Please advise on this new type of basement construction

I’d like to get some feedback on a new type of basement construction I came across recently.
Background: I signed up for a GBA account two or three years ago as I began planning my eventual retirement home. I don’t participate much but I am a regular reader. I originally was interested in ICF due to being in west Texas and the chance of tornadoes. Technically I’m in zone 3B but just a stone’s throw from 4B. I will assume 4B for winter and 3B for summer when planning the house. I will still consider ICF but after discussions with the only local builder I’ve found who uses it, it looks like the cost premium will be too much. So, I am also considering a wood frame / brick house built to Florida type hurricane standards along with a basement. While checking out homes being built in the area, I came across a new type of basement construction I had not seen before.
They start the home construction by trenching walls for the basement. The trenches for the walls appear to be about 6” wide. After the trenches are dug, they insert rebar in the outer third of the trench leaving enough room for a 2” x 4” top plate to sit on the wall flush with the interior side. The concrete walls are then poured. Then the basement is dug out and a concrete floor is poured. The rebar is then bent 90 degrees so it can be integrated with the slab when poured. A treated 2” x 4” top plate is installed on top of the basement walls. Next, 16” trusses are installed on top of the basement and the opening for the stairs is framed up to be flush with the slab when poured. The tops and sides of the trusses are then covered with ¾” plywood. The plywood is covered with tar paper. The slab is then poured (including over the basement ceiling). I’m not sure of the construction details beyond what I’ve shared but the basement ends up fully finished.
The size of these types of basements is restricted such that the exterior wall of the basement must be at least 5’ to the inside of the exterior wall of the house. Apparently, this mitigates moisture issues. We only get around 15” of rain a year. The joke is that you ought to be here the day we get it.
Questions:
1) Overall impression of this type of basement construction? Do you see any particular issues?
2) Would you use Drylok on the interior wall before finishing?
3) In my climate, should insulation be installed under the basement floor before pouring?
4) How would you finish this type of basement? Wood frame walls? What type of insulation? Would you insulate the ceiling of the basement?
Thanks for your time.
DC
GBA Detail Library
A collection of one thousand construction details organized by climate and house part
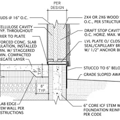
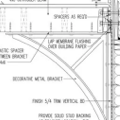
Replies
D.C.,
If I understand your description accurately, this method has the following characteristics:
1. Instead of using conventional concrete forms, this method uses the dirt on the two sides of a trench as concrete forms for basement walls.
2. A conventional wood-framed floor is installed on top of the basement walls, and then a concrete slab is poured on top of the plywood or OSB subfloor.
Is this an accurate description of the method?
If so, the biggest problem is step 1. Very few areas have soil characteristics that allow deep, narrow trenches to be built without the sides of the excavation collapsing. Moreover, most homeowners don't want the bumpy walls that would result from using soil as a concrete form.
@Martin
Yes, you understood my description accurately. We're one of the largest cotton producing areas in the country and apparently what makes our soil good for cotton also makes it good for this type of basement construction.
The concrete walls are not left exposed. Rather, they enclose the room with sheet rock and tend to carpet the floor and use this room as they would in any other location of the house.
If I build such a basement, it would be a finished basement (likely a multipurpose room but possibly a media room). I just want to make sure of the proper details that need to be incorporated after the walls are poured and to see if there are any red flags on such a construction method which led to my initial questions.
By the way, it would be helpful if GBA could make the box you type responses in a little larger. The current size isn't conducive to easy review and edit before posting.
Thanks much for the help.
DC
In most browsers the size of the response box is scalable by clicking and dragging the lower right side corner.
DC,
So the basement is left full of dirt, and the dirt in the center of the basement is only excavated AFTER the concrete walls have been poured?
I can't imagine any advantages -- but I can imagine plenty of disadvantages. Who wants to operate a backhoe to clean out the hole when there are four concrete walls in the way?
@Dana - Thanks for the box dragging tip. Worked great.
@Martin - Yes. Walls are poured, then dirt is excavated, then basement floor is poured. They claim its a less costly way of building basements.
I suppose the advantage would be avoiding the need for construct forms, but I too can see several disadvantages that would seem to far outweigh the one advantage of not needing forms:
1) The soil would need to be the proper consistency to hold the form of the trench.
