Okay to carpet uninsulated brick walls in climate zone 2?

SUMMARY: Am I risking condensation/mold by attaching carpet to uninsulated brick walls in climate zone 2?
DETAILS: I have a brick rental house with no framing — the inside walls are the same structural brick you see on the outside. That means there’s no insulation. I don’t want to insulate the exterior (new framing, insulation, and siding) because it’s too expensive. I’m also not keen on traditional insulation on the interior (framing, insulation, drywall) because it’s a tiny house (~420sf) and eating into the room by 4″ from each exterior wall is too much, because space is precious.
So, I had the idea to install carpet, because it has pretty decent R-value, and I’d have to eat into the room by only about an inch. My idea is to screw 1/2″ x 4″ wood strips to the top and the bottom of the walls, glue a 1/2″ pad in between them, then tack a carpet onto my wood strips.
My concern is that maybe I’m inviting condensation in the padding which could grow into mold. Should that be a concern? Any other problems with my idea, and are there better alternatives?
Thanks!
GBA Detail Library
A collection of one thousand construction details organized by climate and house part
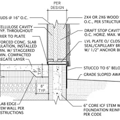
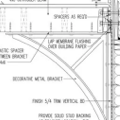
Replies
Michael,
Just to satisfy my curiosity: Do you think you will be able to find renters who want a house with carpet on all the walls?
Absolutely! Much nicer than brick, and the place has been rented for the past 60 years in that condition. Lots of high-end places have carpeted walls, e.g., recording studios, some hotels. Looks/feels nice, keeps the rooms quiet. I'm not sure how easy it will be to hang art, but certainly easier than it would be with solid brick.
Michael,
The risk, if any, would occur when the walls are cold. In Climate Zone 2, your walls aren't going to get very cold. So I don't think there is a moisture risk -- just an aesthetic risk.
You would end up with a much nicer end result putting 1-2" polyiso foam board directly against the wall, 1x4 sleepers screwed to the brick and then drywall. This can be done with 2-3" of room. There are a few different ways to put this together and with a little creativity and a bit more work, you can really minimize the space use.
Curious, are outlets run on the surface?
Anyone ever run a carper cleaner vertically?
I think you’d get a nicer finish by using 1” polyiso instead of carpet. You can get polyiso like dow thermax that has a side rated to be exposed. Glue it to the walls, tape the seams, prime it and paint it. It would look like regular walls. If you have surface mounted electrical, just cut around that, depending on the box depth the polyiso should make the electrical “more flush”. If the electrical devices are recessed, you could use mud rings or box extenders to bring the devices up to the level of the face of the polyiso.
Carpeted walls seem like trouble to me, and does carpet pass the vertical flame test?
Btw, I used to work in recording studios. We never had carpeted walls. Walls were usually covered with either Sonex (soundproofing foam), drywall, or hardwood depending on the particular requirements of any given room.
Bill
Sounds like a bad idea. The carpet would need to be glued to the wall or it will eventually sag. How would you clean it?
In zone 2 it only takes R6 continuous insulation on the interior side to meet code minimum on a masonry wall. That could be 1" foil faced polyiso strapped to wall with 1x4 furring through screwed to the brick with masonry screws, onto which you can mount wallboard, eating up only 2.25" of interior space.
Alternatively the foil faced polyiso can be glued to the brick, and the drywall glued to the polyiso, with a few cap screws through-screwed to the brick per sheet (in case the adhesive ever fails) eating up only 1.5" of interior space. (This solution would take 96 linear feet of exterior wall to lose just one square foot of living space.)
With either solution the big screen TV's wall mount would likely have to be through screwed to the masonry unless you went with 2x4 furring. With 2x4 furring 24" on center you could hit code-min performance with continuous half-inch polyiso on the brick, and 1.5" foam (any type) filling the space between the furring. With half-inch wallboard that would be 2.5" of encroachment on the living space.
When insulating on the interior it can sometimes be a PITA dealing with all the interior window & door trim issues. Leaving a 4-5" clearance around pre-existing door & window trim that you don't want to touch and just plastering directly onto the brick in those areas won't be a huge energy-use hit.
Hanging a rug on an uninsulated masonry wall sounds like a way to get into the mold-farming biz. With the right rug type and the right humidity levels you might even be able to grow mushrooms!
