-12″ of fill sand (depending on my stem wall height). Next I would top it off with a 6 mil or better plastic and place the concrete on the plastic. I thought I might possibly spray a retarder on top to slow down the evaporation and reduce cracking. I would have to specify a water to concrete ratio as close to .5 as I could and try to get my contractors to place it. I have big slabs, some in excess of 5,000 s.f. so spreading low slump concrete could be an issue. I appreciate anyone’s comments and suggestions.
GBA Detail Library
A collection of one thousand construction details organized by climate and house part
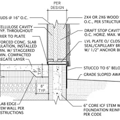
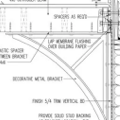
Replies
we use asphalt foundation damp-proofing painted on the footings as soon as the points are set for a capillary break. When we pull strings between the points for our perimeter lay-out they show up well on the tar but we don't run into the water wicking under the break that we have had in the past when we used poly under ICFs as a break.
I use washed stone only, no sand, under slabs then two layers of foam with offset joints and then the six mil poly directly under the concrete. Instead of trying to talk your finisher into using low-slump concrete just have the plant add super-plasticizer to the mix. Makes dry concrete act like it's been all watered down.
For pigment, give shake-on color hardener a try. it only goes on the very top layer, scattered on dry after the concrete is first floated and troweled in with the first bleed water. I like it because if I'm ordering mix-in color i don't get any variation over the slab and I can't risk ordering too little concrete and needing to call in a make-up order so my order has to be spot on (which I seem to have issues with) and that acid stain needs to wait 28 days to go on by which time I have the doors set and ready to insulate and the acid really eats stuff up if you don't mask it all off.
James,
I find it fascinating that such a high percentage of Oklahoma slabs lack a poly vapor barrier or crushed stone. Sand is unnecessary (and in some cases, counterproductive). Just be sure that the 6 mil poly is directly under the concrete.
According to the Portland Cement Association, http://www.cement.org/index.asp, you need to install a vapor barrier under your concrete and above your capillary break. They sell a great book I bought a while back, “Concrete Floors on Ground”, which is really helpful in teaching you how to properly design a good concrete slabs or basements.
The American Concrete institute has a paper called “Guide for Concrete Floor and Slab Construction”, http://www.concrete.org/General/f302.1(04)Chap3.pdf, where in Chapter 3 it tells you how to design a slab properly as well.
If you are using wood, carpet or vinyl floorings, or control temperature and humidity indoor rooms, you should install a VB. The aggregate and the VB work together to prevent ground moisture from wicking though the slab. You don’t need the sand you are using now. The VB under the slab allows the moisture to stay longer for the concrete to cure correctly. Also, if you where in an area of radon gases (not OKC) you would use the capillary break to install a 3” socked drain tile tied to a PVC stack for passive off gassing.
To minimize cracking, install 3,500 PSI concrete with fiberglass at a slump 4-5, never higher. If it’s too dry, hot, windy or large use plasticizers or split the slab in two pours. Always use controlled joints and/or score you concrete and cover your new slab while it dries for the first 2-3 days. Double reinforce all your inside corners, as they are all weak points for slabs to crack.
I should have added to start your pour as late in the day as you can and still allow time to finish; that way your concrete will set better at night than in the sunny hours of the afternoon. Of course you have to convince your contractor to do it.
James:
I’m in Houston and I too worry when we place concrete on a large job on a 100 degree day, some of my slabs are in the 5-6000 sq ft too. Regarding a vapor barrier, I noticed your link was with Stego Industries, they make a 15 ml vapor barrier, called Stego Wrap. I’ve used it before.
http://www.stegoindustries.com/photo_gallery/
No matter what you will get some hairline cracking as the concrete dries. I watch water content and slump carefully during the placement. The best thing I have every used is something called cotton curing pads, which are basically large blankets totally covering the slab, placed immediately as soon as you remove the trowling machine. You wet these blankets and spread them out on the slab, and add more water to them, soaking them thoroughly. They keep the slab wet continuously for several days, which slows the drying and curing process. In 100 degree weather water is removed too quickly, causing excessive cracking. The worst thing you can do is wet the slab, let it dry, re-wet it, let it dry, repeating this over and over. It must be kept wet for several (5-7) days in really hot weather, I’ve found these cotton curing pads the best thing to use.