2) The trenching machine would need to be run on a very precise path to match the building design. Any excursion to the inside during the trenching would produce an irregular bulge in the poured wall. And it would be impossible to correct the defective trench before pouring the concrete.
3) Any encounter with a sizeable rock during trenching would pose an issue of either removing the rock without significantly disrupting the trench form, or leaving the rock in place as an irregularity in the poured wall.
4) The trencher would have to run on a perfectly level surface in order to produce a trench with plumb walls and consistent depth.
5) There is no way to widen the bottom of the trench to produce a footing for the wall. That raises a question of how this could comply with the code.
6) There would be no way to incorporate an exterior drain tile.
7) There would be no way to check for, and seal off intersecting subterranean drainage passages that might happen to intersect the trench and feed water against the wall.
8) The poured concrete might be dehydrated before it can properly cure because the thirsty soil might suck the water out or the concrete.
9) The bottom of the trench is likely to have a shallow layer of pulverized soil left by the trencher, so pouring the wall will place concrete on soil that is likely to settle slightly.
10) Compacting the concrete with a vibrator will likely result in the vibrator contacting the soil at the sides of the trench, dislodging some of that soil, and contaminating the concrete in that location.
Ron,
I agree with you. I'm wondering if this question is a prank, or based on a misunderstanding. I have never seen a machine that could dig a plumb, 6-inch wide trench, 7 feet deep. It's hard to imagine the backhoe or trenching machine that could accomplish such an excavation.
Martin,
It's not a prank. If you think it's a prank, get GBA to send an email to my login address and I'll give you my name and phone number so we can discuss it. I could tell by your previous responses that you were incredulous at my description of the basement. I stumbled across such a basement in progress by accident when checking out new homes in the area. Then, when I mentioned it to a friend of mine, he told me that was the way they constructed his basement. I don't have photos of the basement I saw going in because its too far from my house to go out there every day but if I get a chance at another one I will take photos. I'll ask my friend if he has photos of his basement construction he will share.
DC
D.C.,
I'm sorry if my reference to a possible prank seemed disrespectful, but I'm still incredulous. Here is my latest question: if this trench is filled with concrete, what type of concrete forms are used to bring the concrete wall above grade? You can't just stop the concrete wall at grade and switch to wood.
Ron,
1) The soil appears to be fine for this type of construction. Apparently we have the right mix of clay below the topsoil. My friend said there were no problems with his basement.
2) I did not get a chance to see the trencher in action. The walls appeared to be reasonably square to the world and I did not see bulges anywhere after excavation of the interior soil. As expected, the interior walls were rough and not at all smooth.
3) Rocks are not a problem where this particular basement was built but there are areas of this county where rocks would be a big problem and so this method would not likely work.
4) They did grade the lot and level the basement area before trenching.
5) This was a concern of mine as well but these walls are not load bearing walls for the house. Does that make a difference?
6) 7) They told my friend such a drain was not needed. We don't get much rain and the requirement to keep the basement walls at least 5' inside the exterior walls of the house is supposed to mitigate moisture intrusion issues.
8) Could they use a slower curing concrete mix to mitigate the potential problem?
9) I didn't get to see them make the trench or do the pour. In fact I've not seen any of the actual construction because Sundays were the only day I could travel to the site and no one worked then so all I got to see was the progress. I suppose its possible they could vacuum the loose soil if it truly posed a problem.
10) Not sure if they vibrate the walls and if so, how they deal with the potential problem you describe. I'll ask if I can find the right person.
Martin,
They hadn't gotten that far the last time I was out there. I wish I had some photos. The last time I was at the site, this is the way it was left. The walls had been poured, the soil excavated, the basement floor poured. The rebar that had been inserted into the walls had been bent over to the exterior side of the basement to tie into the future slab. A 2 x 4 treated top plate had been installed on the top of the walls flush with the inside of the walls. 16" trusses were then installed on top of that top plate and an opening for the basement stairs was framed. The trusses and framing were then sheathed with 3/4" plywood. Tar paper was stapled to the plywood. The top of the opening for the basement stairs was about 6" above the top of the trusses. I was told a slab would be poured directly over the trusses and end up flush with the framed opening for the stairs. There was no extra framing installed at that point to account for the difference between the top of the basement walls and what I would presume to be the bottom of the slab. They had not started plumbing or framing for the slab yet so I'm assuming the slab framing crew will take care of the remaining forms necessary and that this will be part of the slab pour. But I'm just speculating and will try to find the correct answer to your question.
