Plans Review with a few questions

We are getting closer to building our new home. The preliminary drawings have been completed (links to plans at the bottom). We aren’t exactly building a green house, but over the last year I’ve read an enormous amount of good information from this website and a few others to help guide me in building a more durable and energy efficient house than what is typically done around here (vented crawlspaces and ducts in a vented attic are pretty standard here). We are in a more mild part of the mixed humid climate zone 4 (The Hampton Roads area of Virginia), and that does change the cost effectiveness of some upgrades. I’d appreciate any input on my current plan. My above code goals for the house are to have a continuous air barrier with results verified by a blower door test, a conditioned crawl space, all HVAC ducts inside a conditioned space, and right sized HVAC equipment with mechanical ventilation.
The first floor HVAC ducts will be in the conditioned crawl space. For the second floor, these are the three options I’m considering:
1. Open web floor trusses for ducts (Possibly with spray foam to insulate between trusses on the exterior wall?). Attic floor 2″ oc foam + loose fill on top for R38.
2. Open web floor trusses for ducts (Possibly with spray foam to insulate between trusses on the exterior wall?). Attic floor loose fill (R38) with airtight drywall ceiling.
3. Conditioned attic: Ventilation channel under roof, then loose fill between rafter, then 1-2″ of trgid foam covered in drywall. Small supply register to condition attic air. Will require closed combustion appliances.
Exterior wall cladding will be a premium vinyl siding (cedar shake style). Wall sheathing options are:
1. OSB with taped seams +Tyvek
2. ZIP sheathing (taped) + Tyvek
3. Zip R sheathing (taped) + Tyvek.
All walls 2×4 construction with R13 cavity (Fiberglass batts are typical around here), no vapor barrier, just regular latex paint on drywall. The air barrier will be at the sheathing. Upgrading to Zip R sheathing will add more cost to my mortgage than it will save me in energy costs, at least according to modeling using this website: http://hespro.lbl.gov/pro/ Zip R (R3.6) is over 30 dollars a sheet (and I have to buy it in quantities of 30 sheets at a time). Regular Zip is about 15. OSB is about half that. I like Zip sheathing but I also don’t like trusting the tape to flash the windows and doors. If tape fails on housewrap, the seams are overlapped, giving another layer of security. Then there is the question of if I’m going to use a housewrap anyways, what’s the advantage of using regular Zip sheathing versus just taping regular OSB that’s half as expensive.
For mechanical ventilation, my options include:
1. Supply only, integrated with Central fan(s), preferably with an ECM. Possibly ultra aire ventilating dehumidifier
2. Whole house ERV with dedicated ducts (easier with floor trusses).
3. 2 or 3 spot ERV’s (ie Panasonic FV-04VE1)
Supply only will be good in the summertime, but I worry about humid indoor air in the wintertime being force through the walls. I really like the ultra aire ventilating dehumidifier, but they are expensive and with an HVAC system on both floors, I’d probably have to buy two. How much more expensive are AHU with ECM’s? I like balanced ventilation, but I’m not sure if the cost of an ERV is justified in my climate. I do plan on hiring a third party to do the HVAC design to ensure I get a proper manual J.
Windows will be Anderson 400 series with an energy star rating.
First floor plan: http://s18.postimg.org/m3c1ychmf/1st_Floor.jpg
Second floor: http://s18.postimg.org/m4lzrrjg7/2nd_Floor.jpg
GBA Detail Library
A collection of one thousand construction details organized by climate and house part
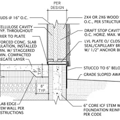
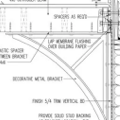
Replies
On the attic floor, skip the 2" opens cell foam, that's 70-80 cents per per square foot of R7 that could be bought for 40 cents/foot with 2" more cellulose, for a net increase in total insulation depth of 0". You need to air seal that plane, but it doesn't take 2" of foam over the whole shebang to get you there. Putting the ducts & air hander in open trusses or soffit structures below the insulation works.
R38 is below IRC 2012 code min for zone 4A. The price difference between R38 and code-min R49 cellulose is probably going to come in something like 20-25 cents per square foot, since the set up and break down time is the same. It adds another 3" to the total insulation depth, easily accommodated in the energy heel roof truss design.
Insulating & air sealing at the attic floor is going to be half (or less) the cost of doing it at the roof deck.
