Zip Sheathing for Exterior Masonry Overclad Retrofit
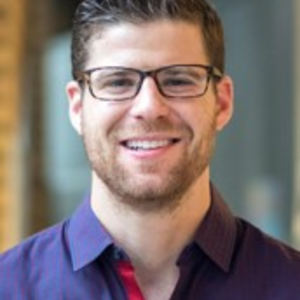
Hey Folks – So, I posted a bit about our situation last year. We purchased a home in Chicago, which is a 1914 brick 2 flat, last summer. We bought it from the builder who performed the gut rehab on the building. Long story short, their interior insulation retrofit did all the things you shouldn’t do, according to building science, and it has resulted in a significant amount of issues, including but not limited to spalling and accelerated degradation of both structure and finishes. We are not only concerned for the building, but also our health, as the assemblies are taking on a lot of moisture, from both from the interior and the exterior. Last winter, we opened up a few holes in the drywall to discover the interior face of the 3 wythe brick wall to be totally frozen over.
For reference, the assembly from outside to in, is: 3 wythe brick, 2×4 wood frame offset slightly from the inside face of the brick, 3.5″ knauf kraft face batts, drywall.
We have been considering 2 options for fixing this mess:
-The first being a proper interior insulation retrofit, whether it follows BSC’s recommendation of spray foam, or 475’s recommendation of Visconn liquid membrane, dense pack in 2×4 framing, and Intello smart vapor retarder. The hitch with this approach is having to uninstall all our finishes and completely demo back to the brick wall. The expense here would be significant. Ontop of this, we would have to still repair the exterior masonry, which we are getting quoted about $60k to bring it up to “standard quality”.
-The second is an exterior insulation retrofit, where we’d likely follow BSC’s deep dish literature. We like a lot of things about this approach. It will provide a continuous air/water/thermal barrier on the exterior. It will transition the brick wall to the interior, bringing it within the thermal boundary, thus allowing for its thermal mass to remain more constant to interior temperatures. It will protect our embedded structural wood members from thermal bridging and condensation risk. It will also give the opportunity to expose some brick walls to the interior too, which will be a nice aesthetic touch. Most of all, we would not need to re-insulate, re-drywall, and re-paint the entire interior of the building. Given that we would like to pursue the exterior insulation retrofit option, we shared the BSC article with our architect. The assembly from BSC is attached, but in short: fluid applied air barrier to the brick, 2×4 vertical furring, rigid foam between and continuous over the furring, 1×4 furring on the exterior face of the last layer of rigid foam, and then siding. Our architect proposed instead of all the individual components, to consider Zip Sheathing instead. Instead of installing the liquid air barrier, furring, and rigid foam individually, integrate it all together into 1 product. Execution wise this makes sense to me. It will probably reduce labor costs as well. It does limit us to R12.5, which is a bit less than I originally wanted.
So – any thoughts on Zip on this application? It never occurred to me to consider it.
Any other thoughts/feedback would be welcomed!
Thanks, -Scott
GBA Detail Library
A collection of one thousand construction details organized by climate and house part
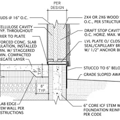
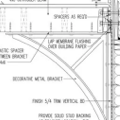
Replies
Attaching Zip R into a spalled brick wall sounds miserable to me.
Are you attached to a particular type of cladding? My guess is that EIFS would be simpler to execute, as well as to find a contractor to do it.
Nothing looks better than stucco, in my opinion, if it's executed well and there's a lot of it around (Vienna, Paris, etc.). On the other hand, if there isn't aren't other stucco finishes in your neighborhood, it can look funny.
Hi Bryan -
We will need to repair the spalled sections regardless. Parapets need to be rebuilt as well.
From an application standpoint, EIFS does sound like a good option. I also know that EIFS with drainage is now a thing, so I'm not opposed on the approach, but we don't think stucco is the most attractive cladding/finish.
We were looking at Hardie Board or Nichiha cement board, regardless of Zip or rigid+furring.
Deleted
Additional thought/concern:
With the ZIP system approach, you would be putting an air tight box over the existing structure.
With the BSC approach, you would be making the existing structure air tight by fluid applying an air barrier directly to the outer masonry surface.
Is there going to be an issue achieving the same quality of air tightness using the zip system? The way the ZIP system terminates near grade will need to be detailed… and any leftover exposed perimeter band of masonry near grade will need to be addressed somehow as well.
Is there significantly more room for error with the ZIP strategy or am I overthinking it?
Thanks
-Scott
Zip-R is a cold, low perm, wood (ie, moisture sensitive) sheathing. And it sounds like it wouldn't include a rain-screen gap. This is higher moisture risk than no wood sheathing and a rain-screen gap. Excessive risk? - probably not.