DC
DC,
I understand your responses, and I agree that the disadvantages I mentioned are not necessarily showstoppers. Even all of them together might not outweigh the advantage of not needing forms. If the soil is known to work and not have disruptive rocks or underground water movement, it would probably be possible to run the trench accurately enough. I suppose the trencher could be steered to follow a string line. I do know that trenchers can cut a trench with very precise walls with a surprisingly smooth surface. The proper trencher and operating technique would be needed, but someone specializing in this approach might have the operation perfected.
I don’t quite understand how the corners would be made as it would seem that one trench intersecting another might be hard to control in a way that keeps the trench form perfect. I would think that some loose soil would need to be vacuumed up to clean up the bottom at the corners.
Some of my listed concerns might not even apply such as the inability to install an exterior drain tile. My item #5 would be my biggest concern. How is it that basements using this approach do not have load bearing walls?
On the face of it, it sounds like an approach fraught with problems for general application in all sorts of soil conditions and trencher technique. But I suppose it is possible that specialized application in specific areas with ideal conditions might render it successful and worthwhile. I don’t know how much it saves by avoiding the need for forms.
My only question ... WHAt's the point ??
This has to be the most ridiculous way of making a concrete fondation that will be used for a full basement ...
Just dig it all out at once, get some proper concrete wall team or better use ICF if you wish to save on labor.
I wonder how good is the concrete poured directly into soil trenches that sucks all and every water ASAP out of it ...
Building a house is about getting it to last ..else get a tent or a motorized home .
Overall, even if this approach could be pulled off with reasonable success, I cannot see how it would be cheaper than just using forms for the pour. The pre-grading for a trencher run, the precision trenching, and the soil removal inside after pouring will surely add cost compared to a conventional approach. And also, it seems that there would be a high probability for complications that make it less than a success.
Original poster DC says that the walls are not load bearing. How can basement walls not be load bearing?
@Jin - Its not a full basement
@Ron - I was told the basement walls did not carry the structure load for the house. The two finished examples I've seen both had the basement situated in such an area of the house that no load bearing walls for the house were above the basement so I think that's what they meant when they told me they didn't carry load. The basement walls do have to carry whatever load is on the trusses due to the slab being poured on top. But I wonder once the slab is cured, what weight is really carried by the trusses and the basement walls?
Also @Ron - They wouldn't be building this way if it wasn't cost effective. Now, whether its a sound method or not I don't know, that's why I'm here.
Here is some more info for you guys:
As I mentioned before, these are not full basements. I was told last night that they are considered more as "basements as storm shelters". Most builders in the area appear to have embraced the method. It has been signed off on by the city's building inspection department.
Here is a link to a local builders blog archive where he has some photos of the process:
http://jwlubbock.blogspot.com/2010_11_01_archive.html
Scroll down to the bottom where you will see a photo of the trencher in action. Then scroll up and you will see the trenches before rebar. The next photo up shows the trenches after rebar and concrete. A couple of photos above that you can see the backhoe in operation followed by the basement after excavation is completed. The next photo shows the trusses being installed.
Here's a link to another post by the same builder with a better photo of the trenches after concrete:
http://www.jwlubbock.com/Wordpress/?p=459
And here's another link to yet another post by that same builder with a better photo showing the trusses:
http://www.jwlubbock.com/Wordpress/?p=448
Some other info I discovered in conversations last night:
Codes here do not require basement insulation but I'd still like to know if it is recommended in my climate.
As far as perimeter drainage the code says this "A drainage system is not required for a basement wall footing where the excavation for the basement wall does not result in a soil disturbance closer than three (3) feet to the exterior roof drip line and there is no evidence of groundwater infiltration."
In response to Martin's question above regarding how they form to bring the walls above grade: My friend said when they did his house, they regraded after the basement framing was complete and then, as I speculated, the framers for the slab incorporated the basement into their framing and the rest of the concrete was poured along with the slab. He is going to look for photos that I can share.
