New cathedral ceiling with unfaced f/g batts, no air barrier or ceiling yet – planning t&g pine under…xps? below joists

Hello, all – first time post. I read all of the q&a posts I could find on cathedral ceiling insulation, and the article on how to insulate a cathedral ceiling, along with every response. So I’m informed, but still have questions about my particular situation.
House is new construction, zone 4A that I bought as a shell – framing done, roof sheathing and asphalt shingles done. Most of upper story is a simple gable roof, made with 2×4 trusses, not joists. Ceiling profile does not match roof profile – ceiling is a shallower pitch. The trusses are about 7″ deep at the eaves over the top plate, and 3′ deep at the ridge. Roof had eave vents, and I had a roofer install a ridge vent.
I hired a large, well known local general contractor to finish the house, who turned out to be nearly totally ignorant of any building science principles. They in turn hired a large local insulation contractor who was even more ignorant, to the point of negligence, and I fought both of them every step of the way.
2/3 of the upstairs has been completed – from the inside of the ceiling out: 1/2″ painted drywall, unfaced fiberglass batts between lower section of trusses, flimsy vent chutes stapled haphazardly on lower section of roof deck, osb deck, asphalt felt (presumably), asphalt shingles. Oh, also recessed cans (sealed or IC for what it’s worth) probably without insulation on top of them.
I scrambled around the day the drywall hangers were working to install XPS air dams between the wall top plates and the underside of the flimsy foam vent chutes, sealing with canned foam. Insulation contractor insisted it was OK to just jam fiberglass into the gap, which obviously left the insulation open to wind wash and air infiltration, and also pretty much crushed the vent chutes at the eaves. Pathetic.
GC would not hold off drywallers so I had to rush, but I did at least a 95% job sealing air dams.
There is no air barrier above the fiberglass, except “sort of” where the f/g fills the space between the drywall and the vent chutes/roof deck. I say “sort of” because these are the cheap corrugated chutes that allow like 2 air flow cavities per joist/truss bay. No sealing over the insulation, just stapled up there. As the trusses open up towards the ridge, there is a 1′ + air space, no air barrier, no vent chutes. If you stuck your head up there you could see from one end of the ridge to the other, over the batts.
SO HERE are the QUESTIONS:
I left the 1/3 end of the floor unfinished – 1 bedroom and bath. It’s roughed in, and has the fiberglass insulation in place. I want to insulate this ceiling properly.
1. Martin stresses the importance of an air barrier above and below the fiberglass batts in an assembly with joists. Is the upper barrier as crucial in my truss assembly, which is in effect more like an uninsulated vented attic, with insulated floor?
2. We want to use tongue and groove pine boards for the ceiling surface – obviously not an air barrier. I propose using rigid XPS board under the joists, over the t&g, as a thermal break, extra r-value, and an air barrier. Taped seams obviously. Sound good? Looks like code approves the t&g as a “thermal barrier” for fire safety. Want to avoid the weight and hassle of installing drywall on the ceiling, as it is pretty tall.
3. Must I install some sort of air barrier over the existing fiberglass batts, where there is a void between insulation and roof deck?
4. Must I eliminate IC can lights, even if I can add insulation on top of them?
5. Should I add an air barrier “wall” up in the trusses, laterally separating this soon to be better insulated space from the existing mess of a ceiling?
FWIW I plan to install rigid foam on the top of the roof deck, and seal soffit and ridge vents whenever we have to re-roof, but that is definitely not in the cards now.
Thanks in advance for the help!
GBA Detail Library
A collection of one thousand construction details organized by climate and house part
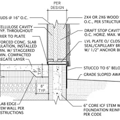
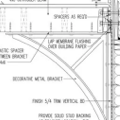
Replies
Use foil faced polyiso with taped seams. Nothing else.
If you want different build at this point, my money says plan the new home while this one is on the market. Sell this one and build the right one from proper planning.
So many come here late in the game. Late in the game, is solveable but not by throwing good money after bad. The above roof foam idea is not economical at this point.
Polyiso your vaulted ceiling and enjoy your home.
Thanks for the fast answer, AJ. It is my impression the foil faced polyiso is a vapor barrier, which I don't want, correct? Just an insulating air barrier.
This house is built pretty well overall, despite some shortcomings, and selling / moving is unlikely, maybe ever, so I'm focused on getting the details right where there is still work to be done.
Regarding the foam over the sheathing later - we're only talking a few thousand bucks for foam, and it's one of the recommended practices here at GBA, so I don't see the fault of this strategy when it comes time to replace the shingles. Am I missing something?
Thanks sincerely for the response, not trying to be combative, but I appreciate a debate!
Chris
Chris you don't understand the layers and types of roofs.
