Pretty Good House – Spec’ing HVAC, Minisplits, and Ventilation in Ontario

First off, thanks to all the contributors in this section–you are greatly appreciated.
Background Info:
Southwestern Ontario, Canada. Climate Zone 6.
I had a local MEP engineering company use Wrightsoft to determine my loads/duct design and to draw it up over top of my house drawings (see attached). I actually paid them to read some of the GBA articles so that they could understand what I wanted in a design. I have been told that the design is as aggressive as allowable in Wrightsoft that will meet local code. I am looking for opinions on deficiencies in the design. By the Ontario Building Code, the house will require around 160 CFM per 9.32.3.3.
In Ontario, we do not calculate Manual J, etc. and usually just design to the province’s implementation of the National Building Code along with meeting local municipal requirements. OBC is too big to be attached so here’s a link to it:
http://www.buildingcode.online/masterindex.html
Full disclosure: I work for a sister company of said engineering company.
Questions:
1. I would like to spec a Panasonic Intelli-Balance 100 ERV as I can “commission” it myself. However, my designer says that I will need 2 of them to meet the 160 CFM. It seems that the Panasonic FV-04VE1 has been discontinued. Are there any alternatives? Preferably one that can have 6′ of separation between inlet and outlet. As of now, it seems I will need 2 of the Panasonics.
2. Annoyingly, the OBC does not have a definition for ventilation in its definition section. In regards to 9.32.3.3, does anyone have any experience in Ontario where they postulated that bathroom and kitchen exhaust fans contribute to the ventilation capacity? Ie. the exhaust fans subtract a set CFM amount from the total required ventilation? Combining the principal exhaust (the ERV per 9.32.3.4 (5) ) and supplemental exhaust (ie. 9.32.3.5)?
Any and all opinions welcomed. This is a “first” for the company doing this type of calculation (ie. a tight “Pretty Good House” using minisplits). I am their guinea pig. Unfortunately, https://hvacloadcalculator.com/ does not allow purchase by Canadians or I would use it to check their work.
All work attached is bound by the copyright of those individuals and may be removed at their request.
GBA Detail Library
A collection of one thousand construction details organized by climate and house part
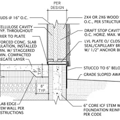
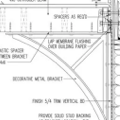
Replies
Looks like a thorough job on their part. It does appear that they missed entering in the ventilation load into the calcs.
Putting the ground floor ductless minisplit in the office seems like a bad idea, that room will be much warmer/cooler than the other rooms in the ground floor for the main floor to reach setpoint, even with the doors.
The second floor ducted minisplit doesn't show any return pathway for the minisplit. Assuming it's mounted vertically and there is a big return filter grille facing into the hallway, (which should be sized and noted) there still isn't a return pathway from the bedrooms to the hall. You'll need transfer grilles or jump ducts, door undercuts won't be enough for the bedrooms.
Looks like you have pretty competent people to work with though! That's great!
You are correct about the ventilation rates, in Ontario we use a "Principal Ventilation Rate" and a "Total Ventilation Rate". The Principal has to be met by 1 fan, usually the HRV. The Total can be met by a combination of the HRV, the bathroom fans, the range hood, etc. The tricky part is if the Principal fan exceeds the Principal rate by 50% or more, it has to be multispeed and turn down to within 10% of the Principal rate. Your principal rate is ~80cfm (not 100), so if you had something provided more than 113 cfm, you would have to hit 72 cfm - 88 cfm on low speed. It's usually simpler to stay under the 150% of the Principal rate. Using this worksheet: https://www.hrai.ca/uploads/userfiles/files/OBC%20Ventilation%20Summary%20Worksheet%20-%2020190813.pdf
might make things easier for you
Hi Yupster. Thanks for your reply.
I will parlay your concern about entering the ventilation load into the calculations.
I agree about the location of the first floor ductless. My hands are somewhat tied on that. My wife does not want the "wall wart" visible in either the living room/kitchen or in the dining room. My possible locations are the mudroom, office, or the front foyer. I am very open to input on its location. The best location, by my understanding, would be on the central wall. I've lost that design fight w/ my better half. I guess an alternative would be above the basement door (I could maybe get her to compromise on that as it is mostly hidden). Any thoughts by anyone?