I tried to get some detailed drawings of the method but have struck out so far.
DC
DC,
It sure looks like the grade is too high. The grade is even with the OSB rim joists. Rot ahead!
.
@ Martin
I asked my friend about that last night when we were discussing this method. He said when they built his basement that no soil ended up touching the wood framing. Once the framing was complete, they covered everything with 3/4" plywood, then tar paper and ultimately concrete. If they keep the basement exterior wall inside 5' of the house exterior wall which puts the basement around 7' inside the roof drip line, is there really any way moisture can get to this framing (absent a leak from above)? Our water table is not high and we have no hills to deal with when considering drainage.
DC
Maybe it would help to think of this as a concrete box with a concrete lid. They pour the walls of the box first, then pour the bottom of the box, then frame the inside, then put a concrete lid on the box. This "lid" ends up being incorporated into the slab. The entire basement is encased in concrete except for the stair opening. Another guy I talked to said this: "Don't think of it as a basement you're building a house on top of, think of it as a storm shelter that gets put under the slab".
DC
When it is finished, where is the elevation of the land grade touching the concrete outside in relation to the lowest elevation of the wood on the inside?
Ron - I'm not sure. Are you thinking they need some sort of moisture barrier where the "lid" meets the top of the wall? I think typically the slabs are poured 12" thick at the edges and for about 1' inside before sloping up to a middle slab thickness around 6". The lowest elevation of wood on the inside would be the bottom plate of the interior walls where it touches the basement floor. Or, were you referring to the bottom of the trusses?
DC
DC,
I was just wondering about the concrete always being damp from the ground and wicking that moisture to wood contacting the interior, but I don't know what the code allows in your area. I am just catching up with your explanation of how this underground space relates to the whole house.
This would be a slab on grade with the slab bearing the load at the edges, and then this poured basement would be considerably smaller than the slab. The framing added to the interior of the basement walls supports framing over the top of the basement, and that framing supports the slab as it spans over the basement.
So this might be a 10' X 10' basement under the center of a 20' X 20' slab. I assume that there is no ground frost in the winter in your location.
What exactly is the function of the basement? You could just place the furnace, water heater, etc. above grade. Is the main reason for the basement to function as a storm shelter?
Yes, this particular basement design is to function as a storm shelter (why I'm considering one) but it ends up finished as a bonus room. It can be a multipurpose room (my plan), media room, kids room, etc. It is a completely finished space. No mechanical equipment will end up in the space. It's basically another room of the house.
We don't build a lot of basements in this area. I'd say less than 5% of new homes and less than that of existing homes. There are homes with full basements but even those end up completely finished and are unlike typical basements in the northeast. They are mostly just another level of living space and don't usually contain any mechanical equipment.
I don't know how damp the concrete walls will be with this type of construction which is one of my concerns. The codes don't require drainage on the exterior walls of basements until those walls get within 3' of the roof drip line. We're pretty dry out here and usually beg for rain. The soil drains well in most places and with most builders keeping these basements 7' or so from the drip line I'm hopeful it won't be an issue. My friend's builder kept a large air gap between the finished wall and the concrete wall and circulates conditioned air through the cavity. I'd still like to know if Drylok or some other moisture barrier would be recommended on the inside of the concrete walls and the basement floor.
The cost of this is interesting to me and I don't know how it compares with other basement construction. I was told the cost to add this type of basement would be about $75/sq.ft. You can easily build a home here for $100/sq.ft. including land and all utilities. I'd say the average for a good builder would be in the $110 - 120/sq.ft. range but you can certainly spend more for a high end home.
DC
Kudos to you for wanting to incorporate a storm shelter into your home.
Whatever money saved using this method would not be enough to alleviate my concerns about its longevity. But I'd prefer to look at either conventional forms with a floor deck system, or ICFs with an Insuldeck-type product.
Thanks Mike. Your method does add cost say the builders but it gives the opportunity to install exterior drainage and waterproof the exterior walls. However, since I'm planning a typical (for around here) small single room basement, the builders generally don't add exterior drainage or waterproofing to the exterior walls unless the exterior basement wall is within 3' of the roof drip line. They say its really not needed.