The wetter you can keep the slab, slowing the curing process, the concrete will test out higher in strength in 28 days.
James,
Blotter sand under slabs is always a bad idea. I wrote an article for EDU on the topic ("Blotter Sand Woes") years ago.
Building Science Corp. has an online article on the topic -- explaining all of the disasters that can occur when builders have sand instead of poly under their slabs:
http://www.buildingscience.com/documents/insights/bsi-003-concrete-floor-problems/
Michael Chandler has described the correct procedure and I agree with Armando to provide the radon loop. A basement floor or slab on grade can be a huge year round indoor humidity source if it is not isolated from the subsoil. You will be amazed at the comfort and dryness of the concrete floor if you use 1/2 to 3/4" aggregate topped with foam and poly under the slab. Some of the extruded foams have a higher density and are more rigid, avoid "scoreboard" under slabs. I also like to include a foam thermal break between the slab and foundation.
I don't have field experience with this application bu is anyone concerning with damage to the 6 mil poly vapor barrier if placed directly over rock? I imagine that the pressure of the concrete would puncture the poly being pressed onto the rock. I'm in a cold climate where typically the poly is laid on rigid foam. Not familiar enough with the Oklahoma climate to know if rigid foam under the slab is beneficial.
J,
Dr Joe speaks of this issue here:
https://www.greenbuildingadvisor.com/blogs/dept/building-science/air-barrier-or-vapor-barrier-building-science-podcast
Great comments fellas! You're helping a bunch.
John, The podcast by Dr. Joe was an excellent explanation of moisture travel. Now I'm not worried about placing the plastic on top of the gravel.
Martin, I've built hundreds of homes over the last 15 years, but have only been building high performance green homes for about 2 years now. I'm amazed at how little I knew about building science and amazed at how many builders (at least in my market) don't understand it. I think I've only scratched the surface in my knowledge. In spite of that fact, I've had very few problems with my homes from moisture, etc (probably because they were somewhat leaky). I feel much better about the product I'm putting out now. I believe I read the article you mentioned. Here's the link: http://www.buildingscience.com/documents/insights/bsi-003-concrete-floor-problems
Armando. Sounds like you know your concrete. I'm a little concerned about the added cost of the plasticisers, fibermesh, etc. I build 100% spec homes and am in a price sensitive market. I'll figure out a way to do it and do it right. How do you reinforce your corners? Also how do you cover your slab while it's drying out? Allen describes the use of cotton curing pads above. How about plastic or tarps?
James,
First thing I’ll do is to have a soils test to tell me what kind of foundation, concrete or reinforcement etc. to use. I’m from OSU and lived in Stillwater, Enid, Ames and Okeene and if I recall many of those soils were expansive, I don’t know much about OKC soils. Now, in NORMAN it’s all bad, specially OU!!! :-)))
Assuming you have good soils, either rebar or wire mesh should be ok. To cover the concrete with tarps or plastic is ok too. I must admit Allen’s suggestion sounds great, but I have not use or spec. that product. I going to check it out myself.
J,
Any type of VB over aggregate may suffer some tear, also when workers are pulling up the wire mesh or rebar or walk on as they pour concrete, but you try to minimize holes and at the end you should have pretty dissent coverage.
Also, as Doug mentions, having the entire slab under rigid foam is great, but that depends on your climate zone, how much energy you want to save, how green your project needs to be. In CZ4 even a 24" or 48" continues rigid insulation under the slab makes a huge difference in your HERS rating.
The cost of plasticizers or fibers are relative to the cost of installing stronger concrete with fewer cracks, which can be just cosmetic cracks, but to the homeowner it could mean uncomfortable questions. You could think as PR cost. Many concrete subs add water so its easier to install and have time to finish, unaware they have reduced the strength of your concrete… weaker concrete means more cracks or more serious problems.
