New Build seeking variety of comments- mech and insul mostly.

Hi.
I know this is all over the place but I wanted to put the whole package out there and see what everyone has to say. I have enjoyed reading the discourse of others here and on other sites… and would love to print and take to architect meeting next week. Let’s see what everyone has to say.
background: new to be built house is a replacement for beach cottage destroyed by Super-storm Sandy. 100yards off beach – not directly water or beach front. old house was 1056 ft2 cottage and the replacement is double sized (adding a second floor). elevated 11 feet above grade. House will be on stilts of tbd quantity and arrangement (pending final sheer wall and deadweight loads currently with structural engineer, etc). we are not in the impact zone and don’t require hurricane glass.
foot print is not negotiable (zoning) neither is height or elevation. 24×44 rectangular box with small front porch (6′) and larger (20′) rear deck.
likely use of metal roof and fiber cement siding for durability and ease of maintenance close to water (also included is stainless and double dipped fasteners, etc). full use of hurricane strapping on each stud, etc. wrapping deck and porch studs with grace vycor — same for sill beams house will actually sit upon. imagine a 1,000 ft deck up on 12′ stilts… and then build a house on top of that. strap like crazy and put on the waders if the water comes that high ever again (we’ll be approximately 6 feet higher than Sandy; if that is not enough, there will be no coastline left!!)
location is central CT shore line (not far from New Haven) zone 5. odd mix of hot in summer, humid and cold winters. best of all zones combined. just not many 100 degree Phoenix days — house positioned nearly perfectly on east west access with north wall less than 3 or 4 o off true north, but solar not an option – a. cost not necessarily a great return but more importantly, the roof is 35′ in the air exposed to the ocean and we are close enough to the 110/130mph line that I don’t want anything on the roof – other then a supremely well fastened forever metal roof with no possible chance of leakage (still trying to figure out how to vent plumbing without piercing the roof (same for wood stove chimney). nobody was willing to guarantee both the roof and pv structure for more than the 10 year calculated payback. Worse metrics (even with the tax breaks!) for geo thermal (and the well does not have to go very far down to hit water. that’s for sure.
current plan is for:
advanced framing, 2×6 walls, 24″: OC – with rockwool batts interior and 3/4 ply walls inside (no gyp; we are nailing bead-board to the plywood for an old cottage look). no inward vapor barrier to allow for inward dry. or possibly use 475’s Intello plus or just tape ply seams before installing the bead-board. still working on the vapor management plan.
seal and tape all electric boxes, etc.
windows (and all doors) are marvin lowE 2 pane fiberglass (close to ocean durability key – willing to trade slightly more inefficient double-hung for longevity over not having casement cranks or awning hinges which will surely fail in my lifetime, etc.) integrity windows double flashed with sill pan extra on the ocean side only. admit, weakest point on the wall structure is the windows – hence wasted time on double studs, etc, just does not seem worthwhile especially considering the amount of glass in a beach house. longer fake (outside the building envelope seal) eave on second floor and artificial solar block (aka the ugly trellis looking thingy attached to the wall above the widows) between first and second will provide passive solar shades in summer yet allow sun to shine in winter.
external fiber gyp wall sheathing (1/2 or 5/8) glued and screwed and then taped. Hunter Xci (Poliscio) with 3/4 ply external to the fiber gyp sheathing with 2″ foam inboard of the plywood. Screwed to studs (holds the polyiso and plywood up with one step and provides 3/4 nail surface for fiber cement fastening – way better than ZipR’s 5/8″ osb to nail fiber cement to (both hardi and certainteed require/prefer 3/4 structure to attach to). plus more polyiso than ZipR for about same money — yes, labor to install fiber gyp and then the foam and ply, but the second step is a one step process. not three. (two inches of foam and one ply nail board installed in one steep). approximate r value of 24 from batts, 12 from polyiso and very limited bridging because of the CI and 2 layer of sheathing. Likely a true R30ish wall. (albeit with a bunch of R2 windows scattered around 🙁
total wall thickness approximately 10 true inches. (3/4 pine, 3/4 ply, 5 1/2″ studs, 5/8″ fiber gyp, 2″ polyiso, 3/4 ply + fiber cement.