I can be a skeptical person but frankly I am amazed at the amount of skepticism about this method on this site. It appears that most people have simply pictured this method in their own backyards and immediately concluded "it can't work". Locally, engineers, architects, builders, building inspectors, codes administrators, and insurers have all signed off on the method. It appears to be here to stay and I've found the method has been around for about 5 years even though I just recently heard about it.
I appreciate all the good dialog above but am disappointed my questions have not been answered. I guess I just haven't done a good enough job explaining the method and I know I am missing some details. Or maybe its just the opposite. Maybe I've been too wordy and people aren't taking the time to wade through everything and understand the process.
DC
DC,
What questions do you have at this point in the conversation? I think I fully understand the basement you have described. I think the application viability would depend on the climate conditions, and would work fine in your climate. But a lot of people reviewing your information are in different climate zones, and will be visulaizing your concept in their climate. For instance, I would conclude that the basement concept you describe would be unsuitable in a northern climate with ground frost. It would be possible to build, but the exterior of the house would need full depth frost footings.
So by the time you build 42" load bearing frost footings, it would make more sense to simply extend them to full basement depth rather than to build the inboard basement that you describe with full depth, non-load-bearing walls.
Upon first consideration of your concept, I was considering it in terms of universal application, and could see problems. But for your climate zone, I don't see any reason why it can't be viable. So I guess it would just depend on cost and whether it fits your house concept.
D.C.,
I know for a fact that here in Vermont, we can't have an OSB rim joist that is even with grade. Perhaps your dirt is different in Texas. Wrapping the rim joist with anything you please -- asphalt felt, polyethylene, or peel-and-stick -- wouldn't be enough to prevent splashback and wicking from destroying the rim joist in short order. Here, the lowest wooden components of the house have to be at least 8 inches above grade -- period.
This method appears to me to have so many disadvantages, and so few advantages, that it isn't worth considering. But be my guest! It sounds like you're going to try it.
Martin,
I am not sure what that OSB in the photo is doing, but I suspect it is just temporary as part of the setup for continued pouring. As I understand it, the slab will cover the basement opening and continue outward past the basement walls by at least five feet all around. So there is no exterior landscape grade adjoining the outside of those poured walls. The slab sits atop the poured wall, so there is dirt up to the top of the wall and bottom of the slab. The wood framing is to support the slab as it spans across the basement walls.
I would question the use of untreated lumber in that support framing near the top of the wall because moisture can wick through the concrete, but I suppose it would be quite dry under the slab, so maybe there is no issue with rotting of the wood on the interior side of the concrete.
I think the confusion is with saying basement.. I thought of a full basement equal to the foot print of the main floor. Instead its a storm shelter in the middle of the house. The slab on grade is poured around the opening for the storm shelter. I would assume there is a moisture barrier to protect the wood when the slab it poured.
@Martin - I don't think you fully understand the process. Ron was right. In the photo you posted, the wood trusses get covered with plywood (or in that builder's case OSB), then covered with asphalt felt or similar and then gets completely covered with concrete.
What you end up with is a complete concrete box with an opening for stairs. There is no wood left exposed to the dirt. There are joints in this concrete box due to the different pours (joints where the floor meets the original walls and joints where the slab/cap meets the top of the original walls).
If you design the slab to be strong enough, the wood you see in the photo could actually be removed after the concrete cures.
I haven't made the decision to try this yet but did come across an existing home for sale that left this type of basement unfinished. Let's tackle my questions from that point of view. Assumptions: Existing home, this type of basement construction, exterior of basement walls are 7' inside roof drip line, well drained soil, proper grade of yard, no water table issues, basement is unfinished. See my original post for unanswered questions 2, 3, & 4.
Martin, I know you are a busy man but I value your input and I don't think you've taken the time to fully understand this method before dismissing it so quickly. Would you please reassess?
@Ron - Thank you for your comments and taking the time to understand the process. I agree with you that it seems viable for my area but if I go this route, I want to carefully think through any ways to circumvent future issues and to just make the process better.
DC
D.C.,
Your wrote, "Martin, I know you are a busy man but I value your input and I don't think you've taken the time to fully understand this method before dismissing it so quickly. Would you please reassess?"
