Optimal thickness of closed-cell foam in unvented cathedral ceiling
Hello,
I live in climate zone 5, and am in the process of refinishing the third floor space of a very old house, around 1800 square feet of ceiling space. It is an unvented roof assembly, with relatively deep rafter bays, between 7-8 inches. I was planning the use closed cell spray foam and was leaning toward using 5 inches of foam which would give me around R35.
However, I’ve read some things lately that suggest very thick foam may be less desirable than ~2 inch foam with cellulose the rest of the way, which could give me close to the same R value if I fill all the way out the full depth of the rafter bay. Something about how with less foam depth the moisture would condense on the surface of the foam, and with more depth it would condense on the underside of the roof decking between wood and foam.
Also, I was thinking of using wood for the finish instead of drywall, and so I am unclear on whether I need an additional air barrier such as MemBrane, with either the full foam, or foam/cellulose options.
Will I be fine either way? Is there a preferable option? From a cost perspective it would be nice to avoid having to use the MemBrane, if possible, since multiple inches of closed cell foam over 1800 sqft is expensive enough…
Thanks,
BPB
GBA Detail Library
A collection of one thousand construction details organized by climate and house part
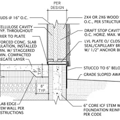
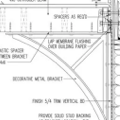
Replies
BPB,
I advise doing more research before you move forward. You could potentially create some problems that would be difficult or expensive to correct.
There are multiple options for improving the insulation layer in your third floor. Ideally, you would increase the r-value to R-49. This article provides a lot of relevant information (https://www.greenbuildingadvisor.com/blogs/dept/musings/how-build-insulated-cathedral-ceiling). After reading it, you may want to post additional questions.
Steve,
Thanks for your reply. I read the article you suggested, and it seems to confirm my thinking - that I have options of either all foam, or foam plus cellulose. No poly vapor barrier, but MemBrain can sometimes be used. I was just trying to figure out which option is preferred.
Unless I am not understanding something correctly? I am open to that possibility!
BPB
Jon,
Is there any way to avoid thermal bridging through the rafters? They are 150 year old, full dimension 2x8 lumber, sometimes 2.5x8!
Warm sheathing is not an option for me as the roof is a low-hip with wide overhanging eaves and built-in gutters, so I can't just add rigid foam on top without rebuilding the whole thing. Plus, the house is on the national register of historic places and I am limited with some things.
As far as I can tell, I am going to have to insulated the underside of the sheathing, right?
Thanks,
BPB
You can reduce thermal bridging with some rigid foam between the rafters and the finish wood.
BPB, yes, to meet code you need air-impermeable insulation directly against the bottom of the sheathing. In zone 5 you need 41% of the total R-value to be toward the exterior, for prescriptive condensation control. Despite advertisers' claims, most closed cell foam quickly degrades to about R-5.6 to R-6 per inch.
The blowing agents in standard spray foam are potent, persistent global warming agents, so if possible it's better to use a product with HFO blowing agents. The two I've been spec'ing are Lapolla Foamlok 2000 4G or Demilec HFO High-Lift. Not only are they better for the environment, they have slightly higher R-values, more info here: https://www.greenbuildingadvisor.com/blogs/dept/green-building-news/next-generation-spray-foams-trickle-market.
To meet the 2015 IRC code for new construction, you should install R-49 total; if 41% of that is foam you need R-20 foam. That's at least 3 1/2" of conventional foam, or 3" of HFO foam. Then you would need about 8" of fibrous insulation to reach R-49 total.
Since you don't have 11" to 11 1/2" in your ceiling assembly, you have a few options:
1. Don't meet code-minimum R-values, but do maintain the 41% (or greater) proportion.
2. Furr down the rafters for additional insulation space.
3. Fill the existing cavity with a mix of foam and fibrous insulation and add additional rigid insulation at the interior. Although Jon recommends rigid foam at the interior of the rafters, I don't think that's a good idea, because moisture could get trapped between the interior and exterior foam layers. You could use rigid mineral wool, which is vapor-open, in a similar application.
