Nitrogen pressure test
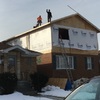
Just finished my lineset (52ft)run.
To my Fujitsu 18rflcd.
I currently have 200psi of nitrogen and have been holding @ 200psi for the last 2 hours.
Do I need to get the psi higher? Didnt want to add too much and risk damage.
No where in the the install manual does it talk about nitrogren pressure test buy rather using the vacuum procedure with a micron gauge to check for leaks.
I am in no rush so I planned on leaving it overnight anyway. I did test for bubbles. I thought I saw one at the inside 1/2″ flare connection but perhaps it was my OCD. If pressure holds then no leaks right??
Single vacuum or triple vacuum tomorrow? Any thoughts on that?
Raul
GBA Detail Library
A collection of one thousand construction details organized by climate and house part
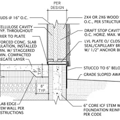
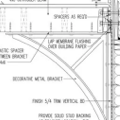
Replies
A small leak might take a while before you'd see a change in pressure. If it holds overnight, that's a pretty good sign. I just had mine hooked up, and according to the guy it was holding the vacuum for 10 minutes. However, when he released the gas there was a huge leak, as in you could tell by the sound alone from 50 feet away. So I'm not so impressed with the vacuum test. 200psi of pressure is definitely a much better test.
Walta,
As always thanks for the help. And you are correct I'm in no rush just want it done right. In my mind I'll tell myself time is of no concern, but ask my wife and you'll get a different answer.
So I just finished the triple vacuum. In my last vacuum I was able to get it down to 99 microns and stabilized around 122 microns after about an hour or so.
Checked the Schrader valve with some bubbles and all good so I release the refrigerant.
Next week I'll be working on electrical rough in for the entire 2nd floor and outdoor unit. Very excited to see what she can do.
Drywall perhaps beginning of June so I can finally see the light at the end of the tunnel.
Raul
Most literature I've found recommended 200psi. But I have come across a few articles that state to put 400 psi to 600psi or more. I wasn't sure on how much is too much. Plus with a slightly longer than normal lineset wasn't sure. But my instinct tells me the lineset length doesn't matter. I'm 3hrs in now and still holding 200psi, so far I'm feeling pretty good about my flares and torque.
Raul
The vacuum test is to check that all water has be cleared from the lines. Pressure test is for leaks.
Sometimes it is impossible to get all the moisture out of the lines without flushing it with dry gas, so you might end up doing a couple of pressure/vacuum cycles.
Short pressure test will not show you if you have a small leak, overnight is much better.
Also be mindful of temperature difference. If you pressure the system on a hot day and check the next day when it is colder, it will look like you lost a bit of pressure.
Thanks Akos,
How much is normal loss based on temperature fluctuations?
I added nitrogen today around noon it was around 85f.
Tomorrows weather report is close to this but overnight low tonight is 70f.
Raul
You'll see 5psi change at 200psi with each 10F.
Very helpful thanks akos. So tonight @70f should read 190psi. But will it rise back to 200psi as temps go up tomorrow afternoon?
Raul
Pretty close. 15F delta so 7.5PSI change. If tomorrow morning, you see say under 150PSI, you have a leak. Small leaks are sometime a pain to find.
Hotter temperatures = higher pressures. Assuming you have an R410a system, normal high side pressures can get up into the 400+ PSI range. I wouldn’t test higher than maybe 500-600PSI, although I’ve seen some charts showing higher than that. In all reality, a test at 400PSI should be pretty safe and likely to catch even a really small leak. I like mega bubble leak detector solution for any suspect spots — it’s much better than plain ol’ soapy water for bubble tests.
For vacuum, I make my guys leave it at least over lunch (about an hour). Ten minutes really isn’t long enough. My most trusted mechanical contractor has always said overnight is best, but no one has time for that. I’d try for at least an hour though.
Bill
It is 410a. I added to 200 psi but I guess I could have gone a tad more liberal with the nitrogen.
But I have 9 hrs so far and still holding @ 200psi.
So since I have more time than money, are you saying i could run the vacuum overnight?? I've read up a bit on a triple evacuation procedure but not sure if this is preferred or even better?
I'm planning on vacuuming tomorrow sometime assuming my pressure test holds. I could vacuum for long as it takes to ensure a deep vacuum.
Everyone says below 500 microns. But is there a Number you shoot for that is better than just good enough??