D.C., I have done my best to understand the method based on the information you have provided. You may well be right that your understanding of the details and advantages of the method is better than mine. After all, you're there looking at it, and my understanding is based on your description.
Your opinion matters more than mine in this case, because it's your house. So if you like the method -- go for it.
I guess the prank is on me. Since Martin is unwilling to assist, does anyone else want to take a shot at questions 2, 3, & 4 in my original post?
Thanks,
DC
DC
It seems pretty clear that no-one here has direct experience of this particular construction you are describing, while your local builders do. I suggest you address these questions to these local builders, review built examples and research any history of problems that may have occurred going back through several years and if possible some extreme weather events. If you can satisfy yourself there is a history of reliability with this construction going back a number of years and if the space so formed is going to be useful to you, go for it, taking experienced local advice on the questions you pose. If not, don't.
DC
As I understand Drylok, it is a waterproofing coating that is said to be breathable. If I were building the type of basement you are considering, in your climate, I would make sure that no waterproofing were necessary. Either none would be needed because the site would not pose any water issue, or I would install a drain tile on the interior side of the walls, under the slab. In any event, I would not rely on any type of waterproofing coating on the walls if water intrusion were possible.
However, even if water intrusion were not an issue or were controlled by a drain tile, the ground will nevertheless have moisture content that will wick through the concrete. This type of moisture is of the nature of dampness rather than flowing water. The Drylok claim that their coating film is "breathable" sounds like it would not prevent the transmission of ground moisture dampness. So considering that Drylok does not prevent the transmission of dampness, and would not be needed to stop actual water intrusion (because I would avoid that by the means mentioned), I would not use it. Instead, I would use a liquid film application that is not breathable, or a polyethylene film.
If I understand your basement concept, there will inherently be wood framing on the inside of the walls which will support the ceiling trusses and bear on the floor slab. I would think you would just use that for the interior finish wall system. I don’t know how much heating your house will require in your location, but assuming that heating will be needed, I would insulate the interior side of the basement walls with extruded polystyrene foam board. I would give some thought to how that foam gets integrated with the stud wall framing and the concrete wall. If polyethylene film were used against the concrete, you would have to screw the foam to the concrete. The foam board itself would act as a fair dampness barrier, so maybe a separate film barrier would not be needed.
I would apply the same insulation and damp proofing objective to the floor slab by the use of the same foam board plus an underslab vapor barrier which is an ultra-heavy duty film product. My objective would be to 100% isolate the concrete floor and walls from the interior of the house in terms of ground moisture transmission by capillary wicking. I would also extend this damp barrier to the ground level slab in the area between the outside of the basement and the outside of the house.
If you are going to use the basement as finished living space, I would recommend heating it. Whether or not you insulate the ceiling of the basement depends on whether you desire to have the ability to isolate the basement from heating at times. If you intend to heat the basement whenever the rest of the house is heated, I see no reason to insulate the basement ceiling. The reason to have the ability to isolate the basement from heating is to save energy if the basement is not being occupied. So insulating the basement ceiling is a judgment call depending on your contemplated use of the basement space.
Ron - Thanks much for your helpful comments. That is the kind of information I am looking for.
James - I do intend to talk to builders and others involved in this process (more than I already have) but I wanted to be as educated as possible first.
One other compelling feature about this type of construction is that I can reduce my above grade footprint by moving a room under the slab and gaining a storm shelter in the process at no additional cost.
I'm not sold on this construction method yet and I'm not trying to sell anyone else on it. Just trying to learn as much as possible and I appreciate those of you who took the time to try and understand the process and offer your thoughts.
DC
I think Martin has gone above and beyond in trying to help. You've described a system that seems fraught with potential problems, various of which have been pointed out - burying wood encased in various other things is typically not a good idea. There must be more data available locally since people are building that way, so please share more if you have it.
Not sure what you think he should be doing differently.
Dan - no wood is getting buried. All wood ends up on the inside of the basement room which has walls, floor and ceiling of concrete. The method of forming the concrete box is what is unconventional but in the end, that's all it is - a concrete box which needs to be finished out to make it a useable room.
DC
This is an old post, but I also feel this is a ridiculously complicated way of adding a small basement to a house. Seems like an experienced wall pouring company should open up a branch in this location.