Partition moisture accumulation
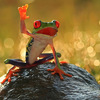
GBA regularly sees cases where some partition {exterior walls/ceiling} design may produce moisture problems and can’t easily be changed. So the question becomes how else can problems be prevented. Answers are things like “reduce interior relative humidity” or “reduce interior pressure”. But these are less than ideal, especially when maintained for long periods. For example, low relative humidity can be uncomfortable. Negative building pressure increases energy use.
I expect that moisture accumulation in partitions occurs primarily during short periods – eg when the wind is blowing hard (causing significant ex-filtration on the leeward side) or when its very cold outside (causing below condensation temperature at the sheathing). So logically, the solution would be responsive to conditions.
Some humidity controls account for outdoor temperature (to avoid window condensation, which is a similar issue). I haven’t seen anything that controls building pressure only as needed to prevent ex-filtration only when it would cause a problem. No question here, just comments about a potential market need.
GBA Detail Library
A collection of one thousand construction details organized by climate and house part
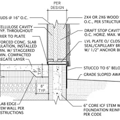
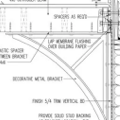
Replies
Wouldn't it make more sense to design exterior building assemblies (partitions are usually walls or ceilings that divide up the interior space) that are robust enough not to be affected by the changes in humidity and pressure every house faces all the time?
I agree with Malcolm here. It shouldn’t be necassary to automatically adjust building pressure to deal with what are basically leaks in the building envelope. Also, if you have a really leaky building, how are you going to change the pressure inside enough to deal with the effects of something like a big windstorm?
It’s better to just build and seal the building properly, and doing that has other advantages too — primarily better insulating to help with heat loss (or gain). Trying to adjust the pressure inside the building or wall cavity with a mechanical system is just putting a bandaid on the real problem which is the leaky wall assembly.
Bill
As stated, this is about cases where the design "can't easily be changed" and "how else". Even in cases where the design could be improved, it's not clear that smart/automatic humidity control isn't sometimes more effective, less expensive and more comfortable than better exterior assembly design.
Even the best air sealing still leaks. With normal ex-filtration, there will be high moisture at those locations. How much and if it causes a problem is largely a coin toss (depends on leak concentration/location, wind, etc). Indeed, some buildings (eg some natatoriums) use pressure control even when alternative designs are an easy option. The building described here used pressure (evidently at a non-optimal fixed Winter pressure) as a more cost effective approach:
https://www.buildinggreen.com/blog/cool-tool-dealing-stack-effect
If you have no other options, then I’d maintain the building under a slight positive pressure all the time. I have to design this way at work for datacenter facilities to make sure no dust enters the “clean” spaces. There are special purpose-built makeup air units that filter and condition (cooling/dehumidifying only) the entering air. It doesn’t take much airflow to maintain a slight positive pressure if your building is reasonably well sealed.
Trying to dynamically adjust the pressure would probably be difficult, but I suppose you could do it with a variable speed fan on the makeup air unit and a pressure sensor in the space. You’d need some logic to avoid oscillations, but I suppose it could be done. I would absolutely NOT ever try to run a negative pressure in the building for any reason. Negative pressure causes all kinds of problems, and tends to suck dirt into places you’d never expect.
Bill
Even with relatively leaky assemblies, if the vulnerable materials (plywood and OSB chiefly) are not located where the moisture will accumulate, and have a good drying path, then there isn't a problem. Almost every instance we see here on GBA where a wall or roof has water damage, the cause was an inherently risky assembly.
What I find puzzling is the number of posters who come for advice in making these assemblies work, after designing a house around their use. My current clients came to me with ideas for a mid-century modern house with a flat roof and minimal overhangs. I suggested something that captured the feel they wanted, but took into account the demands of the PNW climate. There are things we just shouldn't design or build.
>>“What I find puzzling is the number of posters who come for advice in making these assemblies work, after designing a house around their use. “
Probably because they either got bad info originally, or they didn’t listen to good advice from knowledgeable people. I get contracted all the time to correct weird problems with the commerical facilities I work with. My favorite example was a site that would trip a breaker every time power was restored and they went from generator back to utility power. I was the third consulting engineer they called in. What was the problem? Someone didn’t understand the difference between transformer and UPS ratings so battery recharging caused a momentary overload. That and a 130+ degree electrical room! Hot!
Anyway, I think what we see are all the cases where the usual thinking doesn’t work, the weird and confusing cases, and the “it didn’t work I need to fix it” cases. The fix-it is the worst since it costs much more and is far more disruptive than just doing it right the first time.
I like to tell my consulting clients that my job is to anticipate their needs 10, 15 years from now (we plan a lot for expansion over the lifetime of telecom facilities). I tell them that if I do my job right, they shouldn’t be busy because things won’t be breaking.
Bill