A 2x4 R13 wall is also below IRC 2012 cod min for zone 4- can we at least shoot for IRC 2012 minimums, even if your state is currently at IRC 2006 or earlier?
http://publicecodes.cyberregs.com/icod/irc/2012/icod_irc_2012_11_sec002.htm
A 2x6 24" o.c. studwall has the same amount of board-feet of lumber and same structural capacity as a 2x4 16" o.c. wall. Since there is even less labor (fewer boards to cut and install) by all rights it should be a cost savings, or at worst, break even. The only cost uptick is in the insulation. R23 rock wool would be preferable, but R21 fiberglass is fine, and may be cheaper. A 2x6 24" o.c. R23 wall has about the same performance as a 2x4 R13 wall with ZIP-R sheathing, but should come in for less money.
The whole point of Huber ZIP is that it doesn't need the housewrap. If you caulk the framing to standard OSB or plywood it will be as tight or tighter than taped ZIP. If you're going with the housewrap, use the cheap stuff for sheathing, and spend part of the savings on air-sealing the sheathing layer as you go. With a power caulking gun and a case of acoustic sealant caulk you can caulk every stud bay to the framing in an afternoon. Be sure to lay bead of caulk under the bottom plate of the studwall, and between doubled-up top plates.
Whole house dehumidifiers are usually a bit like swatting flies with a 10lb sledgehammer. Combining dehumidification with ventilation is usually a mistake too, since you need ventilation much more often than dehumidification.
With inherently back ventilated vinyl siding you don't need or want an interior side vapor barrier in your climate zone, the"Vented cladding over wood structural panels" exception : http://publicecodes.cyberregs.com/icod/irc/2012/icod_irc_2012_7_sec002_par025.htm
But pressurizing the house with a supply only ventilation scheme would be a mistake, since it would raise the wintertime moisture loading along the exfiltration path. Either exhaust-only or balanced HRV/ERV would be lower risk. As long as you don't use atmospheric drafted combustion appliances indoors, exhaust-only works fine. Running bathroom exhaust fans under occupancy/vacancy sensor switch control with a 30 minute time-out and getting religion about using kitchen exhaust fans whenever you're cooking ANYTHING will usually be enough to keep humidity bounded in winter, unless you're keeping a tropical fish collection with a dozen tanks. The tiny Panasonic ERVs might be useful for sleeping quarters, but they need not run all the time, only when the room is occupied.
It's often better to hire energy nerds for the load calculations rather than HVAC contractors, since they make their money and reputation on the accuracy of the results, whereas HVAC contractors have some incentive to put a thumb on the scale and just oversize the equipment a bit "just to be sure", taking less care on load calculations.
Michael,
Dana gave you good advice. You should certainly upgrade your attic insulation and your wall insulation to at least code minimum levels; more would of course be better.
Research has shown that central-fan-integrated supply ventilation systems work very well in your climate zone, as long as (a) you understand how the system works, (b) you don't overventilate, (c) the system includes a motorized damper on the outdoor air duct and an AirCycler or FanCycler control, and (d) the system is commissioned by someone who knows what they are doing. In other words, verify the air flow once the equipment is installed.
For more information on ventilation systems, see Designing a Good Ventilation System.
"The whole point of Huber ZIP is that it doesn't need the housewrap. If you caulk the framing to standard OSB or plywood it will be as tight or tighter than taped ZIP. If you're going with the housewrap, use the cheap stuff for sheathing, and spend part of the savings on air-sealing the sheathing layer as you go. With a power caulking gun and a case of acoustic sealant caulk you can caulk every stud bay to the framing in an afternoon. Be sure to lay bead of caulk under the bottom plate of the studwall, and between doubled-up top plates."
From this article: https://www.greenbuildingadvisor.com/blogs/dept/musings/airtight-wall-and-roof-sheathing :
"Rosenbaum sprinkled his presentation with interesting observations and useful advice:
“You could have the builders caulk the sheathing when they put it up. The only problem with that is I can’t tell if they did it or not.”
“I don’t use the Huber Zip System without a housewrap, and I don’t use foam as a WRB. I do not believe that housewrap is an air barrier.”"
His first point is one reason I'd rather just tape the OSB. His second comment, which I've seen a few others express the same thing, brings up the question of why use zip in the first place, rather than taped OSB? Your answer seems to be that it doesn't make sense. So then why are they doing it? Is there some other advantage to taped zip covered in a WRB versus taped OSB?
Thanks Martin, I recently readt "Designing a Good Ventilation System". I'm still a bit confused by this part:
"Some builders worry that a supply-only ventilation system (for example, central-fan-integrated supply ventilation) won’t work in a cold climate, because the ventilation fan will drive interior air into building cavities where moisture can condense.
