Replacing a Quonset Hut Roof

Hello,
I purchased a 40×17’ Quonset hut and there is a ton of water damage. The ceilings and above the of the dormers feel wet, so I suspect it is still leaking. I removed some of the rood and paneling and to my surprised the insulation didn’t look wet or dirty. This is a 1950’s style with 4ft framed knee walls. Searching through various forums it doesn’t sound like there are many good solutions, these huts just leak. With 3 young Children, one with respiratory issues, I can’t risk future leaks and mold. That said, I want to replace the metal with wood but have no idea if this is feasible. I was hoping I could remove the horizontal beams that the corrupted roofing is attached to and replace them with 2×6’s and then sheathing but maybe this is too much weight? I also wander if I could put a rubber roof over the corrugated metal? I had 2 contractors estimate what it would take to frame a gable roof. The first guy suggested I tear it down and build a new one, which is not an option. The second guy quoted me ~70k to put new side walls and frame the roof. When buying the house, I budgeted 30k for the roof, thinking was being extremely conservative. At this point, we’ve owned the hut for 2 weeks and I’m starting to lose hope. If I can’t find a cost effective solution, I was thinking about having spray foam added to the interior. I figured this would prevent leaks until maybe the summer, which I could then get on the roof and start patching. The previous owners put several layers of peeling paint. We are in MA, so it’s cold out.
Any advice would be appreciated. I would love to find an architect with experience converting a Quonset hut and familiar with MA code? If there are more cost effective solutions that will work in the winter, I am all ears.
Sorry for the long post and I apologize if I posted in the wrong location….desperate times.
thanks!!!
GBA Detail Library
A collection of one thousand construction details organized by climate and house part
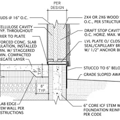
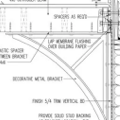
Replies
Can you post a few pictures?
Sure, thanks for replying. Note. They enclosed the front port h, so it looks like a gambrel
1 more
When I opened the wall, I noticed the bottom of it was a few inches below the top surface of the floor. It was also metal.
As in the bottom of the wall has rotted away, or a gap was built in when it was made?
I reached down to tap the bottom of the wall with a screw driver and that’s when I discovered the metal plate, which prevented me from getting to the wood. When I removed the paneling, the panel Mayer and Sheetrock was water damaged but the insulation and framing in that area showed no signs of contact with water. Maybe water dripped from the ceiling and ran down the walls, just missing the insulation and framing. The last photo above shows the metal plate at the bottom of the wall. I assume the vertical metal gambrel supports tie into thay
The moisture could be condensation. In this type of assembly, I wouldn't be surprised to see warm interior air condensing on the inside of the metal sheathing. Pole barns have similar issues. GBA has several threads where owners ask about insulating and air sealing these types of structures.
Yeah, first question is determining if it's condensation or leakage.
If it's leaking, it's tough because in these structures the roof is the structure, there's no replacing the roof. Mobile homes have similar construction and you can buy peel-and-stick and sheet EPDM for mobile home repair.
If it's condensation, there are two ways out: either introduce ventilation between the roof and insulation, or seal off the underside of the roof so that no interior air can reach it. The condensation is coming from warm, moist interior air coming into contact with the cold roof. The usual way to prevent this is either foam board insulation or spray foam, you can't use anything that air can permeate.
Hi, thank you. When I removed the wall, I noticed the insulation was not in contact with the corrugated metal, so I think there is an air gap. However, I also noticed that when they insulated, they skipped the gambrel corners, so there are at least a 2” wide channel not insulated that runs the length of the house. Also, the house isn’t heated or cooled but the previous owners could have had space heaters and I suppose there would still be a temp differential w/o heating. I will remove the ceiling panels this weekend and when it rains next, I’ll go back for some leak watching. I will report back on what I find and Thank you all very much for the guidance.
Ok, removed ceiling paneling and because it’s 10 degrees out, I think I know what the problem is. Looks like frost is coming through the sandwiched metal gambrel frame. There is a small gap. Also looks like frost from the metal. I think this is happening on the sides. The metal on the ceiling looked like this also at first but I can’t tell
If it’s frost, white rust, or mold. My hands are so cold, I can’t feel cold. The metal beam above the metal gambrel is not white and frosty but the gambrel is, which is confusing. Still a lot more paneling to remove but if the story doesn’t change, I guess spray foam could resolve the issue. I heard spray foam only sticks when the temperature is hot, like 70. If that is true, then I still won’t be able to do
Much this whole winter.
Looking at photos can sometimes be disorienting.
In this photo you posted is the up at the top?
