Poly Vapor Retarders and Batt Insulation on Old Basement Walls

We have an old house with an old interior french drain that just failed. Water came through window well windows and through a large crack that formed in one basement wall. We just just replaced the french drain (the old drain was crushed and filled with sediment etc) and also added drains from the three window wells that are piped into the french drain. We also repaired the crack and any other small cracks we found.
As part of the french drain installation to deal with water that could come through the walls, the team put up 6mm poly on all the walls that is open largely open at the top of the wall (not taped down) and then it runs behind the dimple board into the french drain. See photo illustration of the system.
I’ve seen all the posts that poly should never be used in basements walls. But our challenge is we can’t do rigid foam insulation as a retarder and then also batts for maximum insulation value in the framed out walls due to current constraints with our walls, framing, pipes etc.
So the plan is to have the poly on the walls and then r-13 batts inside the framed out walls and then sheet rock.
We’re in northern New Jersey in the 4a/5a zone.
One other note: on other parts of the basement where we ripped out the drywall, the old batt insulation that was between the drywall and the basement walls appeared black and perhaps moldy. We have regular significant issues with the ground getting super saturated and the water table rising in our area.
Thoughts?? Photo is attached.
GBA Detail Library
A collection of one thousand construction details organized by climate and house part
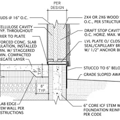
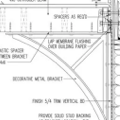
Replies
The reason to use rigid foam in a basement is to avoid condensation within the wall and the mold growth that results. The rigid foam can sometimes double as a vapor barrier too, but that's not usually the primary reason for using rigid foam to insulate in this application.
I would have used a thin dimple mat instead of poly sheet in your application, but it looks too late for that. The advantage to the dimple mat is that it creates an air gapped drainage plane, allowing any water to run down the wall. Poly against the wall will tend to keep the water trapped against the wall over time, which means more risk of mold -- although the poly does mititage the potential for that mold to cause problems, since it should be sealed in.
It looks like you knocked out your studs though, at least partially. I would take them out the rest of the way, put a layer of rigid foam (probably 1", thicker is better though) tight against the poly, then frame out the wall on top of that rigid foam layer and insulate with mineral wool batts. My preference would be to skip the batts and use thicker rigid foam though, then put the studs "sideways" to create a 1.5" space for electricals (standard 4" square boxes are 1.5" deep, and you can use mud rings to bring the device openings up to the surface of your finished drywall).
Is there a particular reason why you don't think you can use rigid foam here?
Bill
Thanks, Bill. I appreciate the note. Here are some further details:
- Yes, I guess dimple boards all the way up would have been preferable. But here we are. As far as the poly, you're saying that should be taped/sealed on the top to the wall?
- Confirming, you're also saying it's fine to put foam board on top and against the poly? Attach the foam board with foam adhesive? Screws?
- The issue I have is a few walls have baseboard heaters or a sink drain pipe and the pipes can only be moved out so much to allow for studs and the foam board.
I wouldn't tape the poly, but I would run a bead of polyurethane sealant (been using Tremco myself these days, since it's cheper than Loctite's PL line) maybe an inch down from the top edge, then use a roller to seal the poly to the wall with the sealant between. This is cheap, quick, and easy to do, and gets a good long-term seal. This way if you get mold between the wall and the poly, it's encapsulated and can't cause you much trouble in the living space.
Yes, you can put foam right over the poly. I like the Plasti-grip anchors for this, since they work well, and they go in quickly. They're not super cheap, but not terribly expensive, either. You can order them from from the orange store, other supply places, or even Amazon:
https://www.amazon.com/Plastic-Masonry-Fastener-50-pcs/dp/B01MPWLJJ9/ref=sr_1_20?crid=1RWYCGPQYO0ZT&keywords=insulation+anchor&qid=1706547443&sprefix=insulation+ancho%2Caps%2C96&sr=8-20
Be sure to get the right fastener for the thickness of foam you're using. Place the foam, drill through the foam and poly into the wall with a hammer drill, then stick the anchor in and whack it a few times with a mallet.
Insulate behind the pipes and heaters as best you can. If you have to cut out some foam in a few small spots, that's not as bad as leaving the rigid foam out entirely. Use thinner material where needed. I'd use foil faced polyiso behind the heaters, since it's a a little safer than EPS or XPS in that location, but I'd be very careful regardless that the heater won't potentially damage the foam or create a hazard. Note that the heater can be a problem for the poly sheet too.
Bill
This is clear and extremely helpful.
Are you a fan of an Owens Formular 250 2" or something like the RMAX Proselect R-Matte Plus-3 2" which has an r-value of 13.1 vs 10 for Owens --- and the price is comparable?
My preference here would be to use polyiso, probably fiber faced (cheaper), unless you have bulk water problems. You can often find factory second polyiso for around EPS prices, if not less. If you can't, or don't want, to use polyiso, I'd use EPS as a second choice. XPS would be my last choice here (more expensive, less green).
Bill
Great. Thanks for the tips. Will try to hunt down the factory second stuff in NJ/NY