Plywood rot – how is it possible with open cell?

This may be a silly question but if I have 6-8” of open cell foam against my plywood roof and let’s say that the plywood was wet when the foam was installed, but the roof is otherwise airtight to the outside (no leaks, shingles installed properly, etc)…can the wet plywood rot without air reaching it? I thought wood rot needs water, warmth, and oxygen. Would the plywood be wet but fine similar to wood from lake bottoms unexposed to oxygen?
I’m asking because I have some wet plywood from a leak, I solved the leak issue, removed the wet open cell foam, but the plywood is still a little wet. I’ll do my best to let it dry but if the open cell foam is reapplied too soon I just wanted to know if that can truly lead to wood rot.
GBA Detail Library
A collection of one thousand construction details organized by climate and house part
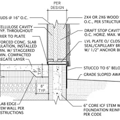
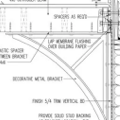
Replies
George,
Open cell spray foam is generally considered an air barrier when it's depth exceeds 5" or so. But that doesn't mean it's perfectly air tight. Even polyethylene passes some air... Also, shingles and roofing underlayment will allow air infiltration.
For your wet plywood to avoid rot, it will need to dry (through the foam) faster than it will be wetted by moisture/humidity from your home (which rises to the ceiling due to wet air being lighter than dry air). Obviously, open cell foam is vapor open. So the moisture will reach the plywood.
If you want to lower the risks, consider installing a dehumidifier in the attic or putting in an exhaust fan. An undersized air conditioner might work too. I would monitor the relative humidity to make sure it stays below 40-45%.
Thanks, makes sense. Follow-up question below then (let me know if best to post in new thread)-
My current setup:
~8-10" open cell along roof
-No fiberglass batts on floor
-Asphalt shingle roof w/ ridge vents
My ridge vent was poorly designed/old & leaked over the years until eventually it worked through the open cell foam and I saw the drips. I cut out all the wet foam (~3' each side of ridge along entire house). Plywood is wet as result so I'm redoing the entire roof (was inevitable in next 5-10yrs anyway), before reapplying the foam.
Roofers will replace any wet plywood & then finish roofing (GAF shingles) as normal WITHOUT a ridge vent. Open cell foam will then be re-applied where it had been cut out.
Question - Use a vapor permeable underlayment (GAF Deck Armour 16perm) or vapor impermeable (GAF TigerPaw <1 perm)?
If the plywood potentially gets SOME moisture from inside the house through the foam, does the benefit of letting that moisture POTENTIALLY diffuse to the outside through a permeable underlayment & shingles (~0.5 perm) on windy or very hot summer days outweigh the negative of vapor potentially going into the plywood from the outside?
Or am I better off isolating the plywood from the outside as best as possible (i.e. impermeable underlayment) so all the vapor diffusion to/from plywood occurs only to the interior (where I can use a dehumidifier in the attic if humidity levels are above 40-45%)?
George,
What climate zone are you in? Also, are you saying that you currently have a ridge vent but no vent path between the rafters from the eaves?
I wonder if it was actually bulk water coming in or a classic case of ridge-rot? (Often found with fluffy ceiling insulation and SIP roofs). Without plywood at the ridge, you have no air barrier other than the open cell foam. I can imagine warm, moist interior air finding its way to that ridge vent and then condensing on the plywood edges around the gap at the ridge.
If you are in a warmer climate, a built-up mini roof along the ridge might release some of that interior moisture, as you described. I believe the gap will need to be larger than a conventional ridge vent. I think cosella Dorkin makes a rain proof/vapor open membrane for the exact purpose. It's also an air barrier- something missing from your current ridge vent arrangement. The Building Science Corp has articles, videos about this that might be helpful.
If you are in cooler climate, then I would cover the ridge with plywood and work on an interior air barrier/vapor retarder. Better yet, I would remove the roofing, add a peel and stick membrane over entire roof and then add 4-8 inches of rigid foam. (Easier said than done, I know!!) :-)
When the dew point on one side of an insulated assembly is higher than the temperature on the other, there will be a point inside the assembly that is at the dew point temperature. If air from the warm side can reach that point condensation will form there. In heating weather it's the inside air that's warmer and moister, and in cooling weather it's the outside air.
There are two approaches to dealing with this condensation, either seal the warm side or provide a drying path. Moisture tends to travel from warm to cold, so the drying path is most effective on the colder side of the assembly.
