Radiant Ceiling Heat, CI and building moisture control

Hello all,
I have to say I love all the different things I have learned on this site over the years and used it to design our new house. I usually can find the answers myself but this one is nuanced.
The Short: I am renovating (gut reno including wall sheathing) a 2×4 framed house with CI (Huber R12 Zips for walls, 4″ EPS for roof) in zone 4 (across the river from NYC) and with radiant ceiling heating (aluminum transfer plates). The walls (r15) and ceilings(r34) will also have mineral wool for interior insulation. Does this mess up the building moisture control insulation equation stated in the article: https://www.greenbuildingadvisor.com/article/how-to-install-rigid-foam-on-top-of-roof-sheathing? In the article it mentioned the mix was different if it was a 2×6 frame so is it different with a heated ceiling? I know I can increase the exterior insulation but I am already at the building height max. Also, am I sitting on a moisture time bomb with the polyiso on the exterior walls?
The Long:
We are building this house to be very tight with a new third floor and flat roof
3 floors with basement (2 units- 2 floors per unit)
2×4 framing
Exterior insulation Walls: Huber R12 Zips (Polyio) (yes I know, no one likes zips insulated sheathing here)
Exterior insulation Roof: 4″ EPS in-between 1/2″ plywood for for a closed roof system.
Flat roof (EPDM) using crickets above the Plywood/EPS sandwich (my understanding is the crickets will also be insulation but shaped to push the water from the center of the building(21′ x 47′) to the four drains, two on the sides in the front and two on the sides in the back of the house.To be clear, the crickets taper down from the center to the exits. We have not ordered the crickets yet so I don’t know how thick they are in the center. (I understand thicker exterior insulation is ok)
Interior insulation Walls: mineral wool R15
Interior insulation Roof(s): mineral wool R34
Rain screen: 3/4” battens
Siding: Hardy Plank
1st floor and basement extend out 10 feet with a flat roof (EPDM). Again sandwiched 4” EPS with crickets on top to control the water movement.(so same moisture question but no height limits here)
Ventilation: ERV per unit
AC: duckless ducked mini splits per unit (no previous HVAC)
Heating: Radiant ceiling using Wirsbo Joist Trak Extruded Aluminum Heat Transfer plates with the ceilings joists on each floor packed with mineral wool.
Dehumidifier: None (plan to control this during shoulder weather with radiant heat and mini splits)
So after all of that, does the heating on the ceiling change the r15/r34 roof insulation equation where moisture is concerned? Will the polyiso/mineral wool wall insulation cause moisture problems in the future?
Thanks,
Jeff
GBA Detail Library
A collection of one thousand construction details organized by climate and house part
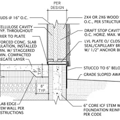
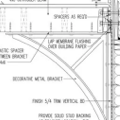
Replies
The concern with insulation that can't dry to the outside is that condensation will occur in the wall. The thickness of the exterior insulation is calculated so that the spot where the temperature is equal to the dew point of the interior is within the continuous insulation.
With ceiling heat, the temperature of the interior side of the ceiling is higher, but the dew point of the interior doesn't change. So the point where the temperature is at the dew point will be further to the exterior. So in theory you need thinner exterior insulation.
That said there's an argument for thicker insulation given that your ceiling temperature is higher.
I should also point out that the aluminum plates themselves are impermeable, depending on how you install them you may end up with an assembly that has vapor barriers on both sides. In theory this shouldn't be a problem if the outer insulation makes the assembly safe but it's something to worry about.
"That said there's an argument for thicker insulation given that your ceiling temperature is higher." Assuming you are meaning external insulation. So you think the 4" of EPS will work then? Your answer is conflicting.
Still letting the vapor barrier statement sink in.
At the risk of being too elementary, here's a fuller explanation:
Whenever you have one side of a wall or ceiling assembly colder than the dew point on the other side of the wall you have to worry about condensation. If the inside of your house is at, say, 70F and 50% relative humidity that's a dew point of 52F, if it's less than 52F outside you have to worry about condensation. If your assembly is insulated with a permeable insulation like fiberglass, cellulose or rock wool, that condensation will cause rot and mold and all kinds of problems.