Is panel B lapped over the top of panel A on the exterior of the building so any water running down panel B is directed over panel A? In this photo is does not look like it is to my eye. It seem impossible anyone would have built the way it looks to my eye.
Discounting the foil facing on the insulation I do not see a vapor barrier in the photo and I think you need one.
Walta
It’s actually the very top of the roof, down the middle. The picture is misleading, it confused me and I took it. Water collected in that area, which is why I took off that panel
Most likely what you are seeing is condensation from interior air leaks. Unless there are flashing issues around the dormers, the metal panels are rusted through or the fasteners have corroded, water won't make it in from the outside.
Since the structure is just batts and wood paneling, your warm side air barrier is practically none existent. All that nice warm moist air from the house leaks into the roof space and condenses on the metal panels which is what you are seeing. SPF is one way of sealing it up, won't be cheap but probably the simplest.
Looking more at the picture, there are way too many ugly details on the roof. I'm not sure if putting any more money into it is really worth it. Even if the SPF fixed the condensation issues, the original curved roofing looks to be in very rough shape.
If you really want to turn this in a long term home that is water leak and mold free, unfortunately I think in this case, your best bet is to re-roof the whole place. This is one of those cases that the structure is just not worth saving.
I have called 6-8 contractors and 5-6 architects and finding it very difficult to connect with people. I got a quote for 75k to frame a gable roof and the 2 side walls, which feels really high. I don’t think there is anything around here that does roofs like what I have now, so I figure if I am going to spend money, might as well go gable style. I just can’t spend 75k. Meeting an aluminum roof company next week. They said 20-30 k to remove the metal, install plywood, then their product. I’m not sure what I’m going to do. Thank you for your input!
The problem will always be that fixing this structure is more work than building anything new.
If you can at least get the roof replaced for reasonable cost, that would be a good starting point. This won't solve your current condensation issues, but at least there won't be water leaks.
Once the roof is fixed, you can look at building either an unvented assembly underneath with spray foam against the new roof deck or a vented roof.
A vented roof would require a clear air path from soffits up to a ridge vent. This might be a challenge with a mansard type structure but doable if designed in when you are re-roofing.
One more option I just though about.
If the curvature of the roof is not too tight, you might be able to bend thinner rigid insulation panels to match without breaking. Assuming you have 2x4 roof framing underneath (so ~R14 batts), in climate zone 5 you would only need about about R10 of exterior rigid for condensation control. That means if you can cover the roof with about two layers of 3/4" plyiso you are set. The polyiso can be fastened to existing metal roof with self taping screws and give a flat surface for a new roof. You can than roof over the polyiso with your choice of single ply roof (EPDM, TPO or PVC). The exterior insulation would warm up your metal roof enough that you won't get condensation from interior air leaks. This would let you keep most of the existing interior insulation provided you install a decent warm side air barrier such as taped drywall.
1 contractor said building new would be cheaper but I have to believe that 2 walls and a roof would be somewhat cheaper. This house is technically in a flood zone, so I think building a new requires a lot more hurdles and headaches related permits and approvals. The whole process is overwhelming and most of the larger companies that would help with these sorts of things are too busy to work with me, so I have to deal with it in my own. I don’t remember if I mentioned this but one of the main reasons why I want to frame new walls is because the only entrance to this house is at the back, which I think is really dangerous. I have 3 children, 2 are autistic and 1 of them loves to turn on knobs and press buttons, which is scary. I am hoping I can find someone to frame the walls and roof for a reasonable price and I’ll do the rest. If this proves to be impossible for whatever reason, I going to try foam spray on the roof and maybe it’s possible to add a dormer between the metal gambrel frame for a second door down the road. No idea how hard it would be to do this with an current paint peeling, messy roof. I don’t think I will have to pay much for the foam because we have energy efficiency programs in MA that will cover much of the cost, at lease 75%. Don’t get me wrong, if someone offers to build a new house for 25% more than framing walls/roof and can deal with all the permits, I’ll definitely listen, I just don’t know how feasible this is. My biggest challenge right now is finding a MA licensed Architect that will take the job before spring. I can’t apply for permits, which can take a long time, w/o drawings.
Again, thanks for all the tips.
I think your project is beyond the scope of the MA energy efficiency program. Best check before you rely on this assumption. This project is like trying to fix up an antique car to use as a daily commuter. Your money is best spent elsewhere. Maybe Habitat for Humanity might be able to help.
+1 to Akos
I wonder whether it makes sense from a cost perspective to go one step further and simplify the work (to a point).
Yes, the metal roof is not the WRB anymore and you have to add that which is itself a kind of waste but maybe fixing the existing roof is worse than separating the job and adding more layers.