Your present roof is ventilated. The polyiso will be an air barrier a vapor barrier and continuous insulation. That all is good and OK. Why? Because the roof is vented. The moisture is stopped and trapped in the home and what is not is free to go out with the vent space.
XPS is mostly used under slabs. EPS too but was rare and is rare except for those that like all this BS.
As to foam on your roof some day later. You have to pay for the reroof and the foam and if done right you should vent above the foam. For the annual savings of energy costs... it's won't ever pay.
Smarter would be to get rid of the recessed cans or convert them to the new surface fake cans made with LEDs. Cans are popular, I despise them. You have to pick one or the other, be smart about energy and money or just do what you want regardless to the conflict your ideas have with each other.
Why can't you sell in five years and build your dream, green, net zero energy, home?
The amount of thermal break you get out of an inch or two of foam-board on a scissors truss isn't really very much, since the truss elements SHOULD be fully covered by the fluffy stuff above, which is it's own thermal break.
A cheaper air &/or vapor barrier would be houswrap or 6-mily polyethylene (Canadian-style), detailed as an air barrier. That means joining sheet seams ONLY at the framing elements, overlapped and sealed with caulk, and caulking under the edges of the sheet goods where they hit the walls. They need to be sealed to the electrical & plumbing penetratinos, and the recessed cans too. If the recessed fixtures aren't sufficiently rated you need to put a box /bucket over the fixture, sealing the box to the air-barrier with can-foam.
Rather than haphazardly strewn fiberglass batts (did they at least put a layer cross-wise, to cover overt the truss chords?), damp-sprayed "stablized" cellulose will cover in and fill any voids, and won't get blown around by wind in the soffits or slide down the slope. If you blow at least 3" over the top of any pre-existing fiberglass, it's as good as an air-barrier, from a thermal performance point of view, since even low-density cellulose is VERY air retardent compared to standard-density batts like R38s or R30s, and is about as air-retardent as high-density "cathedral ceiling" batts.
What's more, cellulose is opaque to infra-red radiation where as fiberglass is somewhat translucent. Under a 140F mid-summer roof deck the hottest point in a fiberglass-only insulation will be a couple inches below the attic air due to the absorbed IR. And it will be hotter than the attic air(!). In effect you're insulating against a higher temp with fewer inches of insulation. With cellulose the absorption is at the top layer, where it is convection cooled by the attic air, and stays pretty close to the attic air temperature.
If you can't find anybody to blow cellulose, this can be a DIY deal, even without damp spray equipment. Do do it with a cheap rental blower, buy some "stablized formula" cellulose (you may have to special order it through a distributor, but the box-store chains should be able to do that as well), dry-blow it in sections, rake it smooth to depth, and use a garden spray atomizer to lightly dampen the surface (not soak it, to where it darkens appreciably turning in to papier mache, just a fine once-twice over-misting), which will activate the water based adhesives. When it dries (give it a day, maybe two) it will have a somewhat hardened crust to it. The hollow fiber nature of cellulose will redistribute that moisture over time, and activate more glue. This approach is good enough for a scissors-truss application. With a damp-spray blower you'd be able to blow it directly onto the underside of a roof deck and make it stick(!).
True, I am just learning about the layers and types of roofs - that's why i'm here! Great knowledge base. I do understand vented vs unvented roof though.
I'm down with the air barrier and continuous insulation, but my impression was that the foil faced polyiso, being a vapor barrier like polyethylene sheeting, is generally considered bad inside any roof or wall assembly in my mixed humid climate. Especially since this vented roof may become unvented someday. I certainly may be wrong but that's how I've read the articles here - air barrier, vapor retarder - good; vapor barrier anywhere except under a slab - bad.
As for the re-roof idea - certainly only later when we need/want a new roof, but without putting too fine a point on it, I can figure the cost of r-15 of rigid foam with furring strips and new sheathing above, and it's really a drop in the bucket compared to the cost of the whole project. Our energy bills are high enough that the payback may be reasonable, if we are counting. If it's a good practice for a new house, why not for a new roof?
I'm with you on the recessed cans - they just kind of happened - I'll leave it at that.
As far as my dream house - I really don't care about net zero, I just want a reasonably efficient, healthy house that won't leak or get moldy!
Plus, it's not a just a tract home in a city or neighborhood - rather a relatively unique, beautiful property close to family, friends, work, and recreation, that would be harder than average to replicate. I want to make it right. Otherwise, I totally agree - flip it and move on!
Thanks Dana for the info on the Cellulose. No, there are no cross-batts of fiberglass, nothing above the lower parts of the trusses. Just batts placed in between the trusses. Surprisingly, they have stayed in place for a year! We have the room sealed off as there is no air barrier whatsoever right now.
I am stuck on the rigid foam simply as a slightly-insulating alternative to drywall, for about the same price, and easy to place/seal on this very tall ceiling.