I’d love to do 2″ of rockwool (good rain screen, etc) which might be better/greener than the polyiso bonded to the ply, but i would have to install it and then install the wood over. two steps.. Hunter xci saves a step. might be worth it. working with the builder on this one. also, how does even the densest rockwool hold up (vertical drag – settling) between the sheatings..? the polyiso surely wont give or droop. don’t think the rock wool will either. but just asking.
have not done the price comparison on this yet. did hunter vs zip and hunter/zip versus no CI (bad idea). so, if we go this route, it would be fiber gyp, rockwool, plywood on the outside.. with the rockwool esentially a 2″ drainage plane. (best attribute yet!)
Rain barrier (Grace or Solotex mento 1000) outside the plywood and then the fiber cement screwed and/or nailed to the plywood. Not sure if we’ll have the foil face on the polyiso over the fiber gyp… or another vapor permeable layer there…
10 foot tall ceilings with fans provide airy and light in summer. reversible on low in the winter pushes heat back down. vaulted tall ceilings on second floor master, too. same process – fan up in summer, down in winter.
first floor small wood stove (more for romanticism.. and backup heat, but designed to face the stair well up to the second floor and it will provide heat and fun Saturday night glow when desired. nearby independent make up air provided.. not sure if it will be conditioned or not. likely not.
hydronic radiant in floor heat on both floors. 2 multi-loop zones per floor. routed into ply sub floor, 3/4″ pine TG flooring laid over pex which was not installed under sub-floor with diffusers/shields (keeps hot pex tubes as close to feet as possible).
Hot water provided by Takagi direct vent likely located in the egress stairwell — unit will almost be on outside of conditioned space.. also provides domestic water supply. depending upon final heat loads, two might be ganged together, but it looks like with only 2 occupants that one unit will suffice with sufficient BTU capacity to feed both heat and water. short runs to both bathroom and the kitchen. small domestic 3/8″ pex tubes and insulated all hot water pipes (see recent comments about saving heat loss on domestic water designs). all heat system also insulated to the floor sections… from supply unit to the wood sub floor to help save heat.
non-vented “HOT” cathedral ceiling on second floor. 10-12″ rafters filled with closed cell foam again with plywood and beadboard inside… studs externally covered with 1/2′ ply sheathing and 2 (or 3 tbd?) layers of 2″ polyiso foam. another layer of 3/4 ply for nailing surface covered double layer (over and under) Grace at the flashing. single layer elsewhere. Rhino UDL50 synthetic felt (light grey/almost white to shield the heat from/under the metal roof). standing seam metal roof. approx R of the sprayed foam is 55-60 and the external is supposed to be 1/3 of that.. or 20 which the 4″ would suffice… thinks we’ll wind up with 8″ foam blown in and the 4″ on top of the sheathing is close to true R-72 again with little thermal bridging waste. mid 60’s ? bitch will be how long the screws will need to be if we do a third layer of 2″ foam.. 3/4 ply, 6″ foam, 5/8 or 1/2 ply and then into the studs… damn! Nine Inch Nails, anyone? ouch. more likely 10″ nails… is one reason to stick with 4″ of layer foam outside the sheathing. and the code wants to go to half outside? how the #ell do you fasten all that foam board? 3 1/2 to 4/12 roof, by the way. (final design might flatten from 4 down to 3 1/2 based upon the height restrictions and the amount of external foam, etc. if we lose a few too many inches, we’ll squat out the design just a wee bit. but not below 3/12.
ridge beam construction set up on side walls – mostly shed dormer but not truss system.
Panasonic whisper hrv in each of two full bathrooms. with timer and auto sensor on. approx cost of $125 each is too good to pass up. The fresh air exchange available by Panasonic is only mini HRV available?? can run at 20cfm or 10 even when not occupied. problem with the Panasonic is it is exhaust only at 20o outside temp and lower efficiency from there to 45. (BIG downfall — but the big HRV will be operational in the winter.. so not as big a deal as it could be).