Yes, the upstairs minisplit is to be mounted vertically w/ the return grille out to the hallway. I will make sure they spec it. Transfer grills or jump ducts are a possibility. Per talks w/ the residential part of the company, they felt that the best way to have a service cavity in the ceiling without fighting the inspectors too much was to do it by OBC w/ 2"x8" and plywood on top. Definitely overkill, but it offers some advantages:
1. easy, safe working surface for the framers when doing trusses (ie. crane them up to one end and then just drag them over by walking).
2. easy air sealing w/ caulk and tape (ie. no different than do a plywood wall)
3. one could put down a layer of poly if they were concerned about water intrusion
4. service cavity easily allows mains electrical and low voltage electrical to be run.
5. not having to fight the inspectors--OBC is OBC.
6. I never need to worry about falling through my ceiling drywall when I'm up in the attic like Chevy Chase in Christmas vacation ;)
Sorry, I'm confused about the Principal rate. As I understand it, one just sets the CFM in and out for the Panasonic ERV. My Principal rate is 80 CFM per 9.32.3.4. Principal Exhaust (I had previously, mistakenly used the 5 bedroom #..........my bad) and the unit only can do 100 CFM. So it would not exceed it by the 50%, no? There is no concern w/ the high/low speed in that regard?
The kitchen and bathroom Supplemental Exhaust (9.32.3.5.) would make up the rest for the Total ventilation Capacity (9.32.3.3.).
For me, the TLDR for Ontario is:
1. Use 9.32.3.3. and add 'em up for your Total ventilation.
2. Use 9.32.3.4. to size your Prinicipal aka your HRV/ERV.
3. Use 9.32.3.5. to make up the difference.
Thanks again for your input--much appreciated.
Yes, sorry, I went off on a bit of a tangent and just confused things. Your understanding is correct.
I would go with a second ducted minisplit like Akos suggested. It gets too cold here for a single unit to be a good comfort decision unless you have wide open spaces. (insert country song here). I speak from experience, pretty good house after renovation, single minisplit with a better configuration than what you have shown here, 3-7°F difference between closed off rooms most times. It's just not an acceptable comfort variation unless your a cheapskate like me. :)
You have a basement, I would just put another ducted unit there. Simple runs through the joist bays. Besides the look, wall mounts are a bit more maintenance as you have to clean the blower on them periodically. If you size the ducts right, you can save a bit of cost by sharing part of the ducting with the HRV. Plus your floor plan is not very open, without supplemental heat, your dining area will be cold even in a well insulated house. The extra ducted unit does add a fair bit of cost though.
Your plans show 6" ducts, which are not very common. 8" is standard and much easier to find.
Make sure to size the filter correctly. Most ducted mini split need a filter about 1.5x to 2x size of a standard furnace of similar capacity.
Ducted units can also be converted to be bottom intake (some need a adapter plate) which makes return much easier as you can just put filter grill directly under the unit sealed against the bottom side.
PS. Your wall R value seem low and basement loads seem a bit high. Depending on which compliance package you are using, a 2x6 24OC wall with batts and R5 rigid is closer to R24.
Hi Akos,
Thank you for your insights. I will pass them all along to the designer. Any idea (napkin-wise), what the cost difference would be between?
-ducted in the basement sharing ducting w/ the ERV professionally installed
vs.
-ducted in the basement professionally installed w/ 3" & 4" ventilation ducts I'd be installing myself
vs.
-"wall wart" professionally installed w/ 3" & 4" ventilation ducts I'd be installing myself
Choosing which compliance package seems to be more complicated then it should be. My guess that best fits would be Type IV, Package A. There will be no combustion appliances--at all--in the house so I take that to mean it is an all-electric residence.
https://cdn.shopify.com/s/files/1/0332/7677/files/Table_2.1.1.2.C.pdf?14462988891113549204
I usually just deal w/ stuff outside of the building. In my world, as long as I remember that fluids like to run downhill............the rest of the design seems to come together ;)
Mini split cost are very hard to pin down. About the only way I've gotten reasonable pricing is having the ductwork and mini split install costs priced separately. You'll probably pay at least 2x for ducted unit. One way to save some cost is to go down to a single unit in the basement for the whole house. This does mean more bulkheads but you do have a lot of interior walls that can be used for chases. This also eliminates the cost of the attic chase.