In a roof assembly with open cell foam you tend to get condensation only when it is very cold outside. In a moderate climate most of the time it is rarely cold enough for the point where condensation forms to be close enough to the surface for meaningful amounts of air to get there, open cell is something of an air barrier. In a moderate or warm climate it is also often warmer on the outside of the roof than inside, even in the winter the sun warms up a roof quite a bit. When that happens moisture in the foam is driven down by the heat transfer and it tends to dry to the inside.
In a cold climate there is much more of the year when condensation can happen, and it tends to happen closer to the surface so more air is available, which means more condensation. Much more of the time the roof is colder than the inside, so the heat flow is up, taking moisture with it. Open cell is not generally recommended in a cold climate.
George,
The problems of wet plywood aren't limited to rot. The material is made up of wood and adhesives. Wood swells when wet, and adhesives fail. Plywood subfloors and sheathing exposed to the weather often delaminate without any rot being present.
Malcolm, understood thank you. DC - really appreciate the science behind the drying path & condensation. Sounds like the permeability of the underlayment is almost irrelevant in the equation, but is it better to err one way or another? I'm in southeast NY so sorta on the border of what I would consider a moderate climate.
FWIW when I pulled off the "dry" portions of the open cell foam (to ensure I got all the wet stuff out), the plywood looked & felt fine to the touch, no "give" when I pushed it, no wetness that I could tell, & for all intents & purposes seemed like no major issues (after 5-6 years of foam being there) so I'm probably overthinking this...
I would read through this a bit:
https://www.buildingscience.com/documents/building-science-insights-newsletters/bsi-016-ping-pong-water-and-chemical-engineer
https://www.buildingscience.com/documents/insights/bsi-077-cool-hand-luke-meets-attics
Basically, you need to condition your attic. With this any water that is in the sheathing will eventually dry through the foam.
From what I understand about these assemblies, in colder climates it is also helpful to have a vapor retarder over the SPF. This could paint of one of the smart vapor barriers.
Extra permeability on the outside of the roof is a good thing in cold climates, even a small amount of drying can help a fair bit if there are leaks. I would go for the permeable underlayment.
Thanks! Read the links. Super interesting (and actually entertaining). I’ll look into the supply and return for the attic especially since there won’t be an energy penalty so just the cost to install it one time.
I used to have super leaky ducts, until I just redid my entire central air system and ductwork... go figure. At least I was smart enough (after reading here 5-6 years ago) to remove all the fiberglass batts on the floor of the attic to allow for much better conditioning of the attic (not trapping the moisture up there)...I think. Maybe I’ll put a moisture meter up there this summer just to see how high the humidity levels get. If they are indeed similar to the rest of the house, do I really need the supply/return?
Then comes the issue with the fire code/intumescent paint given a potential active air exchange as the author wrote....in the interim I’ll go w the breathable underlayment, appreciate it!!!
>"I have some wet plywood from a leak, I solved the leak issue, removed the wet open cell foam, but the plywood is still a little wet. I’ll do my best to let it dry but if the open cell foam is reapplied too soon I just wanted to know if that can truly lead to wood rot."
Open cell foam has a fairly high permeance to water vapor. At 6-8" of thickness half-pound open cell foam. runs about 3-5 perms about the same as a single coat of standard interior latex over standard latex primer. Wet plywood can DEFINITELY dry through that layer of foam- the real question is whether it's too vapor open to avoid seasonal wetting from interior side moisture drives over a winter. The roof deck's average temperature will be below the dew point of the conditioned space air for at least part of the winter.
Your local climate makes a huge difference in how risky an all open cell solution at the roof deck is- where are you located?
See also: https://www.buildingscience.com/sites/default/files/migrate/pdf/BA-1001_Moisture_Safe_Unvented_Roofs.pdf (In particular see the "Full-depth oc SPF" column on Table 3)
Dana,
How risky is 8.25" OC conditioned attic with dedicated mini split just outside of Boston (Brookline)? Could heating to 76F in the winter and running in dry mode during the summer get my risk down?
Southeast NY (central east portion of Rockland County) so technically Zone 5 but maybe 15 miles from Zone 4 NJ - https://www.rocklandhistory.org/page.cfm?page=53
And again for what it's worth, the plywood under the dry portions of foam that have been ripped out feels/looks to be totally fine at least visually/to the touch and walking on it from above (and this is mid-winter too so you'd think i'd potentially feel or see SOME moisture on the surface of the interior sheathing given the dew point observation), so 5 years of real world exposure seems to have played out ok so far which is probably the best peace of mind at this time.
While zone 4A/5A boundary isn't as risky as zone 6 & higher, installing an interior side "smart" vapor retarder would be prudent, particularly on any north facing or fully shaded pitches. The sun offers a lot of additional drying protection by daily heating during the shoulder seasons, and a warmer average temp at roof deck even in winter. It's the pitches that get little to no sun that are at highers risk.