- Keep the metal as structure, use some elastomeric spray coating from inside or outside to make it the airtight layer (or a WRB membrane wrapped around outside or..)
- Do the insulation (mostly) from outside and put a roof over that. Vented or not not - whatever is easier for the builder. In image 1 the front is simple - straight lines, the other round sections will be more time consuming.
- inside just some basic frame to hold the drywall or whatever you want to use. This way you do not have to do the fiddly air sealing etc., maybe something for diy if you have the time and nerves for that.
If you are afraid of corrosion for the metal then this will not work.
Is there a known WRB membrane that can be wrapped around corrugated metal? Mine has several layers of peeling paint, which I imagine would be really hard to remove but maybe necessary for adhesion. Still haven’t made it to the dormers yet, which also have water damage. Hopefully it is condensation not a leak. Thanks!
I thought along the lines of en EPDM membrane for the outside and either EPDM or PE or PVC in contact to the old roof. The inner layer does not need the UV resistance and elasticity at subzero temperatures as the outer one needs.
If the old roof is checked /smoothed out before so not been able to cut the inner membran it should be ok. Maybe a geotextile as in between layer? (typar, whatever is used in the drains to separate soil and gravel)
Fiddly and maybe a job-killer is a penetration through the roof.
In effect you create an unvented roof sitting on the corrugated old roof. Two layers of rockwool in between both membranes would do the trick, inner and outer layer would have to be joined and sealed around the perimeter. The EPDM would need some tie-downs (strap-downs) to secure against wind forces altough I reckon that the lifting forces will be small (the metal roof is nearly air tight and will not allow the air under the inner membran to lift that assembly up.)
I do not see that idea fly because for a roofer that is unchartered territory - frankly speaking - and you will either receive rejects or a hefty premium. Maybe a roofer used to commercial flat roofs of similar design would be comfortable enough to tackle it.
Look at mobile home roof repair products. They have metal roofs that often fail. There are brush-on products as well as rolled out sheets.
Is this a real Quonset Hut from WWII or just a Quonset-style building? See:
https://en.wikipedia.org/wiki/Quonset_hut
Interesting trivia: The Quonset Hut gets it's name from the factory where they were first built, which was in Quonset Point, RI. "Quonset" in the Narragansett language meant "peninsula" or "point," Quonset Point literally means Point Point.
In some mobile home repairs they do what is called a "roof-over," which is essentially building a carport-like structure over the mobile home to keep the weather off of the roof.
I believe it is the real deal. The location of the house used to be a navy training camp. I’ll check out the RV products. Earlier today, I was thinking pool liner :).
Thanks
A pool liner and a roof membrane do not have the same spec.. I would not go too cheap on that membrane - if it becomes brittle and something hits you have a leakage you do not want to fix.. Mind, my only experience was flat roof membran after a tornado and then all bets are off anyway, still look at quality.
Hi, I think Akos is correct, it is more of a condensation issue, although there might be 1 small leak. I removed more paneling and insulation and discovered 2 things, one of which I could really use direction on. Item 1: for whatever reason, they did not add additional framing (16 on center) on one side of the hut, so the insulation was all over the place, like a 10” gap between two rolls. This is where most of the water damage is and my first run in with mold. The other side of the room had the framing, good insulation except one spot and no mold.
2: I found an 8” diameter ceiling vent that was closed. It had a chain, which was wrapped around metal framing and it was above insulation and paneling, so not accessible. It took me an hour to open because a mouse filled the area above the open/close door with insulation and other things. I cleaned it out but at some point, I need to put insulation and paneling back up. Do I leave it open? If rain water wants to come in, it will, the door would not stop it. I am thinking about making an insulated access door beneath it, so I can keep it open in summer and closed in the winter, does this make sense? Pic of vent attached.
Another thing I plan to do is remove the rolled insulation, which has a metallic covering on the interior side and install a reflective thermal barrier close to the roof but not too close because I want to reinstall the insulation. Is there anything wrong with metal roof / gap / thermal barrier/ tiny gap / roll insulation with reflective backing?
Finally, there is 7/16 particle board on the knee wall and the first angled wall has Sheetrock. Everything else is just paneling. I feel like the particle board and Sheetrock absorb too much moisture, so I’d like to remove both and keep it paneling on 2x4’s. I will add framing so it’s 16 on center in both sides. Right now, I can stick my finger through the particle board it’s so rotted. Any concerns with this? Thanks!
Thank you!!!!
Rich
No tips? The work starts tomorrow, hopefully I don’t mess this up.
Have you diagnosed the problem as a bulk water leak from the exterior or condensing water vapor from interior moisture sources or both? The two problem require very different solutions.
Tell us what is your repair plan is?
Walta