New construction building design

Your collective assistance in reviewing my building design is greatly appreciated. Key design parameters include the following.
Central Arizona building site, 6100 ft. elevation, on the border between climate zones 4 and 5, mean winter (Dec – Feb) temperature 36.2º F, mean annual precipitation 26 inches, 40-lb/sq. ft. roof snow load design, heavily forested – high wildfire risk area.
As an owner-builder, I want to maximize the economic value of my own labor, so I want to avoid building systems that require expensive specialized equipment or hired subcontractors where possible.
Given those parameters and much research, I have arrived at the following building design.
Walls – 2×6 frame construction, ½” exterior rated plywood structural sheathing (and air barrier), 1 ½” exterior foil-faced polyisocyanurate foam (PIR) insulation, all seams taped for WRB and drainage plane, 1×4 vertical strapping for vent channel and siding attachment, all covered with fibercement siding. Interior unfaced fiberglass batt insulation in the stud cavities should allow the wall assembly to dry to the interior. Combined interior and exterior insulation will result in an R-value approaching R-30 and should keep the first condensing surface above the dew point at the mean winter temperature.
Roof – unvented cathedral style, stick framed with either 2×12 lumber or I-joists, sheathed with 5/8” Huber Zip panels (air & vapor barrier) and covered with 3 ½” of PIR insulation and ½” OSB (nailbase) sheathing. Rafter cavities will be filled with R-38 unfaced fiberglass batts for combined interior/exterior insulation of R-60 that allows drying to the interior and keeps the interior Zip sheathing surface above 45º F at the mean winter temperature. The roof will be finished in Class A fire rated architectural shingles laid over synthetic roofing membrane.
Other than general design thoughts, my specific questions include:
1. Am I solving potential moisture problems with the plywood wall sheathing under the impermeable PIR insulation by using the unfaced fiberglass batts in the stud cavities and allowing drying to the interior?
2. I had a design conflict with the roof assembly in the twin risks of ice dams and wildfire entry. A vented “cold roof” assembly would be best to prevent ice dams but allows for easy entry of burning embers during a wildfire event. I chose the unvented roof design to favor fire protection and included a synthetic membrane to mitigate ice dam effects. Did I choose wisely?
GBA Detail Library
A collection of one thousand construction details organized by climate and house part
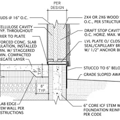
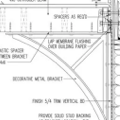
Replies
You will get beat up here for mentioning fiberglass batt insulation but my experience with it has been positive especially coupled with high R sheathing. The walls sound fine along with the roof, what are your plans for insulating the foundation?
This is Armando's part of the world, hopefully he will chime in.
Jim,
It looks like you have educated yourself very well. You do have a good wall and roof design and yes, they are drying well to the inside and you are protected from condensation/dewpoint issues. I would suggest a couple of things: 1. Do not install a vent channel on the walls for the same reasons you don’t do it on the roof; also some manufacturers of fiber cement siding do not want vent channels. 2. I would prefer to use cellulose insulation rather than batts. With batts insulation there is too many chances to be installed incorrectly and you usually get grade 2 or 3 installation. 3. I would use open cell foam for the floor or joist rims (its about the only way to seal them right, fast and cost effective). 4. Use the Airtight Drywall Approach (ADA) on your sheetrock and that will be a great air barrier from the inside; your taped WRB is more than enough air barrier from the outside.
If you are looking for good verifier/rater or some one to consult any deeper in your area, contact Daran Wastchak, 602-885-0861, [email protected]
Doug and Armando,
Thanks for the replies!
The foundation will be a cmu stem wall with a conditioned crawlspace. All of the plumbing and HVAC will be in the crawlspace so I was planning on insulating the inside of the stem wall with rigid foam (2" XPS and 2" PIR, R-23) and conditioning it.
Good catch on the wall vent channels. If I don't want convection introduced embers in the roof assembly, why would I want them in the walls?
I originally was intending to use dense packed cellulose in the wall cavities, but switched to unfaced FB batts due to the plethora of warnings over potential moisture problems in shell assemblies that can't dry in at least one direction. Wouldn't the 5 1/2" of cellulose be a relatively impermeable vapor barrier, trapping the plywood sheathing between two impermiable layers?
Jim,
Cellulose is a great product to use. It can absorb a small amount of moisture when the humidity is high and release it when is dry. It has a high permeability rating so it will let the wall dry to the inside; and just like in NM, you don’t have to worry about humidity in the AZ air too much.
Good that your crawl space is insulated and conditioned. Make sure you install a passive radon mitigation system (very inexpensive); and as I said before, seal your floor rim joist with open cell foam.
Jim: I'm not a pro. First, absolutely forget the fiberglass batts and use dense packed cellulose. Worry not about it being a vapor barrier. It will actually absorb and release ("buffering"0 small amounts of vapor. I have 13" of batts in my house, and they are working OK, but I have (since 1980) learned a lot. I will never touch those things again in my life, if I can avoid it. PP insulation, to some folks; OK, but not good, in my mind. I'd also skip the OSB in the lid and use plywood, in case water ever penetrates.You'll goo and tape the exterior wall plywood, right?