Partial insulation of old house

I live in a c. 1923 house in Toronto. It is unusual for its age because it is constructed somewhat like a modern brick veneer home with a single wythe of relatively soft moulded brick set in lime mortar tied to (1) a 2×4 stud wall 16 O.C. (2) sheathed with 3/4″ boards (3) covered with tar paper, (4) and an airgap of about 3/4″ behind the brick.
There are no weepholes at the base of the brick wall, but there are no signs of rot on the sills. Some re-pointing and brick replacement work was necessary (especially at the base of the wall) a couple of years ago, the brick was in pretty good shape overall for enduring 93 Canadian winters.
There is no insulation in the wall cavities. However, I have blown something like R-50 into the attic and done extensive air-sealing. My heating bills are more than manageable given the age of my house.
I anticipate an upcoming renovation which will include removing the plaster and lathe from the exterior kitchen wall on the northwest corner of the house and replacing it with drywall. I am considering installing rockwool batt insulation in the stud bays and covering it with a vapour barrier. However this modest ‘upgrade’ will be confined to this particular area.
I have two concerns:
1. I will get wetting of the wall owing to air and moisture leakage around the perimeter of the insulated section (bottom, tops and sides)
2. It will result in damage to the brickwork, which will be unable to absorb heat from the interior of the home to assist drying after periods of wet weather.
3. EDIT: after doing some reading on here, it occurs to me that a third concern may be solar vapour drive especially given the western exposure and the permeability (i.e. gaps) in the sheathing boards.
If there’s any significant risk of these things happening, I would
rather just leave well enough alone.
Any input on these points would be appreciated.
GBA Detail Library
A collection of one thousand construction details organized by climate and house part
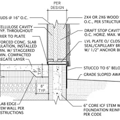
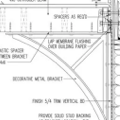
Replies
The plank sheathing will now run much cooler in winter than previously, and the biggest risk is to the sheathing, not the brick, which is much more moisture tolerant than wood.
The plank sheathing will need an air barrier on the interior side, between the sheathing and rock wool to limit the amount of interior moisture reaching the planking. This air barrier should be at least semi vapor permeable to allow the stud bays to dry through the sheathing into the 3/4" cavity behind the brick.
In the original construction the brick veneer didn't necessarily need weep holes & top venting, since there was reasonable drying toward the interior via the empty cavities (and likely semi-permeable plaster & lath & paint.) Installing weeps every 18-24" in the vertical mortar along the bottom (or nearly bottom) course of brick and corresponding vents along the top course would be prudent.
Most framed homes in 1923 were build with full dimension rough-sawn lumber at full 2" x 4" nominal dimensions, unlike the modern milled 1.5" x 3.5" framing lumber. This makes for awkward and incomplete fit for standard batts. The additional side compression is less of an issue than the depth. If that's the case at your house, making the air barrier made of half-inch asphalted fiberboard or 3/4" unfaced EPS would fill up the space with a moisture tolerant fairly vapor permeable material, lowing the likelihood of large compressions or convection paths around the batts.
Hello fellow friend of the maple leaf! I recently did a similar project on a brick veneer house, not as old as yours and with excellent quality brick but no air space behind the brick (filled with mortar) and no weep holes. Also no quality board sheathiing, I had fiberboard covered with 1/4" OSB. I re-insulated my cavities with rockwool and then put 2.5" reclaimed fiberfaced polyiso on the interior side and then strapped it and hung drywall. The fiberfaced polyiso keeps it a relatively vapour permeable assembly allowing drying to the inside. It also eliminates the risky poly vapour barrier and has a way higher r-value. Even in this relatively small 1500 ft² house the loss of a few inches from all the rooms was unnoticeable. I sealed all the polyiso with spray foam to the existing floor and ceiling. Not the ideal air barrier but pretty decent. If I were you, that's what I would do. You could use less polyiso if needed. But just upgrading your batts probably isn't worth the work of tearing apart your wall. And poly vapour barrier, while common in Canada, usually creates a risky assembly and should be avoided. Building technology moved past poly a long time ago.