Alternative is the Lunos mini hrv from foursevenfive.com they run all the time… with a boost override for the time shower is actually in use, if I can get over the price, I think this is a great option. Not likely to use for whole house, though. no concern over external temp as it self defrosts each 70 second cycle. another vote for Lunos. 2 x $125 for Panasonic.. and some ducting etc . versus $1200 all in for the Lunos… not that much more to get what seems like a better unit. price is closer than it seems… might be a better idea.. given the panasonic freezes up when it is cold out for what would amount to probably more than 100 days a year – Thanksgiving to April 1 it can easily be under 20 degrees at night. starting to talk the Lunos back into first place…
Additional Fantech mini HRV in insulated inside the conditioned roof/attic crawl space. fresh air into the two bedrooms and evacuate air from first floor – results in convection flow of air in tightly sealed winter house. likely not used in summer (hence Panasonic hrv or Lunos in bathrooms which will stay on/available all year). Fantech is less than $600 for the HRV unit and some short ducting, even add a filter or hepa inline without ruining the heat/cooling bank. we get ASHre satisfied bath (Lunos at 20 constant meets ashre) and in the winter we have the “big” 100 cfm unit for supplement balanced air. meets code and our usage patterns (lots windows open from april to october. generally, no need for make up air. This meets the ASHRe all by itself, with or without the bathrooms, but add a hepa or other filter and… well a 10 or 20 cfm over is not overkill. well conditioned space with fresh air all the time. win for homeowners.
less worried about raw humidity (hrv vs erv argument), if needed, we’d install a built in dehumidifier and duct/pipe it right outside. no 40pt pans to empty! manual dehumidifier is crazy inefficient and royal PIA. . ps. no basement to keep dry.
in the kitchen, we’ll have a fantech (or similar) hood fan motor likely sized above the ASHre requirement for make up air… we cook, so the stove will be big viking/wolf range top. the make up air will be separate and in the kitchen MUA will likely heated – I have thought of using the Myson toe kick heater and just ‘funding’ its intake air requirements with external air.
see http://www.mysoncomfort.com/FanConvectors/Kickspace. This is only 110cfm blower, but if we don’t use a 1200 hood and stick with 400-600 and supply more than 110cfm of intake air into the myson, it should get warm and fulfill needed MUA. — we should be fine with the smaller amount of make up air. In the summer, we can (will) also have windows open anyway. I dont see a better way to condition the incoming air in the winter. Martin’s several articles talk about an $1,800 10,000 watt heater.. but that is crazy heat and money. I don’t agree the MUA should be right at the stove, as I think the drafts and curtain of cold air will be noticeable. I have seen a few comments about putting it near/behind under the fridge… might make filtering or flows difficult.. just the same, it should be provided. somewhere… inside a closet? seriously… will cut down on the draft if it is supplied farther from the suck spot.
two LG mini-splits for a/c. for those handful of days a year when it is really hot hot. two heads per floor (each likely 9,000 btu) I know I know — martin wrote it can be done with one head for the whole house… but the cost of a second head per unit is only a few hundred dollars.. and if we have the air on, we will want the house to be an ice box because it is hot hot outside. not used for hot air in the winter except after return from extended time away to boost temp upon return to house. so, one ac in each bedroom and one in the living/den and one in dining/break nook/kitchen = 4 heads total. hvac people still determining loads to ensure sizing of the units is appropriate, but moving from 9,000 to 12,000 does not involve much cost. plus, the seer21 of the LG is crazy efficient. might tuck one or two in the ceiling instead of hanging on the wall – just for aesthetics…
oh. loads and loads of closed cell foam under the house (and further insulated/covered/sealed for fire rating so I can park under house). remember, we will be 11 feet up in the air! could wind up with only 6″ of foam under and 4″ batts, not that much cheaper than to just blow another layer of foam. same problem in roof rafters.. is it worth it to only get to 6″ for vapor/water barrier and then fill with one layer of batts? don’t think so. and the foam rigidity bonus on the floor (see up on stilts part) will help make the whole first floor more “solid” and secure… bonus over other insulation materials.
thanks for reading… comments appreciated.
Patrick
GBA Detail Library
A collection of one thousand construction details organized by climate and house part
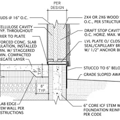
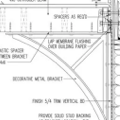
Replies