Detailing for Moisture Control Between Grade and Sonotube Floor Assembly

I am in climate zone 4 Ontario (apparently that is zone 6 on your map)… planning a 24′ by 16′ workshop, 8′ high walls with a studio second story… 2x 6″ stud walls, Rockwool insulation between studs, 1 1/2″ Zip panels outside studs… I do not want to do a concrete pad (too much concrete)… instead I will use sonotubes @ 8′ centers, so 3 rows of 4 tubes… the site is well drained and I will also install drainage tile along base of the tubes on the 24′ sides to drain to a lower area, backfill around tubes with a coarse gravel… the tubes will finish up 6″ above grade and I will build 2×8″ pressure treated floor frame to rest on tubes… again, Rockwool between floor joists and Rockwool Comfortboard on bottom of floor frame… in effect this leaves a 6″ space between floor and ground, so questions… can I fill this space with 2′ minus crushed gravel..? vapor barrier under floor..what and where?
GBA Detail Library
A collection of one thousand construction details organized by climate and house part
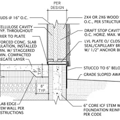
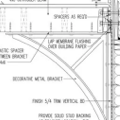
Replies
Personally, I don't care for your foundation plan. It would be much easier and cheaper to pour a frost protected shallow foundations (i.e. a gradebeam slab with perimeter foam). A slab that size would actually be easier to pour yourself and with a few helpers than it would be to properly install the sonotubes and get them deep enough for frost protection and level. You'll also end up with an easier to air seal and better insulated building.
As I said I do not want to do a concrete pad, for 2 reasons.. 1. too much concrete and.. 2. I will build a shed roof off the long axis of the shop as a place to park my tractor, it will be uninsulated and have a gravel floor, the roof posts will be supported on sonotubes and the building official will not allow 2 types (pad and tubes) of foundation in the same building... I still have the same questions about gravel and vapor barrier...
Mark,
The problem with these close to grade framed structures isn't how they perform when finished, it's how to fasten the necessary layers (rigid insulation and the pt plywood necessary to protect it) to the bottom of the joists, when they are so close to grade.
Since you are considering filling the area underneath with gravel, that makes things easier. What about this:
- Pour the footing pads and sono-tubes.
- Frame a surround out of ground contact pt 2"x8" to the level of the top of the sono-tubes.
- Fill with 3/4" clear crushed leaving enough depth for the Comfortboard.
- Lay 6 mil poly and Comfortboard.
- Frame floor system.
Thank you, these are good thoughts... Questions....why does the Comfortboard need protection, is it not engineered to be in contact with the gravel ?...( I would install a wire mesh around perimeter to keep walking/crawling critters out).... should 6 mil poly be directly under the Comfortboard or can it be a couple of inches under top of gravel layer..? ...Thanks again...
Mark,
Edited reply: The Comfortboard only needs protection from pests if it was g0ing to be exposed under the joists with no gravel.
I would place the poly on top of the Comfortboard as J0n suggests.
The way I see it if this is a more or less temporary building than go ahead and put your wood in the rocks where it will get and stay wet more often and longer.
From my experience ground contact PT wood fails in about 20 years. Look at the railroads their PT is more heavily treated than anything you are likely to use and set high on well drained gravel and they are out every day replacing wood.
If you want it to last longer keep the wood dry.
If you want to last forever make it out of concrete.
Walta
Would be interesting to see numbers. Does well drained (ie, above grade) ground contact rated PT wood with a roof over it last so long that the the life advantage of concrete isn't important?
That is what I am wondering... if the floor assembly is 8" above grade, the gravel is 2" minus crushed, the roof has good overhang and there is drain tile at the base of the foundation tubes then I don't see why the PT frame should be wet... I am still asking where the moisture barrier below the floor should be placed....
Wood/vapor barrier/Comfortboard/gravel/fabric/soil makes sense to me.
Mark,
If the floor system is 8" above the surrounding grade, I'm not sure any perimeter drains are even necessary.
I believe Comfortboard can be placed directly over the gravel, as the high density versions have been used under concrete floors. Typically you would want the vapor retarder on the warm side of your assembly. You can't put the vapor barrier a few inches under the stone or you'll make a bathtub. I think it would be best to install vapor retarder over the floor joists before you install your subflooring. You could also install Zip tape on the top of your subfloor as a combination air barrier and vapor retarder, but only if you are installing another layer of protective flooring over the zip tape.
Nobody likes an answer they don't want to hear, and I realize that, however I still think this is a bad assembly. Filling the gap with stone is probably the best option at the expense of slowly rotting your floor assembly. Whether you fill the gap between your insulation and the ground with stone or leave an airgap, you're creating a literal rat's nest. In addition to rats, animals like raccoons, foxes, opposums, snakes, etc will all really enjoy living in this space! Or it will fill up with leaves. It's also almost guaranteed you'll end up with a musty smelling shop and studio. It's for this reason that modern building techniques favor sealed crawl spaces. Your assembly is more akin to building a deck with a living space above it.