Our soils are expansive. We do soils testing on every house I build, 2-3 bores 20'-30' deep. From that the engineer designs the foundation. All of my homes have drilled piers, usually 12"-16" shafts with 36" -48" bells, 10'-15' deep. Approx 80-100 per house. Grade beams are usually 12" w x 30" deep, with 6 #5 rebar, the slab floor is 5' of concrete with #3 rebar criss-crossed on 12" centers.
For a really super-duper designed foundation, we place "carton forms" (basically cardboard boxes) under the concrete before placement, to create a void whereby the foundation is 100% independent from the soil except for the drilled piers.
The main thing in watering a foundation in high heat is to keep it wet 100% of the time, using water hoses and sprinklers do not work well. The cotton curing pads are the best thing I've used, I've heard of using straw also.
We also do concrete cylinder testing on the job for every 50 yards (typical slab is 300 yards), to verify slump. I watch closely that water is not added excessively by the finishers, which they tend to do. The water weakens the strength of the concrete.
The last I heard was extruded or XPS was another name for "scoreboard"
http://www.constructionmaterialsinc.com/catalog_data/DIVISION7/Styrofoam%20Insulation%20Board/Polystyrene%20Insulation/Dow%20Styrofoam%20Scoreboard.pdf
Scoreboard is scored for easy size reduction in the field but the scored lines in the 4 x 8 sheets will spit under the weight of a wheelbarrow or just by stepping on it. Unscored 2" extruded polystyrene is available but you have to look hard to find it. CertiFoam will make it to order in bundles of 6 sheets.
Always interesting to hear what others do in their area. Residential builders in my area rarely do any soil testing, we build with full basements mostly, slabs are used in low cost housing like cheap townhouses and condos, and until lately many poured foundations had not a foot of rebar.
Changes are here now though. I do get offered rebar in foundation bids, and personally have turned down projects when customers would not have soils tested. I have no interest in dealing with a failed build.
Very informative thread, glad all of you have posted. I like the pasiticizer hint and will be calling the ready mix plant for availabiltiy and pricing.
That's true, I never thought about it that way. I've never been involved with a project where the whole slab had it installed underneath it. Thanks for pointing that out.
Forget a sand blotter layer, this will trap moisture which will eventually migrate through the concrete and may affect your floor covering. Regarding the vapor barrier, DO NOT USE PLAIN 6 MIL POLY! Any recycled poly film will degrade overtime , even when not exposed to UV. These products are produced using post consumer recycled plastic. While it's good recycle, this is not a place you want a recycled product!
I will also state emphatically to never install a sand blotter (read that water reservoir) in contact with a slab. That's a recipe for moisture problems.
Also, never allow a contractor to water down the concrete in placement. It should be placed exactly as ordered with no more than 4" slump. If they insist on a more workable mix, then add plasticizers or water reducers at the batch plant.
As another just said, never use a conventional 6 mil poly under a slab. It come with pinholes and will tear on stone or by rebar, mesh or walking during the pour. There are several tear-resistant vapor barriers on the market made specifically for subslab application. I use Tu-Tuf reinforced 4 mil for this purpose, but I also install it between the aggregate and the XPS insulation.
It matters little, in terms of moisture management or concrete curing if the vapor barrier is below or above the foam board, particularly if the foam board is T&G with taped seams. This allows the foam to act as a secondary moisture barrier and the tape keeps the foam sheets from separating and cracking. Protecting the VP with the foam board, prevents tearing from rebar ties and the brutes who place the slab.
I always install a radon vent in the subslab aggregate. It's the cheapest insurance for a healthy home, and 95% of radon problems are mitigated with a simple passive through-the-roof vent.
With well-compacted sub-slab fill on stable, well-drained soils, there's actually no need for rebar or mesh, which rarely gets place in the center of slab height where it belongs. It's primary purpose is to prevent shrinkage or settling cracks from opening. To prevent surface drying cracks, use fiber mesh in the mix (it should be short-fiber polyester not fiberglass which fuzzes when power-troweled), and prevent rapid drying of the surface either by pads or plastic or old-fashioned straw or a sprinkler or a curing sealer applied immediately after power-troweling (which is best for colored concrete).