4. Fill the existing framing cavity with closed-cell foam. If you want additional R-value, then in this case you can safely add rigid foam at the interior.
In zone 5 at least 40% of the R-value has to be outside the first condensing surface, which is where the foam and fiber insulation meet. So R20 foam, R30 cellulose would make it, but R12 foam R38 cellulose would not.
Download and archive the MassSave Deep Energy Retrofit Guide:
https://buildingscience.com/sites/default/files/migrate/pdf/GM_DER_Guide_2013-01-18.pdf
The section on attics & roofs starts on page 49. Note the 40% minimums in the diagrams on p50 & p51, when some of the insulation is on the exterior of the roof deck. Those same minimum ratio applies when it's closed cell foam + fiber on the interior.
An inch of interior side unfaced EPS foam won't trap moisture. Foil facing would.
As you research, consider a few points:
a) warm sheathing is more robust than cold
b) reducing thermal bridging is beneficial (for moisture and heat)
c) best to avoid trapped moisture (ie, low perms on both sides of a moisture susceptible material).
d) taped foam can be an interior side air barrier and an interior air barrier is always beneficial (especially with cellulose or bats).
e) spray foam on sheathing makes repairs harder
Jon R has it right, an inch of unfaced EPS won't trap moisture, but an inch of interior EPS also isn't much of a thermal break.
A mere 2" of HFO blown foam is a bit shy of R14, leaving 6" for fiber insulation. You can't go over R21 of fiber in that 6" without potential wetting of the fiber, so you'll need at least 3", leaving 5" for fiber insulation. With 5" f depth with 1.8lb fiberglass you'd be at R21 fiber, R20 foam R41 total at center cavity, which isn't terrible, but it's sub-code, and the thermal bridging of the rafters deliver enough heat to a snow covered roof to start ice dams.
The wooden rafters are on the order of R1.2/inch, so an 8" rafter depth would be about R9.5. An inch of Type-II EPS is only R4.2, so it's not even doubling the R value of the framing fraction.
Installing edge strips of 2" foil faced polyiso through screwed to the rafters with 1x furring more than doubles the framing fraction, and increases the cavity depth from 8" to now 10.75". (This type of edge strip construction is sometimes referred to as "Bonfiglioni strips", explained in more detail here: http://www.finehomebuilding.com/membership/pdf/9750/021250059.pdf )
With 3" of most vendors' HFO-blown 2lb foam you'd have about R20 of foam, and with a 10.75" cavity depth about 7.75" left over for fiber insulation.
With 7.75" of cellulose you'd get about R24, which added to the R20 foam yields R44 at center cavity. Depending on the actual framing fraction that MIGHT be enough to hit IRC code performance on a U-factor basis due to the fact that the framing is now north of R20 instead of being just shy of R10. The R20/R44 is a 45%+ ratio, which would be decent dew point margin.
With 7.75" of 1.8lb density fiberglass (Spider, Optima, L77) you'd be at R32.4, and a total of R52.4. That definitely meets code on an R-value basis, but R20/R52.4 is only a 38% ratio. The roof deck would be protected, but there's some potential of wetting of the fiberglass over a winter, particularly if you're on the cold edge of US climate zone 5.
The 7.75" of cellulose solution is definitely a safer bet with the R12-R13-ish edge strips.
Thanks for all the advise. I ended having 5" closed cell spray foam installed on the underside of the roof decking. Then, I took Dana's advice and added the 2" foil-faced polyiso strips to block thermal bridging.
Now I need to decide how to fill the remaining space in the rafter bays. I was contemplating using batt insulation - either fiberglass or mineral wool. Will it matter much what I end up using, since I already have a moisture barrier and air barrier with the spray foam? I'll be fine on the ratio of foam to fiber, I think.
Right now I have around R33 center cavity, so any of those options should get me close to code, and I was thinking of just going with the cheaper option since I already have spent plenty on the foam. Is this correct thinking?
BPB,
Either mineral wool or fiberglass will work. Denser (higher R-value per inch) versions of fiberglass perform better than less dense versions, and installation quality is important. But either of the products you mentioned will work.