One way to prevent condensation is to put a vapor barrier on the interior and construct the assembly so that it can dry to the exterior. This is commonly done with walls and vented roofs, but it doesn't work with unvented roofs. Another way is just to insulate with an impermeable insulation like spray foam or foam board. A third way is to put enough impermeable insulation on the outside so that every part of the assembly that is below the dewpoint is within the impermeable insulation. That's what we're talking about here.
So you want every part of the assembly to stay above 52F in this example. If your outdoor design temperature is 15F, that's 57 degrees below indoor temperature. The dewpoint is 20F below indoor temperatures, so at least 37/57 -- 65% -- of the insulation has to be impermeable, and no more than 35% can be permeable. If your roof is R50 that means you need at least R32.5 of impermeable coupled with no more than R17.5 of permeable.
Now, let's say with radiant heat the underside of your roof is now at 100F. The dew point of your interior air doesn't change, so 52F is still the magic number. Now you have 85 degrees between interior and exterior, and the dewpoint is 48 degrees from the interior temp. So now the impermeable insulation needs to be at least 37/85 or 44% of the total and the permeable insulation can be no more than 48/85 or 56% of the total. So with the same R50 you can now do R22 impermeable and R28 permeable.
Finally, insulation levels should be developed using cost-benefit analysis; insulation is added until the long-term benefit no longer justifies the cost. If your ceiling temperature with radiant heat is 100F rather than 72F, the heat loss at 15F exterior temperature is 85/57=49% greater. With 49% greater heat loss, a higher level of insulation may be justified.
"Still letting the vapor barrier statement sink in."
When you use permeable insulation there has to be a way for moisture to exit the assembly. The most common way to do this is to have a vapor barrier on the warm side and build the assembly so that it can dry to the cold side. If you can't do that -- like under an unvented roof -- the alternative is to use impermeable insulation on the cold side, and no vapor barrier on the warm side. The impermeable insulation should prevent condensation from happening. Water vapor flows in the same direction as heat, so in the summer when the roof is hot and heat is flowing from above down, any vapor in the roof assembly will be driven out. Drywall is very open to vapor, so as long as there is no vapor barrier on the insulation this will dry out the roof. So long as there is no condensation happening it's considered OK to have your assembly absorb moisture part of the year and dry it out the other part, it's what happens with any assembly using permeable insulation.
With all that as the preamble, an aluminum plate is going to act as a vapor barrier. I don't know whether enough of the ceiling is going to covered to keep it from drying. I don't know how much of a risk it is to have an assembly where the permeable insulation is kept from drying but is always kept above the dew point. I do know that on the Building Science website they have gross pictures of walls with exterior vapor barriers and mirrors, cabinets or vinyl wallpaper on the interior wall.
In my own home I have ceiling radiant heat with aluminum panels. I have exterior foam insulation on the roof and an unvented roof. I was unable to come up with a conclusive answer to this question, so I insulated the ceiling above the panels with spray foam.
I think before looking at equipment too much, I would get all your ducks in a row.
This means figuring out how much heat and cooling the place will about need. This a simple (free but they want your e-mail) tool for running a heat loss calculation:
https://betterbuiltnw.com/hvac-sizing-tool
Once you have that, you can look at what makes the most sense. Right off the batt, Rip R12 in zone 4 has an ROI of never. It also needs a special nailer that can shoot 4" nails, R6 or R9 is a much cheaper and easier to install option.
Generally once you are into this ~R25 walls and R40 roofs, the heat loss with a well sealed place is so low that anything hydronic makes little sense especially if you are already running ducts for cooling and ventilation.
For a bit of extra luxury comfort, the resistance floor heat systems work very well, much simpler to install. Provided that the bulk of the space heat is provided by a heat pump, the operating cost of the resistance is also minimal.
According to the table here: https://www.energystar.gov/ia/partners/bldrs_lenders_raters/downloads/County%20Level%20Design%20Temperature%20Reference%20Guide%20-%202015-06-24.pdf
Bergen County has a heating design temperature of 15F and a cooling design temperature of 90F. Assuming an indoor heating temperature of 72F and a cooling temperature of 78F that's 57 degrees of heating and 12 degrees of cooling. So you're going to need a lot more heating than cooling, how much is determined by your solar gains. Plus a heat pump moves about 70% of the BTU's when it's 15F outside as it does when it's 90F outside, so even if your heating loads and cooling loads were the same a heat pump that met your cooling needs would be 30% undersized for heating.
