New home building in Northern California: Some wall sheathing ommitted?

Hi All,
I live in Northern Calif about 50 miles south of Sacramento. Hot in the summer, usual NorCal rains and cooler temps in the winter, rarely below freezing. I bought a new construction home from a fairly well-known builder in a senior development which will have 3000 homes soon. They build these homes in about 90 days. I am watching a new construction home across the street being built.
All OSB sheathing with black paper/tar paper (possibly two layers), chicken wire and eventually 3 coats of stucco over about a 10 day period. However, one whole area of the home has no OSB. Partially in the garage but continuing into the living area. Maybe 15 feet long.
In place of the OSB, there are robust steel wires (maybe solid 14 gauge) attached to the outside of the wall studs, running horizontally and repeated every foot, so there are about 8-10 wires. Black paper already attached to the outside and the chicken wire is in place.
Is this a good practice?
Why not just complete the remaining 10-15 sheet of OSB?
There have been a handful of homes built here in the past 2-3 years where mold developed on inside walls and baseboards and had to be completely opened from the outside and re-constructed.
Wonder if this same (some missing OSB sheathing) building practice was used in my home? The interior garages are nicely finished wall board.
Thx DD
GBA Detail Library
A collection of one thousand construction details organized by climate and house part
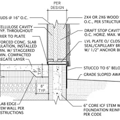
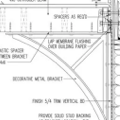
Replies
D.D.,
In the boom years of residential construction after World War II, California builders often installed stucco on chicken wire stapled to the wall studs, without installing any sheathing. Tens of thousands of homes were build this way.
I would never buy a home using this approach, however, even if it is still legal. There are several problems with omitting sheathing. For me, the most serious is the likelihood that this type of house has a higher rate of air leakage than a house with sheathing.
It is also harder to address a moisture entry problem when the sheathing has been omitted.
If you have already bought a house in this development, you can either (a) ask the builder whether your house was built the same way as the one you noticed, or (b) make some inspection holes and investigate.
Speculation on the wires: In some seismic zones OSB or plywood sheathing may be deemed too rigid, making the house more prone to walking off the foundation during an earthquake.
I've read that in some locations caulking the sheathing to the studs with construction adhesive is expressly dissallowed for that reason, but I've never heard of limited sheathing or using wires in lieu of some of the sheathing as a seismic resilience solution. If that turns out to be the rationale, it would be news.
Are other homes currently being built in that area fully sheathed? (Which would rule out that explanation.)
This is common in production houses in California. I am in San Diego. They omit the OSB or shear panel where it is not needed for shear strength. The engineering dictates how much shear wall is needed. To save cost the extra is omitted.
The paper is the water resistant barrier and the wires support the paper while the stucco is applied. The wire is not a designed structural element.
Stucco is not typical used in modern construction as the Lateral Force Resisting System. It has performed poorly in past earthquakes and has a low design shear value & low Response Modification Coefficient used in seismic design. So it is no longer cost effective to build a stucco shear wall building that anyone would want to buy.
Using Plywood shear walls is the favored material. The nails attaching the sheathing to the studs bend and dissipate energy in a seismic event. They performed lab tests of plywood walls to learn how the fail and to determine the design strength.Thus adhesives are not allowed due to the poor energy dissipation of the adhesive. It suddenly breaks unlike the nails which bend. The plywood wall being too rigid is not an issue.
The walking off the foundation is an foundation issue. the bare minimum is 5/8" anchor bolts and often 3" sq plate washers and holddowns on the shear wall ends.
Tim,
That's my experience up here in BC too. Between seismic concerns and rain-screens, stucco has almost entirely disappeared from residential construction.The one thing our seismic code doesn't mandate is plate washers, which surprises me.
The Shear Wall provisions in the IRC's reference allows you to eliminate plate washers if you have hold downs at the ends of the shear walls. They ran a bunch of tests on sill plates and anchorages in recent years. The reports are out on the web.
Stucco finishes are still king here in San Diego and most of Southern California, they just don't use it as part of the calculated structural system. Not many rain screens here.
Tim,
That makes sense. Epoxied rods with Simpson hold downs on the ends of shear panels are typically specced here.