Thanks for the responses! Based on them, my plan now is 1" polyiso glued to the brick, 3/8" plywood screwed through the foam to the brick, and 1/4" drywall screwed to the ply. What do you all think?
I know that 2" of polyiso would be better, but 1" seems like a good compromise between some insulation and not making the house smaller.
The 3/8" plywood buys you what, exactly? Unless it's baltic birch or something its not going to hold up the big screen TV (but through screwing the TV mount to the brick with masonry screws would work.)
That stackup isn't a pre-approved already-tested timed thermal barrier against ignition for the foam for code purposes, but half inch wallboard is. Keep it simple.
In US climate zone 2 going with 2" continuous polyiso might be overkill- the cost of that second inch is likely better spent on other building envelope upgrades or higher efficiency air conditioning, or window upgrades, if there are any single-pane windows. (Low-E storm windows over wood sash single panes is a relatively cheap upgrade to code-min or better performance, far cheaper than code min vinyl replacement windows.) But 1.5" wouldn't necessarily be crazy. In new construction with all better-than code features 2" polyiso would be about the limit- beyond that spending money on rooftop solar is likely have a better lifecycle return on investment.
Why not just skip the plywood and use regular 1/2” drywall screwed through the polyiso into the brick?
Bill
That's really possible? Thought I would need something more substantial to attach the drywall to. If I can really skip the ply, I might go ahead and do 2" of polyiso.
Yes, you can screw the drywall through the polyiso into the brick. The only thing you’ll need to be careful of is that the polyiso has a little more “squishability” than framing lumber, so you don’t want your drywall screws to dimple the face of the drywall too much. It’s easy to control though.
You’d get more benefit from eliminating the plywood layer, using 1/2” drywall, and using thicker polyiso. 1.5” polyiso is probably a good amount as Dana said. That will give you about R9, and continuous R9, so probably better than a normal 2x4 framed wall with fiberglass batts would be.
Bill
Dana: "The 3/8" plywood buys you what, exactly?"
(1) Less work. The screw schedule for drywall is 64 per sheet. That's a lot of drilling into brick! I'm sure I could get 3/8" ply to be nice and secure with half that or less, then I could put 64 screws into the drywall + ply. ( On the other hand, maybe I could *glue* the 1/4" drywall to the polyiso?)
(2) Easier to hang stuff. Big-screen TV's might be out, but most other items will be able to be hung more securely.
(3) More stable installation? Drywall is flimsy. It's much easier to imagine it getting cracked or damaged with squishy foamboard behind it than a nice solid piece of ply.
I found IBC 2603.4 and Table 721.6.2(1). Extrapolating the numbers, 1/4" drywall + 3/8" plywood *should* provide the necessary 15-minute barrier, but since it's not prescribed, it probably won't be allowed, unless my local code inspector is feeling particularly generous.
1" polyiso (R-5.5) + 3/8" ply (R-0.5) + 1/2 drywall (R-0.45) = 1-7/8" and R-6.45
I already planned to replace the single-pane, wood-framed windows with energy-efficient ones.
>"I found IBC 2603.4 and Table 721.6.2(1). Extrapolating the numbers, 1/4" drywall + 3/8" plywood *should* provide the necessary 15-minute barrier,..."
No it won't. The dumb math goes: 3/8" plywood buys you 5 minutes ( per the Table) , and it takes 3/8" of gypsum to buy another 10 minutes (per the Table), which adds up to the 15 minutes (exactly.) Without the rosy glasses 1/4" gypsum doesn't look as fat as 3/8" gypsum, and isn't likely to buy the 10 minutes. Maybe in conjunction with one another they will pass the test, maybe they won't, but an extrapolation like that is no better than WAG.
>"Drywall is flimsy. It's much easier to imagine it getting cracked or damaged with squishy foamboard behind it than a nice solid piece of ply."
Half inch drywall supported only by ultra squishy R11-R20 fiberglass between studs 16" on center is the interior finish wall of most homes in the US. Foam backed by brick is orders of magnitude less flexible/squishy, and far more supportive of the drywall. It's stiffer and firmer than plaster on lath too. Unless your hitting your wall with sledges it would be hard to tell the difference between the plywood-reinforced assembly and the foam sandwiched between a brick wall and half-inch wallboard. It won't flex anywhere near the elastic limits of either the foam or the drywall.