So it's a perfectly legitimate strategy to size your minisplits for your cooling needs and then add radiant to make up the additional heating that you need. What this allows you to do is put spot heating exactly where you want it. For example, in one bathroom I have 24 square feet of radiant floor heat, I estimate it can produce 300 BTU/hr. It's exactly what the room needs to stay cozy. Pretty much the smallest minisplit head you can get is around 6000 BTU/hr, or 20 times as much. Radiant heat allows you to match the heat in every room to the load in a way that minisplits never will and is hard with a ducted system.
@ Akos
We already did a full workup on heat loss years ago when we we went through the design process and then when we were fighting for our permits. We had a radiant system designer (Rich McGrath) configure the system in both units. He thinks we will be able to keep the system water under 100F. I wanted radiant floor heating but Rich suggested we go with the ceiling heating since I wasn't willing to pay the ridiculous Warmboard prices. Other ceiling advantages are we can completely change the rooms around down the road and use whatever flooring we want. Plus all the insulation will help minimize sound between floors. As to why I want radiant, when we designed the building a couple of years ago it got down to single digits a couple times, heat pumps were still not as efficient in the cold weather as we wanted with the crazy weather. (Same with the mini splits.) I am super excited about the radiant heating and it is less than 25K per unit not including new boilers and insulation. That does include design costs, tubes, manifolds, plates, 23 zones between the two units and having a very experienced radiant heating plumper setup my control panels, utility rooms and test the systems. I will attach the high level view of the system.
As to the Zip R12 sheathing, I agree with you totally but we are pot committed at this time. We already bought and installed it on the lower floors. The Huber brochure was missing quite a bit of the "extras" required to make their system work. Yes I had to buy a big bertha nailing gun(super expensive), and a ton of 5" nails. We had to add blocking between all the studs so we could shoot nails every 6" on the edges. We also had to cantilever 2x8s on the sides and bottoms of the windows since it would not handle the weight.
I originally wanted to go with the mineral wool batts (youtube on perfect wall) on the outside but my Architect convinced me that was way too much work.
If I could go back, I would have used nailbase.
DC_Contrarian I totally agree. The mini splits can supplement for immediate heat changes but the bulk of the lifting will be the radiant heating system.
I would go through and rationalize the heating plan a bit.
How big is the place and how many sqft of emitters are you installing? What is the design load for each unit?
23 zones is way more than I have at home where I consider my setup microzoned. The fact that there is a buffer tank in the setup confirms this fact. This just adds extra complexity, cost and controls, a two story place needs at most two thermostats, maybe an extra one if you are running floor heat in the bathrooms. I have even gotten way with no bathroom thermostat by slaving it to the rest of the zones, this way if any zone calls for heat the bathroom floor heat is on. With a bit of flow tuning, this works great as the bathroom is always hotter than the rest of the house.
Radiant ceiling panels will do very little for sound, if anything they will make proper soundproofing hard as it will be very difficult to decouple the assembly from the floors.
Warmboards are spendy that is why I stay away from it, for low cost floor heat I use either a staple up with Ultra Fins or 1.5" slab with embedded pipe. Slower response but for a rental a radiant slab would significantly improve the sound separation between places plus would definitely eliminate the buffer tanks.
I have radiant floors at home and it has never effected furniture placement.
For a previous project I went through a similar exercise and in the end it ended up with ducted hyper heat mini split for heat and cool. For $1500 BOM cost, you can beat the efficiency and comfort it provides. Compared to a similar place with radiant + wall mount mini split, utility costs are lower.
23 zones just seems crazy unless this is a place the size of Versailles. I would believe 23 rooms in a room-by-room Manual J, that sounds about right for a thorough job. But you should be able to group them into 1 or 2 zones per floor.
Also, have you thought about how the control system is going to work with a mix of minisplits and radiant? I have a similar system and I'm struggling to "civilianize" it, to get it to the point where someone other than me can operate it. Especially tenants aren't going to want to learn a complex system, they're going to want to set one temperature and forget it.
That area is borderline Zone 4/5. I'd calculate as if in Zone 5. In real life, there's zero difference in the weather between NYC and let's say, Hoboken.