>"...this is mid-winter too so you'd think i'd potentially feel or see SOME moisture on the surface of the interior sheathing given the dew point observation..."
Wood takes up moisture as adsorb, not condensation on the surface. Try putting a dry chunk of 2x4 in the refrigerator overnight, then put it on the kitchen counter. Does it form condensation or look/feel wet after sitting out for several minutes? Unless it was already quite high in moisture content before it went in the fridge it won't change much in appearance or feel, unlike the can o' beer undergoing the same experiment.
Until you're already into the red zone on the risk scale the wood will never appear or feel damp. A 2-pronged wood moisture meter would be the only reliable way to tell if the wood was a fairly safe 15% moisture content vs. a fairly risky 30%.
The simulations in the BA-1o01 study were north facing pitches, at a somewhat higher R than your 8" of open cell foam, but pretty ALL zone 4 & 5 locations in Table 3 indicate more than 4 weeks per year above 28% moisture content (unless indoor humidity was well controlled), which is fairly risky in the long term.
Would roof pitches E-W and low indoor humidity (steam heat with humidity in the 20% range unless humidifier is used), get me out of the risky 4 week 28% group, outside of Boston?
Thanks a lot, sounds like humidity control is key, I'll monitor it closely and look into the supply/return in the attic as others have suggested. Or, better yet, I'll just install a dehumidifier up there with a drain into the gutter like my central air...
Dehumidifer costs power to run whearas your AC is free. Much better to get some conditioned air into the attic.
Nobody says that you can't put some leaky ducting back in there instead of supply vents. Try to route one of these leaky return ducts near the ridge of the roof. My guess your rotten ridge was more due to interior moisture buildup than a bad ridge vent, preventing hot humid air from stagnating up there should prevent this.
If there isn't an easily modifiable one, it might be simper to just run a new return to say the upstairs hallway and snake this to the top. Putt a register on it that you can close. Key is to think like a tract home builder and try to one up them on not sealing this duct.
Good pt. re: cost to run, etc. I can't say I'm savvy enough to do the supply/return (or route a leaky duct) but I'll see what my central a/c installer can manage and what that would cost.
I will say though that the ridge wasn't rotten from moisture buildup from below, the ridge vent 100% let rain water in during noreasters & storms, etc. The foam was SOAKED (picture running a sponge under a faucet and squeezing it, that's what I was dealing with) directly under the ridge. I know the ping pong theory but this would have required a holy man with a staff to keep the water out. I'll let you know in 5 years if I'm wrong since I'll have a new roof, plywood, and no ridge vent.
>"I will say though that the ridge wasn't rotten from moisture buildup from below, the ridge vent 100% let rain water in during noreasters & storms, etc."
Rot doesn't usually get started in just one or two seasons. Historically bulk water leaks are responsible for more rot issues than vapor diffusion, but both are important for the long term.
>"I'll let you know in 5 years if I'm wrong since I'll have a new roof, plywood, and no ridge vent."
Installing 3" of roofing polyiso (~R17) above the roof deck while re-roofing the overall performance will then hit current code minimums and greatly reduce the average moisture content of the roof deck. The IRC currently calls out R20 on the exterior for dew point control (with up to R29 under the roof deck) for zone 5, and R15 on the exterior (with up to R34 under the roof deck) for zone 4. Since you have something like ~R30 open cell (8" @ R3.7/inch) under the roof deck and are on the zone 4/5 boundary R17 above the roof deck is fine. It would be a few R shy of code compliance on an R-value basis, but the R17 thermal break over the rafters would still get you there on a U-factor basis. The warmer wintertime roof deck would take up dramatically less moisture.
Interesting thought ty, I'll need to find out the cost for that from my roofer. A few follow-ups:
-Is this just to solve for the potential moisture issue?
-Let's assume my plywood has some moisture in it currently - any concern that it couldn't migrate back into the interior conditioned space during the warmer months? Or does this simply minimize moisture in one direction (into the plywood, but not from the plywood)?
-If PolyISO is used, do I still need the breathable Deck Armour membrane or ok to go with the vapor impermeable & less $$ Tiger Paw (since I'd imagine the PolyISO would nullify any potential vapor diffusion on windy days to the exterior, etc.)?
FYI - it would nearly double the cost of my roof. I’m better off getting a new roof done in 10-15 years than adding it on. They use hunter board w cdx plywood as they want a solid surface to nail into since ISO not dense enough by itself he said. Also would require building up the wood trim w aluminum on the side of the house. So I’ll risk the moisture migration as it hadn’t been a problem (yet at least).