Raul
Most vacuum pumps won't survive long runs, never mind the oil in them. Long lunch is good. The important part is looking for vacuum decay. Once you reach your target vacuum, shut off the vacuum port. If you slowly start loosing vacuum (wait a couple of hours) than you have moisture in the lines, which you need to remove with some dry gas.
Nitrogen is great to help you fund a known leak but not much help for deciding if you have a leak.
The best way to know if you have a leak is to pull a vacuum close the valves, turn off the pump and wait 24 hours. If the gage stays the same you are good. If it goes down an inch or 2 and stops you may have moisture in the system. If it goes down more than 5 inches you have a leak.
Do you have a micron vacuum gage? This is a very sensitive vacuum gauge so you can do this test in minutes instead of hours.
Triple evacuation is absolutely the best practice but almost never happens in the field because it take time.
Walta
Walta,
I do have a micron gauge. I purchased specifically for this install. I am still holding my nitrogen pressure @200psi and I'm 23hrs in at this point. I'm going to add another 200 psi and bubble test one more time.
Per your recommendation I will proceed with the triple evac. So as I understand it once I get the microns down to a number I like and turn the pump off the number will rise but stabilize and hold. If the micron gauge continues to rise and never stabilizes then I have a leak somewhere.
Raul
Raul,
Did you buy everything just to do this install? I'm curious how much that bumps up the cost as I'm looking to put in my own mini split and was thinking I would have to hire getting the system vacuumed and charged. I have a small vacuum pump for car A/C systems, but don't think that would be sufficient for a job like this. Would love to hear your experience on getting the tools and doing the work yourself.
Alex,
I will put together a list of items I purchased to complete this install. Depending on the your intentions long term it may or may not be worth it.
I intend on swapping out my basement gas furnace this summer as well and installing a ductless unit at my parents so that's 3 installs this summer with possibly more in coming years.
It's more so a cost question for me of labor vs tools, and I love tools so normally I'll just bite it and buy more tools. I'll post later tonight when I'm all wrapped up and enjoying a cold one.
Raul
Thanks Raul. I'm looking at replacing my gas furnace as well since I want to get off gas and have been looking into adding AC to our house. I could see myself installing another mini split or two over the next 5 years or so and here in San Jose labor is extra expensive so something like $500-$1000 in tools could easily be cost effective as long as they aren't too complicated to use.
Alex,
The entire process was not physically daunting but rather tedious. The most physical was some stretches of the lineset run. I opted to use a low static ducted indoor unit so this add to the workload but I did not need any special tools other than what I already had.
As far as the nitrogen pressure test i referred to stuzman youtube channel. He has a few good videos on bending lineset, nitrogen testing and vacuum procedure. I also referred to AC service tech Youtube channel. I basically watched both and extracted what I thought was the best practices from both channels until I had a solid gameplan They both provide a tool list in there video descriptions but I found these to be either incomplete or over prepped. So after deciding how I wanted to proceed, I purchase the tools I would need based on there step by step. Some items I already owned but Ill included them
Here is everything I needed,
stocked locally
Spring type tubing bender--performax--Menards
tubing cutter---Milwaukee--Homedepot
3" hole saw--Milwaukee--Homedepot
nitrogen tank--praxair and airgas are 2 local/national? companies that will sell you or rent you a tank.
online
eccentric cone flaring tool 45--yellow jacket--test equipment depot
metric torque wrench set-- robinair---test equipment depot
Digital Vacuum Gauge--yellow jacket--test equipment depot
Single Test Compound Gauge--yellow jacket--test equipment depot
series 41 Test & Charging Manifold--yellow jacket--test equipment depot
appion valve core removal tool 5/16"-- amazon
appion valve core removal tool 1/4"-- amazon
nitrogen regulator--uniweld ----amazon
appion 3/8" to 1/4" vacuum hose--amazon
rectorseal bubble leak detector--amazon
nylog blue--amazon
vaccum pump 2stage---Robinair--amazon
tubing bender--imperial--amazon
If you need to add refrigerant you will need a refrigerant scale and refrigerant.
You will need a epa type 608 certification to purchase and handlee the 410a.
you may not need this depending on your lineset length and units precharge but something you should account for if needed.
In the end I ended up not using the imperial tubing bender, I actually had great luck with the spring hand bender considering my lineset sizes where 1/4" ans 1/2". I did in fact bend the 1/4" line by hand. slow and steady wins the race here.