OBC is not friendly to heat pumps, so you'll have to go with the all electric table. I would go with B since you'll be installing a high efficiency ERV already and R20 VS R12 basement insulation doesn't make that much energy difference but takes up less space.
This does mean that the wall R value there is significantly higher than Wrightsoft, I would re-run your heat loss numbers with your actual wall assembly R values and basement insulation. There is probably 1/2 ton saved there.
You might be able to get your heat loss down that something like this (or with a small resistance aux heater) can carry your place:
https://ashp.neep.org/#!/product/31992
As an FYI, the OBC allows dwelling units with an ASHP and no supplementary electric resistance backup heat to use any of the regular SB-12 compliance packages in Table 3.1.1.2.A, so you don't have to use the electric house one if you don't have any electric baseboard. I can't remember if you do and didn't feel like checking :D Reference OBC SB-12 3.1.1.1.(17)(c)
I do have electric baseboards, but that's *very* interesting to know in regards to OBC SB-12 3.1.1.1.(17)(c). Thanks for that! Do people try and "scoot" around that by using electric fireplaces? Or do municipalities usually consider those also an electric baseboard?
As general information for those still reading, the Township had originally required that the HRV/ERV provide all of the Total Ventilation Capacity (TVC). I filled out the HRAI worksheet graciously provided above (thanks Yupster!) to show that the fans should be allowed for Supplemental Exhaust Fan Capacity. The Township is pretty good on questions and will allow back-and-forth prior to submission. For general information to the reading audience, I have included their response:
"Hi,
I’m going to bring us back to the beginning of 9.32, as this is a Part 9 building. Your route would be via 9.32.1.1.(1) (residential occupancy, house, individual dwelling unit), which states that Section 9.32 applies. The routes via 9.32.1.1.(2) (3) (4) or (5) do not apply to a house and therefore Part 6 does not apply to the design of this residential ventilation system.
As you consider your residential ventilation design under Section 9.32 please note that all of 9.32 applies, to be read start to finish. That being said, 9.32.1.2 and all of 9.32.3.7 are of particular note for a Type IV system (electric baseboard heat) as proposed.
Though the heat is not being delivered through the ventilation ductwork a duct design layout will still be required. We will also need to know the location of the baseboard heaters – this could be indicated on the construction plans or within the HVAC package.
As a heads up, note that electric space heating requires insulation values as per SB-12 table T.3.1.1.2 (attached). You seem to be at or above those values on your construction drawings, but please resubmit your EEDS to reflect a package chosen from table T.3.1.1.2. If you intend to do energy efficiency substitutions within a chosen package please submit an approved equivalency software analysis – see SB-12 3.1.3.1 for more on other acceptable compliance packages.
In regards to the proposed supplemental exhaust fans, they will need to meet all the requirements of 9.32.3.5. Note in particular 9.32.3.5.(5) and (8) that a manual switch is required in addition to the automatic control. Also please consult with your designer that these fans meet all HRAI requirements as the OBC does
In regards to the specifics of the Residential Mechanical Ventilation Design Summary, this is more the purview of HRAI than the OBC. I will hold off on general comments on a partially completed summary—it’s always better to have the full picture!
Please give me a call sometime to discuss your proposed ventilation system. I’ve answered each question as best I can with code references but I’d like to get a big picture overview.
Thanks,"
I'm a bit confused as to why they would still require a duct design for the first floor. Jump ducts for ventilation? If I have to put in duct work, that kinda defeats the purpose of saving money on the "wall wart" minisplit head. I'm quite a bit confused on that. I understand ducts for the bathrooms. Do I just need to run jump ducts from the rooms to the basement?
As to the fans meeting HRAI standards, I proposed using the Panasonic FV-0511VQ1 fans in all bathrooms. They allow the following modules to be installed:
-turning on at a set humidity (Model FV-CSVK1)
-turning on upon presence of motion (Model FV-MSVK1)
-a timer with selectable CFM to meet ASHRAE 62.2 requirements (Model FV-VS15VK1)
They can be installed as 6" so they can be used for everything in the chart.