Please help me figure out how to best insulate this space – prior three seasons room

Good Morning,
I live in Madison, WI which is right on the edge of zone 6 for climate.
I thought I had insulating this area all figured out but upon reading that XPS is both terrible for the environment and loses R value I am back to square one.
I have three areas that need to be insulated;
1 – Ceiling, which is 2×12 24OC and will be vented with chutes. Chutes have not been installed yet but I had planned on 2″ foam for the chutes. I hadn’t initially planned for air permeability into the chute area but now I read that I should be. I had gotten a quote for spray foam @ 7″ but that’s out of the budget at $4,700.
2- Walls, as you may expect this room is full of windows, and almost solid framing! Very little room for insulation. I wanted to either add 1″ of rigid foam on the inside or outside of the framing and do jamb extensions. Inside appears to be my only real option because I don’t have room in my 2×4 walls to support enough insulation for the proper ratios to avoid condensation.
3 – Floor, this room is 6′ off the ground. Construction is strange and they are 2x6s 12″ OC so tons of thermal transfer through lumber. It’s also built ontop of decking boards so there are lots of holes and slots for air to move through from bay to bay. I had planned to spray foam this due to the very challenging am0unt of gaps and cracks, then ideally do 1″ foam board on the outside of the framing which would then be covered with something more permanent like white aluminum. Hindsight being 20/20 I would have put down foam under the subfloor. It would be pretty difficult to do this now.
I know there’s a lot to digest here, and I appreciate links to any articles that may help me navigate this. Comfort is important but it seems to me that the biggest culprit here is usually air leaks. The room is pretty big, about 9×30.
If it matters the house is forced air NG, and built in 1969. The rest of the house is tremendously leaky, but one step at a time.
I’ll put some photos up later today for context, for some reason I can’t seem to find them.
GBA Detail Library
A collection of one thousand construction details organized by climate and house part
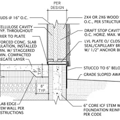
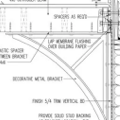
Replies
What kind of roof is this? Pitched? Flat? Not flat, but almost flat? Venting doesn’t work well if the roof is flat or close to flat, so keep that in mind. Assuming you have enough pitch for venting to work, you can use 1/4” waferboard to build vent chutes, since it’s cheap and relatively easy ti work with. You can probably get close to R38 worth of batts in the rafter bays after a 1” vent space, but I’d try for 1.5” of vent space if possible. It’s easy to put in these baffles using a finish nailer and some 1x2 furring strips as spacers. Put some polyiso across the underside of the rafters if you need more R value, and you should really have more than R38 if at all possible.
Note that XPS doesn’t lose value with temperature, but it does with time as it ages. It will eventually stabilize at near the same R value per inch as EPS. Most polyiso does lose R value in colder temperatures, but it too gets down to around the R value per inch of EPS in extreme cold, and it does much better all the rest of the time. If you use polyiso on the interior side, you won’t have any change in R value in cold weather since the polyiso will be on the warm side of the assembly.
If you have the ability to build a vented assembly, that’s much preferred over a non-vented roof. I would only consider spray foam here if you have no other option except to build an unvented roof, in which case I would use closed cell spray foam.
I’m not clear on the strange framing for your walls. Can you provide s drawing or pic? Regarding insulation ratios though, if you can’t fit batts in the walls, you can put all the insulation on the exterior in the form of rigid foam. The ratios require a minimum amount of exterior rigid foam R value for a given amount of in-wall R value, but that in-wall R value can safely be zero, or really small. You only run into problems when you have too little EXTERIOR R value in a wall that uses both in-wall insulation AND exterior rigid foam. You could use exclusively exterior rigid foam and be ok — the “perfect wall” concept actually does this, putting all R value on the exterior of the stud wall with nothing between the studs.
I would see how much R value you could fit in your walls using batts or cut’n’cobble between studs if you have to. Once you figure out what you can fit between studs, you can use the ratios to work out the minimum R value you need on the exterior for your climate zone. I would try for 2” of polyiso on the exterior if you can, which is almost certain to be more than you need to be safe, but it will reduced thermal losses through the wall.
Your under floor area sounds crawlspace-like. I’d look at articles about “crawl space encapsulation” and see if those methods sound like they’d work for your project. If you have lots of hard to get to air leaks, spray foam might be worth considering here, but I’d try to use polyiso as much as possible and only used spray foam where you have no other options. This is common in crawlspaces and basements where the walls are insulated with rigid foam and the rim joist area is the only part insulated with spray foam, for example.
Bill
Hi Bill,
Take a look at the attached photos for a bit more context. The room is almost all windows so there is very little room to add insulation on the inside because it's all studs and headers pretty much. I don't think I can swing 2" on the outside, it'd require removal of the siding from the entire back of the house. I think I could do 1" maybe 1.5" and not have it obvious that there's a transition. I presume I'm better off with say R7.5 on all exterior surfaces, leaving the stud bays under the windows empty? I could cut/cobble about 3.5" underneath the windows as it's 2x4 framing.
Venting is a priority as this roof ties into my regular roof and I want to ensure there's ventilation inside my attic to the areas that need it. Pitch is very flat, about 2.5/12. I could do waferboard with the 1.5" gap for ventilation and end up with roughly R38 as you mention but code calls out R50 here, which is why initially I wanted to go with XPS until I learned about the R value falling to 4.2/inch after 10 years.
My spray foam contractor was pretty up front when he estimated and told me they never spray 7" of foam which struck me as odd because that'd be about code. I guess the question is does the extra cost/effort to achieve R50 up there vs R42 including 1" of polyiso + fiberglass really worth the effort? Plot twist. I already have a LOT of unfaced fiberglass insulation here that was salvaged from a c0mmercial building, maybe enough to do half the project.