For pressure testing I used the single gauge yellow jacket in combination with the two appion valve core removal couplers. Although I didn't use or need the manifold gauge set it was mostly for the ball valve hoses it came with.
Probably $800 in tools and accessories. Based on my location I couldn't find an installer that I totally felt comfortable with considering none had any actual field experience installing a mini split before. I knew of one local outfit recommended to me by a member of the community here but they never returned my phone call so I decided to move forward on my own.
Labor cost has gotten quite pricey here as well considering the quality of work. And if you want top notch work you will pay for it. Beyond reading thoroughly through installation manual and youtube, I always feel confident in the members here to guide me on anything Im unsure about.
If you have some basic tools already you might be able to bring the cost down a bit, I decided to invest because It made sense in my situation but not for everyone. If you decide to go forward just read as much as you can and watch some you tube but try to stick with the channels above. I found them to be the most thorough and competent. Most importantly this site is a great resource and everyone has been willing and available to offer advice. Should you move foward a load calc is invaluable. My was done by a local engineer because my numbers were close but not dialed in like his.
Raul
My guys always run the vacuum for a time period, not to a specific micron number. That’s mostly because it’s production work though, so we can’t take forever to do the job. The most important thing is that your vacuum doesn’t decay. You can’t get under 50-100ish microns without a much more complex (and expensive) vacuum pump than the typical refrigeration tech unit.
What you’re doing with the vacuum is getting the last of the moisture out, basically boiling it off. I disagree with Walter about leak checks though: vacuum will not find leaks as well as higher pressure. Vacuum is limited to atmospheric pressure, and it doesn’t force fittings apart the way that high pressure can. I would leak test with high pressure (which is how I write my specs), and then pull vacuum and check for decay. Triple vacuum is good if you have time, as is a looong (overnight) window to check for vacuum decay prior to charging the system. You don’t need to run the vacuum pump for a super long time when you’re just looking to see if the system holds whatever level vacuum your pump can achieve.
Bill
Bill,
Just staring my triple evacuation. Got it down to around 140 microns first go. I Will try to get it deeper each cycle. It seems to have stabilized @ 170 microns after about 15mins. I'm taking it slow and steady since I'm outside enjoying a balmy day here in chicago anyway.
Raul
The way I see it any positive pressure you measured and record is relative to the current air pressure and temperature. Your gage reading is in PSIG will change will change when the atmospheric pressure changes because mechanical gages measure deference inside and outside of a bourdon tube. Also nitrogen is almost certainly in a 100% gaseous form and when you warm the gas it must expand in a solid container the pressure inside the container must change.
https://blog.wika.us/products/pressure-products/pressure-measurement-understanding-psi-psia-psig/
The great thing about a vacuum is you are measuring against an absolute. If you have a leak when a small number of atoms entering the vacuum they will make a larger change in the gage reading than the same number of atoms escaping a 400 PSIG vessel may not move the needle more than the noise.
Some leaks will self seal under a vacuum making them impossible to detect with vacuum.
Pressure and vacuum are both tools in our box nether is perfect for every job and they both have a time and place.
It is clear that Raul has the luxury of almost unlimited time on this job.
Walta
Walta,
As always thanks for the help. And you are correct I'm in no rush just want it done right. In my mind I'll tell myself time is of no concern, but ask my wife and you'll get a different answer.
So I just finished the triple vacuum. In my last vacuum I was able to get it down to 99 microns and stabilized around 122 microns after about an hour or so.
Checked the Schrader valve with some bubbles and all good so I release the refrigerant.
Next week I'll be working on electrical rough in for the entire 2nd floor and outdoor unit. Very excited to see what she can do.
Drywall perhaps beginning of June so I can finally see the light at the end of the tunnel.
Raul
Atmospheric pressure at sea level is a little under 15PSI though, so you don’t really stress anything with that. Gauge or absolute, you’re still stressing the system much more with high pressure than with vacuum in terms of the absolute forces being exerted on all the connections, so the high pressure is more likely to expose any weak spots.
Vacuum checks are best for finding residual contaminants in the system. Pressure tests will never find that stuff. The longer you wait holding vacuum, the more certain you can be that you’ve gotten all of the moisture out.
Best is to do do both tests. Especially if you have the time :-) My crews don’t usually have the time, primarily because the customers get upset seeing a tech sitting and watching a gauge that “isn’t moving anyway” (hopefully it’s not moving that is :-).
Bill