>"1" polyiso (R-5.5) + 3/8" ply (R-0.5) + 1/2 drywall (R-0.45) = 1-7/8" and R-6.45"
The code prescriptive Rs for mass walls only allows you to count the insulation layers, not the finish materials. Most 1" foil faced polyiso is labeled R6, which WILL meet the IRC code minimums, but R5.5 foam won't. See Table N1102.1.2 :
https://codes.iccsafe.org/content/IRC2018/chapter-11-re-energy-efficiency?site_type=public
That said, it's not crazy to go with 1.5" polyiso or 1.25" polyiso (available from some manufacturers.) Building Science Corp suggested R15 "whole wall" (with the thermal performance all layers counted, including air films) as the point at which the lifecycle values might worth analyzing more carefully. See the zone 2 row in Table 2:
https://buildingscience.com/sites/default/files/migrate/pdf/BA-1005_High%20R-Value_Walls_Case_Study.pdf
>"I already planned to replace the single-pane, wood-framed windows with energy-efficient ones."
IRC 2018 code min windows for zone 2 is U0.40. For zone 3 it's U0.35. A tight low-E storm window over a wood sash single pane would even beat the minimums for zone 3. If the original windows are in decent shape or reasonably salvageable the low-E storm and some tightening of the originals are a better value, (though architectural purists and historical commissions sometimes object.) Table 2 in that BSC paper calls out U0.35 as the financial rationality frontier for climate zone 2.
The denser clearer grain old growth wood of antique windows is better stuff than almost all new wood windows, is well protected with exterior storm windows, and will outlast almost any replacement window.
Thank you for your help. The windows are old, poor quality, and falling apart. I'd replace them even if energy efficiency weren't a goal.
Now I'm trying to figure whether the labor cost of drilling 64 holes into brick to screw the drywall directly over the foam would outweigh the materials + labor cost of putting a 3/8" layer of ply over the foam first, with half as many holes or fewer.
1/4” drywall isn’t enough for a thermal barrier. You need at least 1/2” drywall for that. The thermal barrier is required by code to “protect” the foam insulation. You could also use foam that is rated to be exposed, like Dow Thermax, but it’s much more expensive and can’t be finished the way drywall can be (mud and tape) to give a smooth, paintable surface.
Bill
I had to put this problem on the shelf but now I'm revisiting it.
I came up with 10 different options for wall assemblies, each with various degrees of pros and cons. I summarized them in a color-coded table as part of an article I wrote here: https://michaelbluejay.com/building/insulate-exterior-wall-from-inside.html
Thank you everyone for your advice, which has been extraordinary helpful. Zephyr7, thank you very much for your tip about Thermax not needing a thermal barrier. That's saving me adding depth on my wall assembly, and sparing the materials and labor to install a thermal barrier.
Dana, you said that a 1.5" assembly would take 96 linear feet to eat up 1 sf of living space. Seems to me that 1.5" takes only 8 linear feet to eat up 1 sf. (1.5" / 12" x 8' = 1') Am I missing something? If I'm correct, the 7/8" I'm adding over 30 linear feet will eat up 2.2sf, or 1.7% of the room.
I know normal adhesives eat through foamboard, but can they be applied to the foil face? They're a lot cheaper than foamboard adhesive.
Iso board is not as solvent sensitive as polystyrene.
And I have successfully used urethane construction adhesive on xps. It does not melt it
You can use any regular adhesive with a non-perforated foil face. The foil facer is usually aluminum, so anything that sticks to that will be OK. Since the facing acts as a barrier, the adhesive won't come in contact with the foam material itself so solvent compatibility is not an issue in this case.
Bill
Thanks for the tips on the adhesive. I don't know why it didn't occur to me at first to look up what the manufacturers say, so I did, for R-Max Thermasheath (foil-faced polyiso), which says to use "a quality grade construction adhesive", with no special mention of special foamboard adhesive.
I would be ever so delighted if someone would comment on the color-coded table I made which I linked to in my previous comment.
Is the cost for all the walls in the house? I’d mention in your table how many square feet you’re covering to arrive at the number in the “materials cost” column.
Bill
It was already mentioned under the table, but I put some figures in the header cell also, just now.