Rick,
Edited reply:
The poly doesn't need to be under the subfloor (a detail I've never seen) because for most of the time the vapour drive is from below, and the plywood is already a vapour-retarder. In very cold weather, when the vapour drive may be from above, locating the poly above the Comfortboard should stop moisture accumulation. With a pt wood surround filled with compacted gravel you won't have pests living in the space, because there is no space,
As I see it, condensation and moisture accumulation above the poly may occur with the poly below the fiber insulation. For example, say Winter, where the soil near the edges is 40F and it's 72F/35% inside (dp = 43F, vapor drive is from above). This trapped water would lead to moist wood when the soil warms up. I'd stick with the usual "vapor barrier on the warm side".
Jon,
Yes that's probably what distinguishes those from a slab - the space for water to accumulate on the poly. Moving it above the Comfortboard makes sense.
I am seeing interesting discussion here from all of you... just to recap my plan and my reasons... Sonotube with flared base set down to 4' below grade, drain tile at bottom of each of the long sides draining to a lower grade ( and this is just to be sure water cannot collect below building), this will be easy to install because the hoe will dig trenches for the rows of Sonotube.... the floor assembly is PT 2x8" with Rockwool between joists and Comfortboard on bottom of floor to reduce thermal bridging, the floor itself will be either 3/4' ply or 1 1/2' pine.... Comfortboard will rest on 2 0r 3" of 3/4" clear crushed and below this a layer of 2' minus clear crushed 12" deep (this 2" gravel will also fill the trenches around the tubes), with a heavy 1/4" mesh around the perimeter the largest animal that could get under the floor is an ant (and I don't think they will bother the insulation or the PT, unlike blue SM board that ants seem quite happy to burrow into).... I am less concerned about moisture migrating downward through the floor (this is a shop, not a house so a dry room above floor) then I am about soil moisture rising into the floor, thus my question about placement of moisture barrier. And I was asking about placing the poly barrier under the top 2" of gravel just so it is not being damaged while the floor is being placed (there may be a better option than this).... From Jon's comment about condensation above the poly, perhaps it makes sense to place a Comfortboard perimeter around the base going down say 2'. And Jon, I am not sure what you mean by 'fabric' layer....
> not sure what you mean by 'fabric' layer....
I usually put geotextile fabric as a separation layer between soil and gravel (which prevents settling as soil moves into gravel). But I suppose that with dry soil and no load, it doesn't matter.
Rethinking the gravel fill of an area that is usually air - make sure that if the ground freezes anywhere, it doesn't push upwards and bend your floor. A true FPSF design will prevent any soil from freezing (even at the perimeter).
Malcolm—can’t say that I know exactly what system Michael Maines is using. Is it vapor barrier, foam, flat sleepers, and two layers of subfloor screwed together? I’ve read articles where they use a setup like this confined within foundation walls. If so, this setup seems like it would be a lot easier to properly install a vapor barrier than it would be to to do it on the underside of a floor structure where you must work around the sonotubes and anchoring system. Regarding the critters, I’ve see plenty of instances where they tunneled through crushed stone underneath buildings. I think it’s the combination of dry and warmth they like. If it’s under a concrete slab it isn’t such a big deal, but not sure I’d want them under my wood floor.
Edit: Missed the follow up by the OP. Mesh hardware cloth around the perimeter would be effective.
Regardless, if he satisfies the building inspector and is happy with his system that’s all that really matters. Guess I’m more into tried and true methods.
Rick,
I've edited my posts, which I apologize for. Its really annoying to reply to something that then changes.
I'm not ready to switch to a concrete-free foundation yet either. These are interesting discussions, but I'm very conservative about what I'll actually do. I'd rather let innovators like Mike Maines iron out the details first, and then hopefully benefit from his and others experiments.
The one similar assembly I have used successfully for small unheated garden sheds is a perimeter of pt 6"x6"s filled to 2" from the top and floored with concrete pavers. Goes up really quickly, lets you do messy stuff inside and wash down the floor, and keeps the entrance close to grade.
I like that your garden house idea. That’s something I could see myself doing. It’s hard for me to wrap my head around the idea of no concrete. Besides avoiding a material with a high embodied energy, are there any other advantages of avoiding concrete? I’d have to imagine the costs of a treated wood subfloor system would be substantially higher.
Rick,
No that's the problem; concrete is a wonderful versatile material.
Also note that a concrete slab plus a $100 donation to the right cause will be much greener than a wood design.
A full FPSF design (ie including tractor parking area) can meet the "only one type of foundation" requirement. Even if the insulation is covered with gravel in the tractor parking area.