This worry is needless. As energy expert Bruce Harley explains, “The upper portions (walls and ceilings) of every home — typically most of the second floor in two-story homes — already operate under positive air pressure in cold weather, due to the stack effect. The relatively small airflow of most supply-only ventilation systems (75 cfm to 150 cfm) will have little effect on this situation other than to shift the neutral pressure plane down slightly, in all but the very tightest of homes. … In cold climates, I believe that distributed, supply-only ventilation such as that supplied by a ducted distribution system controlled by an AirCycler, or other ducted low-flow supply ventilation, is vastly preferable to single or multi-port exhaust-only systems, except in extremely tight homes (in which case balanced supply and exhaust ventilation is the best choice).”
One one hand, we are told we need to build an airtight enclosure, not just for energy efficiency, but because 10 to 100 times more water can enter a wall assembly through air leaks than through vapor diffusion. On the other hand, the above quote says it's just find to add an additional 75-150 CFM through the walls. The shift in pressure plan isn't the concern, it's the extra air. Is the amount of water in 75-150 CFM of air not enough to be a concern? If it isn't, (setting aside energy concerns), why is it so important to seal air leaks to keep moisture laden air from passing through the walls?
Michael,
I'm not sure that I understand your question.
We perform air sealing work for two reasons: to lower our energy bills, and to limit the amount of moisture-laden air that might contact cold surfaces. It makes sense to do this.
However, that doesn't mean that our homes are 100% airtight. Nor does it mean that the stack effect and wind won't overwhelm the effects of our ventilation systems.
Dana, A minor point: Why would you caulk between the top plates on walls if the pressure boundary is the sheathing?
Correct me if I'm wrong on any of these points, but this is how I understand it. We ventilate because houses are tight and natural infiltration and exfiltration is insufficient to maintain IAQ. As you said, we air seal to decrease energy usage and to limit the amount of moisture-laden air that contacts cold surfaces. If we ventilate, we are by definition increasing the amount of air passing through the structure (in a non balanced system). Even if wind pressure and the stack effect change how the house is pressurized, are we not still putting more air through the structure with non balanced ventilation? Am I way off base here? I hope that makes sense.
Michael,
Here's my point: because of the stack effect and wind, all walls, ceilings, and floors are subject to air movement through the assembly. As long as any moisture that collects in these walls as a result of this air movement can be safely handled -- through hygric redistribution, evaporation, diffusion, or ventilation drying -- then the assembly will be safe. You want the rate of drying on an annual basis to exceed the rate of wetting.
We know how to build assemblies that achieve this goal.
As I wrote, most of the air movement that occurs through our assemblies occurs due to the stack effect and wind. The very small contribution made by unbalanced ventilation systems is not enough to matter.
Dana,
"A 2x6 24" o.c. studwall has the same amount of board-feet of lumber and same structural capacity as a 2x4 16" o.c. wall. Since there is even less labor (fewer boards to cut and install) by all rights it should be a cost savings, or at worst, break even. The only cost uptick is in the insulation. R23 rock wool would be preferable, but R21 fiberglass is fine, and may be cheaper. A 2x6 24" o.c. R23 wall has about the same performance as a 2x4 R13 wall with ZIP-R sheathing, but should come in for less money."
As I've studied up again on Advanced Framing/OVE, I'm not so sure. My builder hasn't built anything with 24" OC walls, and it's unlikely his framers have either, as it's not common in this area. I'm sure there is a learning curve, which means more time, which means more money. My builder doesn't think the inspector would approve anyways. Might take some convincing. We do live in a Hurricane prone area. Then there is the issue of siding, we may be required to fasten it every 16". Then we have to deal with deeper windows, and increased cost for 5/8" drywall. So maybe in theory 2x6 advanced framing is cheaper or break even compared to 2x4 16" OC, but in practice I have my doubts. I'm not a builder, so I really don't know, but I will discuss it again with my builder and see. I do appreciate the response and information I've received here.
I would ditch the crawlspace and put in a slab, it will never be cheaper to do it then now, and your house will be a lot nicer and cleaner
Also you drastically reduce radon concerns with a solid floor.
The crawlspace will increase indoor humidity which your system has to handle, rust your appliances in contact with the dirt (in time) and take away what would be usable space with a proper floor (even if its not deep it can still be used for storage).
Michael, I am building in Knoxville and just posted for some input under a different topic. I find that most of the articles/case studies out there are for much more extreme cold weather environments than I (or you) are in. I'm planning on using OSB and tyvek. I've got a lot of reading to do on ventilation to make sure I know enough not to get taken. Luckily, there have been quite a few experimental houses built by the good researchers in Oak Ridge and I have found the HVAC company they used. Good luck to you.