@Jon - The plan was to still apply furring to the ZIP System so that it would still be a rain-screen approach with the cladding.
If an AWB wants to be protected, why are we seeing so many high performance constructions that use ZIP system’s outer AWB coated layer as the drainage plane for rain-screen applications?
I got to ask are you sure it is a smart move to cover the brick from a financial point of view?
I have to wonder if covering the brick would cut the market value of the house.
I have to wonder if you cover the brick will potential buyers may assume the brick is in so bad you had to cover it.
I have to wonder if the home is historic will you need the historic district’s approval.
At least price the job with EFIS, my guess is be about half the cost of having hardy installed.
Walta
@Walta - if you read through the original post, I laid out the financial benefits of the exterior retrofit...
We are currently being quoted $60k for masonry work + $20k for new roof. We have not been quoted window re-installation, and I did not mention it in the original email, but we have bulk water coming in at a number of the fenestration openings. Then a complete demo of the interior to properly insulate the brick so that condensation doesn't occur within the wall assembly. I didn't price out the re-retrofit of the interior, but it would be demo of existing drywall + insulation, then ccSPF to about 2,400 sqft of wall surface, new drywall, new paint...re-install any finishes that needed to be pulled down (kitchen/bath/etc), that is probably $75,000? Total for this is approach is approx. $160,000?
According to the BSC Deep Dish article, https://www.buildingscience.com/documents/insights/bsi079-deep-dish-retrofits, while it is from 2013, they paid $14/sqft to perform the entire exterior retrofit. We have approximately 5,000 sqft of exterior surface area, coming in at approx. $70,000. Waiting on getting quotes for this from a contractor who is interested in the job. We would not need to pay for extensive interior fixes, as we would just be demo'ing damaged areas back down to the brick and exposing it ($5,000-ish). Let's throw another $20-30k at it for unforeseen issues, and this approach comes in approximately $75k cheaper overall.
Covering the brick from the exterior may result in a slight real estate hit. The data states: "“The analysis in the whitepaper noted above shows that comparably-sized homes, the brick home sees an immediate increase in value by about $4,000 over a home with wood or fiber-cement siding." I can't think of a reason to go with a more expensive fix, that is worse for overall performance just to try and pick up a few extra thousand dollars on re-sale. My thought is revealing brick on the interior could possibly make up for that. Additionally, there is real estate data out now on high performance homes yielding higher real estate sales. The exterior retrofit will result in significantly improved thermal performance as the insulation will be continuous. Additionally, the thermal mass will be within the thermal boundary resulting in improved effectiveness to keep temperatures more stable.
At this point, we are not interested in EIFS...we are not terribly fond of the aesthetics. I do acknowledge it would likely be cheaper overall solution though. I'd also pose an argument that stucco is considered cheap and would definitely be a hit to market resale value over a nice fiber-cement panel.
The home is not in a historic district.
At the end of the day, we are going through with this for us...not for other people (resale). If we were specifically concerned with maximizing resale value, we would band-aid fix things and sell the home off.
Bumping for the Monday morning readers! Hoping to get a good conversation going.
I've done a fair amount of research on ZIP over the weekend. I see why many of the building enclosure specialists would be less than enthused with it. At the end of the day, it is a coated OSB product that is susceptible to air and water infiltration if fasteners are overdriven and tape is poorly applied. Interesting enough, Matt Risinger seems to be very much on board with the product...but then again he is down in Austin and not in a cold climate like Chicago.
What I find attractive with the ZIP System approach is it will be an all-in-one application that will reduce the overall thickness of the retrofit assembly. Because zoning setbacks are a concern, going with the additional 6-7" of exterior wall BSC recommends may not be feasible. It seems to fit well with the complexity of our situation. With proper site oversight to manage the installation of the ZIP System (I'm going to push for the ZIP liquid flashing over all fasteners), I am less concerned about the final performance of the system being in jeopardy. It is making more sense from a cost/installation/execution standpoint.
Any additional thoughts would be welcome!
Thanks
-Scott
Bumping again, hoping to catch Martin’s eyes :)
You may want to reach out to someone local like Scott Sanders at Bright Leaf Homes. He's mentioned in the Acknowledgments at the end of that BSC Deep Dish article.
In addition to working with CEDA on those Chicago brick retrofits, I know that his company has experience with Zip and Zip-R, so maybe he can offer some guidance in terms of overall ease of installation along with material costs, whether you decide to pursue the BSC method or the Zip-R over the brick.
Hey Eric. Yea, great recommendation.
I was able to speak briefly with some of the BSC folks and they recommended to reach out to Scott Sanders as well. It would be great to get his input.